Как напечатать мамонта в натуральную величину? | Крупноформатная 3D-печать в действии | Скелет, сканирование и «невидимые» поддержки | Внимание к деталям от начала до конца
В Королевском бельгийском институте естественных наук в Брюсселе (RBINS), основанном в 1846 году, работает более 250 ученых-исследователей. Здесь находятся 38 миллионов экспонатов, в том числе, с 1869 года, лирский мамонт – первый в своем роде скелет, выставленный на обозрение общественности в Западной Европе.
Обнаруженный, как следует из имени, близ городка Лир в провинции Антверпен, скелет до сих пор остается одним из нескольких целиком сохранившихся скелетов мамонта. Раритетный экспонат чрезвычайно важен для науки, не говоря уже о том, что он привлекает любителей естественной истории со всего мира. Таким образом, появился отличный шанс сделать подарок городскому музею Лира, приуроченный к его повторному открытию. Перенести скелет мамонта из Брюсселя невозможно, но его можно воссоздать!
Команда, занимающаяся сохранением истории Лира во главе с местными волонтерами из организации Kiwanis, обратилась к компании Materialise с захватывающей идеей: использовать 3D-печать для создания точной копии скелета в натуральную величину. Другими словами, применить современные технологии, чтобы вернуть доисторического жителя Лира в родные края. После того как за 1260 часов было напечатано 320 костей, на свет появился «лирский мамонт 2.0».
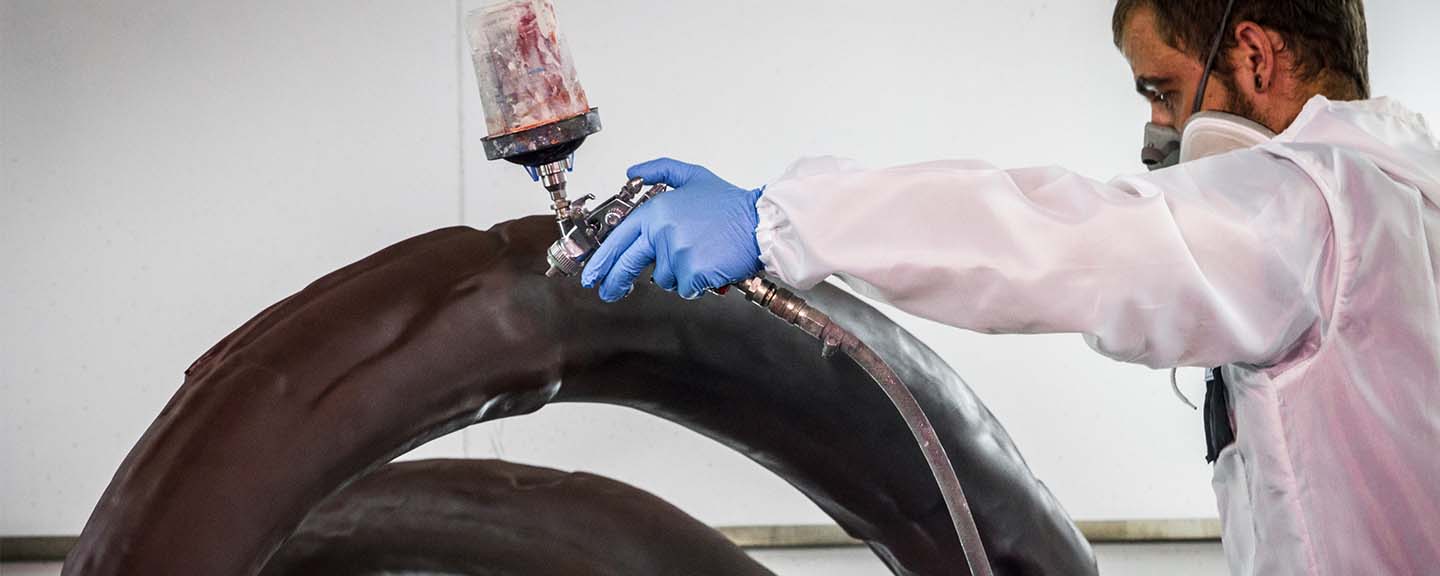
Как напечатать скелет мамонта в натуральную величину?
Когда требуется воспроизвести точную копию мамонта, становится ясно: размер имеет значение. Воссоздание 300 с лишним костей, часть которых имеет более 2 метров в длину (больше взрослого человека!), – работа не из легких. Принимая во внимание хрупкость и опасность повреждения подлинных костей, проект стал уникальным испытанием.
«Когда скелет появился в музее в 1869 году, инновационная технология состояла в том, что не нужно было просверливать или иным образом нарушать целостность костей, чтобы показать мамонта в полном размере, — рассказывает палеонтолог Королевского института доктор Митье Жермонпре, который тесно сотрудничал с Materialise в рамках проекта. — Естественно, никто не хотел рисковать естественной целостностью скелета в этом новом начинании».
Подобное творческое мышление и технические решения имели место и при создании копии. Вместо того, чтобы использовать внешнюю поддерживающую конструкцию, как у подлинного лирского мамонта, планировалось создать максимально незаметную внутреннюю поддержку, которая бы реально воплотила модель в жизнь.
Впервые стереолитографические принтеры, которые мы назвали Mammoth, были использованы в 2001 году. Благодаря камере построения 2100 х 700 х 800 мм они идеально подходят для печати крупных объектов за одну сессию.Гертьян Бринен, руководитель проекта
3D-печать предоставляет невероятную свободу и точность проектирования, поэтому выбор пал на эту технологию естественным образом. Как отмечает доктор Жермонпре, «3D-печать все чаще оказывается чрезвычайно полезным инструментом для палеонтологии. Например, мы можем изучать окаменелости, не повреждая драгоценные подлинные образцы, и работать над одной и той же окаменелостью в виртуальной среде вместе с коллегами со всего мира». Но как напечатать кости в натуральную величину?
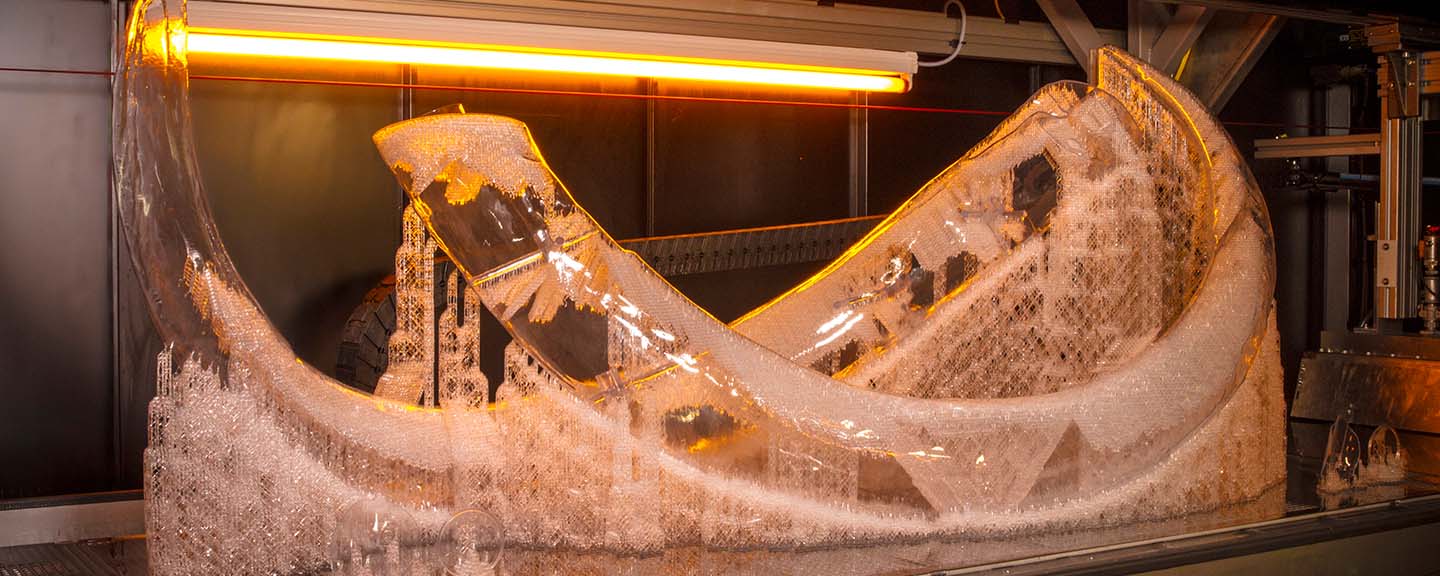
Крупноформатная 3D-печать в действии
Адекватным ответом на этот вопрос стали стереолитографические 3D-принтеры от Materialise, за работу которых отвечали руководитель проекта Гертьян Бринен и команда из 19 человек, в том числе инженеры, специалисты по САПР и постпроизводству, а также эксперты Института, включая доктора Жермонпре.
«Впервые стереолитографические принтеры, которые мы назвали Mammoth («мамонт»), были использованы в 2001 году . Благодаря камере построения 2100 х 700 х 800 мм они идеально подходят для печати крупных объектов за одну сессию, — говорит Бринен. — На тот момент мы думали о решении таких задач, как печать прототипов автомобильных приборных панелей, архитектурных макетов, крупных деталей для промышленных и производственных нужд по индивидуальным заказам. Но кости... Это был новый вызов, который мы приняли с гордостью и волнением».
Стереолитографические принтеры Mammoth от Materialise за раз наносят слой чувствительного к ультрафиолету жидкого фотополимера толщиной 1/10 мм , который подвергается выборочному упрочнению лазером так, чтобы точно соответствовать требуемым характеристикам конструкции. Для создания специальных поддержек под форму костей и спекания лазером малых костей (включая позвонки мамонта) и точек соединения, девять 3D-принтеров должны работать в течение месяца. Но прежде чем начать печать, необходимо было зафиксировать размерные данные и оптимизировать их для 3D-печати. «До даты запуска оставалось всего два месяца, — добавляет Бринен, — и каждый шаг должен был быть тщательно спланирован».
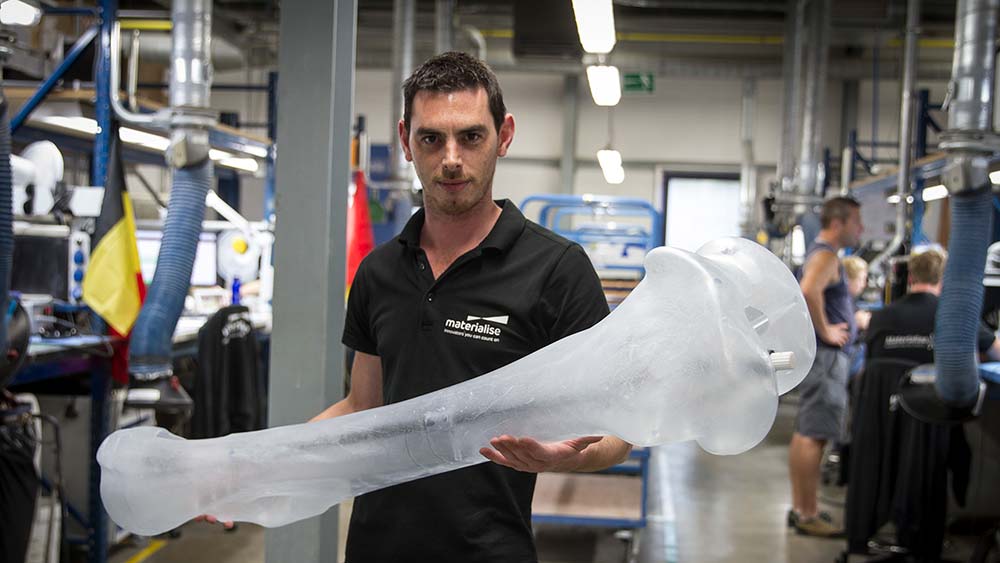
Скелет, сканирование и «невидимые» поддержки
Внешняя поддерживающая конструкция оригинального скелета позволила музею откреплять и сканировать на месте каждую кость по отдельности, передавая данные компании Materialise. Поскольку копии точно воспроизводили исходные размеры костей, каждый скан чистился и оптимизировался для 3D-печати с помощью программного обеспечения Materialise Magics, при этом каждая кость была сориентирована по трем осям для точного позиционирования. Это позволило доктору Жермонпре и инженерам Materialise провести полную цифровую реконструкцию и анализ скелета.
«Это был решающий момент в проекте, — вспоминает доктор Жермонпре. — Мы могли проверить соответствие подлинному скелету, применяя развитое научное мышление и технологии. Не стоит забывать, что скелет был смонтирован более 150 лет назад на основе анатомических знаний того времени. Например, в XIX веке ученые предполагали, что у мамонта хвост был длиной, как у слона, однако после обнаружения замороженных останков мамонтов в Сибири мы знаем, что на самом деле он был короче. Это была прекрасная возможность виртуально адаптировать скелет к новым знаниям об анатомии, которыми мы обладаем сегодня».
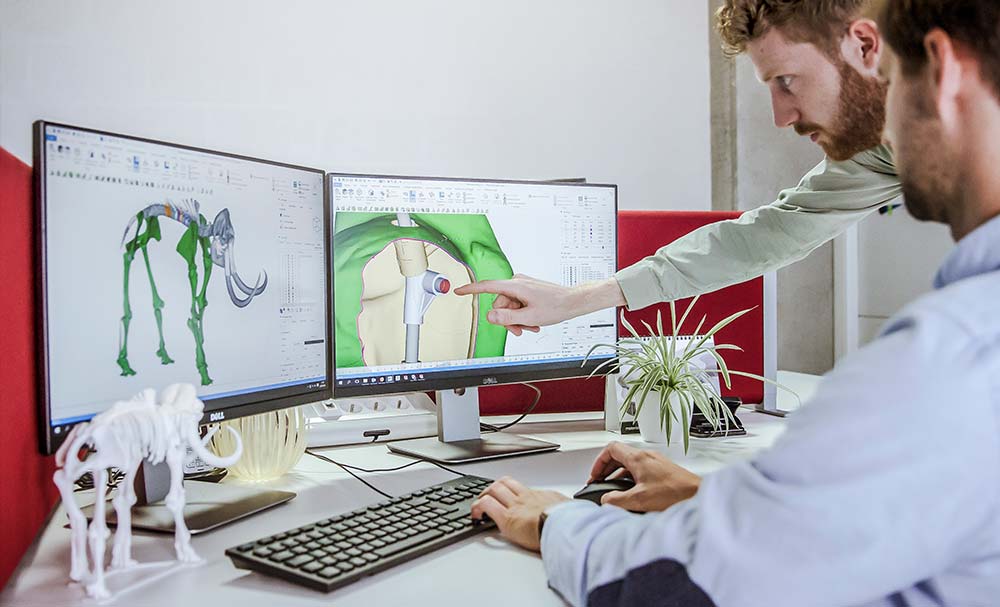
Воспроизведение посредством 3D-печати также дало возможность команде решить еще одну проблему подлинного скелета: «У лирского мамонта не хватало нескольких костей, включая левый бивень, — объясняет Гертьян Бринен. — Они были заменены поделками из скульптурной древесины. С помощью ПО Materialise 3-matic нам удалось сделать более точную копию, создав зеркальное изображение правого бивня. Так же была восстановлена сломанная верхняя челюсть. В целом, реконструкция недостающих костей и исправление ошибок сборки, по мнению доктора Жермонпре, означали, что новый лирский мамонт, напечатанный на 3D-принтере, стал даже более точным с научной точки зрения, чем оригинал».
Цифровой этап проекта также включал в себя продумывание новой «как бы невидимой» системы крепления, которая позволила бы мамонту выглядеть свободно стоящим. Для Гертьяна Бринена это был ключевой момент. «Наша дочерняя компания, RapidFit, имеет большой опыт в использовании каркасов из углеродного волокна для автомобильной оснастки. Контекст совершенно другой, но задача та же: создать относительно легкую, но при этом прочную структуру. RapidFit помогла нам разработать индивидуальный модульный углеродный каркас, который располагался преимущественно внутри напечатанного скелета.
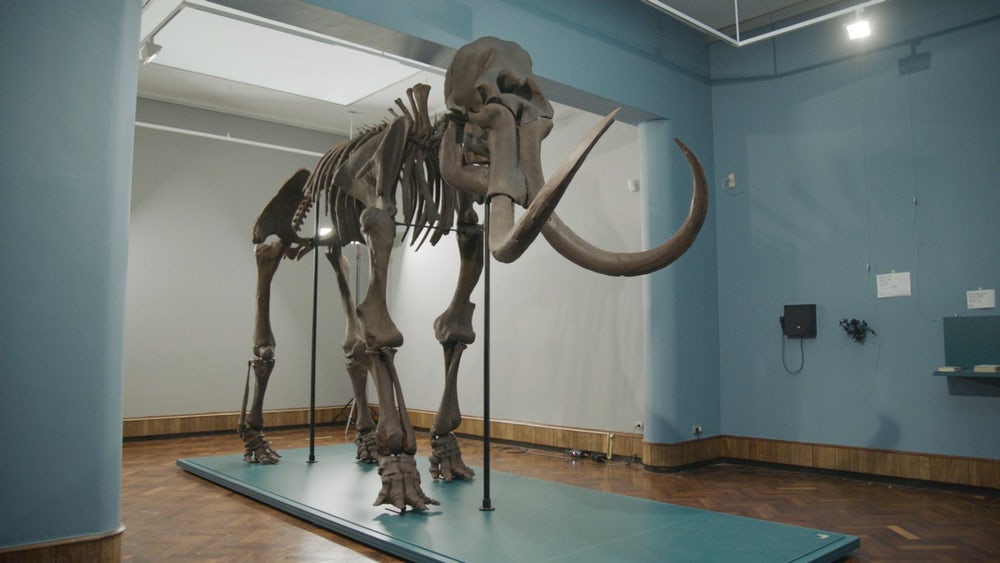
Нам было также необходимо, чтобы копии костей точно воспроизводили оригиналы и совмещались с внутренними углеродными трубками, которые должны были быть состыкованы с помощью специально спроектированных соединителей, спекаемых лазером, — все это для удержания полного скелета. Наши проектировщики справились с этой задачей путем интеграции точек входа и выхода таким образом, что они в итоге полностью совмещались с каркасом. Окончательная структура, включающаяся каркас и сам скелет, весила чуть менее 300 кг».
Внимание к деталям от начала до конца
Общее время печати скелета лирского мамонта составило чуть более 52 дней при одновременной работе нескольких 3D-принтеров — только так можно было уложиться в сжатые сроки. После печати каждой новой партии костей специальная команда Materialise обрабатывала их различными красками, текстурами и лаками так, чтобы напечатанные кости были максимально похожи на подлинные. В конце концов, пришло время новому лирскому мамонту принять свой окончательный вид.
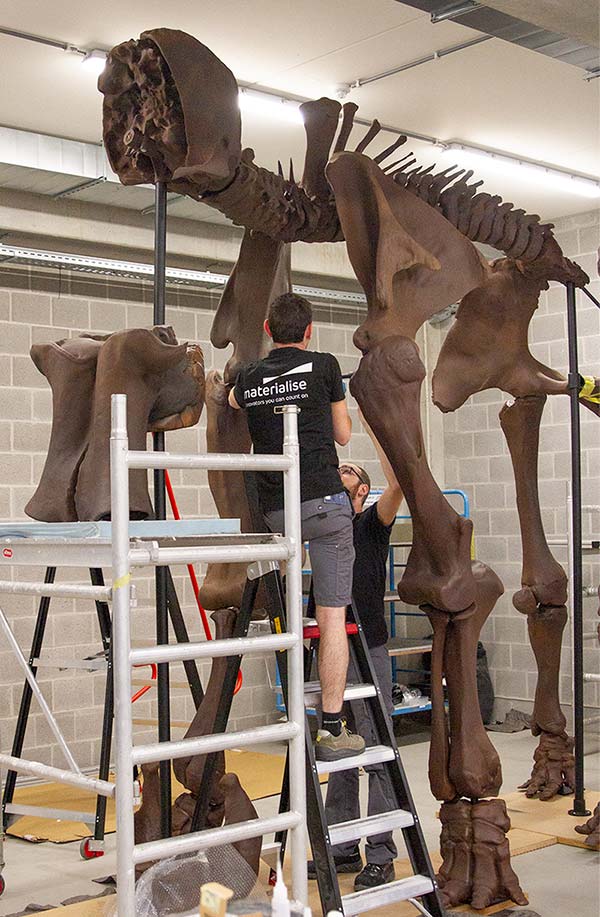
«Во время цифрового этапа проекта мы приняли все меры для того, чтобы кости, каркас и напечатанные полиамидные соединители идеально сочетались друг с другом, формируя окончательный скелет мамонта. Был только один способ сделать все точно, — вспоминает Бринен. — Поэтому наша отделочная команда приступила к сборке мамонта на нашем объекте в Лёвене. Это было великолепное зрелище!»
В результате получилась точная, анатомически верная копия. Но ее еще надо было перевезти на новое место. Бринен продолжает: «Учитывая необходимость транспортировки, мы сконструировали скелет из шести сборочных единиц: четырех ног, позвоночника и головы. К примеру, позвоночная секция состояла из 30 отдельных частей, соединенных углеродными трубками». После того, как отдельные части скелета прибыли в пункт назначения в Лире, мамонт был собран повторно — вновь на своей родной территории, которая теперь станет местом его постоянного обитания.
Бринен заключает: «Всего за семь недель нам удалось создать новую частицу истории, которая принесет огромное удовольствие новым поколениям посетителей. Этот проект задействовал все сферы нашей компетенции — от оптимизации для печати и проектирования до производства и отделки — всего, что делает компанию Materialise уникальным игроком в области 3D-печати. И это определенно была командная работа: мы не смогли бы совершить это без чудесной команды экспертов-консультантов и ученых, которые работали с нами. Несмотря на то, что речь шла о сохранении прошлого, проект стал идеальным примером футуристического применения 3D-печати уже в наши дни. Лично мне было очень приятно увидеть, как клиент успешно воплощает масштабную — в буквальном смысле слова — идею вместе с нами!».
Материал предоставлен компанией Materialise. Оригинал статьи – по ссылке.
Статья опубликована 04.12.2018 , обновлена 07.02.2022