Классификация и группы титановых сплавов | Применение Ti6Al4V в аддитивном производстве | Bugatti оптимизирует гиперкар Bolide с помощью бионического дизайна и 3D-печати титаном | Кронштейн для самолета стал легче на треть | Благодаря титановому протезу пациент смог вернуться к нормальной жизни
Среди материалов, применяемых в 3D-печати металлами, особое место занимают титан и его сплавы, в особенности Ti6Al4V. Титан – это металл, который существует в природе в виде оксидов. Чаще всего встречаются рутил (TiO2) и ильменит (FeTiO3). Получение чистого титана производится методом Кролла.
Если не вдаваться в подробности, процесс выглядит следующим образом. Сначала хлорированием в присутствии оксида углерода при 1000 °C получают тетрахлорид титана (TiCl4). После этого с помощью магния или натрия оксид углерода удаляют в инертной атмосфере при 800–850 °C. В результате получается чистый титан. Абсолютно чистый титан добыть сложно из-за его высокой реакционной способности, поэтому на рынке за него принимаются образцы с чистотой 99,9%. По этой причине титан в основном используют в виде сплава с другими элементами.
Основными физико-химическими свойствами этого металла являются высокая механическая прочность, низкая плотность и высокая коррозионная стойкость. По этой причине титан и его сплавы – привлекательные материалы для различных отраслей, в том числе авиационной промышленности и медицины. Единственный существенный недостаток титана – дороговизна. Благодаря свойствам своих сплавов этот материал обладает огромным потенциалом для производства деталей и элементов аддитивным способом.
Поможет ли 3D-печать оптимизировать производство в вашей организации? Закажите бесплатную консультацию экспертов iQB Technologies!
Классификация и группы титановых сплавов
В зависимости от микроструктуры и фазового состава титановые сплавы делятся на три группы: α, α + β и β. Что такое микроструктура и фаза? Микроструктура – строение материала, различимое под оптическим или электронным микроскопом. По ней можно определить размер, форму и ориентацию отдельных кристаллов и гранул, из которых состоит материал. Также она в значительной степени определяет его физико-химические свойства. Фаза, наоборот, представляет собой участок материала с одинаковыми физико-химическими свойствами. Каждая фаза отличается от других по своей микроструктуре и/или составу. Обе эти характеристики зависят от скорости, с которой материал при остывании переходит из жидкого состояния в твердое, а также от применения термической обработки.
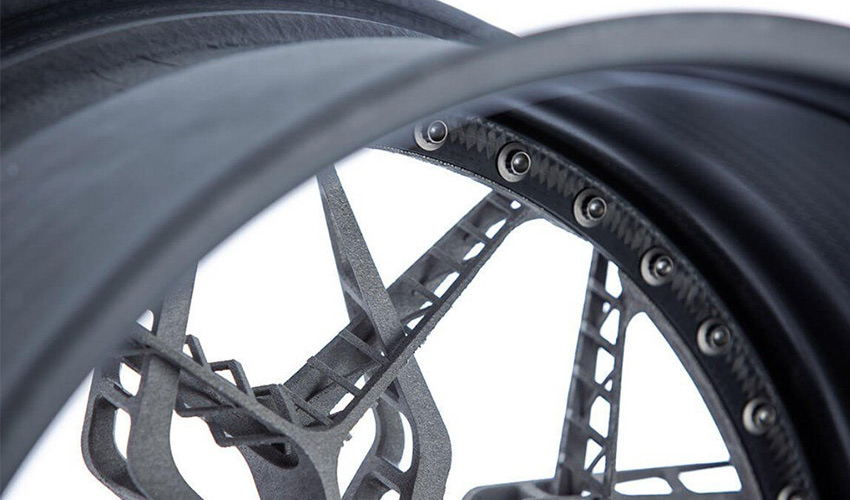
Сплавы распределяются по группам в зависимости от элементов, входящих в их состав помимо титана. В сплавах группы α преобладают α-стабилизаторы (алюминий, углерод, кислород, азот). В сравнении с остальными титановыми сплавами такие сплавы обладают относительно низкими механическими свойствами и высокой коррозионной стойкостью. Наиболее широко из этой группы применяются Ti3Al2.5V и Ti5Al2.5V.
Сплавы группы β разрабатывались для повышения механических свойств материала. В их состав входят β-стабилизаторы (железо, молибден, ванадий). К этим сплавам относятся, в том числе, Ti10.2.3, Ti555.3 и Ti17.
Наконец, существуют сплавы группы α + β. Они лучше всего изучены и содержат стабилизаторы обеих групп, в результате чего обладают микроструктурой смешанного типа и хорошим набором свойств. Наиболее широко применяется Ti6Al4V. Благодаря оптимальному соотношению между механической прочностью, пластичностью, сопротивлению усталости и трещиностойкостью его доля составляет 56% от всего рынка титановых сплавов. В зависимости от группы рынок сплавов делится в следующих пропорциях: 26% (α), 4% (β) и 70% (α + β).
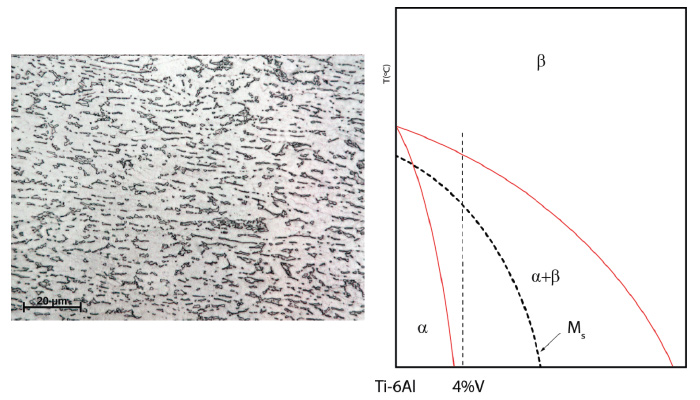
Эксперты iQB Technologies рекомендуют статью: 3D-печать металлами: краткие ответы на большие вопросы
Применение Ti6Al4V в аддитивном производстве
Если брать рынок в целом, сплав Ti6Al4V наиболее широко применяется в 3D-печати, поскольку обладает высокой прочностью, низкой плотностью, высокой коррозионной стойкостью и высокой биосовместимостью. Такой набор свойств делает его ценным материалом в таких отраслях, как автомобилестроение, авиакосмическая индустрия, медицина и биомедицина, стоматология, химическая, оборонная промышленность и в других сферах.
Перед началом 3D-печати с использованием Ti6Al4V сплав необходимо превратить в порошок. Это делается с помощью двух основных технологий: плазменной и газовой атомизации.
Плазменная атомизация применяется для производства особо чистого металлического порошка (Ti6Al4V). Сплав в форме прутка подается в емкость атомайзера и плавится под воздействием плазматрона. Падая, расплавленный металл застывает в форме сферических частиц.
Чаще всего применяется технология газовой атомизации. Расплавленный материал подается в сопло и распыляется с помощью инертного газа (аргона или азота). В потоке газа расплавленный материал затвердевает и распадается на сферические частицы, которые скапливаются на дне камеры.
Также читайте Тонкая работа: как 3D‑печать титаном меняет индустрию смартфонов
Выбор технологии производства металлического порошка (в данном случае – Ti6Al4V) чрезвычайно важен. От него зависят размер частиц и свойства порошка, что, в свою очередь, определяет характеристики конечного продукта. Сегодня на рынке представлены три промышленных сплава Ti6Al4V:
-
TC4, соответствующий стандарту GB/T 3620.1-2017;
-
Ti6Al4V класса 5;
-
Ti6Al4V класса 23, соответствующий стандарту ASTM B348-13.
Они отличаются друг от друга размером частиц, что ограничивает минимальную толщину печатного слоя. Чаще всего 3D-печать с помощью Ti6Al4V осуществляется по DMLS- или SLM-технологии. Выбор технологии зависит от типа детали и нужных характеристик.
Источник: 3dnatives.com
Bugatti оптимизирует гиперкар Bolide с помощью бионического дизайна и 3D-печати титаном
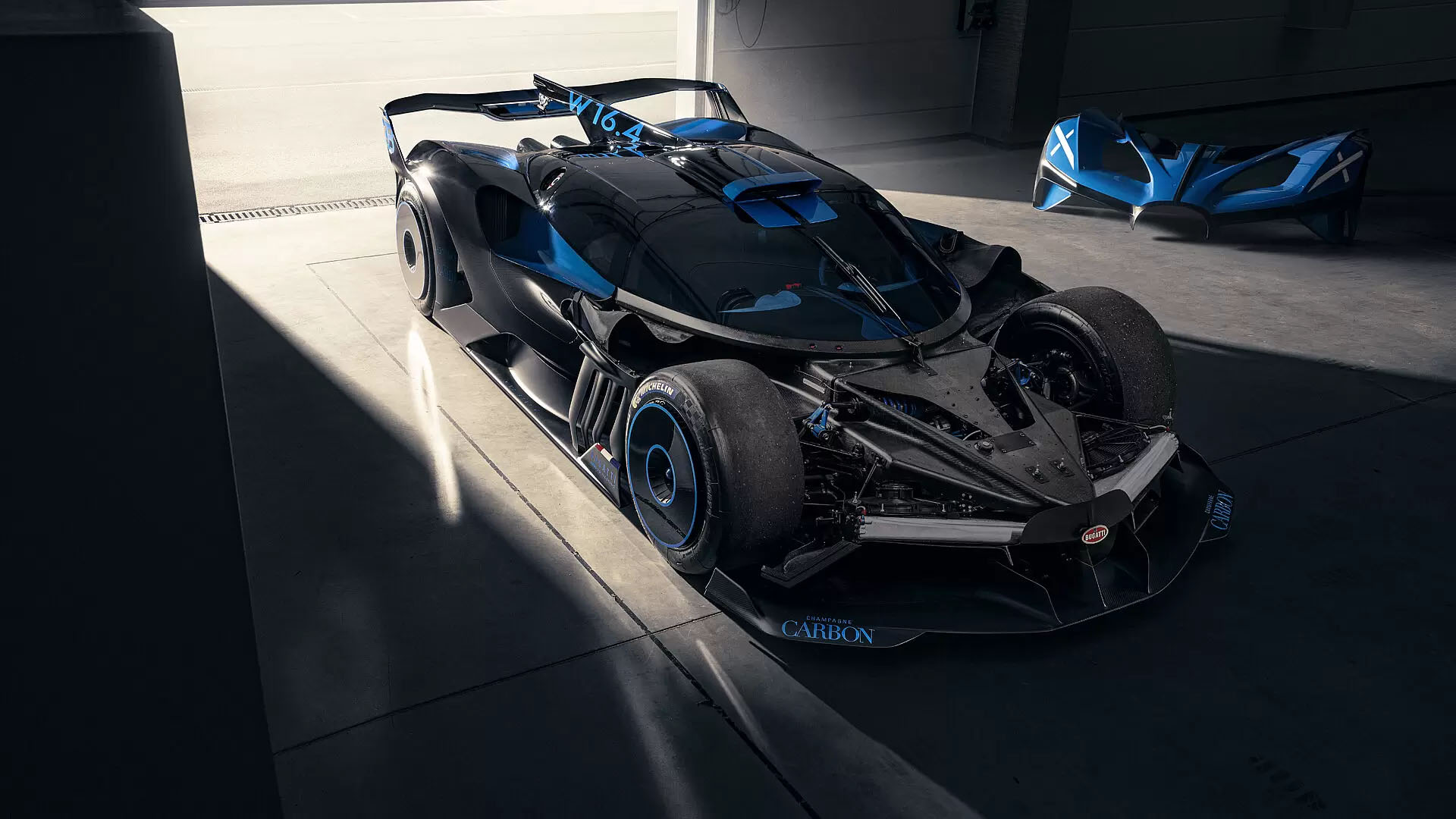
Производитель люксовых автомобилей Bugatti уже не первый год использует аддитивные технологии. Новые достижения 3D-печати были применены в разработке гиперкара Bolide, представленного в октябре 2020 года. Bolide оснащен восьмилитровым двигателем W16, весит всего 1240 кг и при этом способен разгоняться до более чем 500 км/ч.
Вдохновившись структурой кости, команда разработчиков создала на 3D-принтере автомобильные компоненты полой конструкции с тонкими стенками (до 0,4 мм) и мелкими разветвлениями. Использование бионического дизайна позволило придать деталям исключительную жесткость и в то же время значительно уменьшить их вес.
Из компонентов, произведенных для Bugatti Bolide аддитивным методом, особо выделяются штанги толкателя. Несмотря на легкий вес – всего 100 г – они могут выдерживать давление до 3,5 тонн.
Еще одна напечатанная деталь, которой особенно гордится Bugatti, – титановый кронштейн крепления заднего крыла гиперкара. При весе в 600 г кронштейн способен выдерживать аэродинамическую прижимную силу до 800 кг, при этом у него полая конструкция и толщина стенок 0,7 мм.
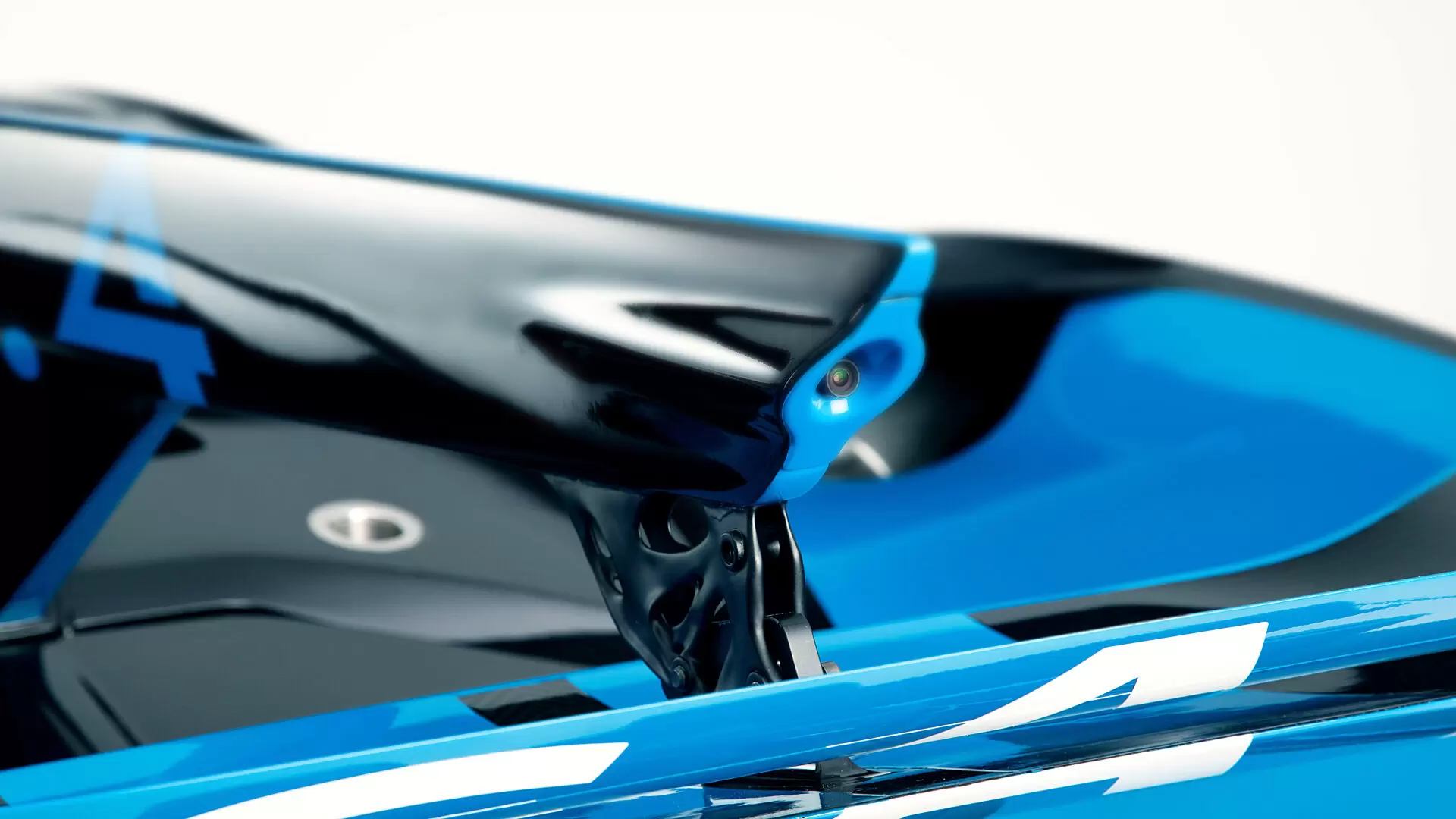
Ранее Bugatti создала тормозной суппорт из титана для гиперкара Chiron – он был первым, изготовленным на 3D-принтере, и самым большим в истории автомобильной промышленности. 3D-печать была выполнена на мощной 4-лазерной установке SLM 500. Титановый суппорт примерно на 40% легче и одновременно прочнее исходной алюминиевой детали.
Подробнее в статье: За 45 часов Bugatti сделала невозможное благодаря 3D-принтеру
Кронштейн для самолета стал легче на треть
S-образный кронштейн – элемент исполнительного механизма системы увеличения подъемной силы самолета, напечатанный из Ti6AI4V на установке SLM 280 компанией ASCO Industries. Его элегантная форма – результат жестких требований к распределению пространства и высоких нагрузок на посадочные поверхности. Изначальный проект предполагал изготовление кронштейна из высокопрочной нержавеющей стали и сложную механическую обработку.
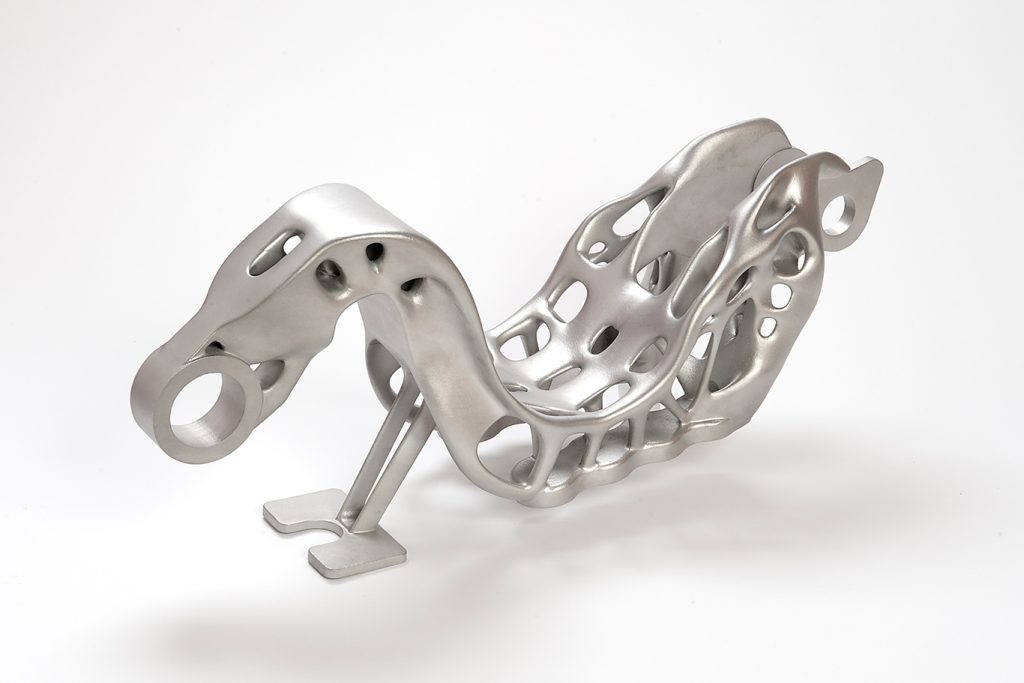
Конструкция изделия была переработана под аддитивное производство путем топологической оптимизации. Ее целью было минимизировать массу с сохранением необходимой прочности, позволяющей выдерживать аэродинамические нагрузки, оговоренные в проекте.
Результаты применения селективного лазерного плавления:
-
cнижение массы на 31% и сокращение общего времени сборки;
-
объединение трех деталей в одну;
-
уменьшение коэффициента использования материала с 17 до 1,5;
-
значительное сокращение времени механической обработки.
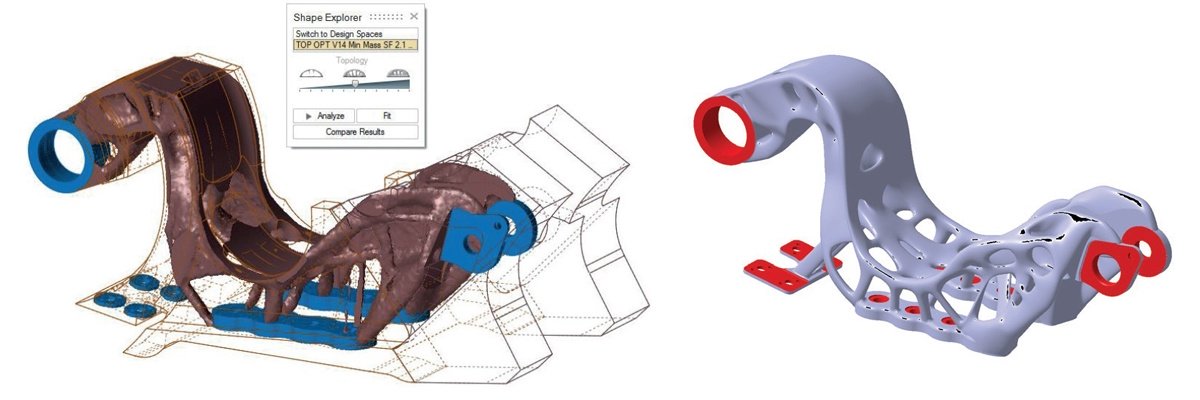
Подробнее в статье: Как снизить вес элемента конструкции самолета на треть
Благодаря титановому протезу пациент смог вернуться к нормальной жизни
Биосовместимость титановых сплавов (таких, как Ti6Al4V ELI) делает их идеальным решением для 3D-печати протезов костей челюстно-лицевой области, межпозвоночных дисков, ключиц, коленных суставов, лопаток, тазобедренных костей, имплантатов, а также различных медицинских приспособлений. В стоматологии эти материалы применяются для изготовления цельных имплантатов, а также металлических основ коронок и мостов из титана, кобальт-хрома и других сплавов.
Пациент в возрасте 81 года страдал от дефекта вертлужной впадины типа 3B по классификации Paprosky. Предыдущие ревизионные восстановительные операции этого пациента были неудачными из-за расшатывания чашечки и смещения в заднюю краниальную область.
Для проведения операции был спроектирован протез тазобедренного сустава aMace, индивидуально выполненный на 3D-принтере в соответствии с дефектом. Именно благодаря этому протез помог достичь нужной степени восстановления и фиксации.
Протез aMace (разработка компании Materialise) позволяет учесть все медицинские особенности пациента и сложные механические требования к этой важной подвижной части человеческого тела. Сложная пористая структура задней части изделия, обеспечивающая врастание кости, – особенность, которую легко можно воспроизвести с помощью 3D-печати.
Протез помог восстановить центр вращения с учетом нужного расположения и ориентации, а также обеспечил достаточную поддержку, несмотря на ограниченное количество костного вещества (особенно в задней краниальной области).
Итак, наиболее важными особенностями протезов, созданных с помощью 3D-печати титаном, являются:
-
отличная биосовместимость и идеальная геометрия, учитывающая индивидуальные особенности пациента;
-
отсутствие побочных эффектов и осложнений после операции;
-
уменьшение веса протеза, в том числе за счет возможности создания полой или пористой конструкции;
-
более быстрое в изготовлении и экономичное решение по сравнению с традиционными методами.
Подробности в статье: Протезы, созданные с помощью 3D-принтера, преображают жизнь пациентов
Фото в заставке: деталь передней стойки шасси бизнес-джета, напечатанная компанией Safran на установке SLM 800 © slm-solutions.com
Статья опубликована 26.11.2021 , обновлена 23.06.2025