Концерн «Океанприбор» (Санкт-Петербург) занимается разработкой, производством, обслуживанием и модернизацией гидроакустической техники гражданского и военного назначения. Основным заказчиком является Военно-Морской Флот России. В концерне работают около 2 тысяч человек, 40 из них – в научно-производственном отделе протяженных антенн. Отдел ориентирован на разработку и штучное производство уникального гидроакустического оборудования. В 2012 году отдел получил необходимые средства на приобретение 3D-принтера ProJet 660Pro компании 3D Systems. Устройство планировалось использовать при прототипировании разрабатываемых функциональных узлов приборов.
После покупки принтера в отделе протяженных антенн производство каждой итерации изделия стало занимать один день. Раньше с момента подачи заявки в отдел макетирования до получения прототипа проходило минимум две-три недели. Благодаря внедрению аддитивных технологий удалось добиться многократного сокращения времени на каждый цикл выпуска детали. Себестоимость разработки снизилась в разы, что позволило в кратчайшие сроки окупить средства, затраченные на приобретение 3D-принтера. Опробовав возможности ProJet 660Pro, отдел расширил сферу его применения: теперь устройство используется и при создании литьевых форм.
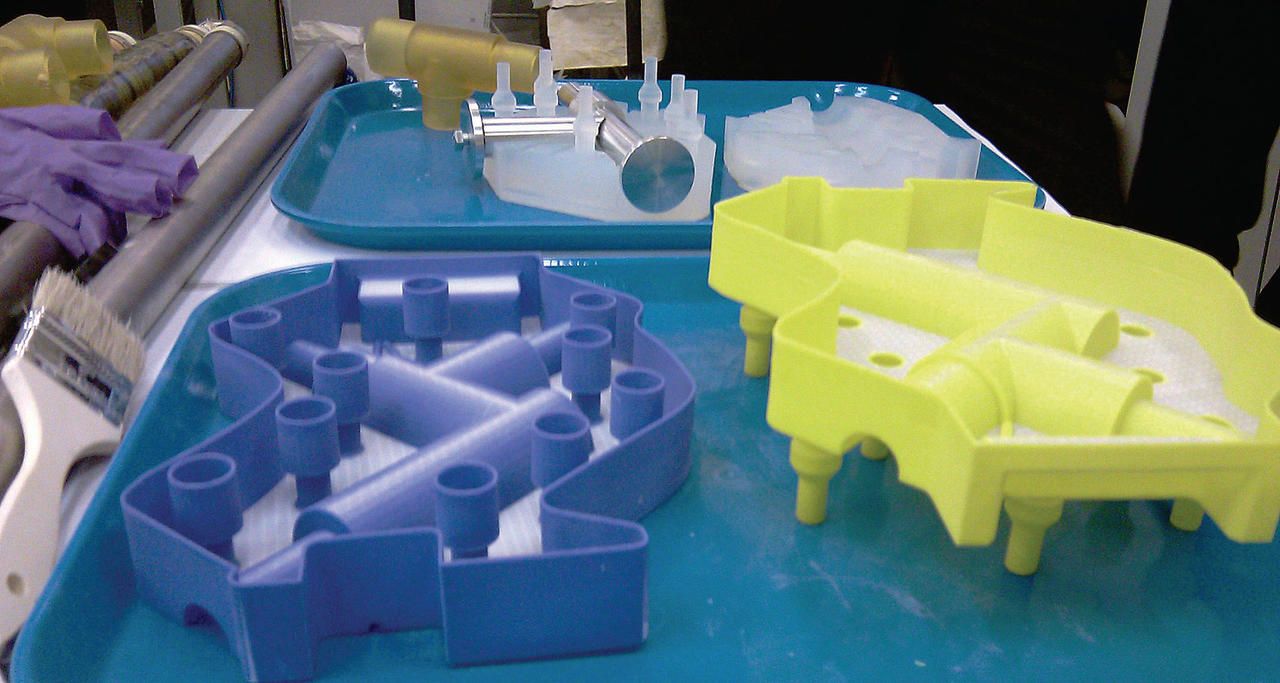
Хотите заказать услуги 3D-печати и 3D-сканирования? Обращайтесь к нам! Отправьте онлайн-заявку или звоните: +7 (495) 272-81-50.
Одной из задач, поставленных перед отделом, была разработка сложного коммутационного узла – разветвителя из полиуретана. Это одна из основных структурных единиц новой гидроакустической антенны. На создание антенны с помощью 3D-принтера ушло три месяца, а на освоение приемов работы с ним хватило одного дня. «Для нас как пользователей технология не представляет никакой сложности. Она очень проста в освоении и не вызывает проблем», – говорит руководитель проектов научно-производственного отдела Дмитрий Ермошкин.
На 3D-принтере выращивается литьевая форма разветвителя, которая затем заливается силиконом. В силиконовую форму можно заливать любой другой материал, в данном случае это полиуретан. В результате предприятие получает своего рода форму для форм – не просто прототип, а опытный образец, готовый к использованию.
Вот как выглядит весь процесс изготовления литьевой формы разветвителя:
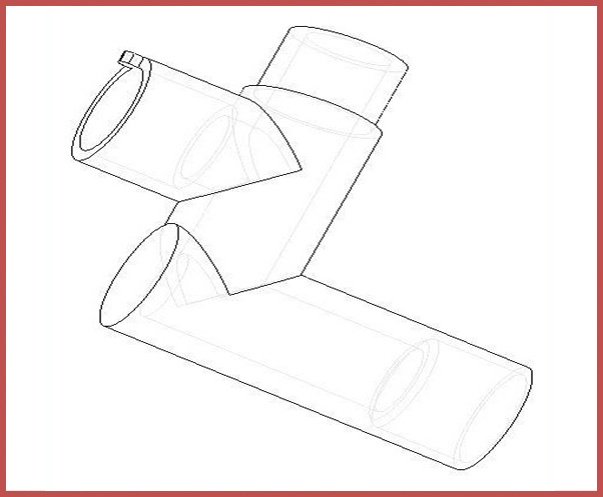
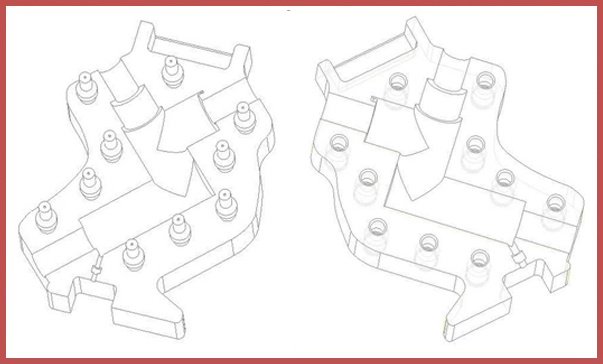
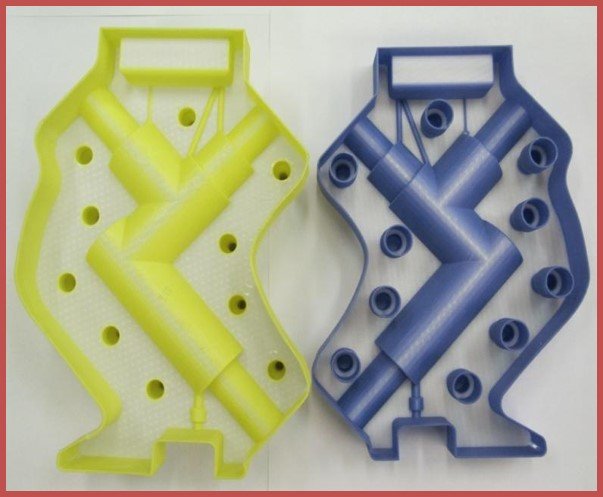
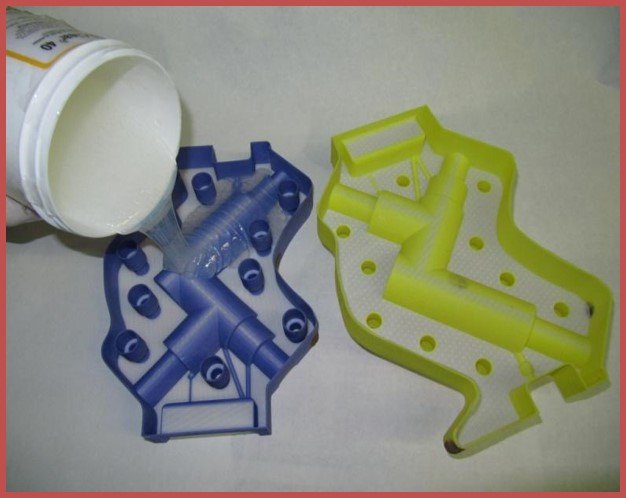
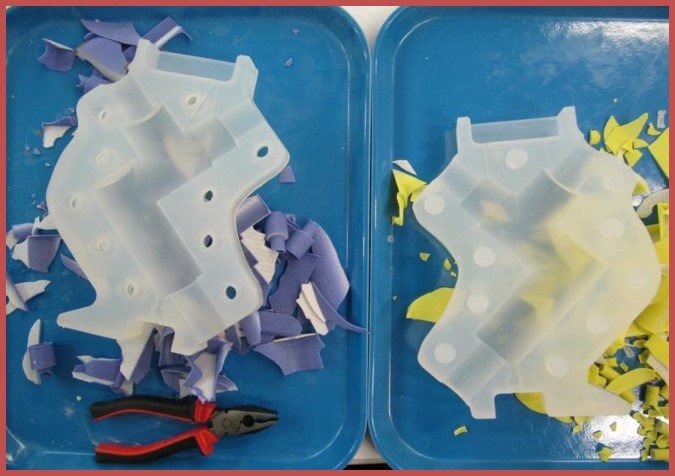
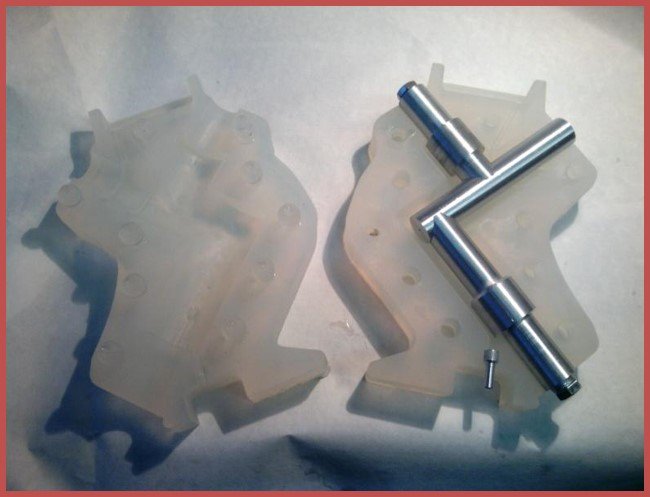
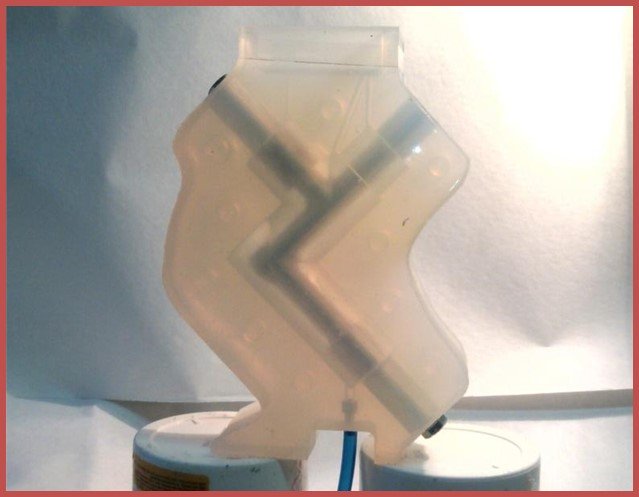
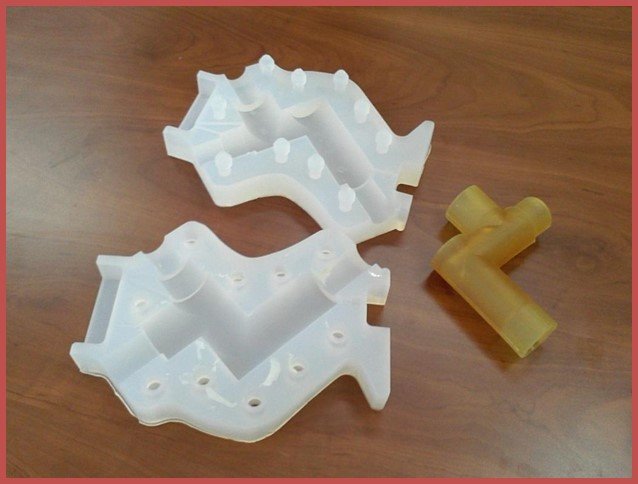
Все подробности об успешном применении 3D-печати концерном «Океанприбор» – в нашей брошюре:
Статья опубликована 30.06.2017 , обновлена 13.04.2021