3D-прототипирование как способ сократить расходы | Захватывающая история: 3D-печать оснастки для производственной линии | Опыт проектирования для аддитивного производства | Оборудование для 3D-печати прототипов
Инновации на всех этапах, от новых идей до массового выпуска, – неотъемлемая часть производства Samsonite. Каждый год команда дизайнеров Samsonite Europe в Ауденарде (Бельгия) создает новые коллекции чемоданов с твердым корпусом для европейского рынка. Коллекция может включать как незначительные модификации, так и совершенно новые модели с уникальными функциональными компонентами. Все проекты подвергаются тщательному анализу и тестированию перед запуском в производство на одном из трех европейских заводов Samsonite в Бельгии и Венгрии. Уже десять лет 3D-печать помогает команде дизайнеров находить оригинальные решения для сложных задач в рамках новых проектов.
«Благодаря 3D-печати нам удается быстро найти удачное решение, соответствующее требованиям рынка и высоким стандартам, к которым привыкли наши клиенты, – поясняет Вивьен Чен, руководитель по разработке продукции в Samsonite Europe. – Каждый чемодан должен быть легким и, вместе с тем, невероятно прочным. Долговечным, но удобным. Изначально мы использовали 3D-печать главным образом для наглядных, а затем и для функциональных прототипов. Сейчас мы используем эту технологию на каждом этапе процесса производства: для наглядных моделей, экспериментов, функциональных прототипов и собственно производства».
Несмотря на большой объем деталей, который требуется Samsonite каждую неделю, компания приняла стратегическое решение обратиться к стороннему поставщику – компании Materialise, вместо создания собственного аддитивного производства. Это решение было принято исходя из соображений экономии затрат, гибкости, возможности постоянного доступа к передовым технологиям и сотрудничества с экспертами в области 3D-печати.
Напечатаем прототип по технологии SLA за один день!
3D-прототипирование как способ сократить расходы
Большая часть деталей чемоданов Samsonite с жестким корпусом изготавливается методом литья под давлением. Создание настоящей детали, таким образом, обходится довольно дорого. Задача дизайнеров и инженеров – избежать затрат на модификацию литейных форм, вплоть до пустой траты ресурсов.
«Трата больших сумм на прототипирование может показаться неоправданной, – продолжает Вивьен, – но если это позволит сделать каждую деталь идеальной перед литьем, стоящим сотни тысяч евро, деньги будут потрачены не напрасно. 3D-печать позволяет нам ускорить итерационные циклы и проводить тщательные испытания и оценку каждой промежуточной версии. Мы можем давать быстрые ответы на основные вопросы. Будет ли новый тип ручки удобным? Как он смотрится? Не сломается ли? И, в конце концов, выполняет ли эта новая концепция те функции, которые нужны потребителю? Новые технические идеи могут включать крайне сложные корпуса с новым функционалом, например, с внутренними отделами, которые превращают чемодан в портативный офис. Возможность увидеть эти идеи и концепции вживую перед принятием окончательного решения крайне важна. Иногда мы печатаем крупную деталь чемодана для проверки конструкции и оптимизации изделия, чтобы быстрее принять взвешенное решение».
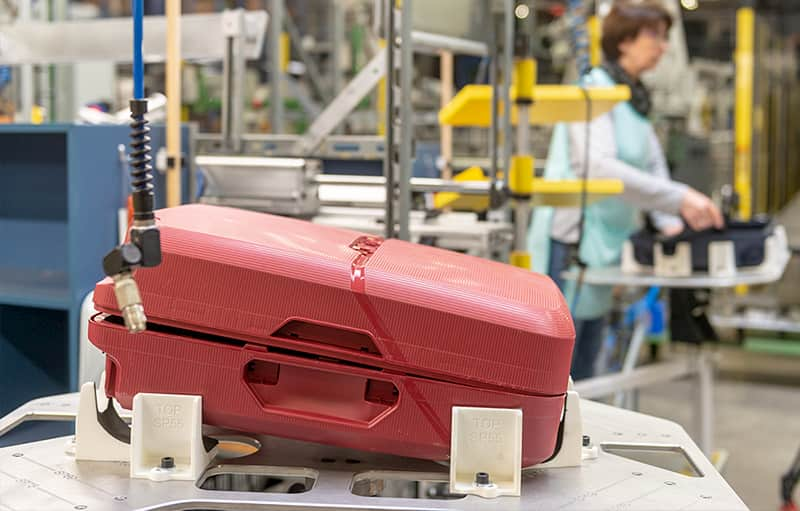
Для проверки качества продукции также используются функциональные прототипы. Элементы жесткости корпуса могут печататься специально для ударных испытаний. По результатам проверки качества их можно дополнительно оптимизировать перед подтверждением заказа на дорогостоящее литье под давлением. Таким образом, мы можем смягчить риск производственного брака перед выпуском готовых изделий.
Наглядные прототипы, напечатанные на 3D-принтере, могут оказаться полезны для маркетинга, поскольку позволяют задолго до производства демонстрировать модели, внешний вид которых не отличается от готового продукта. Возможность передачи текстур (уникальная особенность 3D-печати) и воссоздания внешнего вида различных материалов гарантирует создание точной визуальной копии готового продукта.
iQB Technologies предлагает на эксклюзивной основе современное оборудование и расходные материалы для 3D-печати прототипов и функциональных изделий:
-
профессиональные 3D-принтеры и материалы Sharebot (технологии FDM, SLA, SLS, SLM);
-
крупноформатные промышленные FDM-установки Discovery 3D Printer;
-
промышленные SLA-принтеры и фотополимеры ProtoFab.
Захватывающая история: 3D-печать оснастки для производственной линии
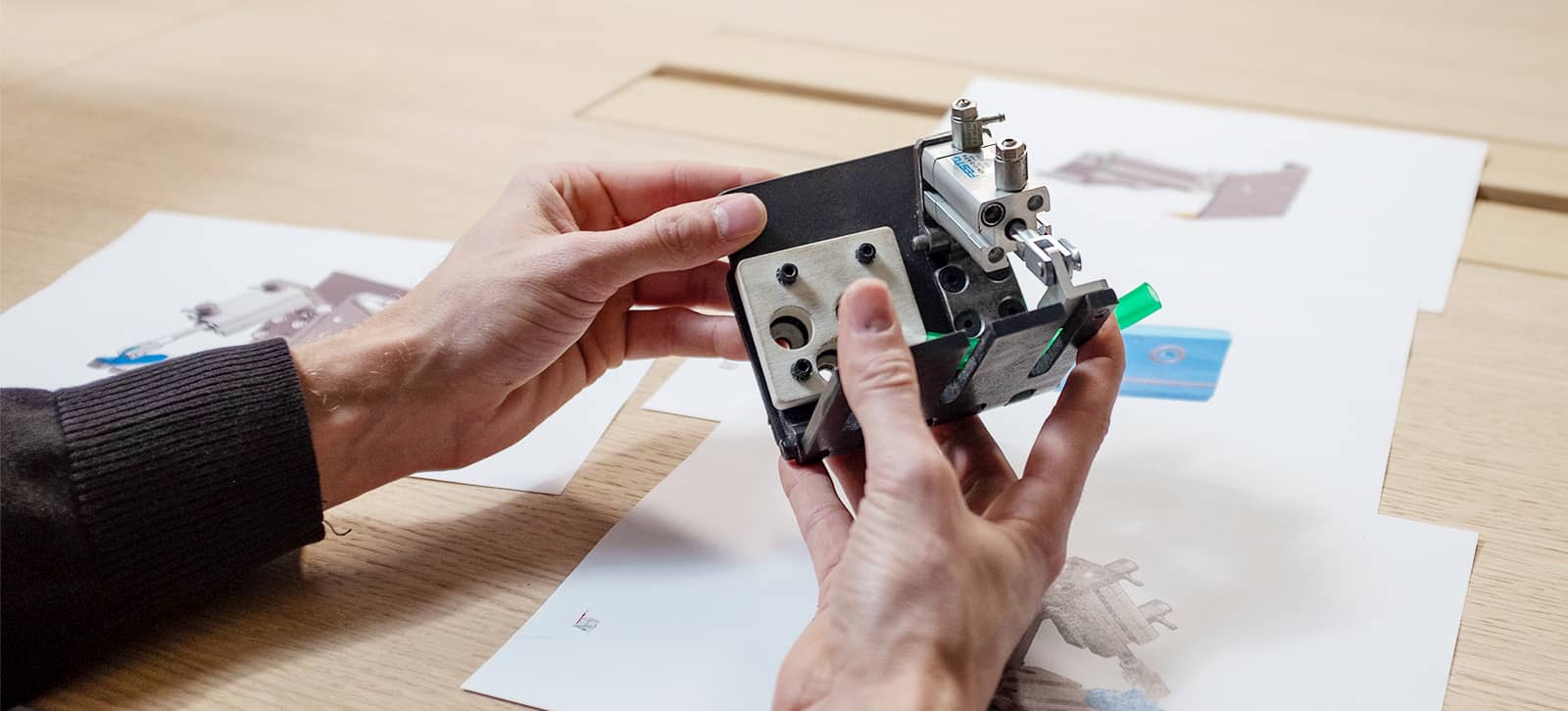
Помимо прототипов Samsonite использует 3D-принтеры для изготовления реальных функциональных деталей: оснастки для производственных линий в Бельгии и Венгрии.
К 2011 году компания внедрила технологии 3D-печати для выполнения лазерной резки на производстве. Чтобы дым, возникающий из-за лазера, не запачкал корпус чемодана, специалисты Samsonite напечатали на 3D-принтере приспособления, которые выполняют роль маски. «Маска» состоит из двух частей: чехла, напечатанного из полиамида 12, и рукава из Duraform Flex. Изготовление такой оснастки на 3D-принтере позволило упростить и ускорить производство. На данный момент от 50 до 60 подобных приспособлений используются на производственных линиях Samsonite.
Другая оснастка, созданная методом аддитивного производства (для облегчения, повышения эргономичности конструкции или добавления особых функций), включает захваты для роботов для выполнения различных подъемных задач и широкий ряд приспособлений, которые легко устанавливаются на корпуса для таких операций, как склейка, позиционирование и резка, необходимых для создания чемодана с жестким корпусом. Напечатанные на 3D-принтере детали также используются в качестве инструментов контроля и калибровки для выполнения проверок на линии.
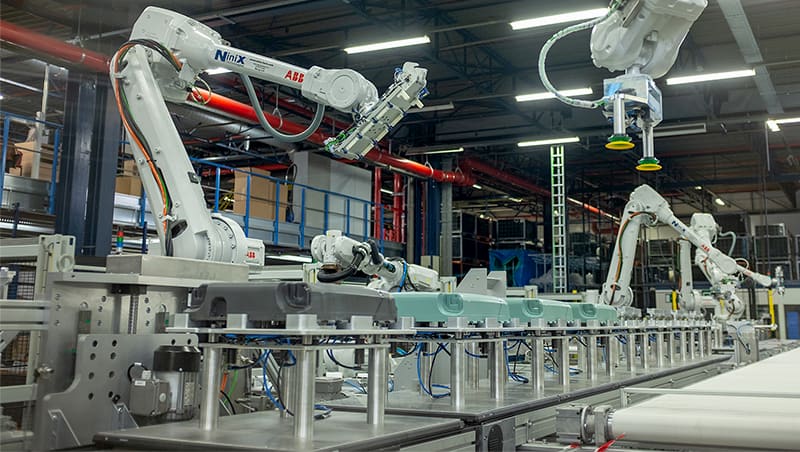
Читайте также: Аддитивное производство формовочной оснастки из полимерных и композитных материалов
«Мы используем много пневматики, например в захватах, – поясняет Николя де Вогелэр, инженер-механик по оснастке. – Пластиковые трубки, которые раньше встраивали в детали для этих целей, могут легко повредиться, что приводит к простою линии. Большим преимуществом 3D-печати является то, что мы можем спроектировать воздушные каналы прямо в детали, без использования отдельных трубок. Так получается дешевле, поскольку не приходится тратить время на сборку, и надежней».
«Другой областью, в которой 3D-печать действительно проявляет все свои преимущества, является вес. Она не только облегчает работу наших сотрудников, которым не приходится поднимать тяжести. У нас есть роботизированные руки с предельной нагрузкой, например 10 кг. Изготавливая захваты традиционным образом, мы постоянно сталкиваемся с этим пределом. Благодаря 3D-печати мы даже к нему не приближаемся, что позволяет нам оснащать захваты новым функционалом».
Наглядный пример захвата, который получил новую жизнь благодаря 3D-печати, – это захват, созданный для сборки чемодана новой конструкции.
Форма для литья под давлением для новой ручки имеет четыре полости: за один цикл изготавливается две разные пары деталей. Как правило, после каждого цикла четыре детали попадали на конвейер, а затем сортировались оператором. Затем отсортированные детали отправлялись на сборочную линию, где происходила сборка и установка на чемодан.
Эксперты iQB Technologies рекомендуют статью: Профессиональные 3D-принтеры Sharebot: воплотите свои самые смелые идеи
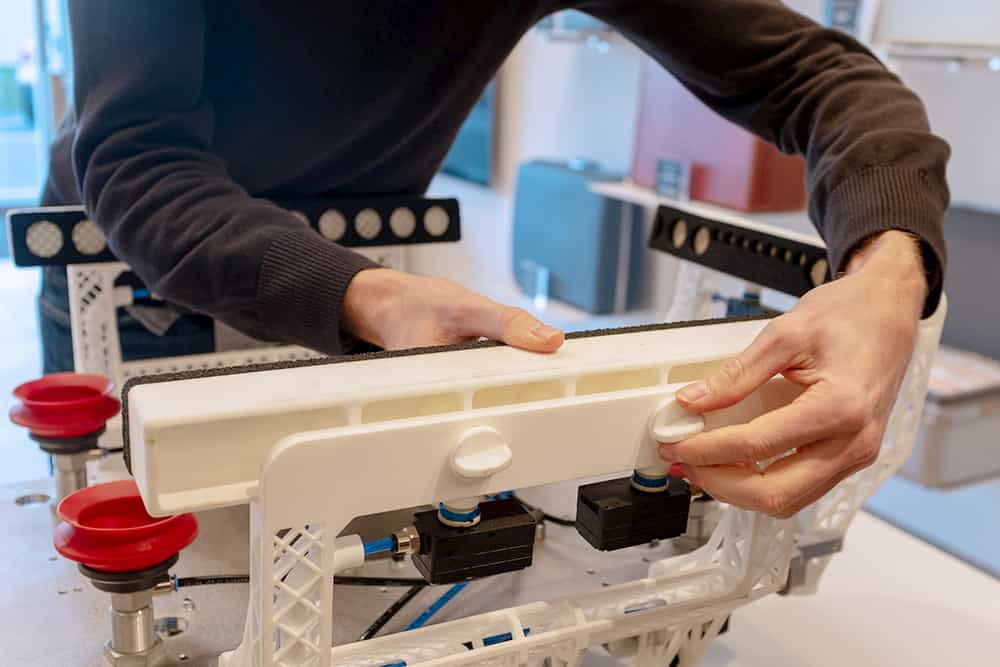
Новый захват будет извлекать детали из формы и сразу соединять нужные части. Это позволяет отказаться от сортировки и исключить один этап в сборке, что экономит время.
«Если бы мы изготавливали захват традиционными методами и из полностью металлических деталей, он бы весил и стоил намного больше захвата, напечатанного на 3D-принтере, – добавляет Николя. – Мы впервые создали что-то подобное, и преимущества в плане производственной эффективности и затрат на оснастку говорят сами за себя».
Опыт проектирования для аддитивного производства
Когда Николя и его коллеги только начали знакомиться с 3D-печатью, они могли обращаться за помощью к специалистам по проектированию и разработке, у которых такой опыт уже был. Тем не менее, применение аддитивной технологии для изготовления технологической оснастки подразумевало проектирование настоящих функциональных деталей для ежедневной работы.
Работая с Materialise, отдел оснастки Samsonite научился иначе подходить к проектированию детали при ее создании методом аддитивного производства. Это помогло углубить знания о преимуществах и особенностях конструирования в 3D-печати, включая правила, которым необходимо следовать (учет слоев, ориентация при построении и т.д.). По мнению Николя, это еще больше укрепило отношения с поставщиком услуг 3D-печати.
«Наши специалисты получили полное представление о доступных нам возможностях проектирования, – говорит Николя. – Таким образом, мы можем сократить количество деталей при сборке, добавить необходимый функционал или сделать то, что при традиционных методах было бы просто-напросто невозможно. Теперь в большинстве случаев, когда мы направляем проект в Materialise, они сразу начинают печатать, а раньше им приходилось его изменять и дорабатывать. Теперь это весьма эффективный процесс, а значит в Materialise могут сосредоточиться на помощи нам при возникновении специфических или нестандартных трудностей в проектировании».
Материал предоставлен компанией Materialise
Статья опубликована 04.09.2020 , обновлена 10.12.2024