Свобода в проектировании и производстве | Высочайшая плотность и точность печати | Экономия времени | Материалы для 3D-печати | Ограничения, связанные с применением аддитивных технологий печати металлами | Новый подход к производству | Заключение
Инновации в промышленности не обходят стороной и технологии металлообработки. Сегодня перед машиностроительными и металлообрабатывающими предприятиями остро стоит вопрос выбора между прочно устоявшимися и новаторскими технологиями. 3D-печать уже зарекомендовала себя как гораздо более эффективное решение, способное в разы сократить временные и материальные издержки на производстве, по сравнению со станками с ЧПУ. Разумеется, аддитивные методы пока не могут полностью вытеснить традиционные. Сегодня речь идет о сосуществовании двух подходов, т.е. о внедрении промышленных 3D-принтеров в тех случаях и на тех этапах производства, где они обеспечат предприятию выгоду.
Селективное лазерное плавление – наиболее распространенная аддитивная технология печати металлами – находит применение в различных отраслях: в авиакосмической, автомобильной и нефтегазовой промышленности, машиностроении, медицине (травматологии, стоматологии, ортопедии и т.д.), ювелирном деле, а также в науке.
Хотите купить 3D-принтер по металлу? iQB Technologies предлагает 3D-решения на базе SLM-технологии от ведущих производителей:
- аддитивные установки и металлические порошки SLM Solutions (Германия);
- SLM-принтеры HBD (Китай);
- промышленные машины 3DLAM (Россия);
- компактный принтер Sharebot MetalONE (Италия).
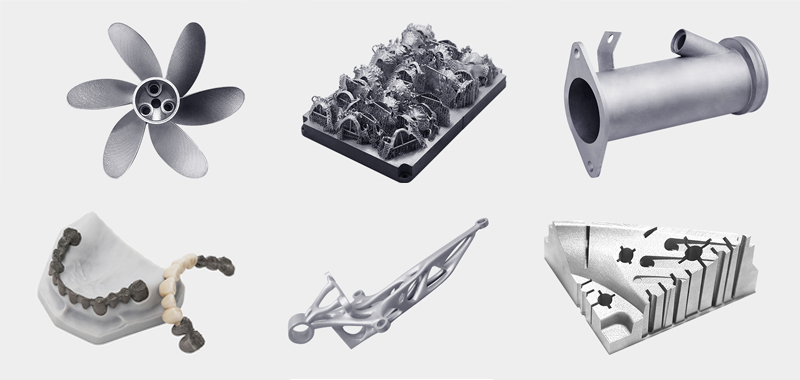
В обработке металлов 3D-технологии решают задачи изготовления:
- деталей для разнообразных агрегатов и узлов;
- сложных конструкций, в том числе цельнометаллических, которые ранее собирались из многих элементов, а также неразборных, меняющих геометрию в ходе эксплуатации;
- элементов пресс-форм для литья термопластов и легких материалов;
- прототипов;
- штампов;
- вставок для литья;
- имплантатов и протезов в стоматологии.
Свобода в проектировании и производстве
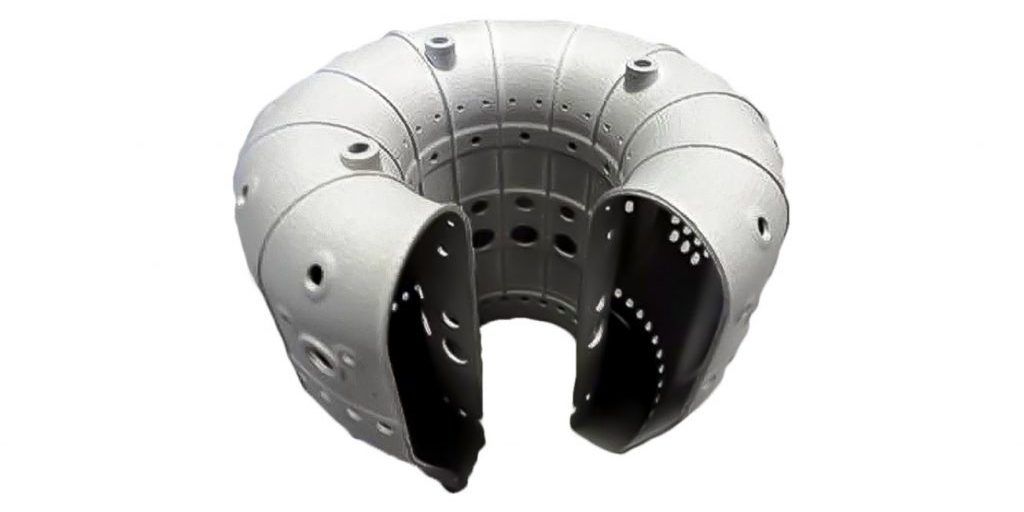
Рассмотрим на примере камеры сгорания топлива самолета, как 3D-печать оптимизирует производственный процесс, в буквальном смысле развязывая руки проектировщикам, конструкторам, инженерам, техникам. Раньше при изготовлении изделий сложной формы приходилось их разрезать. По стандартной технологии все компоненты производятся отдельно и свариваются между собой. На 3D-принтере сразу печатается цельнометаллическая камера сгорания, которая требует минимальной дальнейшей обработки, а схема направленных потоков внутри изделия задается на этапе проектирования.
На фото выше показана сложная конструкция, которую раньше можно было только отлить. Изготовление формы под такую отливку требует многих часов ручной работы либо фрезеровки. 3D-принтер дает возможность вырастить подобное изделие по слоям за несколько часов.
Высочайшая плотность и точность печати
Показатели плотности при 3D-печати на 50% лучше, чем при литье. Это значит, что в определенных технологических режимах для ее увеличения не нужно использовать, к примеру, ковку или прокат. Полученной плотности (а она составляет более 99% теоретической детали) будет достаточно.
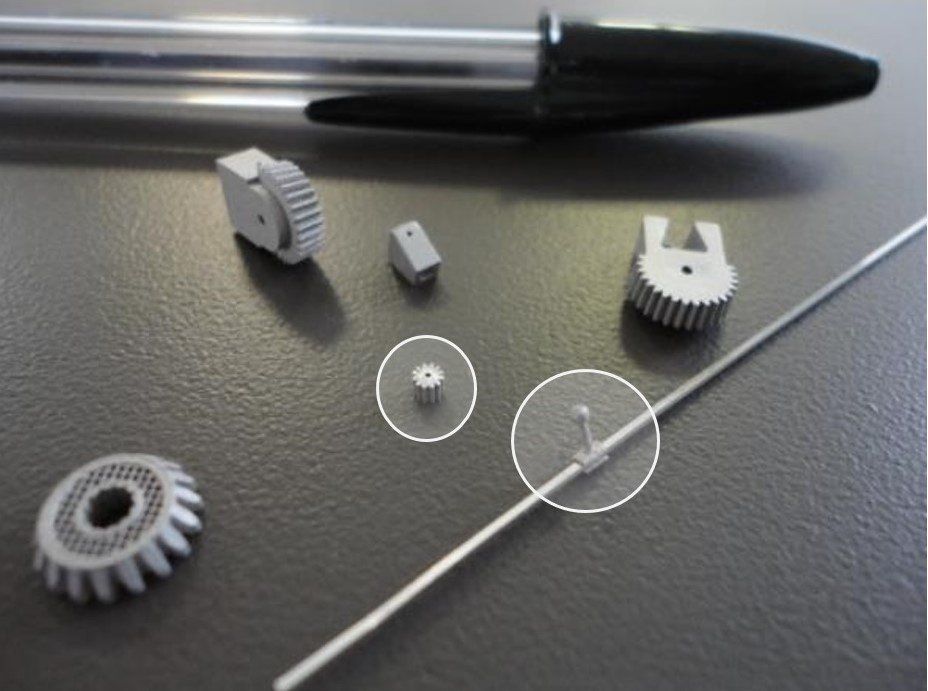
Диаметр работы лазера в аддитивной установке печати металлами – 70-80 микрон. Можно напечатать стенку детали толщиной в два прохода лазера, т.е. минимальная толщина изделия будет всего лишь 140-150 микрон. С помощью порошкового 3D-принтера изготавливаются мельчайшие детали – к примеру, двухмиллиметровая часовая шестеренка с 20 зубьями. А теперь поставим аналогичную задачу перед традиционным производством часовых и иных прецизионных механизмов. Станок для механической обработки делается на основе станины, которая после отливки должна выстояться примерно 50 лет (!), чтобы нейтрализовались все внутренние напряжения.
Эксперты iQB Technologies рекомендуют статью: Российский производитель SLM-машин развеивает мифы о технологии
Экономия времени
Если стандартные производственные процессы на предприятии предполагают отсечение лишнего от обрабатываемой болванки (так называемые субтрактивные технологии), то аддитивные методы основаны на выращивании детали с нуля. Это не только снимает проблему отходов, но и дает возможность намного сократить время, затрачиваемое на производство. Кроме того, вопрос снятия внутренних напряжений металлов, который при механической обработке решается на каждом этапе производства, теперь замещается одним этапом в конце производственного процесса. К примеру, проект, требовавший 196 часов мехобработки, выполняется средствами аддитивного производства за 8 часов, плюс 15 минут на дополнительную обработку посадочных мест.
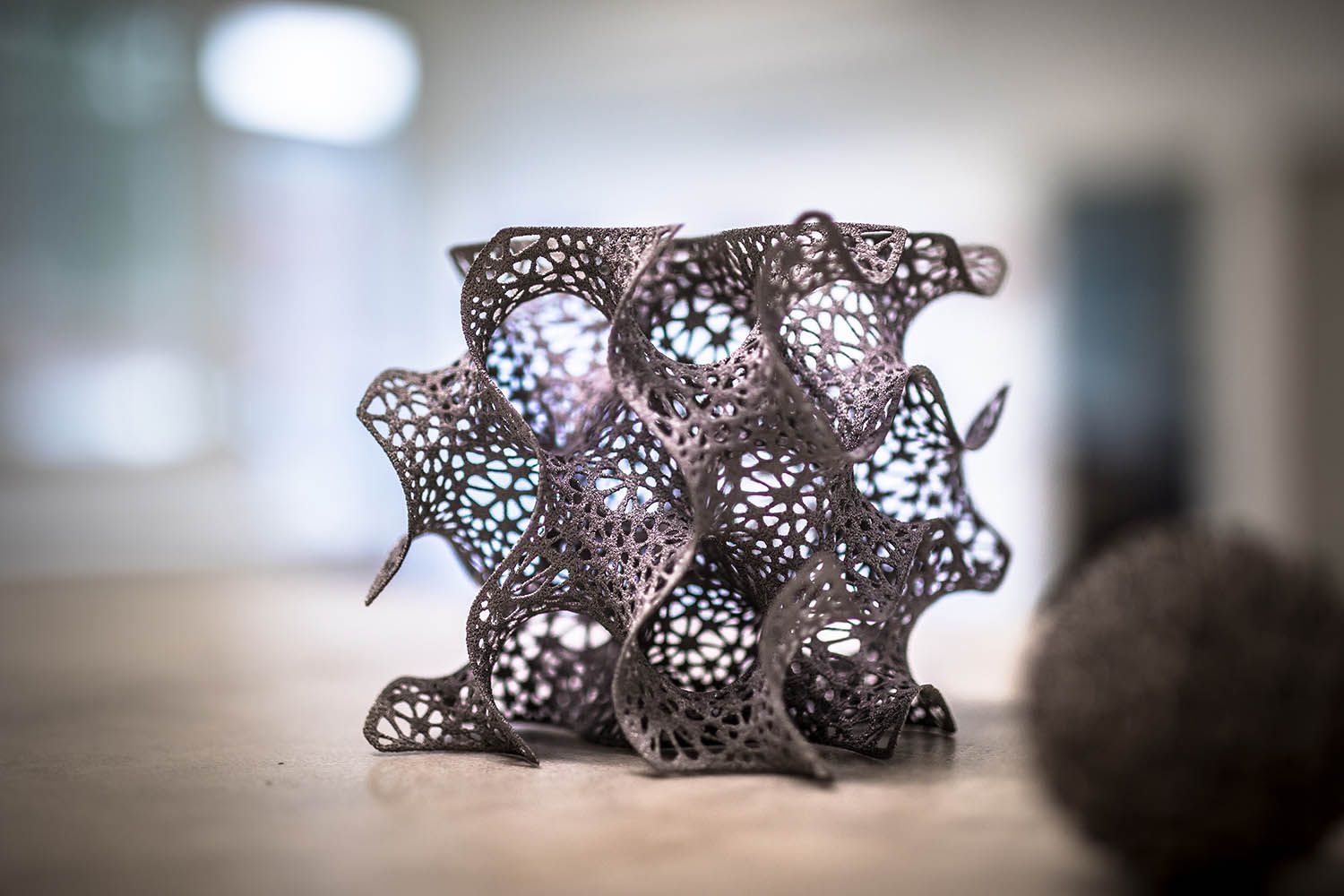
Материалы для 3D-печати
Выбор металлических сплавов, использующихся в данном типе 3D-принтеров, обширен. Сейчас штатно используются 15-20 материалов, которые протестированы и готовы к эксплуатации, в том числе нержавеющие, инструментальные, жаропрочные сплавы, титановые и алюминиевые сплавы, медицинские кобальт-хром и титан. Тем не менее, любое производственное предприятие может заказать для себя необходимый уникальный сплав. Все, что нужно – обучить технолога, который в дальнейшем будет подбирать режимы работы оборудования под выбранные материалы для 3D-принтера.
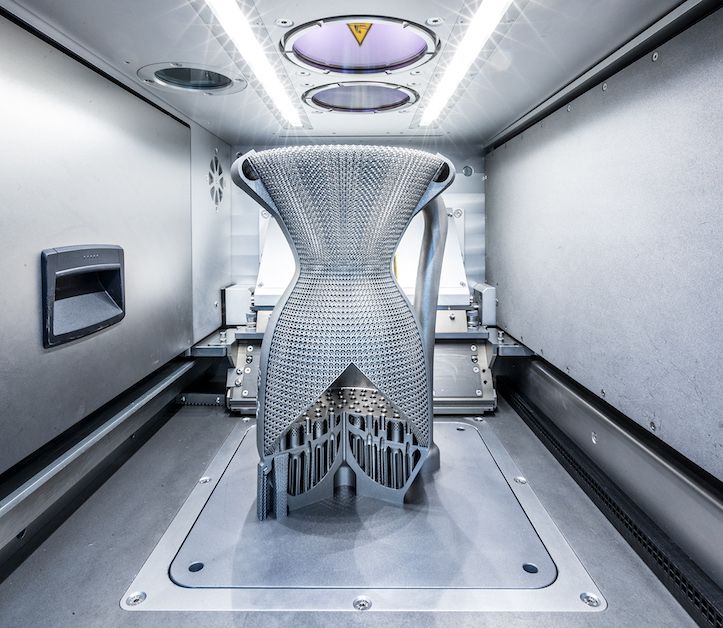
Ограничения, связанные с применением аддитивных технологий печати металлами
Как видим, 3D-печать имеет высокий потенциал для различных производств, однако у нее есть и слабые стороны. Конечно, возможности аддитивных технологий будут расширяться с развитием науки и техники, но направление это достаточно молодое, и каждый сценарий внедрения индивидуален, требует разработки отдельного подхода. Сегодня у предприятий, решивших внедрить 3D-технологии печати металлом в свой производственный цикл, могут возникнуть следующие трудности:
- необходимость в последовательных научных исследованиях (в том числе для изучения свойств металлов);
- ограничения в размерах объектов, создаваемых на 3D-принтерах;
- большие первоначальные вложения из-за высокой стоимости оборудования и расходных материалов;
- особые требования к помещению и условиям эксплуатации;
- сложность в адаптации 3D-решений к существующим технологическим циклам на производстве.
Поэтому сегодня основными пользователями 3D-оборудования становятся крупные промышленные и исследовательские центры, готовые инвестировать в проекты внедрения новой технологии. Благодаря таким передовым предприятиям мы видим, как 3D-технологии действительно помогают оптимизировать производство и приносят выгоду уже сейчас.
Эксперты iQB Technologies рекомендуют статью «3D-принтеры перестали быть чудом»: Самарский университет овладевает SLM-технологией
Новый подход к производству
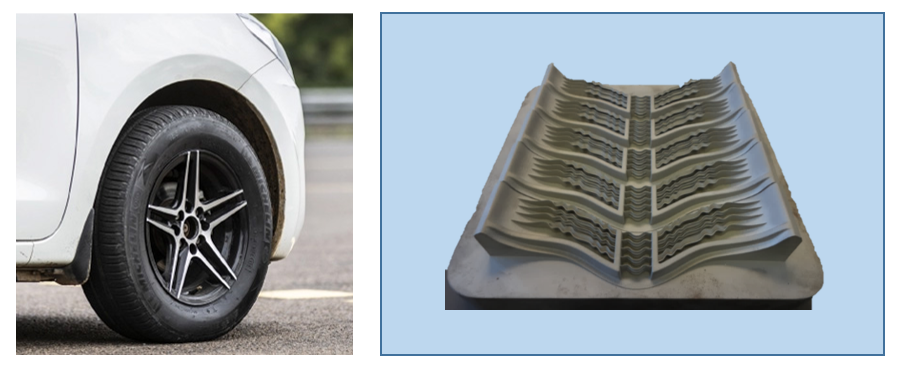
Рассмотрим конкретные успешные проекты с использованием 3D-печати металлами на предприятиях.
Яркий пример – проект французской компании Michelin, лидера в производстве шин. На 3D-принтере была выполнена вставка в пресс-форму для разделителя ламелей – самых изнашиваемых элементов покрышки. Выбор новой технологии, вместо применявшихся ранее штамповки и фрезеровки, обусловлен мелкозернистой структурой металла, лучшей теплопроводностью и, как следствие, меньшим износом.
Двигатели автомобилей, участвующих в Чемпионате мира «Формула 1», оснащены головками блока цилиндров, которые печатаются на 3D-принтере. С помощью аддитивных методов производства внутри блока можно создать любую необходимую конфигурацию охлаждения. При построении учитываются зоны нагрева, в них делается больше каналов охлаждения, что позволяет получить более ресурсоемкие детали.
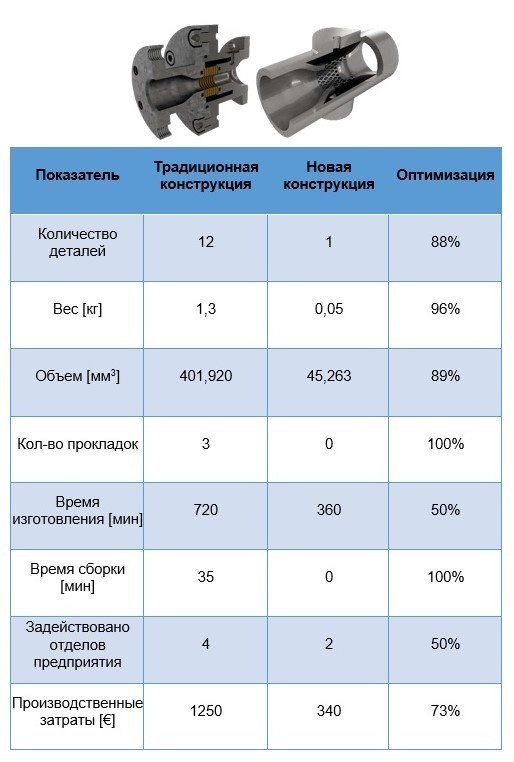
Центр быстрого прототипирования Jurec, использующий оборудование SLM Solutions, выполнил проект по усовершенствованию смесителя жидкости с газом. Изначально устройство собиралось из 12 частей, включая 3 крупных элемента – первое и второе фланцевые корпусные соединения и вставка смесителя. Новая концепция, заточенная под 3D-печать, дала возможность кардинально изменить подход к производству. На принтере печатается единый корпус, то есть количество деталей сократилось с 12 до одной. Отпадает необходимость использовать несколько металлов и фланцевых соединений: внутри цельнометаллического корпуса просто нарезается резьба, благодаря чему вес смесителя уменьшился с 1,3 кг до 50 г. В два раза сократилось время производства. Экономятся и людские ресурсы: задействованы только конструкторский и производственный отделы, а подразделения логистики и сборки исключаются из процесса. И наконец, одно из ключевых преимуществ технологии: финансовые затраты на производство уменьшились на 73%, с 1250 до 340 евро.
.jpg)
Для изготовления влагозащитных колпачков электрических коробок повсеместно используются пресс-формы, которые производятся методом литья. На их остывание затрачивается дополнительное время. По заказу ABB, мирового лидера в области электротехники, энергетических технологий и автоматизации, компания VTT разработала вставки в пресс-формы, позволившие сократить производственный цикл за счет правильного распределения каналов охлаждения. Это стало возможным благодаря 3D-технологиям.
Первоначально, изучив стандартный вид, конструкторы рассмотрели два варианта оптимизации системы охлаждения: просверлить отверстия или сделать керамическую вкладку, удаляемую затем химическим путем. Недостатки этих решений – длительность процесса и трудности в создании уникальной конфигурации внутри детали. Ответом на поставленную задачу стали 3D-технологии, с помощью которых можно задать любую форму. Из нескольких протестированных форм была выбрана самая технологически простая. В результате, с новой конфигурацией каналов охлаждения, цикл производства вкладки сократился в четыре раза – с 60,5 до 14,7 секунд.
Эксперты iQB Technologies рекомендуют статью: SLM-технология бьет рекорды: напечатан самый большой ракетный двигатель
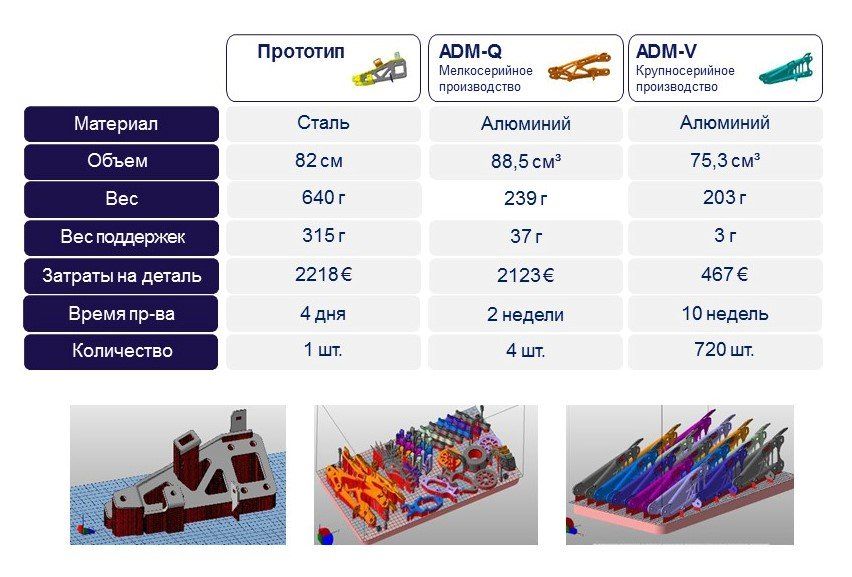
Кронштейн – деталь, используемая практически всеми производителями металлоизделий, поэтому в качестве еще одного примера применения аддитивных технологий мы выбрали интересный проект изготовления задней подвески велосипеда. Сначала на основе стального прототипа было опробовано мелкосерийное производство. В качестве материала подвески использовался алюминий, вес детали уменьшился с 640 до 239 г, а вес поддержек – почти десятикратно. Когда же была заказана крупная серия (720 штук), адаптация под 3D-печать позволила добиться еще большей оптимизации показателей, при этом себестоимость детали сократилась с 2218 до 467 евро.
Этот пример красноречиво говорит о том, что 3D-печать не ограничивается созданием единичных изделий, она уже сейчас используется для серийного производства в самых разных отраслях. У Michelin, например, большой парк металлического оборудования, и вкладки в пресс-формы, о которых мы рассказали выше, печатаются круглосуточно. К тому же, 3D-печать обеспечивает беспрецедентную повторяемость – примерно 20 микрон во всех трех осях.
Заключение
Одно из главных преимуществ 3D-принтеров – возможность получения металлических изделий повышенной плотности. Благодаря технологии SLM (селективное лазерное плавление) и огромному выбору как стандартных металлических сплавов, так и новых высокотехнологичных материалов плотность получается на 50% выше, чем при литье, и всего на 10% ниже, чем при прокате. Методами 3D-печати также удается добиться очень мелкой зернистой структуры и создавать изделия высочайшей точности и четкости – в этом плане традиционные методы остаются далеко позади. Таким образом, аддитивные технологии идеальны для печати металлами при производстве небольших (и особенно миниатюрных) деталей и геометрически сложных объектов.
Статья опубликована 14.06.2017 , обновлена 17.09.2024