В последние годы многие отрасли промышленности в полной мере оценили преимущества аддитивных технологий и эффективно внедряют их в производственный процесс. Все больше предприятий по всему миру, занятых в аэрокосмическом, автомобильном, машиностроительном, нефтегазовом секторах, в медицине и ювелирном деле, извлекают выгоду из поразительных возможностей, которые открывают новые перспективные методы.
Судостроение – отрасль, которую принято считать консервативной, однако и она неизбежно вступает в мир 3D. Трехмерное сканирование и печать обладают уникальным потенциалом, так как позволяют воспроизводить сложнейшие пространственные формы и объекты.
Для судостроения и судоремонта это – возможность добиться значительных результатов в оптимизации производственного процесса. Аддитивные технологии позволяют снизить себестоимость продукта, уменьшить расходы, сэкономить время производства и, в конечном итоге, увеличить доходы предприятия. Владельцы бизнеса, технологи, конструкторы, инженеры-судостроители осознают, что многие традиционные методы устарели и препятствуют воплощению передовых проектов. 3D-технологии диктуют потребность в кардинальных переменах, которые заставят пересмотреть существующие стандарты, нормативы, требования к безопасности и экологии.
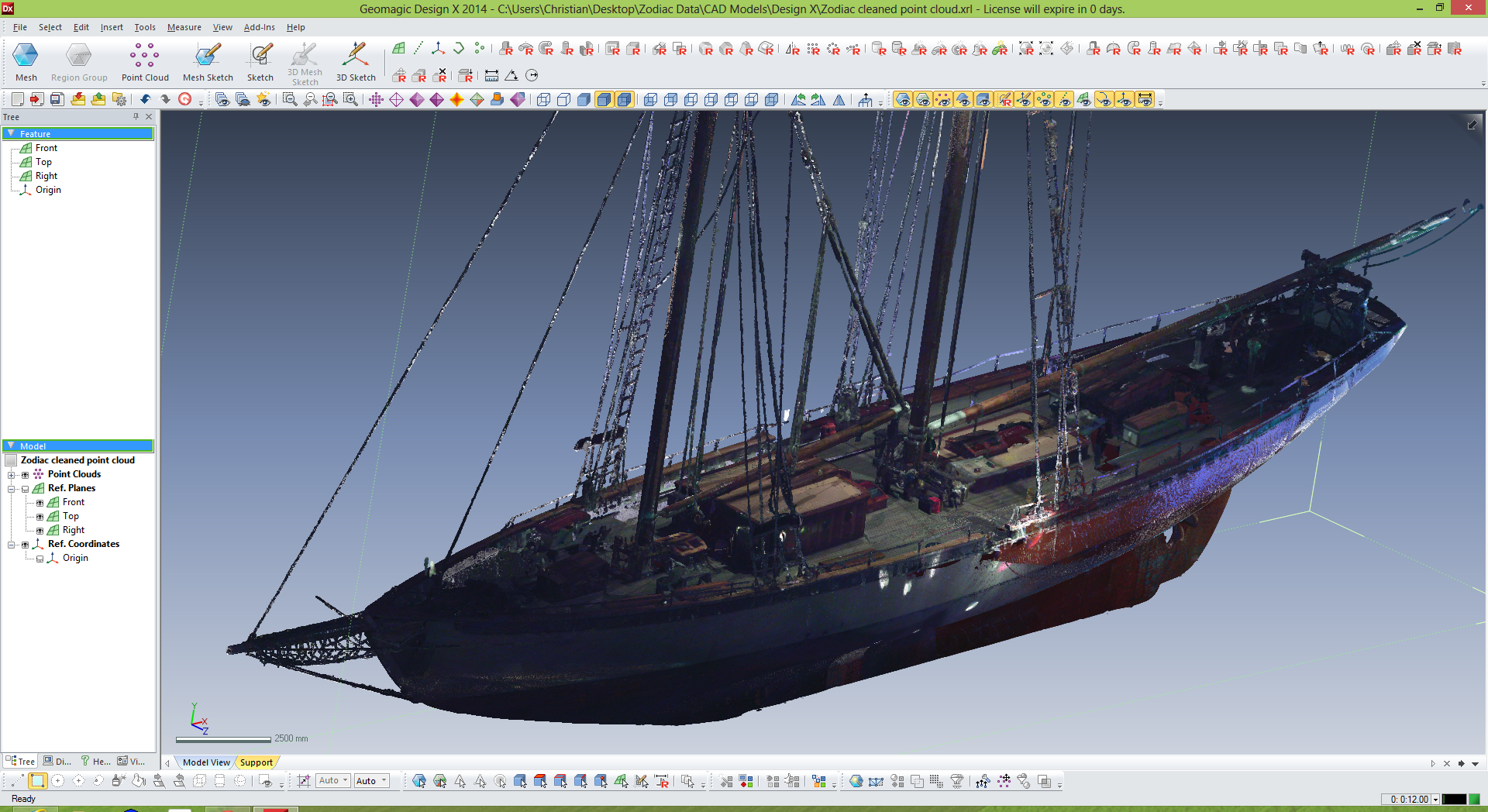
3D-сканеры в судостроении и судоремонте используются для решения задач контроля геометрии, эксплуатационного контроля, контроля оснастки, а также реверс-инжиниринга. Методами 3D-сканирования удается успешно решать задачи таких процессов, как производство, ремонт и модернизация корпусов, сборочные и сварочные работы, прокладка внутренних коммуникаций, механомонтажное производство. В результате, благодаря высокой точности измерений, удается оптимизировать узлы, детали и конструкции судна, сократить сроки изготовления и повысить качество конечного продукта.
Рассмотрим практический пример. Была поставлена задача произвести 3D-сканирование палубы, пульта управления, силовой установки корабля с целью контроля качества и геометрии оборудования, а также вычисления повреждений на судне. Для работы с такими масштабными объектами, как корпус, используются промышленные сканеры-дальномеры. С помощью дальномера Surphaser было выполнено сканирование помещений и оборудования. После анализа данных в программном обеспечении была создана детализированная твердотельная модель объекта с возможностью его моделирования и выявлены отклонения сканируемого объекта от математической модели.
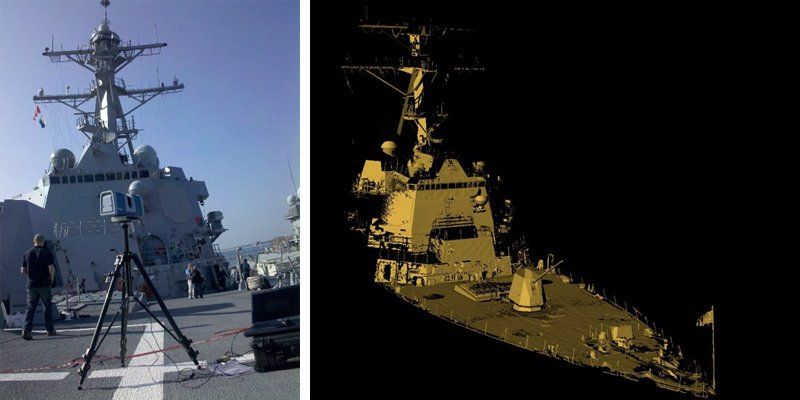
К сожалению, случаи конструкторских просчетов, выполняемых классическими методами, нередки и сегодня, и привести они могут к самым серьезным последствиям. К примеру, вес испанской подлодки S-80 (первой из четырех запланированных к постройке), превысил допустимый почти на 100 тонн, из-за чего она не смогла подняться на поверхность после погружения. 3D-технологии полностью исключают подобные фатальные промахи.
Что касается 3D-печати, то она способна произвести в судостроении настоящую революцию. Сейчас на 3D-принтерах печатаются небольшие детали, прототипы, выполняется ремонт деталей. В перспективе они смогут решить такую насущную проблему, как транспортировка и хранение запчастей. Неисправную деталь можно будет просто отсканировать и напечатать прямо на борту корабля, а материалы для печати будут храниться на судне в компактном виде. Таким образом, сократится логистическая цепочка, у судна уменьшится лишняя нагрузка и увеличится полезная площадь.
Ведущие судостроители (к примеру, Hyundai) инвестируют средства в серийную 3D-печать деталей. Фирма CJR Propulsion (Великобритания), которая занимается изготовлением кастомизированного рулевого оборудования и гребных винтов, – одно из многих судостроительных предприятий, печатающих прототипы готовых изделий и тестирующих модели с помощью 3D-принтеров.
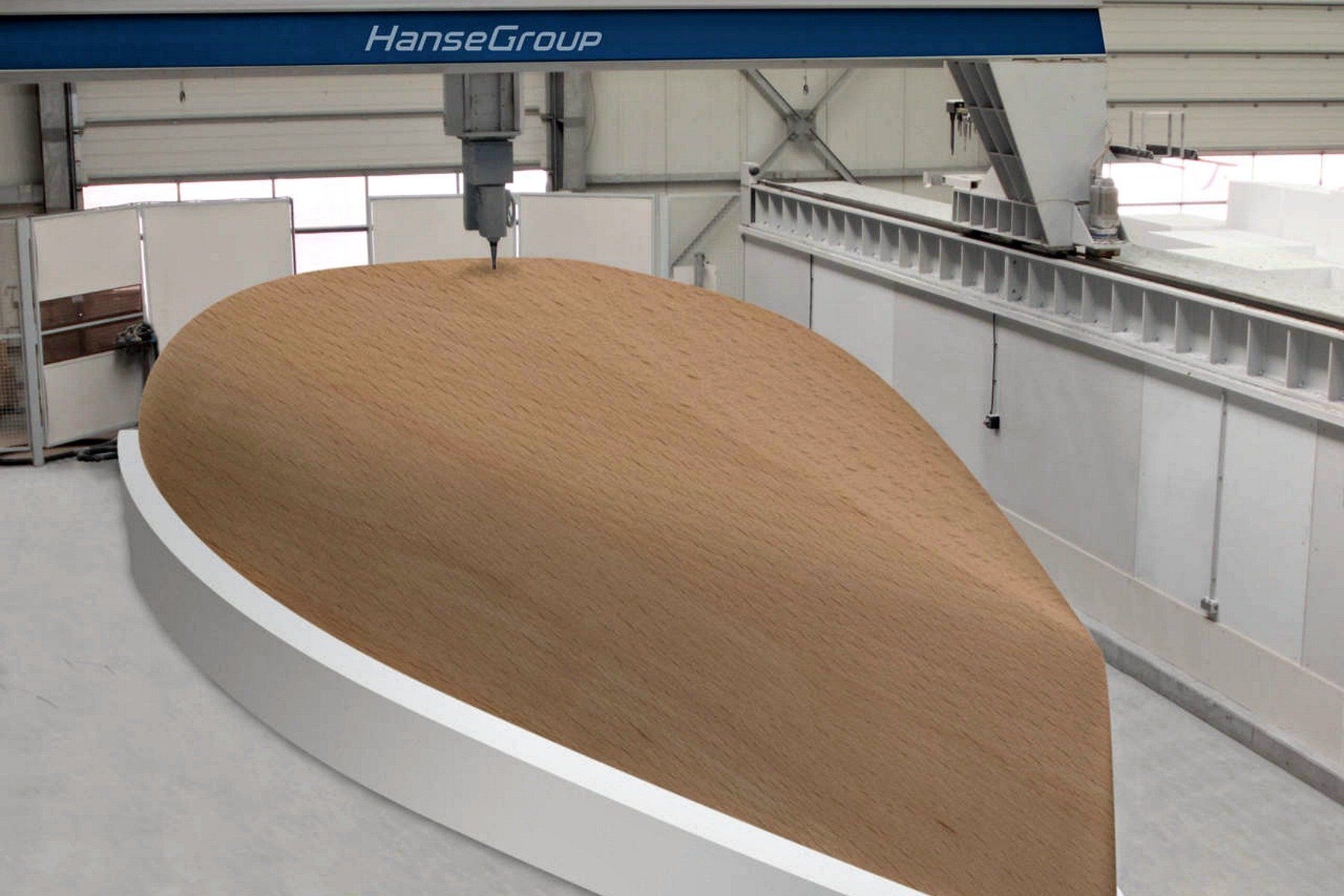
Немецкая компания HanseYachts AG, крупный производитель морских парусных яхт, запустила интересный проект: был разработан 20-метровый 3D-принтер для печати корпуса судна с применением полимерного композита с древесным наполнителем. По расчетам компании, корпус будет отличаться повышенной прочностью, удастся сократить производственный цикл и удовлетворить индивидуальные запросы заказчиков.
Российское объединение «Пульсар» применяет 3D-технологии в проектировании, разработке и производстве винтовых установок. Уже сейчас проходят испытания установок, полностью спроектированных в 3D; мастер-модели и отливки для них изготовлены с применением аддитивных технологий.
Действующие судостроительные нормативы (и в первую очередь это касается России) во многом по-прежнему ориентированы на проектирование на бумаге. В обозримом будущем аддитивные технологии дадут возможность интегрировать программные средства в единую систему, упростят процесс обмена данными в процессе проектирования, сократят время работы специалистов, устранят риск критических ошибок, что позволит повысить качество изготовления, надежность и безопасность судов.
Рынок с оптимизмом встречает всё новые технологические достижения. Полноценное внедрение 3D-технологий в производственный цикл в судостроении – вопрос времени. В мире ведутся активные научные исследования по их использованию в ВМФ. Сегодня есть определенные ограничения, связанные с аддитивным производством, – например, высокая стоимость оборудования и материалов, небольшой выбор материалов, крупные первоначальные вложения, – но и эти проблемы со временем будут стоять менее остро. Потенциал аддитивных технологий для судостроения поистине огромен.
Статья опубликована 26.06.2017 , обновлена 03.03.2022