ЗАДАЧА: снизить стоимость производства серии металлических вакуумных захватов
РЕШЕНИЕ: доработка конструкции под аддитивные технологии, уменьшение объема захвата, увеличение количества деталей, выращиваемых за одну сессию печати
МЕТОД: оптимизация конструкции, изготовление из металла
РЕАЛИЗАЦИЯ: проектно-инжиниринговые услуги, сертифицированное производство методом 3D-печати металлом
Создание технологической оснастки – одна из сфер, где широко и успешно применяются аддитивные технологии. Отличным примером стала оптимизация конструкции вакуумного захвата, который используется на производствах для поднятия легких цилиндрических объектов. Тесное сотрудничество компании Materialise с заказчиком позволило добиться значительных улучшений, в том числе снижения себестоимости в два раза.
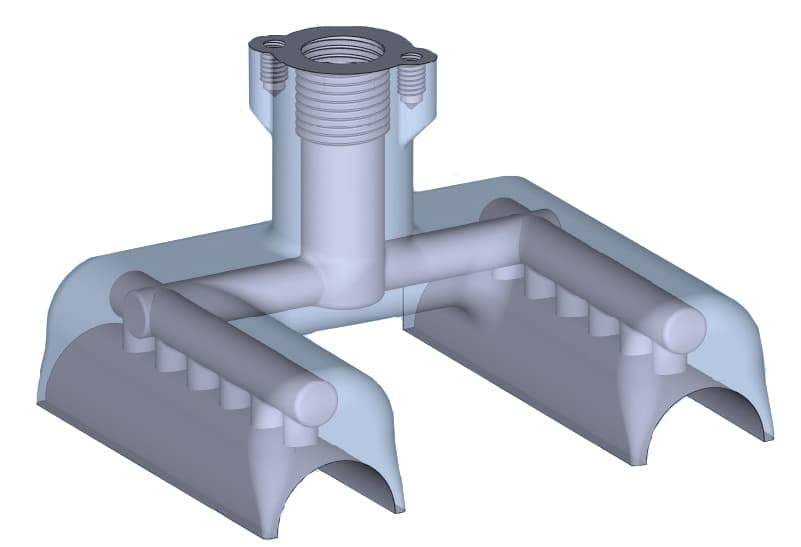
Первоначально конструкция захвата была разработана для производства с помощью традиционной технологической оснастки. Внутренние каналы были образованы пересекающимися цилиндрическими отверстиями, просверленными в разных направлениях. Выходы отверстий на поверхность закрывались герметичными заглушками. Во избежание роста себестоимости деталь производилась без последующей фрезеровки, которая могла бы сократить ее объем.
Читайте также: Аддитивное производство формовочной оснастки из полимерных и композитных материалов
Заказчик уже имел опыт 3D-печати пластиковых деталей и знал, насколько она может сократить расходы и повысить эффективность, особенно при изготовлении оснастки. Тем не менее – как и всегда, когда речь идет о модернизации, – сначала нужно было понять, целесообразно ли использовать 3D-печать для изготовления этого захвата. Сравнение требований к детали с возможностями 3D-печати привело к ожидаемому выводу: всех поставленных целей можно добиться с помощью аддитивного производства и свободы проектирования, которую оно открывает.
Вот каких результатов удалось добиться благодаря металлическому 3D-принтеру:
- сокращение производственных затрат;
- снижение веса;
- ускорение операции захвата;
- лучшее распределение вакуума;
- минимизация утечек.
В качестве материала заказчик выбрал алюминий. Он более устойчив к износу, чем пластик, но при этом имеет небольшой вес, а также дает возможность получать гладкие поверхности, которые легко очищаются. Последнее условие было важным для заказчика, поскольку облегчило бы чистку захвата. Кроме того, использование алюминия экономически выгодно для мелкосерийного производства дорогостоящих деталей небольших и средних габаритов.
Заказчик разработал модель для 3D-печати и заказал изготовление детали в компании Materialise. Специалисты Materialise по проектированию быстро поняли, что модель можно улучшить. Проект заказчика уже обеспечивал значительное снижение веса, но производственные затраты были выше, чем при первоначальном способе изготовления, а внутренние каналы не были аэродинамически оптимизированы.
Рекомендуем бесплатно скачать экспертный материал: 7 вопросов, которые нужно задать перед покупкой металлического 3D-принтера
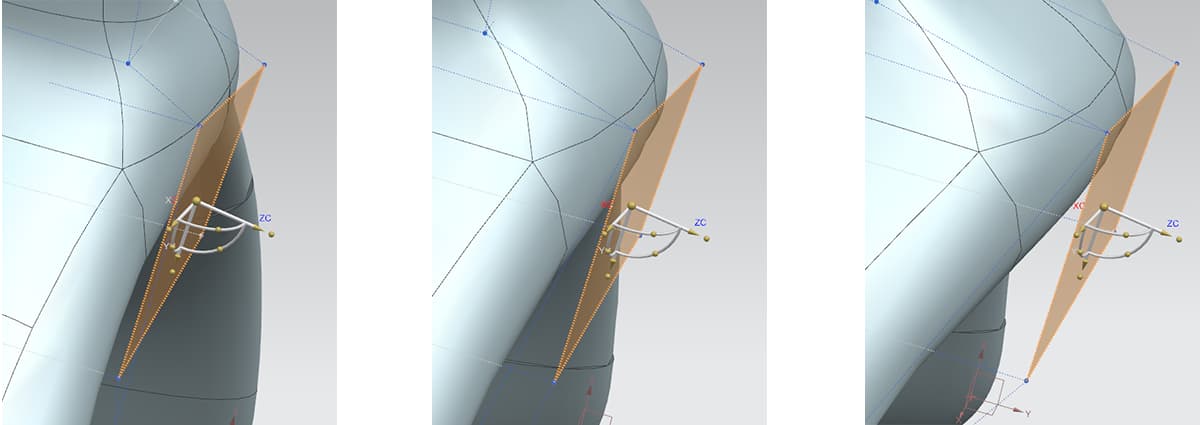
Получив одобрение заказчика, инженеры Materialise приступили к дальнейшей оптимизации модели, используя модуль Siemens NX Realize Shape, который позволяет моделировать произвольные формы. Затем с помощью программного обеспечения Materialise Magics эксперты оптимизировали геометрию модели для 3D-печати. Они использовали функцию предварительного просмотра, которая отображает для выбранной ориентации детали области, требующие наличия поддержек. Это позволило убедиться в том, что стенки детали можно печатать без создания дополнительных поддержек внутри нее. Проектировщики расположили элементы детали так, чтобы свести к минимуму количество поддерживающих структур и оптимизировать качество контактных поверхностей областей захвата. Также было важно, чтобы новая конструкция обеспечивала равномерное распределение вакуума по всем точкам захвата для более надежной фиксации объектов.
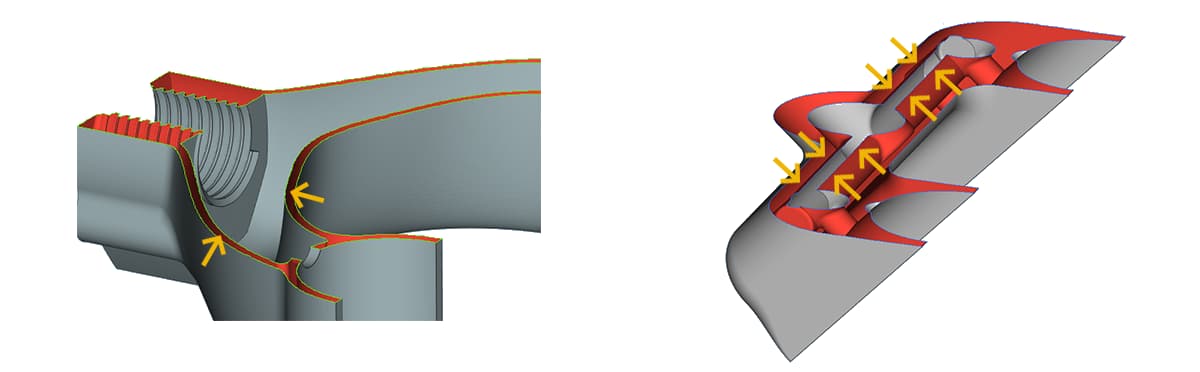
Затем инженерный отдел Materialise устранил линии напряжения, сделав изменение толщины материала более плавным. Это очень важно, поскольку линии напряжения отрицательно влияют не только на внешний вид, но и на механические свойства детали.
Таким образом, общий объем и вес детали были сокращены до необходимого минимума.
Вес и объем напрямую влияют на себестоимость, поскольку, в отличие от традиционных способов производства, большая часть не использованного при 3D-печати материала может быть собрана и использована повторно. Иными словами, используется лишь тот материал, который непосредственно идет на создание самой детали и поддержек. Небольшое количество поддержек и минимальная область контакта в тех частях устройства, на которые не приходится серьезная нагрузка, сокращают временные и финансовые затраты на удаление поддержек и постобработку. Все, что остается после печати – нарезать резьбу.
Необходимо оптимизировать конструкцию изделия, чтобы снизить издержки? Обратитесь в iQB Technologies: мы оценим целесообразность применения 3D-технологий и предложим готовое решение! Возможен заказ услуг тестовой 3D-печати и 3D-сканирования
-und-im-Anschnitt-werden-die-support-freien-.jpg)
По сравнению с моделью для 3D-печати, созданной заказчиком, было достигнуто дополнительное преимущество: количество деталей, выращиваемых за одну сессию печати, увеличилось с 28 до 46. Новая геометрия позволила эффективнее размещать детали на платформе построения, что также уменьшило себестоимость.
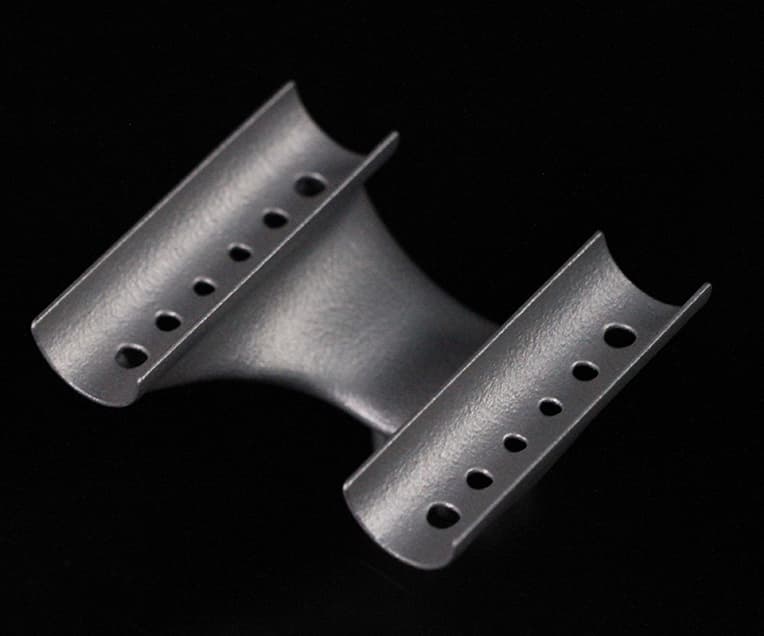
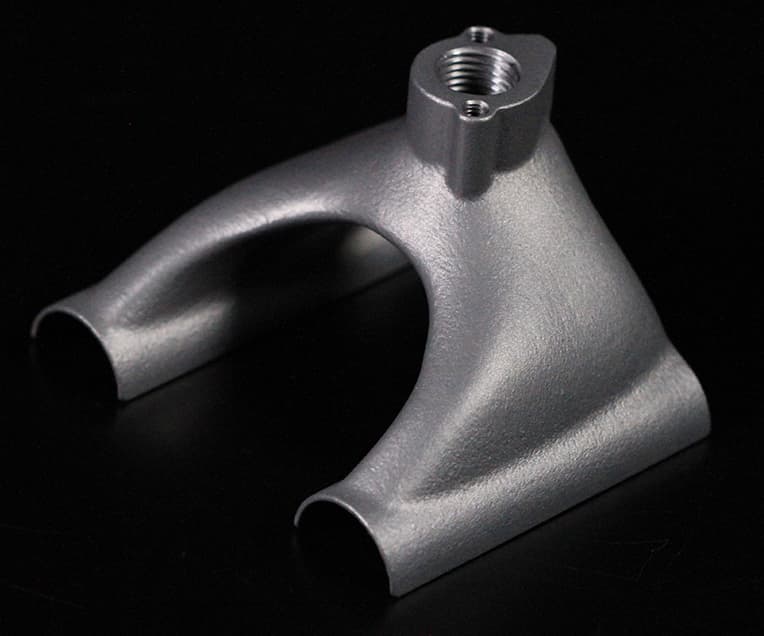
Сравнение объема и себестоимости между исходной деталью, моделью заказчика и окончательным проектом показывает, какой прогресс был достигнут. Объем модели заказчика для 3D-печати уже был на 79% меньше объема исходной детали, однако объем доработанной Materialise конструкции составляет всего 6% от первоначального!
Себестоимость детали снизилась с 300 евро за произведенную традиционным способом до 150 за версию, напечатанную на 3D-принтере. Первый проект для 3D-печати, разработанный заказчиком, был бы на 6% дороже в изготовлении.
Пример с вакуумным захватом показывает, как аддитивное производство и оптимизацию модели можно использовать для создания более дешевых, легких и функционально оптимизированных деталей, а также демонстрирует решающее влияние качества перепроектирования на прибыльность проекта. Ввиду этих значительных улучшений заказчик решил в будущем изготавливать вакуумные захваты по проекту, оптимизированному для 3D-печати.
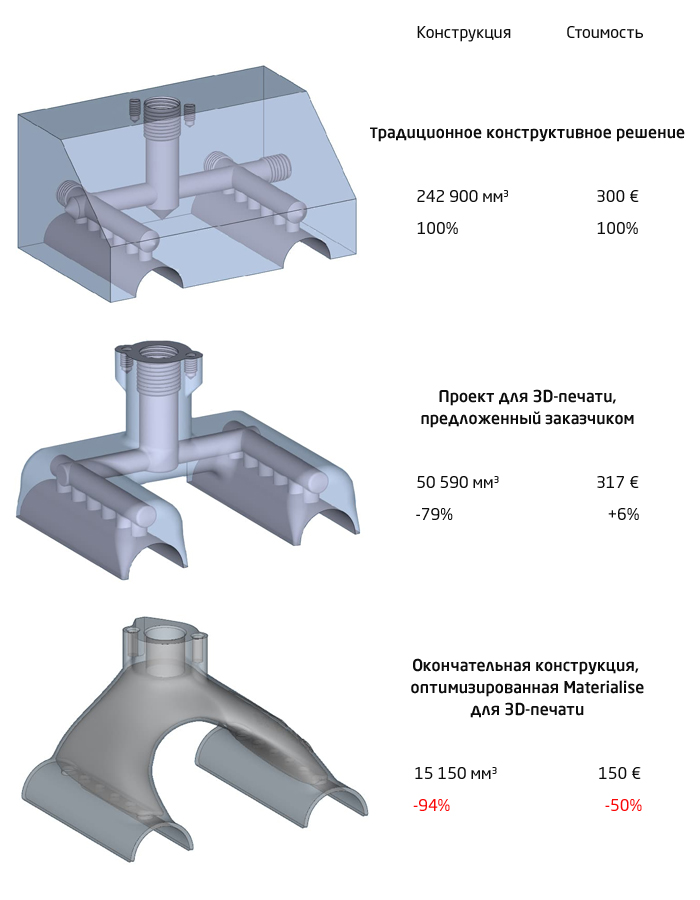
Материал предоставлен компанией Materialise
Статья опубликована 10.10.2019 , обновлена 05.08.2021