Задачи мониторинга | Виды 3D‑оборудования | Проекты: 1. Платформа компрессора 6600 | 2. Опоры крепления электродвигателей | 3. Элементы запорной арматуры | 4. Корпус ротора паровой турбины | 5. Редуктор валоповоротного устройства экструдера | Наши услуги
В нашем блоге уже разобраны многие задачи и проекты, подтверждающие преимущества технологии 3D‑сканирования перед традиционными измерительными инструментами. Быстродействие, высокая точность и надежность данных, которые обеспечивают сканеры в процессах контроля качества и обратного проектирования, – факторы, жизненно необходимые для современных производств.
Сегодня мы рассмотрим несколько примеров, когда лазерные 3D‑сканеры позволяют быстро и эффективно осуществлять системный мониторинг состояния технологического оборудования на производстве.
В ходе мониторинга решаются следующие задачи:
-
контроль геометрии оборудования и резервуаров;
-
экспертиза коррозийного и эрозийно-абразивного износа;
-
инжиниринг проблемных объектов с прямым и обратным проектированием.
Процесс мониторинга и ревизии технологического оборудования состоит из несколько этапов. Прежде всего, это собственно 3D‑сканирование, в результате которого мы получаем цифровую модель и подготавливаем ее к загрузке в специализированное программное обеспечение контроля качества (например, Geomagic Control X, PolyWorks Inspector или PointShape Inspector).
В ПО мы можем выполнять различные измерения, сравнивать полученные данные с CAD‑моделью и на выходе получать метеорологический отчет в разных форматах. На основе этого отчета ремонтная служба принимает решение: если изделие можно эксплуатировать дальше, намечается план ремонта; если нет, оно отбраковывается.
Виды 3D‑оборудования
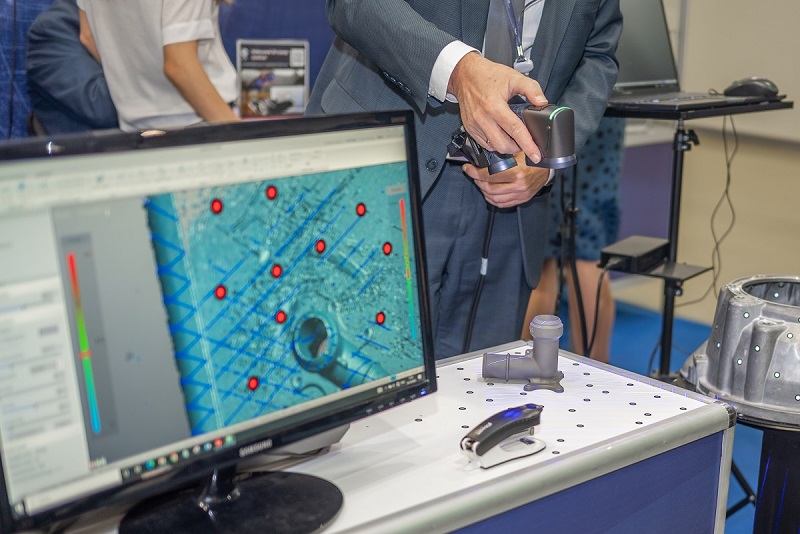
Наша компания имеет в своем арсенале и поставляет решения на основе всех доступных на сегодня технологий лазерного 3D‑сканирования. Это:
-
ручные лазерные сканеры, которые позволяют оцифровывать объекты от 20‑30 сантиметров до 4 метров;
-
портативные лазерные сканеры с оптическими трекерами, предназначенные для больших объектов – до 10‑12 м;
-
наземные (геодезические) лазерные сканеры для измерения помещений, зданий и ландшафтов;
-
лазерные трекеры для высокоточных измерения крупных деталей, узлов техники, машин.
Читайте статью RigelScan Super: безупречный 3D‑сканер для реверс-инжиниринга крупных деталей
Проекты мониторинга оборудования с использованием 3D‑сканирования
1. Платформа компрессора 6600
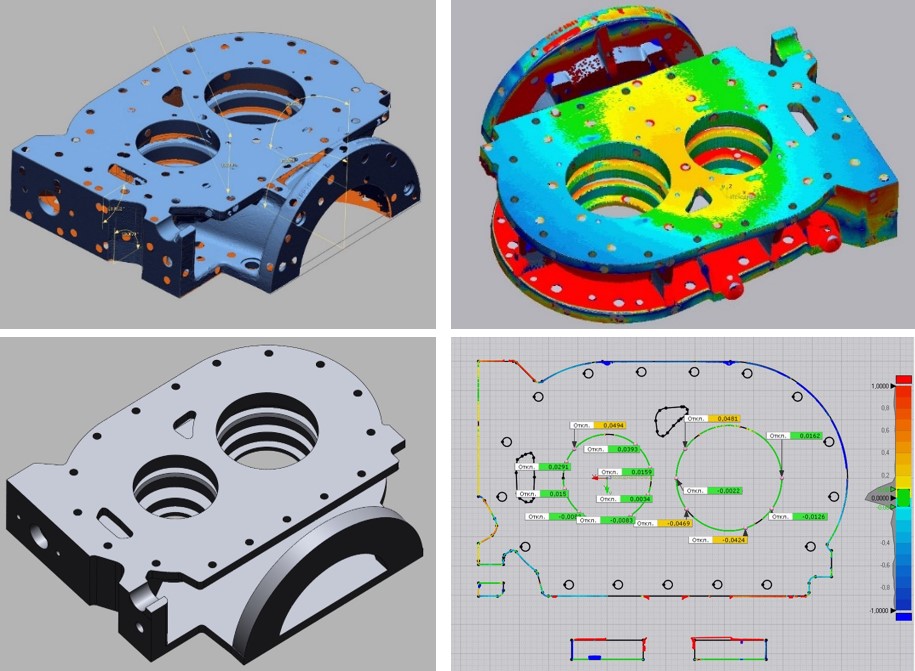
Задача
При проведении ремонта компрессора 32‑K‑6600 потребовалось проверить соосность и цилиндричность отверстий, а также перпендикулярность поверхностей.
Результат
-
Восстановлены необходимые элементы платформы для их анализа и сравнения с данными сканирования.
-
Проведен контроль геометрии, отчет предоставлен коллегам для дальнейшей работы.
Экспертный комментарий
Понятно, что если внутри компрессора используются охлаждающие жидкости, то замена этих жидкостей или расходных материалов определена производителем оборудования. Также необходимо выяснить, что происходит с геометрией корпусных деталей, поскольку в процессе эксплуатации они подвергаются нагрузкам, которые приводят к изменению геометрии.
В ходе планово-профилактического ремонта компрессора произведено 3D‑сканирование привалочной плоскости с двумя посадочными шейками под подшипники. В результате анализа данных получена цветовая карта, которая наглядно показывает все имеющиеся отклонения.
На правом верхнем изображении (см. выше) мы видим, что правая и левая части боковины – в синем градиенте: это говорит о том, что деталь меньше, чем должна быть. Оранжево-желтое пятно по центру, наоборот, показывает, что деталь больше по сравнению с исходной. Явный признак того, что мы имеем дело с линейным короблением.
Проанализировав данные, можем померить, насколько велико коробление, и выбрать тот или иной метод восстановления оборудования.
2. Опоры крепления электродвигателей
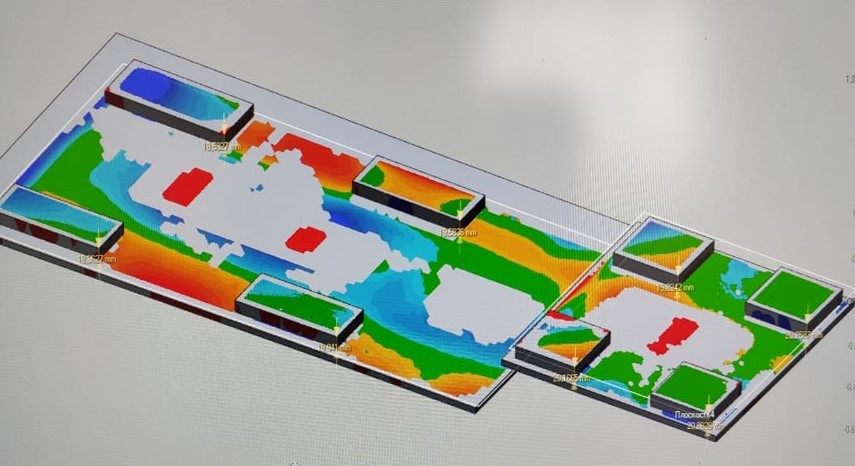
Задача
При монтаже электродвигателей возникла проблема с точным выставлением плоскопараллельности опор для крепления электродвигателя, что приводило к излишней вибрации при работе оборудования.
Результат
-
Получены данные сканирования с точностью до 0,1 мм.
-
Предоставлен отчет с указанием отклонения в изготовлении платформы крепления.
-
Значительно сокращены сроки монтажа оборудования.
Экспертный комментарий
Подобная задача встречается достаточно часто – не только на действующих предприятиях, но и на новых, где используются площадки под анкерные болты для крепления оборудования. Особенно это касается тяжелого оборудования – электродвигателей, корпусов насосов и турбин. Площадки изготавливаются на производстве и затем при заливке бетонных полов или фундаментов туда «вживляются». Добиться плоскостности при решении такой задачи – серьезная проблема.
Любое оборудование, как правило, имеет четыре точки опоры. Как известно, через четыре точки плоскость априори не проходит, поэтому иногда возникает так называемая «воздушная пятка» – когда одна опора оборудования нежестко прикреплена к полу, усиление затяжки болтов приводит к деформации корпуса, а это может иметь губительные последствия.
Чтобы выявить дефекты таких площадок, то есть непараллельность оснований для крепления оборудования, был использован ручной лазерный 3D‑сканер. Сканирование заняло 20 минут, по полученной карте отклонений можно понять, какая опора ниже, какая выше и какая в норме.
3. Элементы запорной арматуры
Задача
На время остановочного ремонта требовалось в сжатые сроки провести замеры определенных узлов корпуса арматуры.
Результат
Сканирование проведено в цеху в перерывах между работами по корпусу. В течение двух часов получены данные о нужных элементах и проведены ремонтные работы. Данные были предоставлены конструкторам в последующие рабочие дни.
Экспертный комментарий
Запорная арматура также нуждается в мониторинге и ревизии. При выполнении планово-профилактического ремонта с трубопровода был демонтирован фитинг, заменены все манжеты и прокладки. Одновременно, пока была возможность, провели лазерное сканирование с целью понять, что происходит с присоединительными фланцами – их плоскопараллельность, перпендикулярность верхнего фланца боковым и так далее.
Полученная информация дает возможность достаточно быстро принять решение по устранению того или иного дефекта технологического оборудования.
Рекомендуем материал 5 причин, почему для контроля крупных отливок необходим 3D‑сканер
4. Корпус ротора паровой турбины
Задача
Требовалось проверить плоскостность корпуса и крышки паровой турбины из‑за течи через прокладку. Ранее проводилась зачистка, выравнивание, шлифовка традиционным способом, но проблему решить не удалось.
Результат
Получена карта отклонений с точностью до 0,1 мм и выявлены места с наибольшей деформацией, после чего на основе данных сканирования произведена шлифовка. В итоге течь была устранена.
Экспертный комментарий
При выполнении планово-предупредительного ремонта разъем паровой турбины был подвергнут стандартной механообработке, но даже после восстановления не была устранена течь через стык двух корпусов паровой турбины.
Для решения проблемы проведены сканирование привалочных плоскостей турбины и анализ данных. Карта отклонений показала, что в одном месте действительно есть просвет (синяя зона). Было принято решение о локальном шабрении в нескольких местах этой привалочной плоскости, что привело к устранению дефекта.
5. Редуктор валоповоротного устройства экструдера
Задача
Редуктор вышел из строя, частично был разрушен. Некоторые элементы конструкции, такие как валы и шестерни, имеют сложную геометрию. При помощи обычных средств измерений произвести контроль геометрии и замеры не представлялось возможным.
Результат
-
Получены цифровые данные отдельных единиц деталей.
-
Произведен контроль необходимых параметров и размеров, которые затем переданы в отдел КТО для разработки КД и дальнейшего изготовления.
Экспертный комментарий
На многих предприятиях используются достаточно большие номенклатуры редукторов. Для анализа их износа также есть смысл применять лазерные 3D‑сканеры. После разборки всего редуктора мы можем его отсканировать и проанализировать:
-
соосность шеек под подшипники;
-
параллельность осей этих шеек относительно друг друга;
-
износ зубчатых колес и т. д.
В соответствии с этими данными, время получения которых варьируется от нескольких минут до нескольких часов, в зависимости от габаритов изделия, можно принимать решение:
-
редуктор еще послужит, но нам нужно, к примеру, расточить третью шейку под подшипник, загильзовать новой втулкой, потом расточить, и она еще какое‑то время будет функциональна;
-
либо, если такой возможности нет из‑за полного износа, просто ее забраковать и поставить новый корпус насоса.
Сталкиваетесь с подобными проблемами на производстве? Эксперты iQB Technologies помогут подобрать наилучшее решение и внедрить 3D‑оборудование и ПО на вашем предприятии.
Весь комплекс услуг на базе 3D‑технологий доступен в центре экспертных решений TWIZE. Оперативно выполним контроль геометрии, реверс-инжиниринг, разработку РКД, анализ металлов и многие другие задачи.Статья опубликована 16.05.2025 , обновлена 01.08.2025