Интервью с Кириллом Меренковым, руководителем центра разработки и внедрения 3D-решений iQB Technologies, экспертом по промышленным аддитивным установкам, взяла Ольга Горобец, менеджер по маркетинговым коммуникациям 3D-направления.
– Кирилл, расскажите, пожалуйста, как происходит процесс 3D-печати металлами с момента постановки задачи перед технологом, когда у него вообще пока ничего нет.
– Когда у технолога ничего нет, дается задание конструкторскому отделу о разработке такой-то детали. Конструкторы могут начать разрабатывать эту деталь по двум направлениям: Первое направление - это стандартные технологии, к которым мы все при привыкли. И второе направление, если конструктор уже подготовленный, если он понимает, что делает, если есть оборудование, то можно начать конструировать под 3D-технологию.
– Что это значит?
– В этом случае у конструктора очень серьезно развязаны руки, так как ему не нужно думать о технологическом процессе. Почему? Помните, как Микеланджело брал глыбу мрамора и отсекал от нее всё лишнее? Такова стандартная технология – мы берем большую болванку и из нее изымаем. При этом получаем много отходов, много времени затраченного. А что такое аддитивная технология? Мы из маленького зерна растим что-то большое. Поэтому нам не обязательно думать, как куда-то пройдет резец, нужно ли ему туда заходить. Например, если нам нужно сделать какую- то полость внутри, мы просто в этой полости оставляем порошок несплавленный, и в дальнейшем удаляем его при помощи какого-нибудь отверстия. И у нас остается именно та полость, которая нам была необходима. Конструктору это открывает огромное поле деятельности: он может моделировать детали так, как ему вздумается. Он может продумать системы охлаждения и любую топологию облегчения. Для этого нужно учить сейчас людей конструировать по-новому, потому что 90% процентов наших конструкторов до сих пор еще живут в 2D-мире.
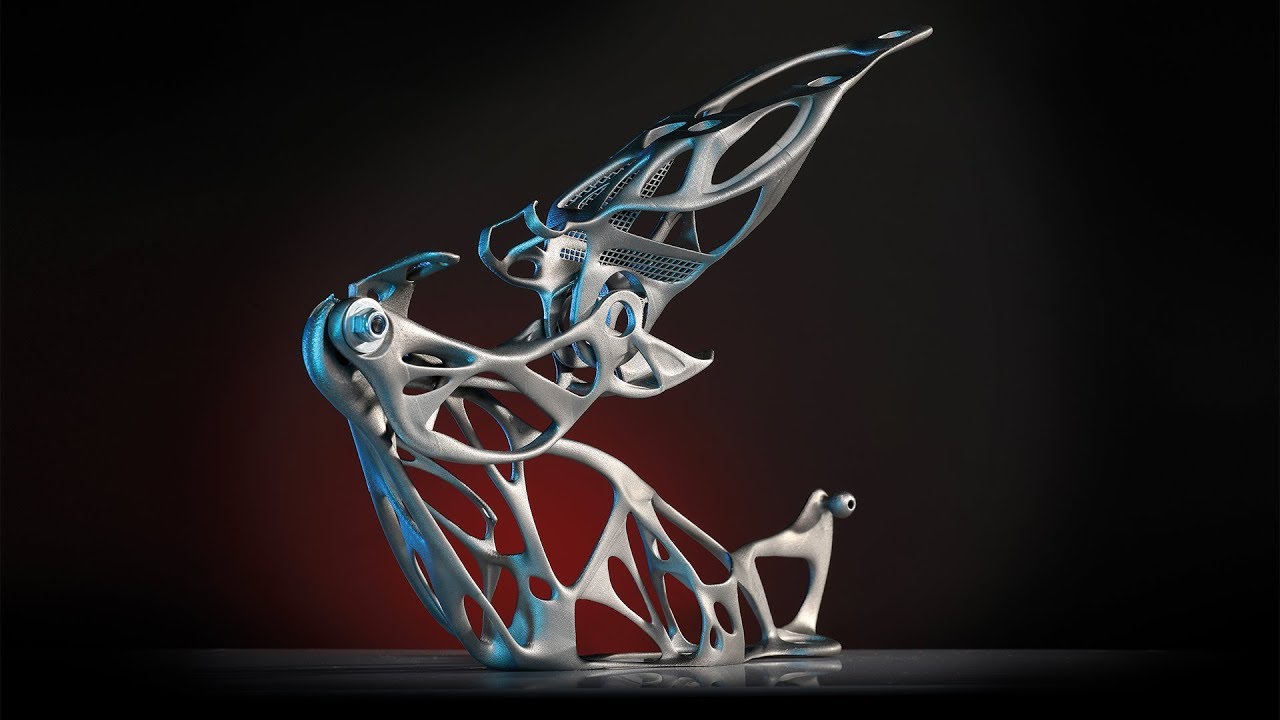
– Конструктор должен это все делать в специализированной программе?
– Да, есть специализированные программные продукты. Они разноплановые. Фактически сейчас любой производитель программного обеспечения делает программные продукты для 3D-технологий, у кого-то получается лучше, у кого-то хуже, но они есть очень-очень у многих теперь. В дальнейшем конструктор передает деталь непосредственно на производство. Ему не нужно её передавать технологу. При этом технолог существует, но это технолог, который работает с аддитивными машинами. Это не целый технологический процесс, а всего один человек, который ставит модель в печать на машину.
У машины есть тоже свои ограничения. Мы можем поставить модель под разными углами в машине и прочее. Почему нам нужно это делать? Потому что при изготовлении на аддитивной металлической машине внутри изделия мы получаем достаточно серьезное внутреннее напряжение, которое в дальнейшем нам придется снять. Чтобы готовую деталь не разорвало своим собственным внутренним напряжением, нужен технолог по аддитивному производству, который будет знать, как лучше всего расположить деталь.
А дальше засыпается материал, который нам необходим, мы нажимаем кнопку, и машина сама начинает процесс изготовления. Она берет информацию из компьютера, и эту информацию преобразует уже в готовые изделия. Когда внутри поддерживаются специальные высокие температуры, платформа подогревается до 200 градусов. Это сделано как раз для того, чтобы модели не коробило, и чтобы внутренних напряжений было как можно меньше.
– Как этот процесс происходит внутри машины?
– У нас есть герметичная камера, из которой мы инертными газами удаляем кислород. Потому что, если мы начнем работать с порошковым металлом, причём любым металлом, в кислородной среде этот порошок у нас начнет окисляться, то есть гореть. При том объеме порошка, который там находится, может получиться даже взрыв. Мы используем инертные газы, чаще всего это либо азот, либо аргон. Далее тонким слоем на платформу наносится порошок слоями 30 микрон или 50 микрон. Затем иттербиевый лазер начинает работать в определенном режиме, потому что для каждого металла свое время нагрева, температура нагрева и т.д. Примерно 160 параметров мы подбираем под каждый металл.
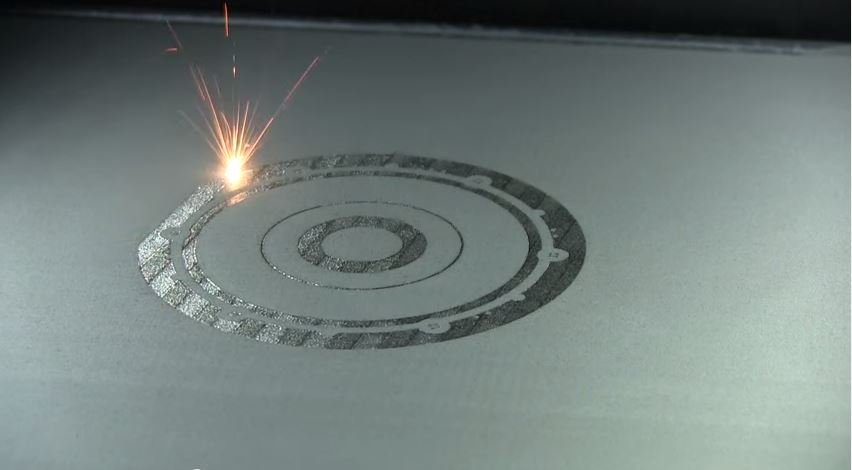
– Скажите, пожалуйста, когда мы изготавливаем деталь именно в принтере, эти параметры отличаются, например, от традиционного нагрева?
– Очень сильно отличаются, потому что традиционный нагрев мы осуществляем разными способами: начиная от сжигания угля и кончая электромагнитным нагревом. У каждого способа свои циклы, свои температуры. Мы нагреваем лазером только очень маленькие элементы – ширина прохода лазера порядка 80 микрон всего. Поэтому это своя технология, и свойства металлов должны исследовать металловеды, которых тоже нужно готовить для аддитивных производств.
Лазер в необходимых нам местах начинает сплавлять металл, и у нас получаются микрованны расплава. В этих микрованнах идет контролируемый рост зерна, и получается мелкозернистрая структура металлического сплава, который обладает уникальными свойствами – например, эти металлы лучше отдают тепло. За счет этого можно создавать вещи, которые когда нагреваются, охлаждаются лучше. Направление кристаллической решетки тоже очень специфическое в металлах, полученных 3D-технологиями. Это всё нужно исследовать, и это серьезная работа для научных учреждений.
В итоге мы получаем деталь с той конфигурацией полостей внутри, которая нам необходима. И нам не нужно просверливать, не нужно разрезать деталь, чтобы сделать эти полости, и потом обратно сваривать – мы получаем то, что нам нужно, прямо внутри изделий. В дальнейшем мы снимаем внутреннее напряжение этих металлов и обрабатываем посадочные места, где необходимо. Для этого мы обрабатываем деталь на каком-либо станке: фрезерном, полировальном, шлифовальном, можем работать с электроэрозией. Это металл, и мы можем его даже ковать. Только ковка происходит не молотом, а газоизостатическим термопрессованием. Т.е. эта деталь нагревается, и газом ее сжимают под очень высоким давлением.
Мы можем работать с разными металлами, так как одна и та же установка может делать разные изделия из разных металлов.
– Если мне нужна модель из какого-то определенного металла, параметры нужно вручную менять? Нельзя выставить стандартные?
К.: Нельзя. Есть металлы, которые уже исследованы, для которых уже есть все разработки по работе с аддитивной установкой, тогда просто вводишь цифры и не думаешь о том, что будет. Если же какие-то свои уникальные металлы, то должен быть технолог, который при помощи экспериментов и своих знаний разработает цикл работы с этим металлом. Еще можно этот металл отправить за рубеж в компанию-производителя 3D-установки печати металлом, и они дадут нам рекомендации. Но мое мнение, что таких технологов нужно иметь у себя.
Такие компании, как Airbus, Boeing, General Electric, Liebherr Avionika, Michelin и многие другие очень серьезно используют аддитивные технологии, в том числе 3D-печать металлами. При этом они уже перешли от единичных изделий к серийному производству.
– По сути, они пока учатся за рубежом, потому что там появились первые разработки в сфере 3D?
– Да, потому что у нас в России, к сожалению, такого обучения пока нет.
– То есть, если предприятие хочет сделать небольшую серию либо свои уникальные изделия, то им нужно поехать к производителям либо к дистрибуторам, которые их обучат, как и что нужно делать?
– Если это маленькая серия, то, может быть, и не имеет смысла. Но если производство купило такую машину, значит, эта машина должна быть загружена работой. Тогда лучше всего отправить одного, двух или даже трех технологов для обучения за границей. И тогда эти методы будут уже на производстве. В дальнейшем они смогут работать с этим оборудованием. И если потребуется установить еще машины, будут свои технологи, которые будут знать, как с этим оборудованием работать, и не придется покупать всю интеллектуальную собственность за границей.
Сейчас, например, есть производства, которые работают с керамическими порошками. И свои технологии работы с ними они продают. Последний раз они предложили купить режимы работы с керамическими порошками за 100 тысяч долларов. Это их интеллектуальная собственность.
– Если людям не нужен большой 3D-принтер, а нужно изготовить маленькую серию или партию, то могут они у производителей или у дистрибуторов заказать какую-то небольшую серию или модель?
– Да, конечно. В России это пока плохо развито, а за рубежом существует очень большое количество центров быстрого прототипирования, которые готовы принимать заказы из России, Казахстана, Украины и Белоруссии и за деньги делать эти серии.
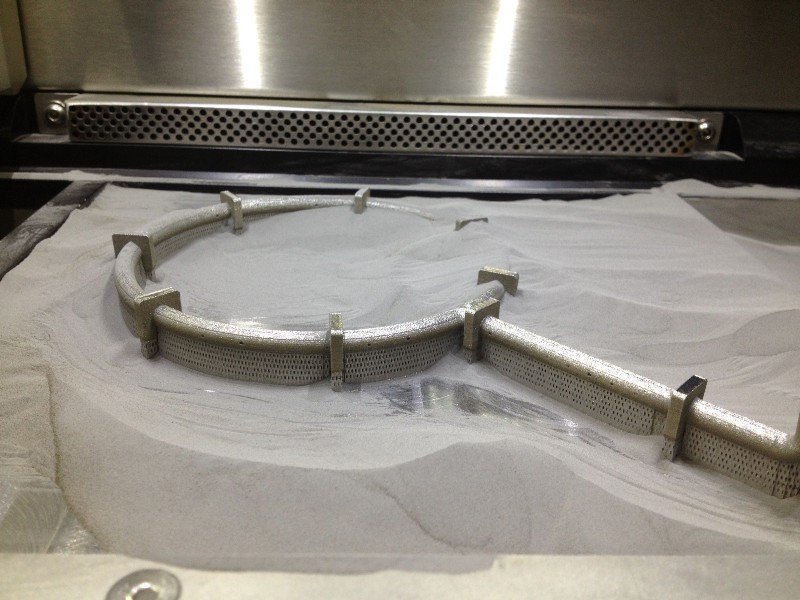
– Сколько по времени печатается небольшая модель? Это зависит от конфигурации, размера?
– Модель высотой где-то порядка 3-4 сантиметров будет печататься от 2 до 8 часов, в зависимости от ее площади и высоты. Тестовая печать принтера с размером камеры 280х280х360 занимает около суток. То есть это не длительный процесс, а действительно очень быстро.
– Качество печати зависит от скорости? Я знаю, что у небольших принтеров выше скорость, но хуже качество печати.
– Конечно, зависит. У нас качество печати зависит от толщины слоя, который мы наносим. Мы можем нанести и работать со слоем 30 микрон, можем со слоем 50 микрон. Скорость мы увеличим, но немножко проиграем в качестве.
– Какой самый минимальный слой сейчас?
– Сейчас самый минимальный слой где-то порядка 25-30 микрон. Есть порошки более тонкие, есть порошки до 10 микрон, ведь у нас слой зависит от величины зерна. Но за рубежом, например, в Европе, порошки меньше 8 микрон запрещены, так как они уже слишком взрывоопасные. В США на это смотрят несколько сквозь пальцы и иногда используют порошки от 4 микрон, на свой страх и риск. У нас – от 10 до 60 микрон. Металлы разные, у каждого своя дисперсность.
– Выходит, что из металлического порошка можно печатать готовые детали, пригодные для использования?
– Действительно, на современном оборудовании аддитивных технологий, работающих с металлическим порошком, можно печатать готовые изделия. Металлы, которые мы можем использовать в аддитивном производстве, – это стали, никелевые сплавы, цветные сплавы, причем стали мы можем использовать нержавеющие, мартенситно-стареющие, высокотемпературные сплавы. Плюс, мы также неплохо работаем с такими реактивными материалами, как алюминиевые сплавы и титановые сплавы.
– То есть, получается, из всех этих материалов можно сделать конечный продукт, который будет не хуже по качеству по сравнению с традиционными?
– Да, по качеству готовое изделие получается где-то на 50% лучше, нежели литье, или только на 10% хуже, нежели прокат.
– А есть уже какие-то испытания, которые доказали, что материал прочный и соответствует качеству?
– Испытания проходят как в нашей стране, так и за рубежом. За рубежом все-таки индустрия шагнула сильно дальше. Такие компании, как Airbus, Boeing, General Electric, Liebherr Avionika и многие другие, в частности, например, Michelin, уже очень серьезно используют аддитивные технологии, в том числе 3D-печать металлами. При этом получается так, что они уже перешли от единичных изделий к серийному производству.
Например, я видел производства, где стоят десятками металлические принтеры и миллионами штук печатают изделия. У нас в России этой проблематикой занимаются тоже в основном в авиации, например, ВИАМ, ОДК, ОАК, но наши продвижения в аддитивных технологиях сильно скромнее по ряду определенных причин.
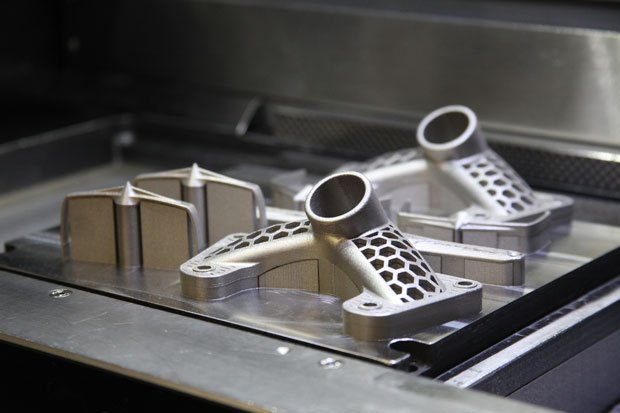
– Из зарубежного опыта опишите, пожалуйста, более подробно несколько примеров. Что именно печатается? Какие именно задачи у компаний? Как они решаются?
– Задач очень и очень много. Начиная от ухода от всевозможных логистических моментов – таких, как сборка деталей из нескольких частей. Мы можем эту деталь напечатать в едином корпусе без сборки, т.е. это будет одна единственная деталь. Это позволяет сильно облегчить изделие, упростить его изготовление за счет сокращения цикла производства и цикла разработки этих деталей.
За счет того, что мы можем сделать любую внутреннюю конфигурацию детали, мы можем сделать каналы охлаждения уникальными. И за счет этих каналов охлаждения увеличивать производительность оборудования и уменьшить его износ.
Также эта технология позволяет нам открыть новые возможности. В авиации она получила очень широкое распространение, потому что облегчение веса конструкции без потери его физико-механических свойств позволяет нам в некоторых случаях до 70% избавиться от веса какого-то изделия. Упростить его и облегчить. Исходя из этого, мы получаем экономию на топливе либо увеличение несущей нагрузки воздушного судна.
– То есть это получается бионический дизайн?
– Не всегда. Это может быть с применением бионического дизайна, а может быть с применением топологического усовершенствования. То есть бионический дизайн пока еще мало исследован. Сейчас в основном улучшение топологии идет за счёт более-менее стандартных процессов. Потому что, когда мы придем к бионике, это будет полная феерия.
– Можете немножко рассказать, чем именно отличается бионика? Я понимаю, что это пока еще в будущем.
– Для этого представим себе кости птицы изнутри. Перепонки дают жесткость этой кости, при этом она получается очень-очень легкой. Если мы перейдем к большим изделиям, эти перепонки станут более толстыми. Нужен программный продукт, который должен просчитать все эти перепонки. Для программного обеспечения нужно заложить логику, которую сейчас разрабатывают в институтах. То есть программные комплексы в состоянии просчитать конструкцию, но для того чтобы они ее просчитали, нужно, чтобы человек придумал логику.
К бионическому дизайну мы можем отнести то, что уже использовалось и раньше: сотовые структуры, тета-структуры, но это простые повторяемые формы, а в биологии, в бионике эти формы не просто неповторяемые, они уникальные. Их каждый раз их надо заново просчитать, и эту логику нам еще предстоит придумать.
– Каким предприятиям можно порекомендовать использование 3D-принтера, печатающего металлом?
– В первую очередь высокотехнологичным производствам. Почему? Зачастую на таких предприятиях цикл производства какого-то небольшого изделия бывает очень-очень длительным. Мы можем его сократить. С одной стороны, когда мы считаем в лоб стоимость материалов, аддитивные материалы стоят дороже. Но когда мы считаем всю экономику, сокращая циклы производства, начиная с сокращения потребления электроэнергии и кончая уменьшением налоговой нагрузки, аддитивные технологии позволяют сэкономить достаточно серьезные средства.
Статья опубликована 02.05.2017 , обновлена 04.03.2022