В автомобильном мире растет интерес к 3D-печати, причем производители используют аддитивные технологии и для прототипирования, и для изготовления конечного продукта. Очередная компания, совершившая прорыв благодаря 3D-печати, – Bugatti, производитель суперкаров Veyron и Chiron. Ее новый восьмипоршневой моноблочный тормозной суппорт примечателен по многим причинам: он первый, изготовленный на 3D-принтере, и самый большой в истории автомобильной промышленности. Также это самый крупный компонент из титана, который будет производиться аддитивным способом.
Суппорт был разработан в сотрудничестве с Laser Zentrum Nord, входящим в исследовательскую организацию Fraunhofer. Ожидается, что испытания транспортных средств с внедрением детали в серийное производство начнутся в первой половине этого года.
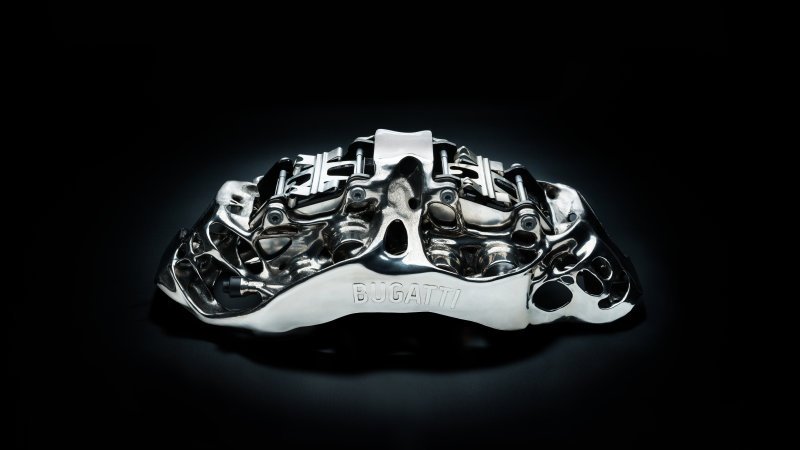
«Разработка транспортных средств – бесконечный процесс. И это особенно актуально в случае с Bugatti, – говорит Франк Гётцке, руководитель отдела новых технологий в департаменте технического развития Bugatti Automobiles S.A.S. – В ходе непрерывного процесса разработки мы все время продумываем, как новые материалы и методы могут улучшить текущую модель и как можно было бы сконструировать следующие автомобили нашего бренда. Наши технические характеристики часто близки к пределу физических возможностей, поэтому мы особенно требовательны. Вот почему Bugatti всегда находится по крайней мере на один шаг впереди других производителей в разработке технических решений».
При 3D-печати титаном суппорт примерно на 40% легче и одновременно прочнее алюминиевой детали
Bugatti использует самые мощные в мире тормоза в новом гиперкаре Chiron. Его тормозные суппорты изготовлены из высокопрочного алюминиевого сплава. Это самые крупные суппорты, установленные на серийном автомобиле, – восемь титановых поршней на каждом из передних суппортов и шесть на задних. Идея такого конструктивного решения заимствована из мотоспорта и сочетает минимальный вес с максимальной жесткостью.
Но это еще не все усовершенствования. Новый тормозной суппорт был напечатан на 3D-принтере из титанового сплава, обычно используемого в аэрокосмической промышленности, в авиационных или ракетных двигателях, высоконагруженных шасси и компонентах крыльев. По своим характеристикам сплав гораздо лучше алюминия – его предел прочности составляет 1,250 Н/мм2. Это означает, что квадратный миллиметр материала может выдерживать силу чуть более 125 кг без разрыва. Также он очень легкий: суппорт длиной 41 см, высотой 21 см и 13,6 см весит всего 2,9 кг. Для сравнения, вес алюминиевой детали – 4,9 кг, то есть при 3D-печати титаном суппорт становится легче примерно на 40% и одновременно прочнее.
Раньше титан невозможно было использовать в качестве материала для изготовления суппортов, так как из-за его высокой прочности подвергать титановую заготовку фрезеровке или штамповке чрезвычайно сложно. Однако 3D-печать – это совсем другая история. Технология не только позволяет создавать детали из титана, но и обеспечивает более высокую прочность, жесткость и более сложную геометрию.
Bugatti изготовила суппорт в Laser Zentrum Nord на высокопроизводительной SLM-машине, которая на момент запуска проекта была самым большим титановым 3D-принтером в мире.
«Laser Zentrum Nord – один из многих научных институтов, с которыми мы успешно сотрудничаем долгие годы, – отметил Гётцке. – Благодаря большому количеству проектов, выполненных в основном для авиационной промышленности, институт обладает всесторонним ноу-хау, особенно в области обработки титана, и предлагает надежные технологии».
За последние несколько лет ученые из Laser Zentrum Nord завоевали несколько престижных национальных и международных премий за инновации.
Доктор инженерных наук, профессор Клаус Эммельманн (Claus Emmelmann) ранее был управляющим директором Laser Zentrum Nord GmbH и возглавлял Институт технологий аддитивного производства Фраунгофера (Fraunhofer IAPT) после того, как Laser Zentrum Nord вошел в состав исследовательской организации Fraunhofer под этим названием в начале года. Он также возглавляет Институт лазерных и системных технологий (iLAS) Гамбургского технологического университета.
«Сотрудничество с Bugatti – ключевой проект и важная веха для нас, – говорит Эммельманн. – Мы были очень взволнованы, когда Bugatti связалась с нами. Я не знаю другого автопроизводителя, который предъявляет такие высокие требования к своему продукту. Мы были рады представившейся возможности».
Разработка суппорта заняла немного временuи – всего около трех месяцев. Bugatti прислала в Laser Zentrum Nord базовую концепцию, результаты моделирования прочности и жесткости, а также расчеты и расчетные чертежи единым пакетом. Затем Laser Zentrum Nord выполнила моделирование процессов, разработку поддерживающих структур и осуществила 3D-печать. Bugatti произвела финишную обработку детали.
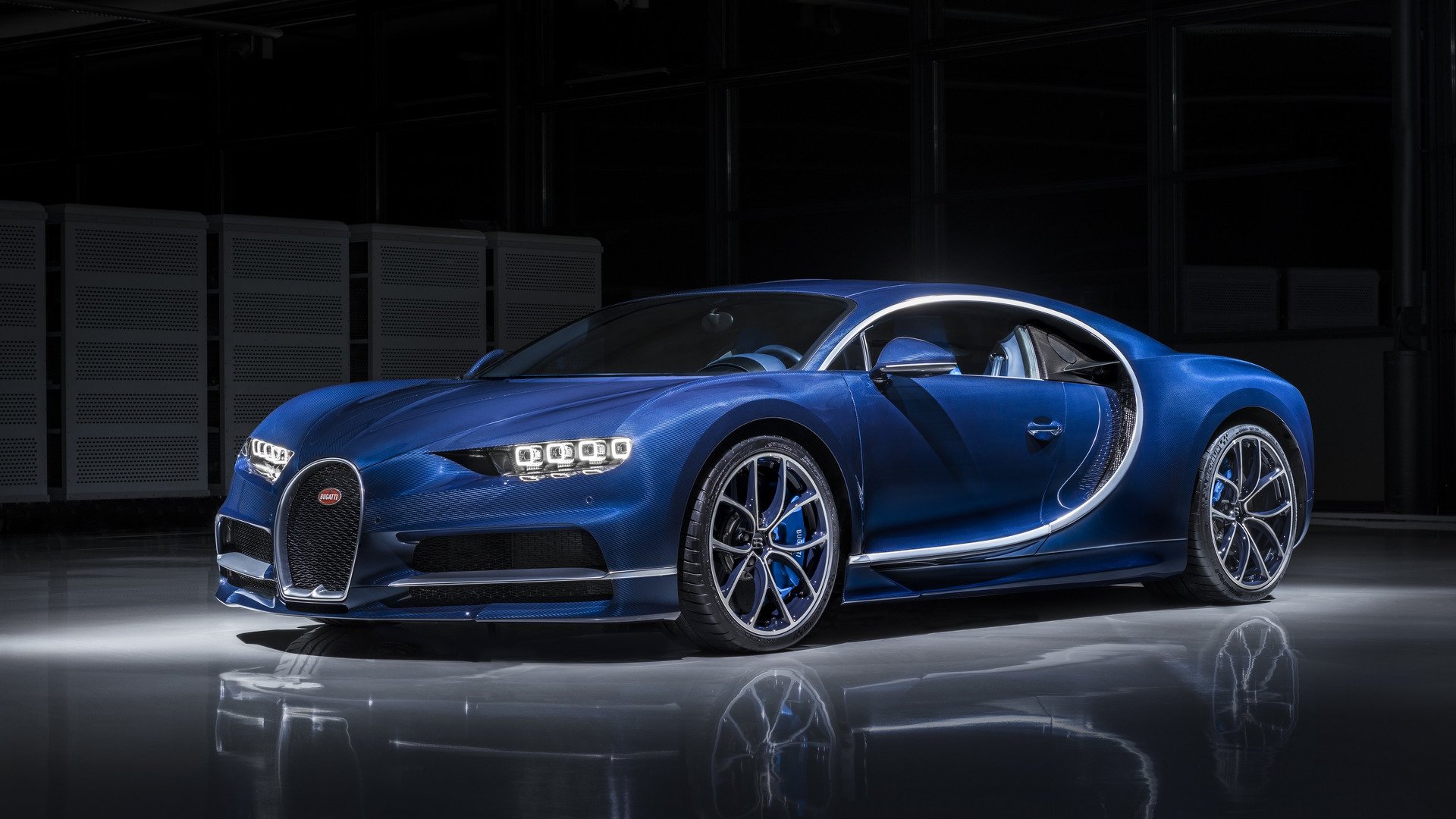
3D-принтер оборудован четырьмя лазерами, и для печати тормозного суппорта потребовалось 45 часов. Общее количество печатных слоев, необходимых для изготовления детали, составляет 2,213. По завершении процесса 3D-печати деталь была подвергнута термообработке в печи при температуре до 700° C для устранения остаточного напряжения и обеспечения формоустойчивости. Затем поддержки были удалены, а поверхность детали была отшлифована механическими, химическими и технологическими способами, что значительно улучшило ее усталостную прочность. Контуры функциональных поверхностей были затем обработаны на станке с ЧПУ в течение еще 11 часов.
В результате Bugatti получила суппорт превосходной формы с толщиной стенки от одного до четырех миллиметров.
«Это был очень трогательный момент для всей команды, когда мы держали в руках наш первый титановый суппорт, напечатанный на 3D-принтере, – говорит Гётцке. – По объему это самый большой функциональный компонент, изготовленный из титана по аддитивной технологии. Каждый, кто видит эту деталь, удивляется тому, насколько она легкая, несмотря на большие размеры. С технической точки зрения это очень впечатляющий тормозной суппорт, да и выглядит он великолепно».
Статья опубликована 21.02.2018 , обновлена 01.10.2024