3D-печать применяется в авиационной промышленности не первый год. Такие авиапроизводители, как, например, Airbus, применяют технологию для изготовления различных компонентов самолетов; количество деталей, которые компания печатает на 3D-принтерах, исчисляется тысячами. В начале этого года был изготовлен первый сертифицированный Федеральным управлением гражданской авиации США конструктивный элемент воздушного судна из титана.
Это событие ознаменовало признание 3D-печати в качестве одной из ключевых производственных технологий в авиастроении. Что касается интерьера салона, то недавно в регионе Ближний Восток и Северная Африка (MNA) для Etihad Airways, второй по величине авиакомпании Объединенных Арабских Эмиратов, была разработана первая сертифицированная деталь интерьера, изготавливаемая по технологии 3D-печати.
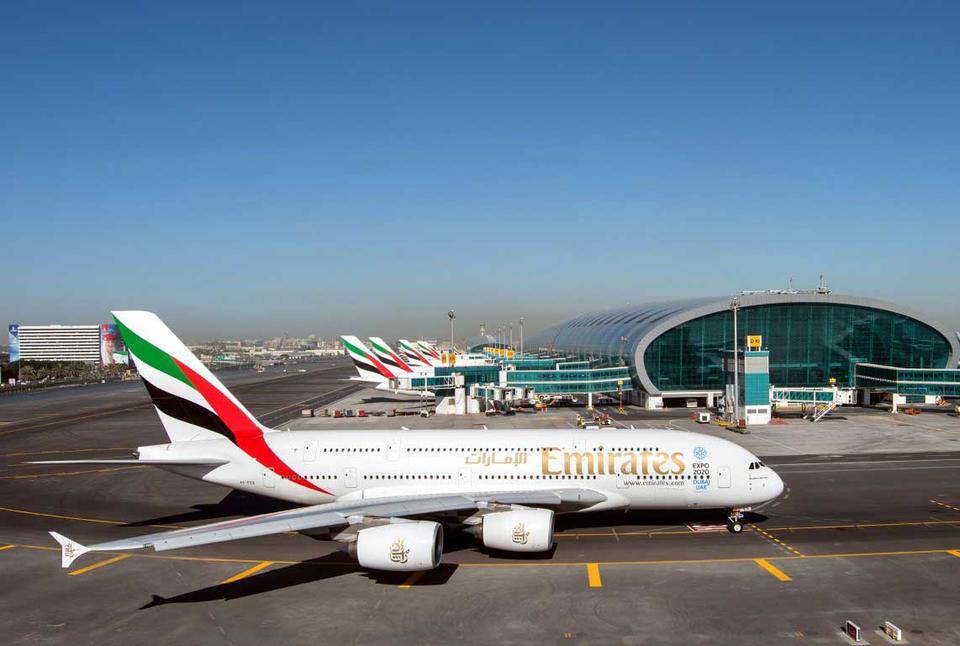
Крупнейшая авиакомпания ОАЭ Emirates не собирается отставать в области аддитивного производства от своего конкурента. В середине ноября 2017 года Emirates объявила, что намерена использовать 3D-принтеры для производства деталей салона самолета, включая кожухи системы видеонаблюдения и решетки вентиляционных отверстий. Последние уже сертифицированы и установлены для проведения бортовых испытаний на самолетах авиакомпании.
Emirates совместно с 3D Systems готовится к производству кожухов системы видеонаблюдения с использованием технологии селективного лазерного спекания (SLS) и нового материала DuraForm ProX FR1200 Nylon от 3D Systems, который соответствует нормам огнестойкости, принятым в аэрокосмической промышленности для деталей салона, а также стандартам густоты и токсичности дыма AITM. По данным 3D Systems, изделия из этого материала обладают отличным качеством поверхности и удобны в постобработке. В ноябре 3D Systems продемонстрировала материал, а также другие решения для 3D-печати на авиашоу в Дубае.
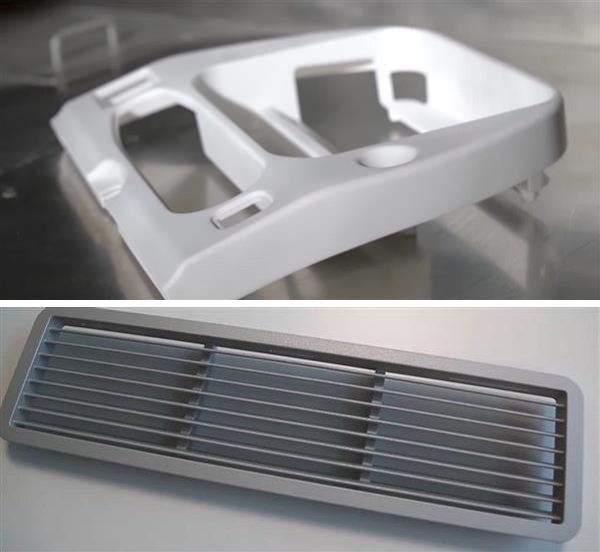
«3D Systems имеет большой опыт работы в авиакосмической и оборонной промышленности и успешного сотрудничества с заказчиками, – рассказывает Брайан Ходжсон, специалист 3D Systems по инновациям в аэрокосмической отрасли. – Мы рады представить на этом мероприятии несколько решений, которые позволяют нашим заказчикам добиваться высокой производительности, воспроизводимости, долговечности и оптимальной общей стоимости эксплуатации».
Emirates совместно с европейской компанией UUDS разработала и изготовила на 3D-принтере решетки вентиляционных отверстий, которые также были созданы с использованием селективного лазерного спекания. Среди причин, по которым было решено применить технологию 3D-печати, авиакомпания указывает на прочность и более низкий вес деталей, напечатанных на 3D-принтере. Изготовленный таким способом кожух видеомонитора на 9-13% легче аналога, произведенного по традиционной технологии, что может способствовать значительному сокращению расхода топлива и затрат авиакомпании Emirates. Кроме того, 3D-печать позволяет производить детали по мере необходимости, устраняя необходимость в поддержании большого фонда запасных частей или длительном ожидании их поставки.
«На протяжении последних двух лет инженерная служба Emirates активно изучала технологию аддитивного производства применительно к деталям салона самолета, так как это революционная технология, которая может быть использована для увеличения эффективности и производительности, – отмечает Ахмед Сафа, старший вице-президент Emirates по инженерной поддержке. – Совместно с рядом поставщиков мы разработали несколько прототипов деталей салона, но в конечном итоге решили сотрудничать с 3D Systems и UUDS. Применяемая нами технология позволяет делать детали салона более легкими без ущерба для структурной целостности и внешней привлекательности».
В будущем Emirates планирует использовать 3D-печать для изготовления других деталей салона самолета, но сперва намерена оценить эксплуатационные показатели кожухов видеомониторов и решеток вентиляционных отверстий.
Автор: Клэр Скотт. Перевод с английского. Оригинал этого материала.
Статья опубликована 24.11.2017 , обновлена 26.04.2021