Вам не составит труда рассердить Фрэнка Зиберну, директора по НИОКР в международной производственно-технологической компании Bi-Link (Блумингдейл, Иллинойс). Просто скажите ему, что поставленную задачу решить невозможно. За последние три года Зиберна и его коллеги из Bi-Link наслушались об ограничениях 3D-печати при создании пресс-форм и готовых деталей: медленно, качество оставляет желать лучшего, материалы нельзя использовать для серийного производства, формы не выдерживают нагрева или высокого давления. Однако все доводы скептиков опровергнуты.
Продукцией Bi-Link пользуются производители электроники и медицинского оборудования по всему миру. Сейчас для изготовления пресс-форм и опытных образцов Bi-Link использует три принтера 3D Systems. 3D-принтер ProJet 3500 HD Max предназначен для создания функциональных фотополимерных компонентов для проектирования и изготовления деталей. Для печати на нем используются специально разработанные 3D Systems материалы VisiJet® M3 — фотоотверждаемые пластмассы различных цветов, разной степени прозрачности и прочности.
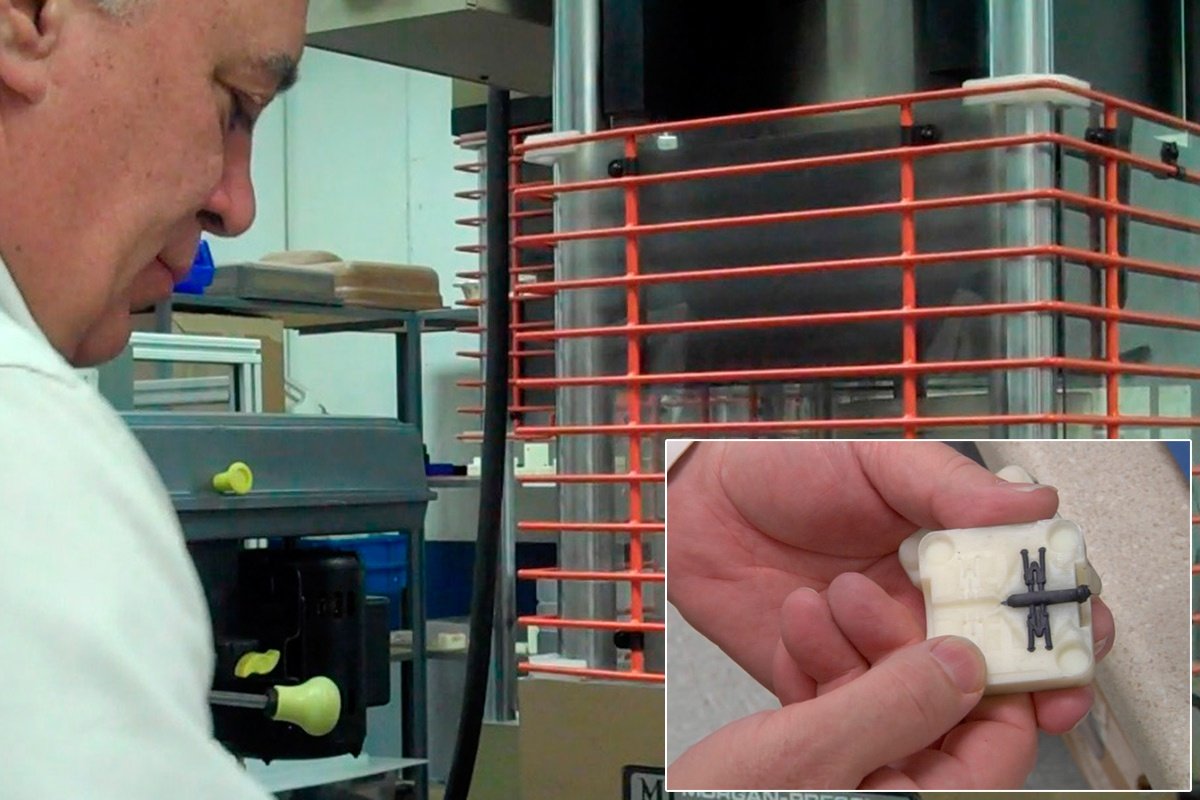
По словам президента Bi-Link Рэя Зиганто, высокое качество 3D-печати, современные материалы и собственные методы термической закалки — вот факторы, благодаря которым прочность готовых форм превышает прочность исходного материала.
Пресс-формы, вставки для литья, гибридные инструменты, термоформованные детали любой сложности — в Bi-Link могут изготовить любое изделие длиной до 25 см. В стандартной пресс-форме, созданной на 3D-принтере и закаленной по технологии Bi-Link, можно отлить 200 деталей. Клиент, отправивший Bi-Link CAD-файл утром, уже на следующий день сможет отливать детали в форме, напечатанной на 3D-принтере.
«Клиенты любят работать с нами, — говорит Зиберна. — Обычно им приходится ждать две-три недели, чтобы получить только оснастку, не говоря уже об опытных образцах. На 3D-принтере мы сделали для одного заказчика четыре варианта детали за шесть дней, и на основе каждого варианта отправляли ему 10–12 деталей ежедневно.
Таким образом, трехмесячный цикл проектирования и испытаний сжался до недели. Что касается медицинского оборудования, мы создаем второй или третий вариант прототипа до того, как конкуренты разработают хотя бы один».
Статья опубликована 30.08.2017 , обновлена 19.04.2021