Новое поколение 3D‑сканеров ZG с повышенной скоростью измерений
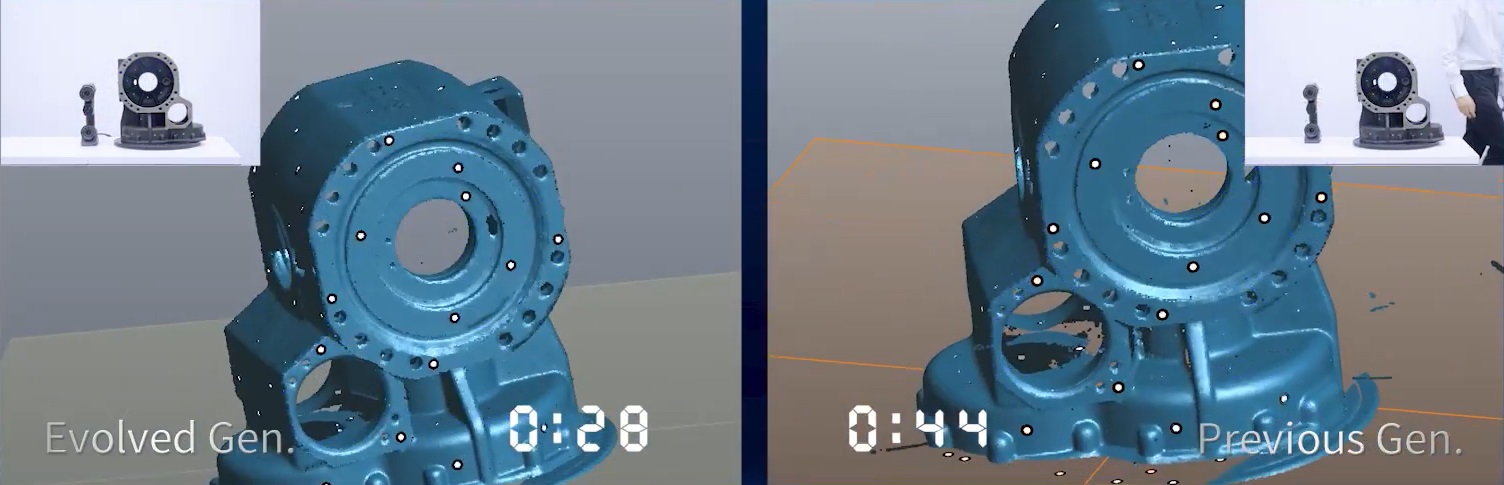
Компания ZG Technology анонсировала выпуск обновленных линеек ручных лазерных 3D‑сканеров AtlaScan и RigelScan. В устройствах нового поколения, которые поставляются начиная с февраля, существенно увеличена скорость сканирования.
Универсальный портативный 3D‑сканер ZG AtlaScan с функцией быстрого захвата отверстий:
-
скорость измерений в стандартном режиме – до 3 млн точек в секунду (+88%);
-
в режиме высокого разрешения – до 1 млн 680 тыс. т/с (+87%).
3D‑сканеры ZG RigelScan для высокоточного измерения темных и блестящих поверхностей:
-
модель Elite: в стандартном режиме – до 1 млн 350 тыс. т/с (+108%);
-
модель Plus: в стандартном режиме – до 2 млн 100 тыс. т/с (+56%);
-
обе модели в режиме высокого разрешения – до 900 тыс. т/с (+100%).
ZG AtlaScan и RigelScan являются приборами метрологического класса и обеспечивают точность измерений до 0,01 мм.
Узнать подробности, задать вопрос эксперту и заказать новые устройства вы можете на нашем сайте.
В России зарегистрировали первые отечественные имплантаты для позвоночника, напечатанные на 3D-принтере
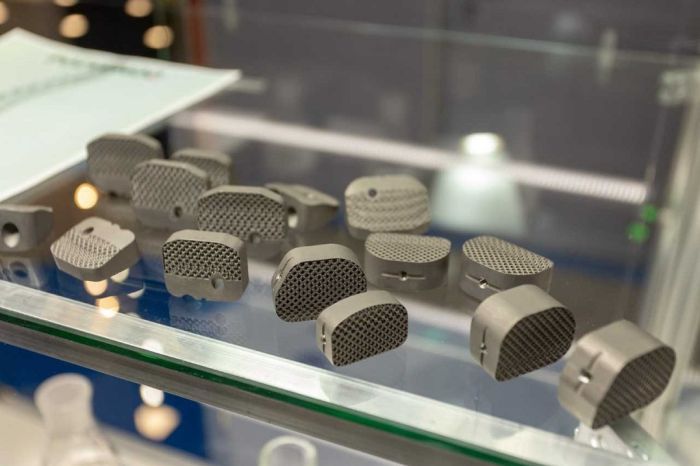
Росздравнадзор выдал регистрационное удостоверение стартапу «3D‑кейджи» на 10 линеек межпозвонковых кейджей, предназначенных для лечения шейного и пояснично-крестцового отделов позвоночного столба. Предполагается, что запуск серийного производства медицинских изделий позволит заместить до 20% импортируемых в страну кейджей для спинальной хирургии.
Имплантаты создаются из биосовместимого титанового сплава c учетом специфики дефекта и анатомических особенностей опорно-двигательного аппарата пациента и имеют высокий показатель приживаемости. Особая геометрия изделий облегчает их установку, кроме того, один и тот же тип имплантата может быть установлен как из переднего, так и передне-бокового доступа.
Источник: medvestnik.ru
Рекомендуем материал Аддитивные технологии в медицине: как снизить риски для здоровья пациентов
Антенны миллиметрового диапазона обеспечат отдаленные районы сетями 5G и 6G
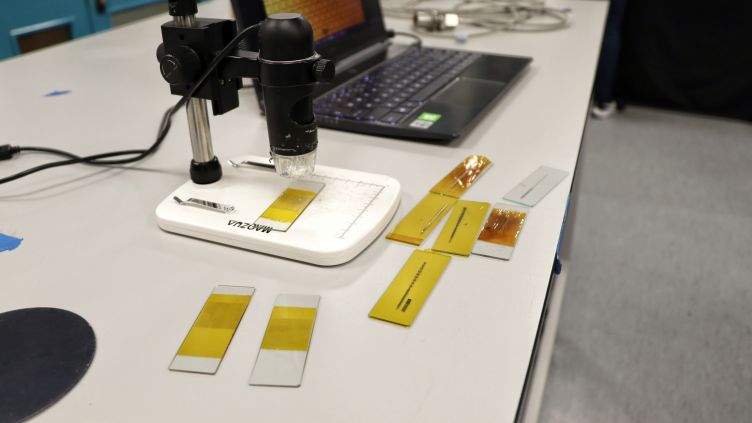
Проект осуществляется исследователями Шеффилдского университета (Великобритания). В антеннах используются серебряные наночастицы, обладающие отличными электрическими свойствами для радиочастот и протестированные на различных частотах, используемых в сетях 5G и 6G, вплоть до 48 ГГц. Их коэффициент усиления и временной отклик, влияющие на направление и мощность принимаемого и передаваемого сигнала, практически неотличимы от характеристик антенн, изготовленных традиционным способом.
«Эта созданная с помощью 3D‑принтера конструкция может совершить революцию в телекоммуникационной отрасли, – говорит Эдди Болл, сотрудник группы исследований в области связи Шеффилдского университета. – Она позволяет нам создавать прототипы и производить антенны для сетей 5G и 6G по гораздо более низкой цене и значительно быстрее, чем нынешние технологии производства. Конструкция также может быть использована для производства антенн в больших масштабах, что позволит охватить больше территорий и обеспечить самыми быстрыми мобильными сетями в те части мира, которые еще не имеют к ним доступа».
Источник: 3dprintingmedia.network
Новые решения для геодезистов и картографов: воздушные сканеры AM.TECH
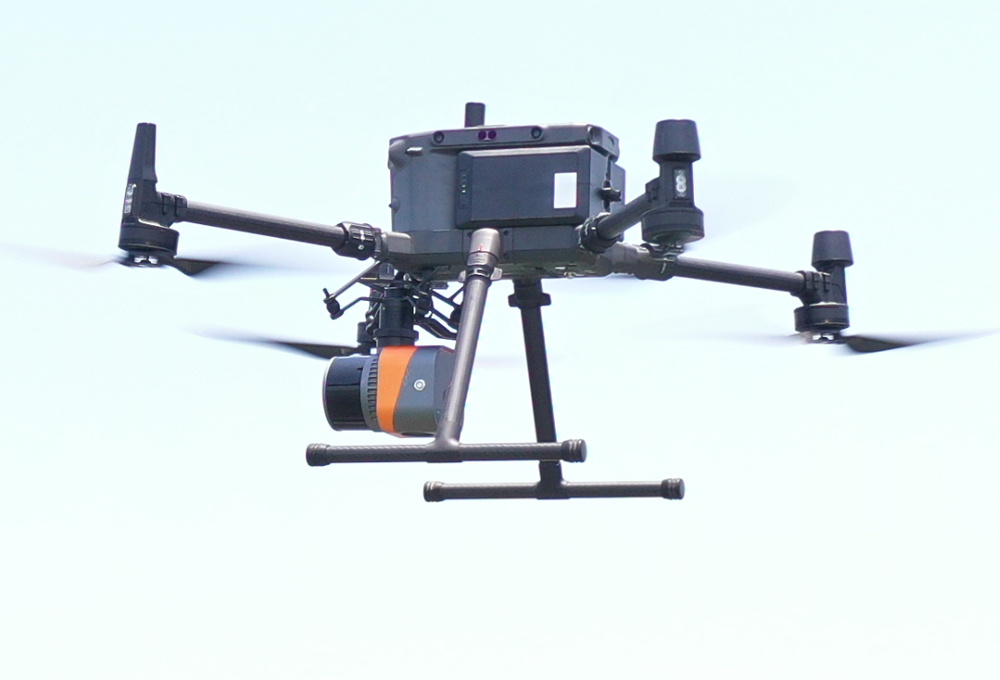
AM-TECH FLS10 и AM-TECH FLS30 (ранее EasyScan W10 и W30) – воздушные лазерные сканеры для БПЛА, предназначенные для высокоточной аэрофотосъемки, картографических и геодезических работ, воздушного осмотра и исполнительной съемки.
В систему сканера интегрированы датчики LiDAR, GNSS, высокоточные IMU и аэрофотосъемочная камера. Одно устройство для решения разных сценариев по сбору данных позволит вам сэкономить значительный бюджет на управлении и обслуживании целого парка оборудования. Сканеры совместимы с различными моделями квадрокоптеров и других БПЛА.
К важным преимуществам данных устройств компании AM.TECH относятся мобильность и компактность. FLS10 весит 1,3 кг, а FLS30 – всего 0,9 кг (это самый легкий сканер этого класса на рынке). Новинки AM.TECH уже доступны для заказа в каталоге iQB Technologies.
Футуристичная обувь: Dior экспериментирует с аддитивными технологиями
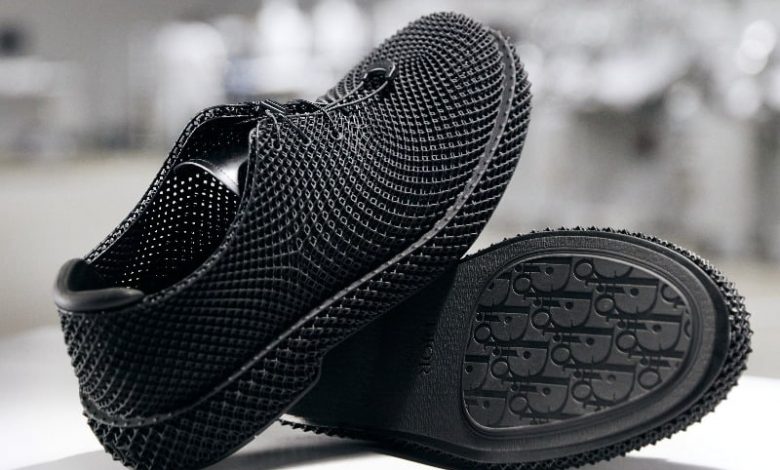
На Неделе моды в Париже в рамках показа зимней коллекции Dior 2023 года был представлен комплект обуви, напечатанной на 3D‑принтере. Модели, созданные по технологии лазерной полимерной 3D-печати (подробности не раскрываются), отражают современный подход к традиционному дизайну ботинок и дерби Dior Carlo.
Компания Dior и раньше экспериментировала с 3D‑печатью, однако эти модели наиболее близки к реальным коммерческим продуктам. Проект выполнен под руководством креативного директора Dior Homme Кима Джонса, с целью создать футуристическую версию моделей Carlo. По словам дизайнеров, обувь кажется массивной, но за счет особой геометрии, ставшей возможной благодаря аддитивным технологиям, она очень легкая и удобная в носке.
Оригинальные ботинки Carlo были отсканированы, затем была подобрана текстура для придания им панковского стиля. 3D‑печать позволяет по-настоящему проявить класс и стиль Dior с элегантными штрихами, начиная с названия Dior и заканчивая изящным узором подошвы. Дизайнеры также утверждают, что материал, из которого сделана обувь, на 80% пригоден для повторного использования.
Источник: 3dprintingmedia.network
3D‑принтеры печатают запчасти для производств Норникеля
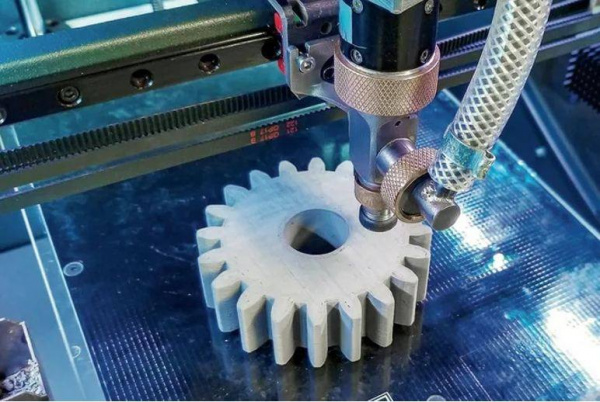
Недавно на Талнахскую обогатительную фабрику прибыл новый бронедиск. Это один из важнейших механизмов в устройстве современных насосов, которые компания использует в процессе пенной флотации. Бронедиск изготовили на песчаном 3D‑принтере методом Binder Jetting (BJ).
BJ объединяет быстрое моделирование с традиционным литьем в песчаные формы. На первом этапе на основе объемного снимка детали создают её цифровую копию, разбирают на слои и получают диаграмму поперечных сечений. На втором этапе активатор соединяют с необработанным песком и наносят смесь на рабочую платформу. Через сопло в соответствии с чертежом поперечного сечения на поверхность подается связующее вещество. Вместе с активатором они застывают. И так слой за слоем, пока не появится песчаная форма, в которую опытный мастер зальет металл и получит необходимую деталь.
Огромная машина, превышающая человеческий рост, работает в 3‑4 раза быстрее, исключая риски простоев производства и финансовых убытков. Если раньше поставка того же бронедиска занимала от 9 до 12 месяцев, то 3D‑принтер справился с этой задачей за три.
3D-печать также сулит перспективы в сфере импортозамещения. 3D‑принтеры позволяют создавать детали для промышленности здесь и сейчас, в сжатые сроки и с привлечением собственных ресурсов и компетенций.
Источник: metalinfo.ru
Читайте в блоге: Что такое Binder Jetting и как изготовить литейную форму за сутки
Разработан новаторский метод 3D‑печати сложных композитных конструкций из металлопластиков
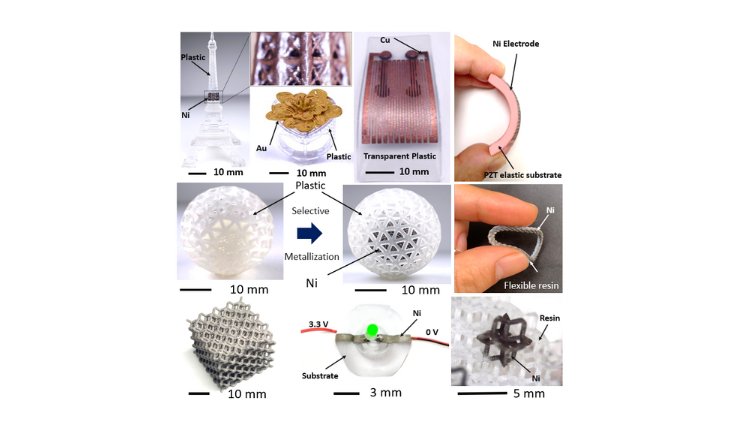
3D‑печать из металлопластиковых композитов имеет огромный потенциал для применения в таких областях, как умная электроника, микро- и наноизмерения, устройства интернета вещей и квантовые вычисления. Создание подобных приспособлений предполагает более высокую степень свободы проектирования, более сложную геометрию и более компактные размеры.
Процесс, разработанный группой исследователей из Японии и Сингапура, представляет собой 3D‑печать несколькими материалами на основе DLP-технологии (MM-DLP3DP).
По сообщению Университета Васэда (Япония), для демонстрации возможностей предложенной технологии было изготовлено множество деталей сложной топологии. Они имеют сложную структуру со слоями разных материалов, включая микропористые и миниатюрные полые структуры. Размер самой маленькой полой структуры – 40 микрон.
Исследователи утверждают, что новый производственный процесс обещает стать прорывной технологией для изготовления схем, которая найдет применение в самых разных отраслях.
Источник: tctmagazine.com
Как создавалась кукла Пиноккио для анимационного фильма Гильермо дель Торо
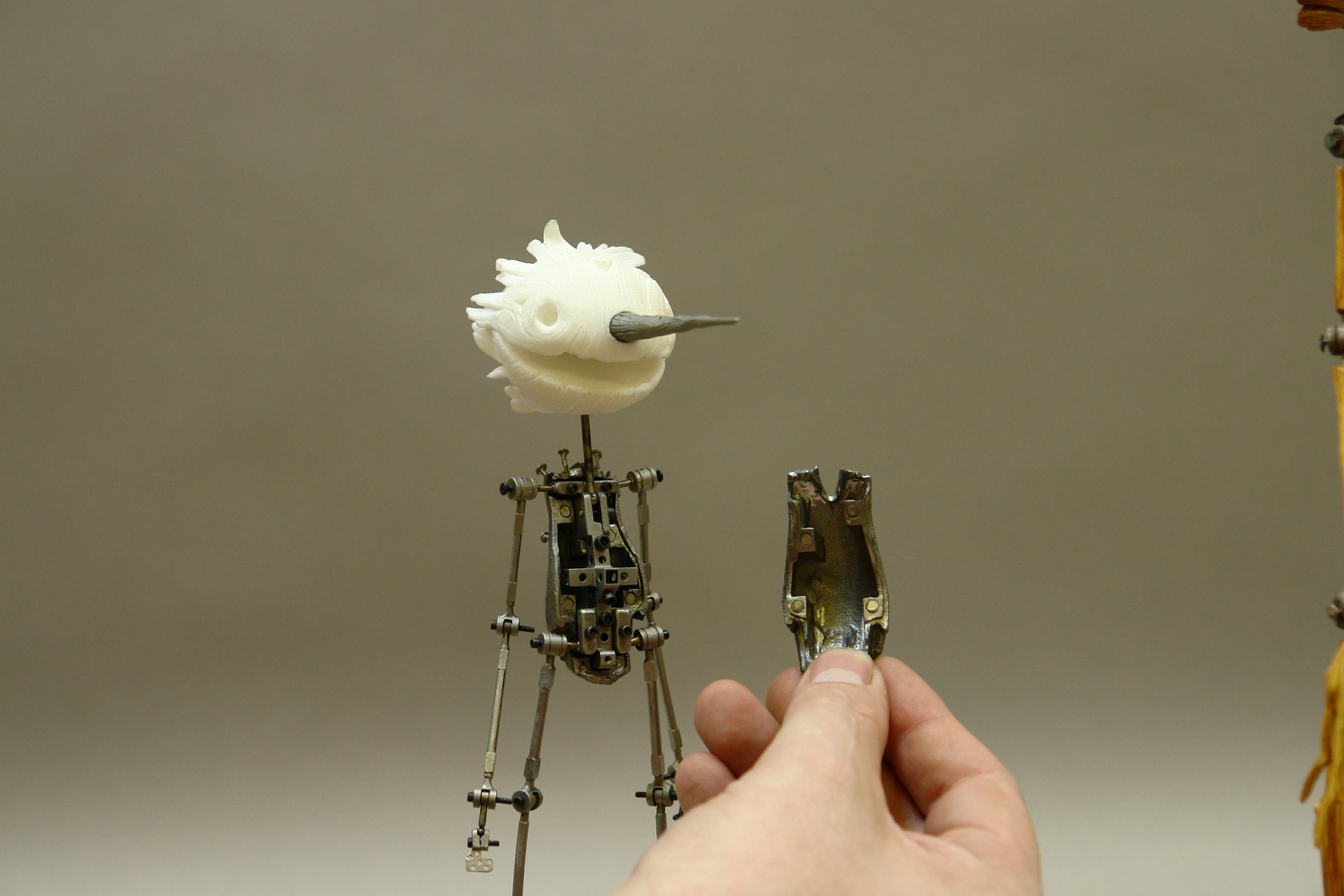
Над персонажами «Пиноккио» работала компания Mackinnon & Saunders из Манчестера, которая славится своим мастерством изготовления кукол. Несмотря на успехи компьютерной графики и скептическое отношение к актуальности стоп-моушена, новый фильм Гильермо дель Торо стал мировым хитом, получившим «Золотой глобус» и номинацию на «Оскар».
После того, как было составлено техническое задание и согласованы масштабы персонажей и декораций, в Mackinnon & Saunders поняли, что предстоит создать маленькую куклу с очень тонкими конечностями. Это представляло собой сложную задачу.
Для изготовления каркаса (позвоночника, задней части туловища, тазобедренных суставов, ступней и рук) использовалась 3D‑печать металлами, предполагавшая изготовление более 100 компонентов и шарниров. Затем команда из пяти человек выполняла отделку деталей, причем отверстия и соединения должны были быть максимально точными, чтобы обеспечить оптимальное движение – диаметр некоторых напечатанных отверстий достигал 1 мм.
Тем временем голова и внешние элементы туловища пластилиновой скульптуры были оцифрованы 3D-сканером, а полученные данные использовались для моделирования деталей, которые затем были напечатаны на полноцветном 3D‑принтере.
«Если бы мы взялись за этот фильм 15 лет назад, мы бы не смогли сделать и половины того, что можем сделать сейчас», – прокомментировал соучредитель компании Иен Макиннон.
Источник: tctmagazine.com
Хотите быть в курсе последних новостей 3D‑индустрии? Подписывайтесь на нас в Youtube, Telegram, ВК и Дзене!
Фото в заставке © Dior / Andrea Cenetiempo
Статья опубликована 09.03.2023 , обновлена 17.03.2025