Американская фирма Idaho Steel, которая производит и обслуживает машины для переработки картофеля, не слишком отличается от других компаний во всем мире – за исключением того, что обслуживает уникальную отрасль и применяет 3D-печать, что сокращает время на изготовление уникальных деталей и компонентов.
Idaho Steel использует 3D-принтер 3D Systems ProX 500, работающий по технологии селективного лазерного спекания (Selective Laser Sintering, SLS). Он позволяет печатать готовые к использованию функциональные детали и узлы для аэрокосмических, автомобильных, медицинских, бытовых и промышленных машин. Для изготовления этих компонентов в принтере используется материал DuraForm ProX на основе прочного нейлона. Конечная продукция по своим характеристикам сопоставима или превосходит детали, изготовленные по технологии литья под давлением.
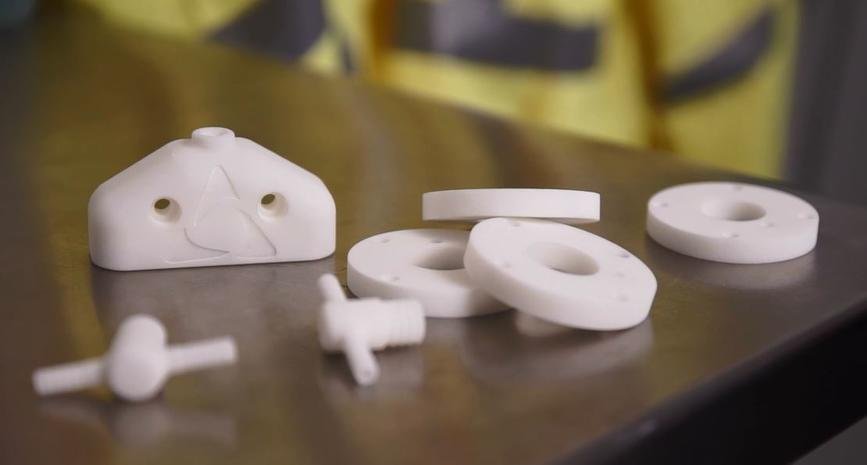
«3D-печать по технологии селективного лазерного спекания обеспечивает превосходную прочность и долговечность продукции, – говорит Джон Кристенсен, менеджер по маркетингу и продажам в Idaho Steel. – Те, кто не знаком с технологией, не могут даже представить себе, что напечатанные из твердого пластика детали обладают повышенной прочностью и спроектированы с использованием способов, невозможных при традиционном подходе».

«Установка может работать ночью или в выходные дни, при этом для создания поршней требуется всего от трех до четырех часов ручного труда, – говорит Кристенсен. – 3D-печать не только экономит время, но и высвобождает станки с ЧПУ, которые выполняли бы ту же работу на протяжении 25 дней». Формовочная вставка и поршень печатаются на 3D-принтере в виде единого элемента с использованием материала DuraForm ProX.
Быстрая поставка, повышенное качество, настройка, надежность — эти преимущества выделяет любая машиностроительная компания независимо от того, какую продукцию она производит. Однако у Idaho Steel есть одно отличие. Ее генеральный директор Алан Брэдшоу говорит: «Мы больше не ограничены стандартными и традиционными инструментами. Наша проектная группа в своем творчестве ограничена только воображением».
Статья опубликована 06.09.2017 , обновлена 19.04.2021