Текущая ситуация и задачи | Проектирование | Функциональная интеграция | Программное обеспечение Simufact Additive | Участники проекта | Итоги: кратко
Компании EDAG, Voestalpine и Simufact разработали петлю капота двигателя LightHinge+, используя потенциал аддитивного производства. Компоненты были изготовлены в Центре аддитивного производства Voestalpine на металлическом 3D-принтере SLM 280 с двумя лазерами (технология селективного лазерного плавления). Результат: снижение веса, экономия материала и функциональная интеграция.
Текущая ситуация и задачи
Активные петлевые системы для капотов двигателя являются очень сложными в силу предъявляемых к ним строгих требований безопасности и функциональности. При дорожно-транспортном происшествии с участием пешехода они увеличивают расстояние между объектом, с которым происходит столкновение, и жесткими компонентами двигателя за счет поднятия капота двигателя. Пиротехнический исполнительный механизм срабатывает за доли секунды и поднимает капот.
При серийном производстве объемом свыше 30 тысяч единиц в год такие петлевые системы можно изготавливать путем штамповки, литья или прессования. Из-за сложной кинематики требуется большое количество отдельных деталей (около 40 компонентов на каждый автомобиль) и высокие затраты на сборку и производство оснастки. При изготовлении активных петель из листового металла каждая петля весит около 1500 г, что ведет к значительному утяжелению автомобиля.
SLM-технология позволила снизить массу изделия на 52% и сократить количество компонентов на 68% по сравнению с исходной конструкцией из листового металла
В то же время, имеющиеся экономические ограничения не позволяют покрывать расходы на мелкосерийное производство объемом от 80 до 30 тысяч единиц в год, используя технологии массового производства. Более того, в случае спорткаров конструкция автомобиля и недостаток места для сборки в его передней части, как правило, исключают возможность изготовления активных петель капота двигателя из листового металла.
Обходные стратегии, призванные свести к минимуму инвестиции в мелкосерийное производство, обычно влекут за собой проблемы с упаковкой и проектированием, сопряженные с адаптацией процессов массового производства активных петель. Таким образом, совместный проект EDAG, Центра аддитивного производства Voestalpine и Simufact был призван использовать потенциал аддитивного производства для решения этих проблем.
Эксперты iQB рекомендуют статью Российский автопром: дорогу аддитивным технологиям!
Решение: 3D-печать металлом
Проектирование
К петле капота с самого начала предъявлялись высокие требования: нужно было выполнить требования к прочности и жесткости при максимально возможном сокращении массы. Также важно было произвести функциональную интеграцию с соответствующим сокращением количества компонентов.
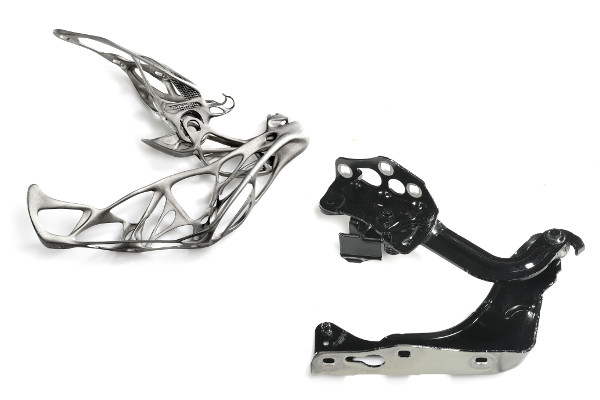
Сначала была выполнена топологическая оптимизация, включающая в себя расчет минимальных требований к материалу на основе фактических нагрузок. Полученные в результате этого процесса сложные геометрические формы обычно можно реализовать только с помощью технологии лазерного плавления с использованием множества поддержек. В проекте LightHinge+ доля удаляемых впоследствии поддержек должна была составить около 50% от общего объема расплавляемого материала. В ходе совместной работы эту цифру удалось последовательно сократить, сначала до 30%, а затем до 18%. Тем самым была устранена значительная часть операций обработки и обеспечена высокая эффективность использования материалов.
Хотя топологическая оптимизация потребовала значительных конструктивных изменений для сокращения постобработки, конечный результат обеспечил снижение массы на 52% по сравнению с исходной конструкцией из листового металла благодаря применению бионических принципов.
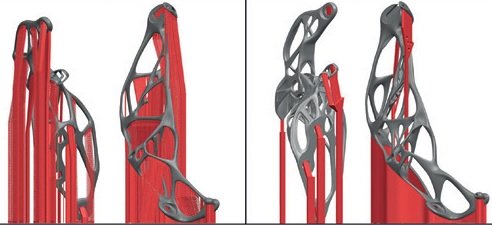
Функциональная интеграция
Данную петлю также требовалось снабдить автоматической функцией открытия капота. Свобода проектирования, которую дает аддитивное производство, позволила инженерам компании EDAG разработать сложные конструкции с заранее определенными точками излома. Кроме того, в петлю удалось интегрировать точку подсоединения газовой пружины, крепления для трубки стеклоочистителя и винт с буртиком. Эта функциональная интеграция обеспечила сокращение количества компонентов на 68% по сравнению с исходной деталью из листового металла, в значительной мере снизив исходную массу конструкции. В таком интегрированном исполнении эта петля может быть установлена в ограниченном пространстве спортивных и других автомобилей с высокими эксплуатационными требованиями.
Программное обеспечение Simufact Additive
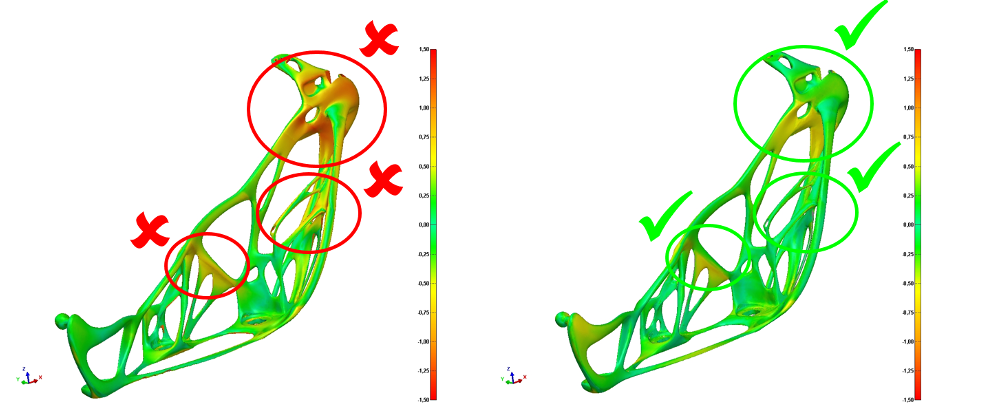
Концентрированный подвод тепла в ходе процесса аддитивного производства ведет к деформации и появлению внутренних напряжений из-за быстрого нагревания и охлаждения. Как показали измерения, без компенсации деформации это может привести к отклонению размера петли от CAD-модели на 1-2 мм. В силу этого важным промежуточным шагом при разработке и производстве компонентов аддитивным способом является моделирование реального процесса лазерного плавления. Для этой цели было использовано программное обеспечение Simufact Additive, разработанное специально для аддитивного производства. Это ПО позволяет моделировать процесс 3D-печати и последующие этапы обработки, прогнозируя появление деформаций и внутренних напряжений.
Моделирование процесса построения сыграло критически важную роль в улучшении конструкции, повышении безопасности и оптимизации деформации аддитивно производимой петли. Использование программного обеспечения Simufact Additive позволило снизить величину деформации петли капота в целом примерно на 80%. Это также дало возможность обойтись без проведения дорогостоящих и трудоемких производственных испытаний, поскольку производимые компоненты находились в пределах требуемого допуска уже с самой первой серийной партии.
Эксперты iQB рекомендуют статью За 45 часов Bugatti сделала невозможное благодаря 3D-принтеру
Участники проекта
Проект LightHinge+ удостоен золотой награды German Innovation Award 2018 в категории 'Достижения в сфере B2B - технологии автомобилестроения'
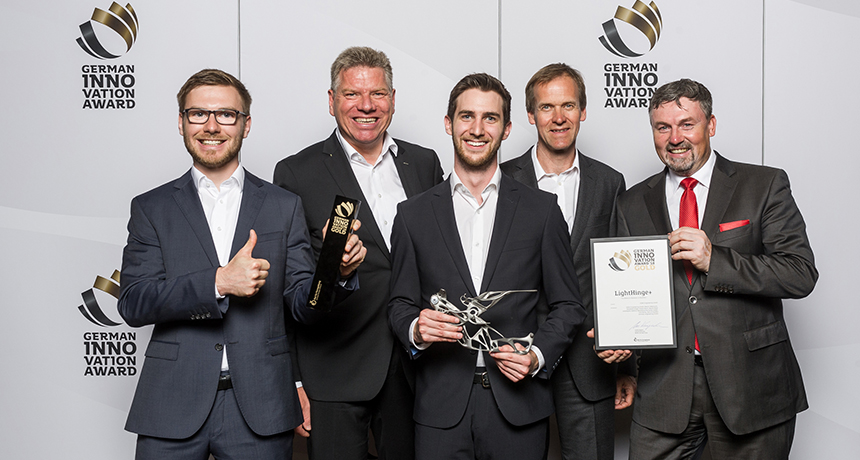
LightHinge+ — совместный проект трех компаний.
- EDAG Engineering GmbH – независимый поставщик инженерных услуг для мирового автопрома. Являясь лидером в области технологий и инноваций, EDAG также руководит работой ряда созданных им инновационных центров, где разрабатываются инновационные технологии для автомобильной промышленности: легкие конструкции, электрические транспортные средства, автомобильные информационные технологии, решения в области комплексной безопасности и новые технологии производства.
- Центр аддитивного производства Voestalpine GmbH в составе Группы компаний Voestalpine — глобального лидера в области технологий и средств производства с уникальным сочетанием опыта в сфере материалов и процессов обработки. В 2016 году на площадях группы Voestalpine в Дюссельдорфе был открыт новый научно-исследовательский центр по 3D-печати металлических деталей для авиационной и авиакосмической промышленности, автомобилестроения, производства инструментов и т.д.
- Simufact Engineering — международная компания по разработке программного обеспечения с головным офисом в Гамбурге (Германия). Разрабатывает программные решения для проектирования и оптимизации производственных процессов с помощью моделирования процессов. На решениях в области моделирования от компании Simufact строится работа отделов разработки, конструирования и производства многих известных компаний.
Итоги: кратко
- Строгие требования безопасности и сложная конструкция — снижение массы на 52% по сравнению с исходной конструкцией из листового металла.
- Функциональная интеграция обеспечила сокращение количества компонентов на 68% по сравнению с исходной деталью.
- Целостный подход к разработке деталей, который учитывает всю технологическую цепочку аддитивного производства.
- Минимизация числа поддержек, ведущая к сокращению расхода материалов и количества необходимых процессов постобработки.
Материал предоставлен компанией SLM Solutions
Статья опубликована 15.02.2019 , обновлена 14.05.2021