Проблемы 3D-печати черепно-челюстно-лицевых имплантатов | Моделирование всей платформы за три минуты | Оценка результатов | В поисках наименьшей деформации
Одно из главных преимуществ аддитивного производства – возможность реальной кастомизации деталей. Эта технология хорошо подходит для производства индивидуальных имплантатов для пациентов в таких областях медицины, как черепно-челюстно-лицевая хирургия (ЧЧЛХ), где требуются оптимальный размер, форма и механические свойства.
- Задача: продемонстрировать, что моделирование может помочь в выборе правильной ориентации и конфигурации поддерживающей структуры
- Решение: создание трех различных конфигураций поддержки деталей и их сравнение
- Используемое ПО: Materialise Magics
- Метод: моделирование и сравнение деформаций финальных конфигураций поддержки деталей
- Отрасль: здравоохранение
Проблемы 3D-печати черепно-челюстно-лицевых имплантатов
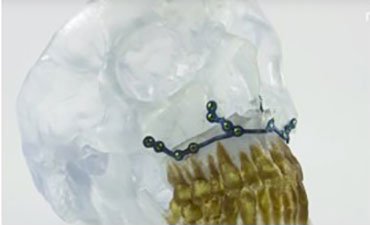
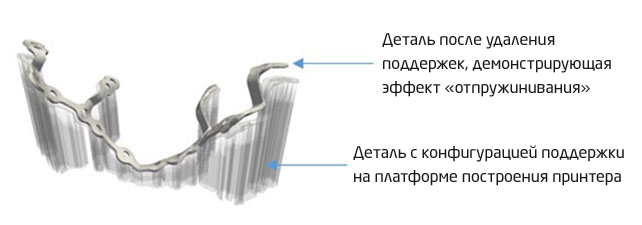
Процесс производства имплантатов для ЧЧЛХ вызывает множество затруднений. Если имплантаты не обработаны термически, они, как правило подвергаются так называемому эффекту «отпружинивания» в некоторых конфигурациях построения из-за остаточных напряжений. Этот эффект вызывает значительные деформации окончательной конструкции, вследствие чего имплантат может не подойти пациенту. Насколько серьезным будет эффект отпружинивания, зависит от ориентации детали и конфигурации поддержки. Однако подбор правильной конфигурации – процесс сложный и трудоемкий.
В настоящем примере мы исследуем различные конфигурации поддержки деталей индивидуального имплантата для черепно-челюстно-лицевой хирургии и определяем, какая конфигурация менее всего подвержена отпружиниванию и, соответственно, максимально подходит для аддитивного производства. Мы делаем это путем моделирования деформации с помощью хорошо откалиброванного метода собственных напряжений* и сравнения конечных деформаций изделий после удаления поддержки. Для подтверждения результатов моделирования мы провели дополнительное сравнение с изготовленными конфигурациями конструкции.
Моделирование всей платформы за три минуты
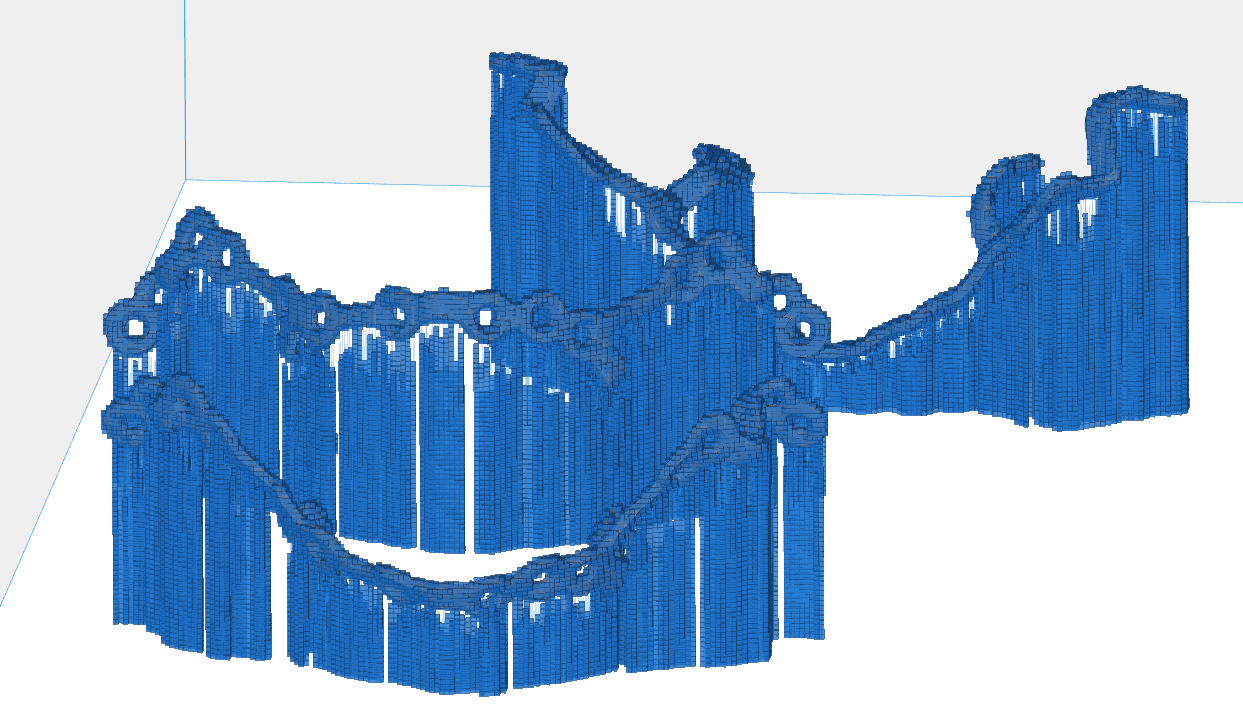
Моделирование является мощным инструментом для минимизации неудачных сессий печати. Оно предоставляет ценную информацию о том, как размещать (или не размещать) поддержки или критически важные сегменты. Давайте посмотрим на рабочий процесс моделирования.
- Получение CAD-геометрии детали и конфигураций поддержек.
- Вокселизация геометрии детали и проверка поддерживающих структур в граничных условиях.
- Моделирование послойного построения методом собственных напряжений.
- Интерполяция воксельных результатов на исходную CAD-геометрию.
Мы решили сосредоточиться на скорости моделирования, поэтому вокселизация деталей имеет довольно крупное зерно. Нашей целью было не имитировать точное искажение любой конфигурации, а определить, какая из конфигураций подвержена наименьшему качественному искажению. Всего за три минуты мы смоделировали всю вокселизированную платформу.
Оценка результатов
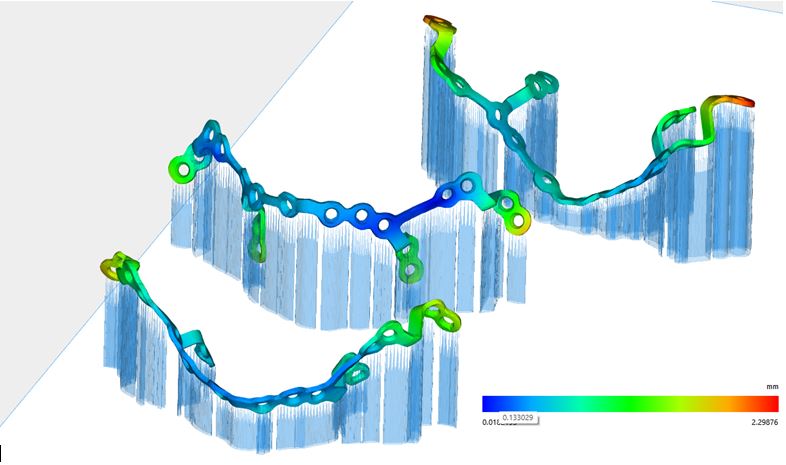
Для подтверждения результатов моделирования мы провели сравнение отклонения в конструкции деформированных деталей от исходной CAD-геометрии у смоделированных и напечатанных деталей. Как видно ниже, cмоделированные и напечатанные конструкции имеют одинаковый характер отклонений. Верхняя конфигурация содержит наибольшее геометрическое отклонение от исходной CAD-геометрии, а средняя – наименьшее отклонение.
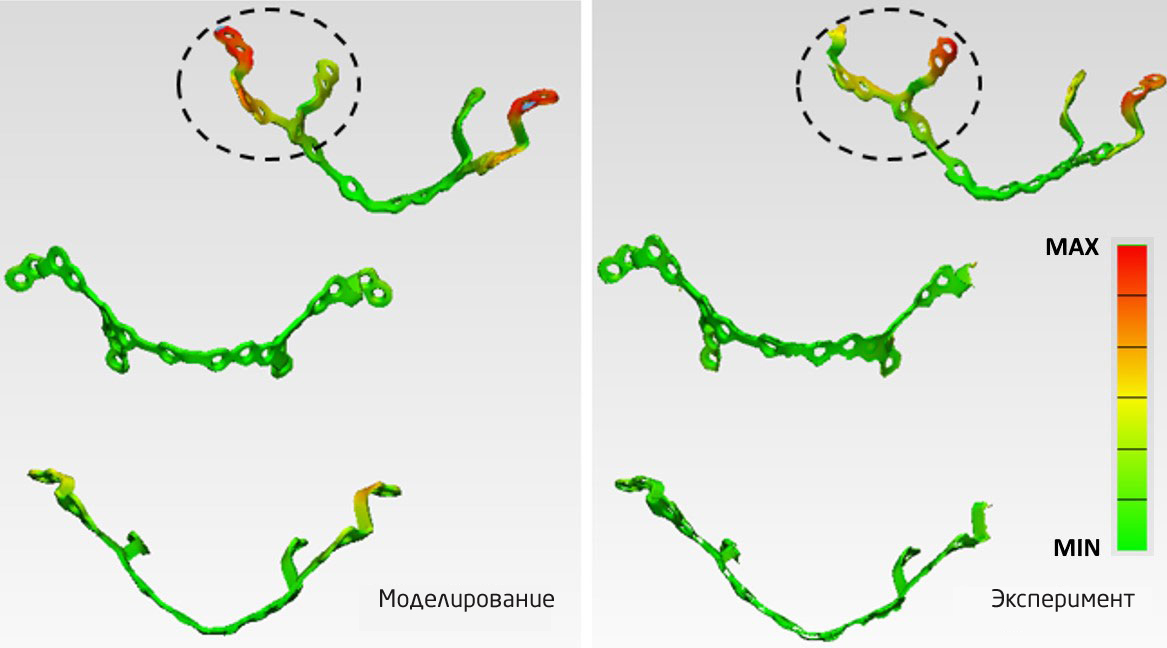
В поисках наименьшей деформации
В данном примере мы использовали конечно-элементное моделирование для быстрого прогнозирования глобальных деформаций трех различных конфигураций поддержек деталей черепно-челюстно-лицевого имлантата. Грубая вокселизация позволила быстро смоделировать и получить данные о качественных тенденциях деформации. Фактические тестовые образцы, напечатанные на 3D-принтере, подтвердили, что из трех предложенных в настоящем исследовании конфигураций средняя подверглась наименьшей деформации после удаления поддерживающей структуры.
Таким образом, вторая модель также подтверждает, что прогностическая способность моделирования является ценным инструментом для инженеров аддитивного производства. С использованием модуля моделирования Magics они могут оценивать свои проекты до этапа изготовления, что позволяет найти оптимальную ориентацию деталей и конфигурацию поддержки.
Обращаем Ваше внимание, что Materialise Magics не является медицинским программным обеспечением. Пользователь сам несет ответственность за утверждение производственного процесса и продукта к использованию в качестве медицинского изделия. Ортогнатические имплантаты компании Materialise защищены патентами EP 2398411, US 8,784,456, US9,247,972, US 9,339,279. Другие патенты находятся на рассмотрении.
* Метод внутренних напряжений (ISM) — это процедура моделирования, адаптированная на основе моделирования сварки для прогнозирования остаточных напряжений и деформации в процессе аддитивного производства. ISM упрощает сложный, трудоемкий термомеханический процесс аддитивного производства до простого квазистатического анализа, позволяя быстро и точно моделировать сложные аддитивные компоненты.
Материал предоставлен компанией Materialise. Оригинал статьи – по ссылке.
Статья опубликована 18.12.2018 , обновлена 19.04.2021