Как создавалась лаборатория аддитивных технологий | Как мы осваивали SLM-технологию: первые опыты и ошибки | Какие задачи мы решаем | О прочности и других механических характеристиках | В каких отраслях выгодно применять SLM-технологию | Примеры аддитивного производства: детали камеры сгорания | О рентабельности 3D-печати металлами | О «волшебном» 3D-принтере
Самарский национальный исследовательский университет имени академика С.П. Королева – один из ведущих российских вузов, уникальный научно-образовательный комплекс в сфере разработки и производства современной авиакосмической техники, а также центр компетенций по аддитивным технологиям в Приволжском федеральном округе.
Уже почти десять лет научные сотрудники университета проводят исследования и выполняют проекты по 3D-печати деталей и прототипов авиационного и космического оборудования, газотурбинных и поршневых двигателей, медицинских устройств и оснастки. В последние годы в лаборатории аддитивных технологий идет освоение селективного лазерного плавления (SLM).
Компания iQB Technologies давно сотрудничает с университетом. Например, в 2019 году результаты работы самарских коллег были представлены на стенде и практической конференции iQB на выставке «Металлообработка-2019».
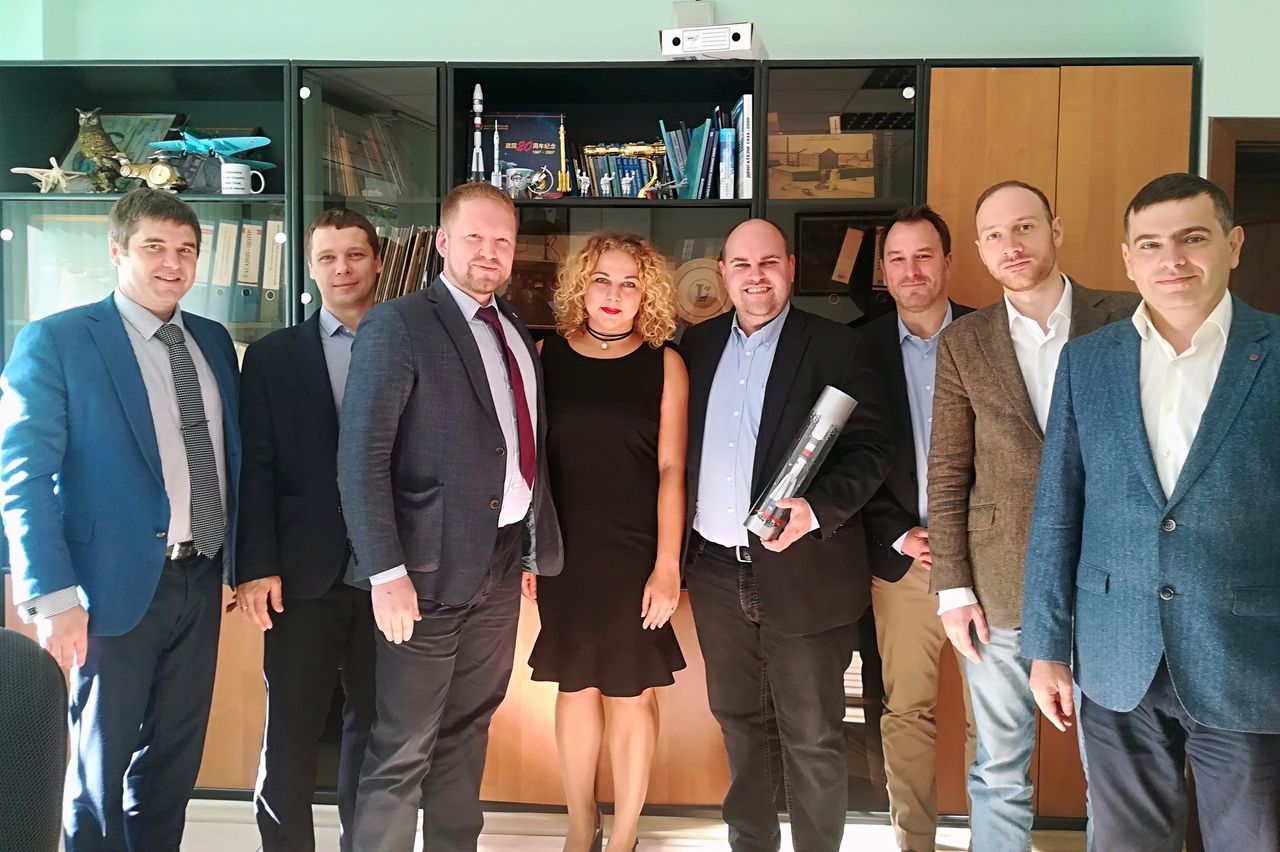
Об опыте и специфике внедрения SLM-технологии рассказывает Александр Хаймович (на фото справа), заведующий кафедрой технологии производства двигателей, директор Института производственных инновационных технологий Самарского университета.
Как создавалась лаборатория аддитивных технологий
В 2008 году у нас был создан межкафедральный Институт производственных инновационных технологий, который возглавил бывший директор завода ПАО «Кузнецов» Игорь Леонидович Шитарев. Внедрять аддитивные технологии мы начали на базе двух лабораторий института, и первые опыты были связаны с быстрым прототипированием для литья по выплавляемым моделям. Модели выращивались из конструкционных пластиков, затем по ним с помощью силиконового литья изготавливать восковки, и далее шло изготовление по серийной технологии. Примерно два года спустя была закуплена установка импульсной лазерной наплавки, которая использовалась прежде всего для наплавления лопаток двигателей.
Виталий Геннадьевич Смелов, который заведует лабораторией аддитивных технологий, загорелся идеей попробовать что-то более серьезное, а именно 3D-принтер, печатающий металлопорошковыми композициями. Мы подали заявку и выиграли грант на поставку аддитивной установки SLM 280 HL. С этого, в общем, и началась наша «эпопея» с внедрением 3D-печати металлами.
Эксперты iQB Technologies в сотрудничестве с коллегами из Самарского университета разработают 3D-решения для оптимизации производства на вашем предприятии. Проконсультируйтесь с нами онлайн!
Как мы осваивали SLM-технологию: первые опыты и ошибки
Под лежачий камень вода не течет: все постигали сами, опытным путем. Связались с ВИАМ, потом с другими производителями металлических порошков – «Полемой», ВИЛС, стали разрабатывать методику подбора технологических режимов и пробовать печатать. Как все это сделать с технологической точки зрения, мы понимали, поскольку уже сталкивались с аналогичными задачами. В Самарском университете хорошая экспериментальная база, есть электронные микроскопы – мы имеем возможность проводить металлографические исследования напечатанных образцов.
Конечно, в начале мы столкнулись с типичными ошибками, которые свойственны технологии 3D-печати металлами и требуют определенного подхода. Это были трещины (не столько даже пористость – она была в пределах нормы), отслоения от платформы, коробление формы, недостаточные механические свойства.
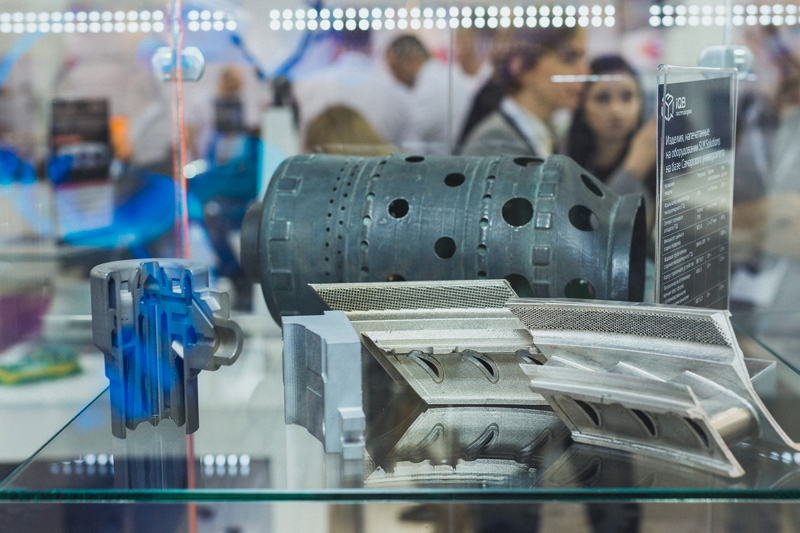
Со временем появился опыт, который мы уже развивали. Анализируя изделия, начинали понимать – что выйдет, что не выйдет. И уже могли давать рекомендации заказчикам, как можно оптимизировать ту или иную деталь.
Работа, которую ведет лаборатория, дает возможность реализовывать проекты на все более высоком уровне. Сейчас мы, например, выполняем проект, где за счет обеспечения необходимого градиента структурной жесткости можно планировать получение детали с регулируемым коэффициентом термического расширения.
Какие задачи мы решаем
Мы занимаемся не только проектированием и изготовлением деталей на 3D-принтерах, но и улучшением функциональных свойств существующих изделий.
Во-первых, помогаем клиентам, которые хотят получить изделие, вписываясь в определенные ценовые рамки. Во-вторых, решаем задачу создания детали, максимально приближенной к готовому изделию, с требуемыми механическими характеристиками. Здесь уже необходимо обеспечить точность геометрических размеров и высокое качество поверхности – структура должна быть без трещин и прочих дефектов.
Обеспечение размерной точности – очень важный момент, поскольку изготовление по SLM-технологии предполагает постобработку. Соответственно, на поверхности печатаемых объектов необходимо задать припуск. Надо определить его величину, чтобы и убрать дефектный слой, и обеспечить обрабатываемость.
Благодаря применению SLM-технологии горелочное устройство камеры сгорания стало легче на 15% и лучше по своим функциональным свойствам, а суммарная стоимость изготовления снизилась более чем в два раза
В двигателестроении, авиакосмической промышленности, машиностроении важно прежде всего получить функциональные детали с заданными потребительскими свойствами и с наименьшим весом. Снижение массы – одна из основных возможностей, которые открывают топологическая оптимизация и 3D-печать. Можно обеспечить ячеистую внутреннюю структуру, что также приводит к уменьшению веса. Свобода проектирования дает массу преимуществ, которые традиционным технологиям недоступны.
Возьмем центробежный компрессор авиадвигателя. Чтобы получить хорошие газодинамические показатели, то есть обеспечить большую степень сжатия, необходима большая закрутка лопаток. Если компрессор изготавливать механическим способом, то межлопаточные каналы находятся вне зоны инструментальной доступности, и единственный выход – аддитивное производство.
О прочности и других механических характеристиках
SLM-технология дает возможность добиться прочностных показателей, скажем так, сопоставимых с традиционными технологиями. Можно заранее просчитать, что получится, чтобы достичь требуемого уровня механических свойств. Если без термообработки – это, естественно, кратковременные механические свойства. Предел прочности может быть и больше. Характеристика усталости – предел выносливости, конечно, будет хуже в силу специфики процесса.
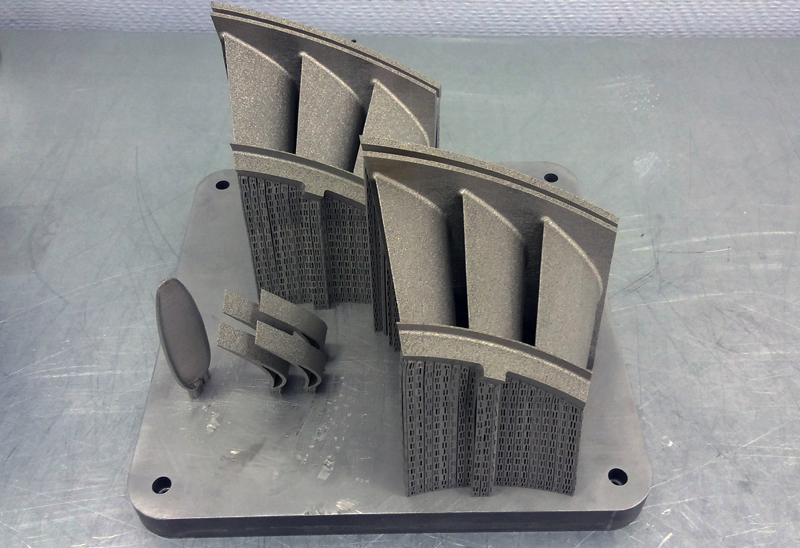
Изготовление соплового аппарата 1 и 2 ступеней ГТД из порошка сплава Inconel 738
Образец | Предел прочности, МПа | Предел текучести, МПа | Отн. удлинение, % |
Исходный | 1030 | 600 | 3,7 |
После ТО | 1430 | 820 | 8,5 |
Но есть такие технологии, как горячее изостатическое прессование (ГИП), которые позволяют вывести эти изделия на тот же уровень механических свойств. Эти данные есть не только у нас – они известны по зарубежным публикациям. По информации от наших зарубежных партнеров, занимающихся ГИП, на титановых сплавах фактически можно получить 80-90% от прочности даже не литых, а кованых изделий. За счет ГИП удается устранить внутренние дефекты, возникающие из-за неоднородности гранулометрического состава порошка, и достичь практически стопроцентной плотности.
Часто задают вопрос, может ли 3D-печать обеспечить более высокую прочность по сравнению с классическими способами. Это целый комплекс исследований, и мы тоже планируем их проводить. Скажем, за счет поверхностного легирования порошков можно получить структуры, действительно обладающие повышенными механическими свойствами. Это могут быть суперинварные сплавы, например, – то есть те технологии, которые могут обеспечить уникальные свойства, в том числе механические и теплофизические.
В каких отраслях выгодно применять SLM-технологию
Мы выполняем проекты для разных отраслей – начиная от теплообменников до авиационных двигателей и наземных газотурбинных установок.
Сейчас остро стоит вопрос создания более сложных и более эффективных деталей для авиакосмической промышленности. У нас есть планы изучения конкретных изделий – авиационных кронштейнов, теплообменников для космической техники – будем смотреть, какие есть возможности оптимизации.
Аэрокосмическая отрасль, с одной стороны, передовая, с другой – весьма консервативная в плане внедрения новых изделий, поскольку проходит очень много времени от опытных работ до установки на то изделие, которое отправится в космос. Тем не менее, все понимают, что за аддитивными технологиями будущее, и работы по их внедрению активно ведутся.
Камера сгорания МГТД была напечатана на SLM-принтере за одну неделю. Изготовление традиционным способом заняло бы 6 месяцев
Нельзя не упомянуть медицину, потому что 3D-печать не имеет себе равных по созданию индивидуализированных изделий. За рубежом эта тематика давно развивается, а в России пока только делаются первые шаги. У «Росатома», к примеру, есть целая программа по медицинской 3D-печати.
Такие работы мы проводили, во всяком случае, экспериментально. Предположим, человек получил травму правой части челюсти. Выполняют томографию левой части, затем получают снимок в формате DICOM, отзеркаливают, моделируют, и на 3D-принтере выращивается недостающий фрагмент из титана. С помощью SLM-технологии это можно сделать достаточно быстро, а скорость в медицине – самое главное. Дальше дело остается за медиками.
За рубежом мы видели, как работает серийное производство медицинских изделий. Замечу, что в этом случае 3D-принтер должен быть «заточен» только под медицину и печатать определенными металлопорошковыми композициями (обычно это либо чистый титан – Grade 1, либо Ti6Al4). Все это сертифицируется, для этого есть свой путь.
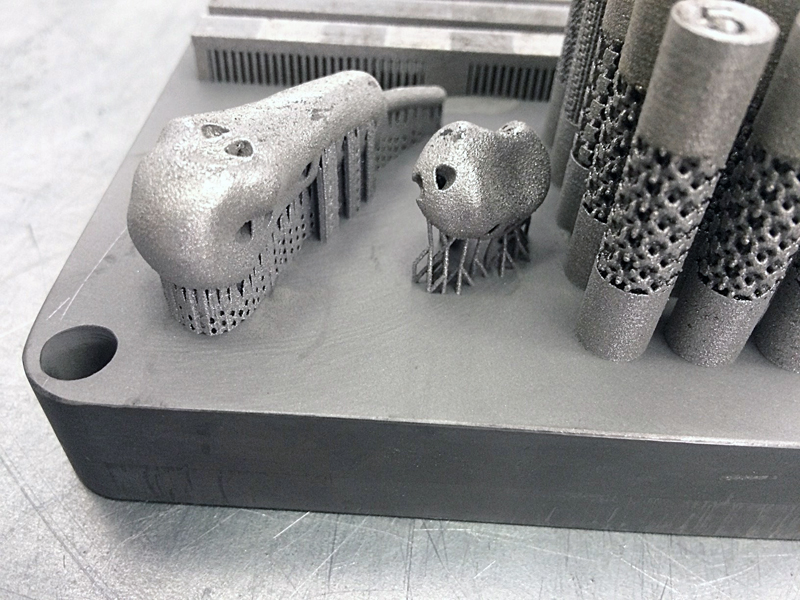
Суммарная масса эндопротезов – 13 г
Материал – титановый сплав ВТ6
Время печати – 1 час
Очень перспективны для внедрения 3D-печати инструментальное производство и изготовление и переработка пластмасс.
70% всех изделий делается из термопластичных полимерных композитов в пресс-формах. Соответственно, качество продукта и его стоимость определяются качеством изготовления оснастки. Цикл производства можно сократить, обеспечив правильный режим охлаждения формообразующих элементов. Так называемое конформное охлаждение можно реализовать только за счет применения аддитивной технологии – когда формообразующие элементы оснастки изготавливаются на 3D-принтере. Сейчас на Западе эти технологии получили широкое распространение, там есть много компаний, которые специализируются только на этой задаче. И мы постепенно к этому идем: отечественным инструментальщикам, естественно, гораздо выгоднее делать заказы в России, а не за рубежом.
Мы проводили опытные работы по проектированию конформного охлаждения. У университета есть программы, которые позволяют рассчитать форму каналов, оптимальную с точки зрения охлаждения, дальнейшая задача – вырастить этот элемент аддитивным способом. К примеру, можно получить сложную, разветвленную структуру внутренних каналов теплообменников, которую никаким другим способом не создать, и обеспечить очень высокую теплоотдачу. Это исключительно эффективное решение и для создания сложных изделий, и для литья под давлением легких сплавов, с последующим мелкосерийным производством.
Интересуетесь российским опытом внедрения 3D-технологий? Читайте статью Как опередить конкурентов: «СИБУР» осваивает аддитивное производство
Примеры аддитивного производства: детали камеры сгорания
Говоря о наших проектах, сложно выделить какой-то самый важный. Каждый, как говорится, становится родным, пока над ним работаешь.
Первые камеры сгорания и горелочные устройства мы напечатали в сотрудничестве с заводом «Металлист-Самара», который тоже активно занимается аддитивной тематикой. Сейчас мы перешли к сопловым секциям из жаропрочного сплава, планируем тестировать суперинварные сплавы.
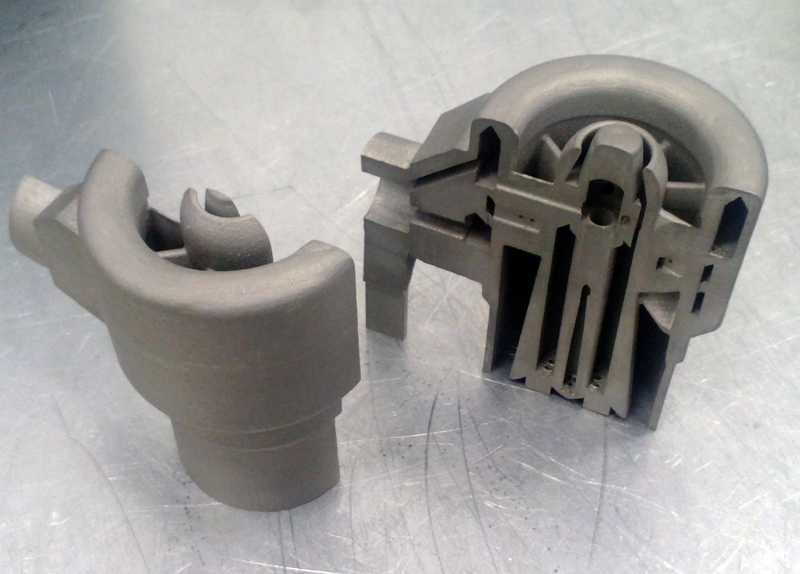
Для «Металлиста» мы создали горелочное устройство камеры сгорания газотурбинного двигателя. Первоначально сборка состояла из шести деталей. Нам удалось, используя SLM-технологию, сделать ее фактически цельной деталью и очень быстро получить хорошие результаты. Горелочное устройство стало легче (масса снизилась с 2 до 1,7 кг) и лучше по своим функциональным свойствам, а суммарная стоимость изготовления снизилась более чем в два раза.
Также мы работали над жаровыми трубами камеры сгорания. Это в определенном смысле сердце двигателя, и до сих пор не существует однозначных точных методов расчета параметров горения, потому что очень сложно обеспечить и полноту сгорания, и эффективность. Это процесс во многом эмпирический – делают один вариант, ставят на стенды, получают результат, анализируют его, и далее идут итерации. А поскольку изделие довольно сложное, подготовка следующего варианта занимает не один и не два месяца. Процесс доводки может длиться и пять, и даже восемь лет.
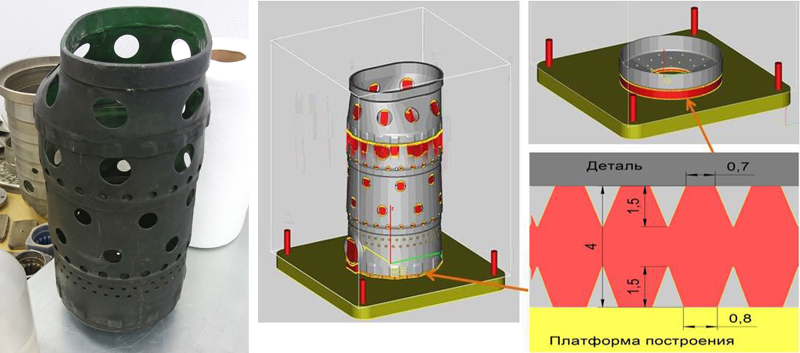
Справа: моделирование материала поддержки и назначение припусков / Изображение: Самарский университет
Материал – ВВ751П
Время изготовления – 39 часов
Вес – 2,5 кг
Благодаря аддитивной технологии новые варианты создаются очень быстро, поскольку сокращается процесс технологической подготовки и получение готового результата, и, соответственно, весь цикл упрощается. Время экономится в том числе за счет того, что за одну сессию, за пару дней, можно вырастить столько деталей, сколько уместится на платформе. При изготовлении малой партии получается не так уж дорого, иногда даже дешевле, как в случае с горелочным устройством.
О рентабельности 3D-печати металлами
Во-первых, нужно четко представлять, что можно сделать на 3D-принтерах. Во-вторых, если есть желание приобрести такую установку, можно сначала заказать печать изделия и сразу получить результат. Так многие наши клиенты делают: сначала заказывают детали, поставляют партию, потом просчитывают экономику. В конечном счете многие приходят к выводу, что лучше установку купить, чтобы получить максимальную выгоду. Это стандартный путь. Заодно они постепенно, пока вводят ее в действие, приобретают собственный опыт.
3D-установка печати металлами, конечно, окупаема – зависит от загрузки. У нас машина SLM 280 работает фактически круглосуточно. Оборудование не несет никаких силовых нагрузок и может эксплуатироваться долгое время, если иметь достаточные компетенции по его обслуживанию и ремонту. Определенные «узкие» моменты есть, но они все решаемы.
О «волшебном» 3D-принтере
3D-печать – не панацея. Как и у всякой технологии, у нее есть свои возможности и свои ограничения, и она сама по себе не дает готового изделия – для этого нужно решать комплекс задач. Неверно думать, что есть волшебный принтер: стоит нажать кнопку – и вы получите деталь необходимых размеров, с необходимыми механическими свойствами, с хорошим качеством поверхности. Сложнофункциональное изделие, которое мы выращиваем, – это заготовка, требующая и механической, и термической обработки. Все это в комплексе позволяет получить продукт с новыми свойствами. И внедряя аддитивную технологию, нужно понимать, что чуда не произойдет. Надо быть реалистом.
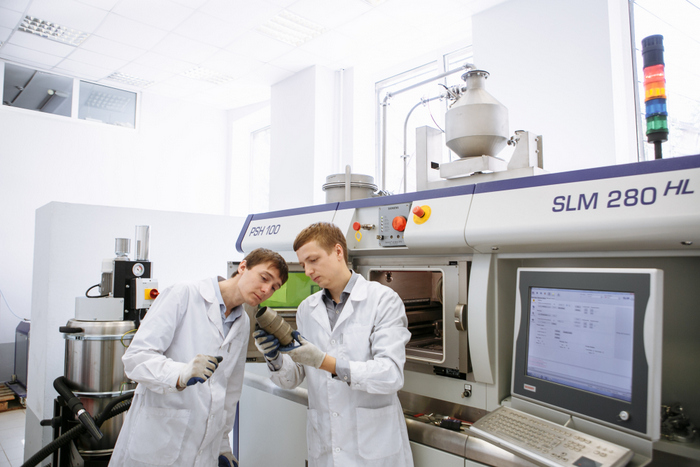
То, что 3D-принтеры целиком заменят традиционные инструменты производства, – это еще одно заблуждение. Но они – существенный элемент, который позволяет выйти на новый уровень.
Разумеется, 3D-печать развивается, оборудование становится более совершенным. Эти технологии не новые – первые опытные работы относятся еще к 1970-м годам. Прошли годы, прежде чем началось их промышленное применение и появились относительно дешевые металлопорошковые композиции. Сами 3D-принтеры уже перестали быть чудом: понятно, как их делать, из чего они состоят, появился опыт, более-менее известны все их «узкие» места.
Зачастую к нам приходят люди, имеющие слабое представление о возможностях 3D-печати и предлагают детали, которые можно получить другими способами, гораздо более дешевыми. Но есть и действительно интересные высокотехнологичные заказы, когда нужно сократить массу, получить новые функциональные свойства. Это всегда захватывающая работа, потому что она во многом исследовательская.
Главное в нашей работе – то, что мы сталкиваемся с действительными, не надуманными проблемами, которые существуют на производстве. И эти «живые» задачи позволяют лучше понять, на что способны аддитивные технологии, и разработать адекватные методики решения.
Статья опубликована 16.12.2019 , обновлена 10.10.2024