Проблемы контроля геометрии мостовых секций | 3D-сканирование vs традиционный подход | FARO: ваш мост в будущее | Процесс 3D-сканирования и моделирования | Результаты применения 3D-сканера и ПО | Наши услуги
АО «Мостострой-11» – одна из крупнейших диверсифицированных компаний российской строительной отрасли. Предприятие работает на рынке с 1975 года, выполняя проекты транспортного, промышленного и гражданского строительства, в том числе строит, реконструирует и ремонтирует автодорожные и железнодорожные мосты, путепроводы. За годы своей деятельности компания сдала в эксплуатацию около трех тысяч объектов транспортной инфраструктуры. Свою миссию «Мостострой-11» видит в предоставлении высокотехнологичных и надежных строительных услуг и внедрении инновационных технологий и современных процессов производства.
Тюменский мостоотряд (одна из шести территориальных фирм АО «Мостострой-11») обратился в iQB Technologies, предполагая оптимизировать процесс контроля геометрии секций моста. Рассмотрев техническое задание, мы предложили заказчику наиболее передовые решения для контроля качества, которые сегодня имеются на рынке, – наземный лазерный 3D-сканер FARO Focus S150 и программный продукт Geomagic Control X. Эксперт направления 3D Юрий Фильцев (менеджер проекта) и технические эксперты Алексей Чехович и Кирилл Романов выехали на место для общения с заказчиком и демонстрации 3D-решений в работе.
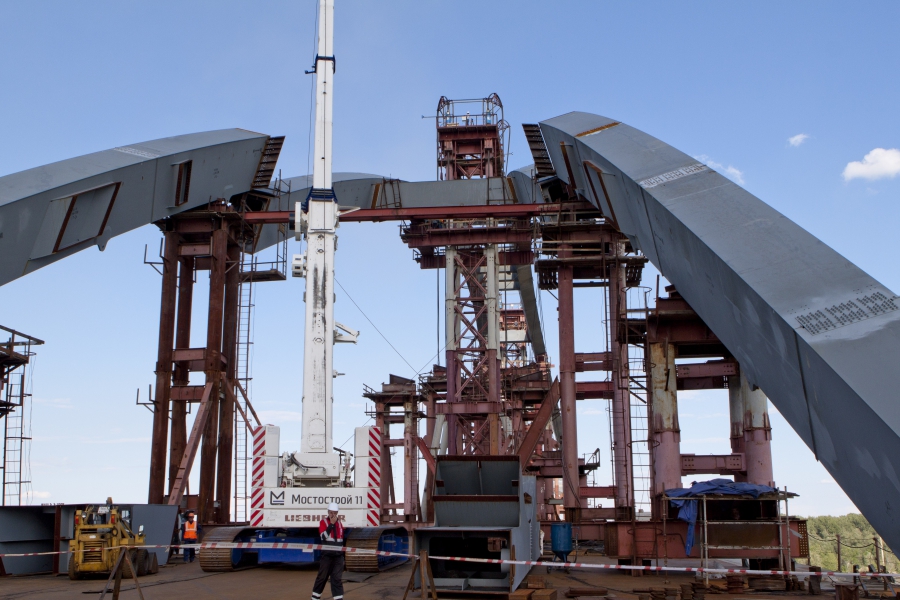
Проблемы контроля геометрии мостовых секций
Все мосты сейчас, за редким исключением, строятся из сборных металлических конструкций. Эти конструкции изготавливаются на заводе по секциям, которые перевозятся на место строительства и там собираются путем сварки и сболчивания. Одна секция состоит из четырех деталей, представляющих собой в собранном виде замкнутый короб. Смонтировать всю секцию реально и на заводе, но транспортировка такого габаритного груза не представляется возможной.
В процессе сварки в листе возникают внутренние напряжения, как следствие – происходят коробления и поводки. Это особенно критично для тюменского региона, ведь лето здесь короткое, и монтаж мостов приходится выполнять в основном в холодное время года.
Выгода использования 3D-сканера в сравнении с традиционными инструментами – не только в высокой точности, но и в достоверности информации. Сканер полностью исключает субъективность измерений.Алексей Чехович, главный технический эксперт iQB Technologies
По нормативам зазор между двумя секциями должен составлять от 8 до 11 мм. После того как сварено несколько швов, самую верхнюю, последнюю секцию прикладывают и вымеряют получившиеся зазоры. Обычно приходится подрезать торец у детали, однако не всегда это удается сделать с первого раза.
Таким образом, была поставлена задача контролировать геометрические размеры каждой секции на этапе производства и там же, в цеху, определять объем поверхности, которую необходимо срезать с каждого стыковочного листа, чтобы соблюсти нужные размеры. Посмотрим теперь, как этот процесс можно оптимизировать с помощью 3D-технологий.
Эксперты iQB Technologies рекомендуют статью Съемка сложных фасадов: 3D-сканер – вне конкуренции
3D-сканирование vs традиционный подход
Как выполняется контроль геометрии на предприятии классическим способом? «Каждую деталь обмеряют рулеткой или штангенциркулем, после чего осуществляется контрольная сборка: все детали выносят на улицу и пытаются собрать, – рассказывает Кирилл Романов. – На сборку уходит примерно семь дней. Если зазоры оказываются больше или меньше требуемых, детали возвращают в цех и дорабатывают. А когда у нас есть 3D-сканер, каждую деталь обмеряют, делают выводы о ее годности и сразу дорабатывают, если это необходимо. Контрольная сборка уже не требуется. Выгода налицо, учитывая, что один день простоя обходится в примерно 500 тысяч рублей».
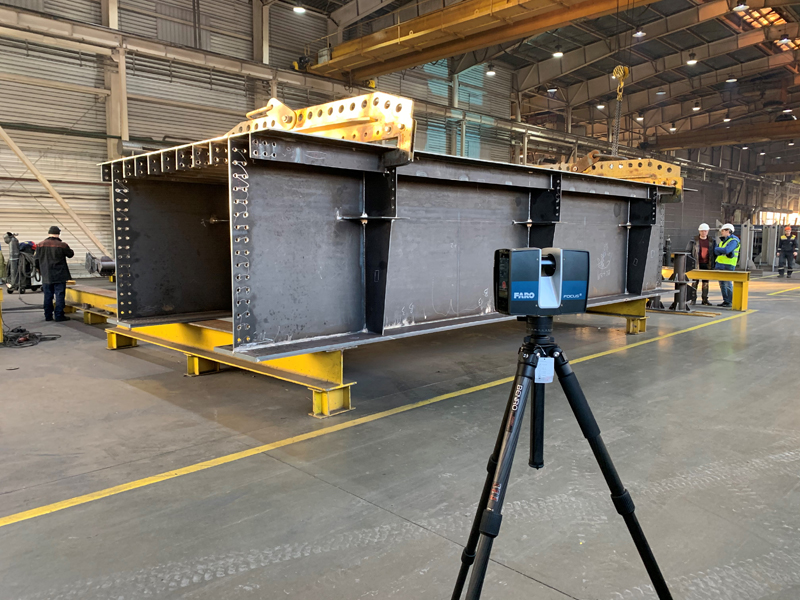
«Выгода использования 3D-сканера в сравнении с традиционными инструментами – не только в высокой точности, но и в достоверности информации, – добавляет Алексей Чехович. – Сканер полностью исключает субъективность измерений. Скажем, необходимо измерить расстояние между двумя ребрами. Что делает человек с рулеткой? Меряет деталь в двух-трех местах. А при сканировании каждая точка участвует в расчете, и сшивка скана производится с погрешностью 1,6 мм. Кроме того, есть вещи, которые проконтролировать рулеткой невозможно, к примеру, оценить плоскостность листа, перпендикулярность одного листа относительно другого».
Эксперты iQB Technologies рекомендуют статью: Мониторинг железнодорожных тоннелей: 3D-сканер FARO справится за несколько минут
FARO: ваш мост в будущее
FARO Focus – самые популярные в мире наземные лазерные 3D-сканеры, выполняющие задачи контроля качества и реверс-инжиниринга при работе с крупными объектами, зданиями, открытыми пространствами. Их отличает большая дальность действия (до 350 м), высокая точность, портативность, возможность эксплуатации в сложнейших условиях, простота в работе и эффективная интеграция с различными САПР. Все лазерные 3D-сканеры этого производителя внесены в Госреестр средств измерений РФ.
Модель S150, которую использует АО «Мостострой-11», – это бестселлер линейки Focus. Система способна сканировать в диапазоне от 0,6 до 150 м со скоростью до 2 млн точек в секунду. Повышенная точность измерений (уровень шума от 0,07 мм на 2 м) обеспечивается за счет компенсатора вертикального отклонения по двум осям и измерению углов.
ПО Geomagic Control X – своеобразный «золотой» стандарт на рынке специализированных программных продуктов для контроля качества. Control X может получить данные с любого 3D-сканера и предоставляет все необходимые инструменты для сравнения реального объекта с исходной CAD-моделью. Уникальность Control X заключается в его интуитивной понятности: с программой могут работать не только метрологи, но и любой производственный персонал, занятый в процессе контроля качества.
Процесс 3D-сканирования и моделирования
1. Производитель предоставил CAD-модель секции моста.
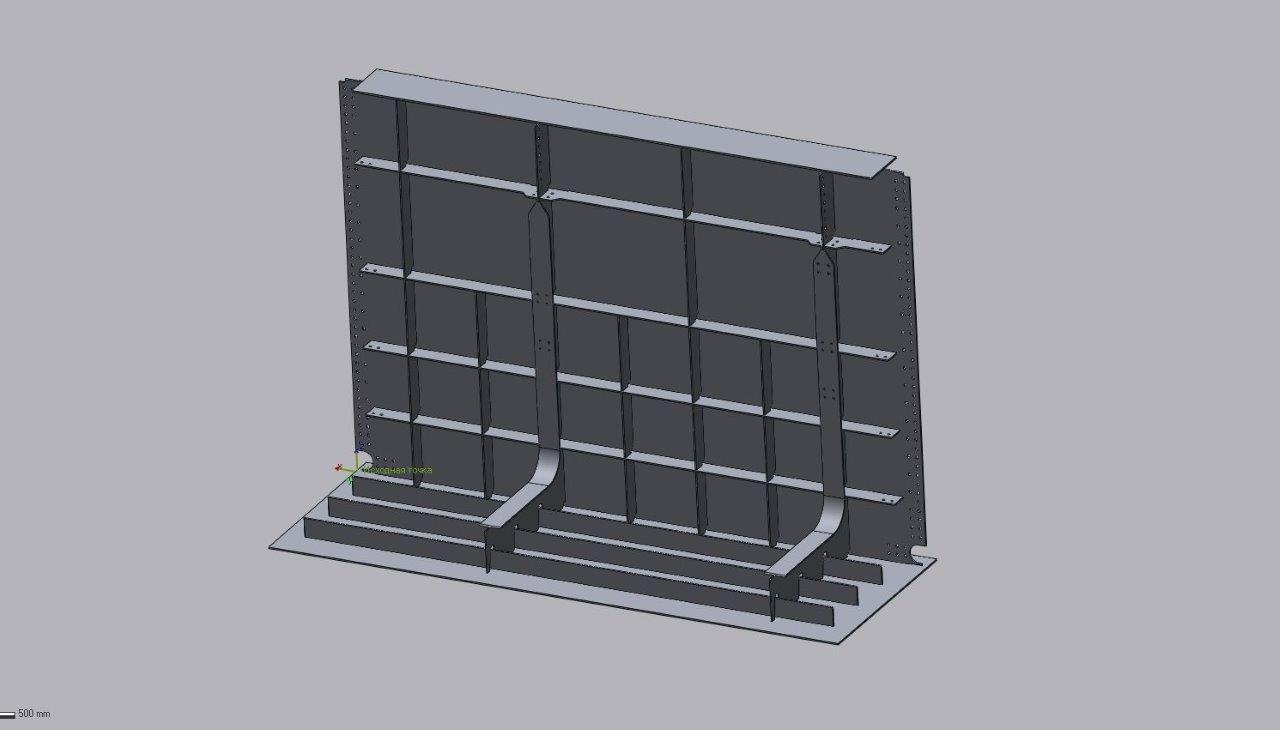
2. В цеху с помощью FARO Focus S150 произведено сканирование секции, получено облако точек.
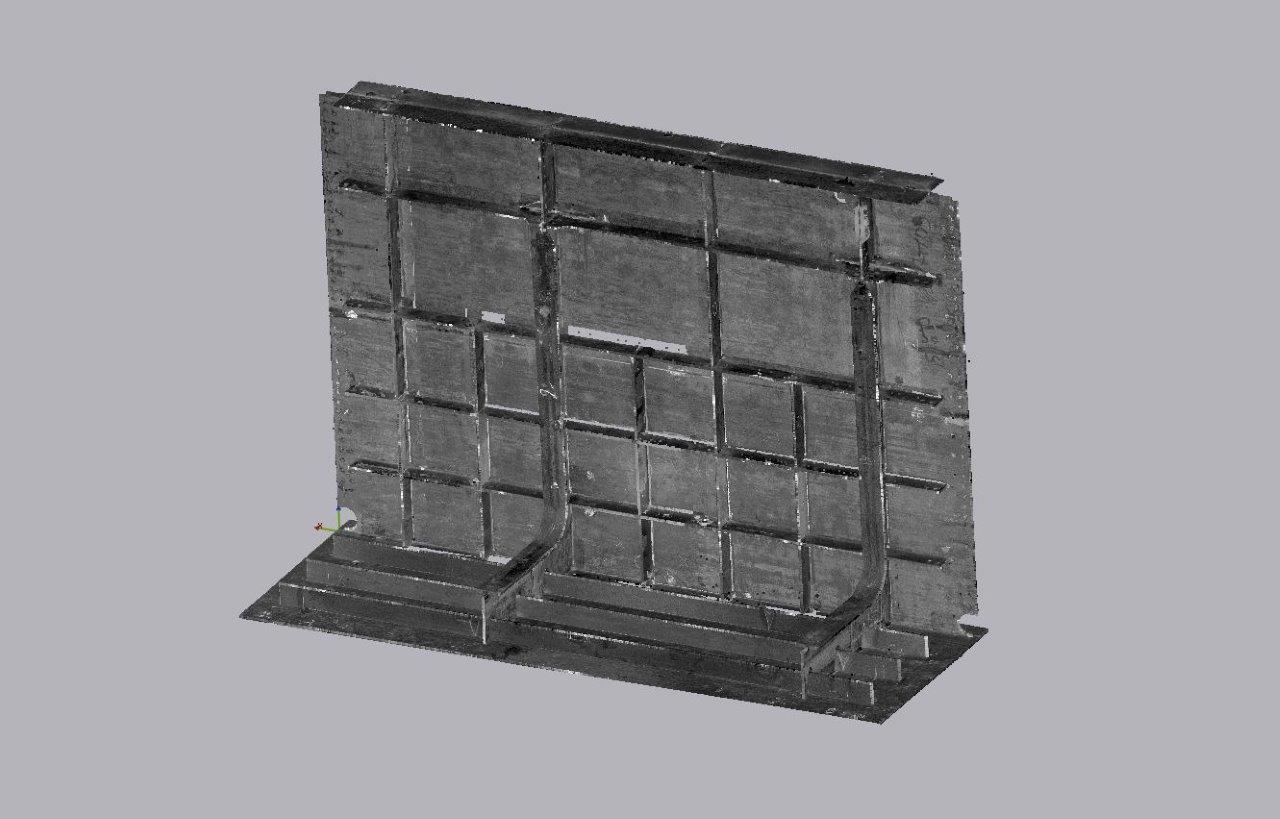
3. В ПО Geomagic Control X выполнено сравнение полученных данных с CAD-моделью и получена карта отклонений геометрии. Желтые и синие участки на карте – «хлопуны» и иные деформации листа, возникшие при сварке.
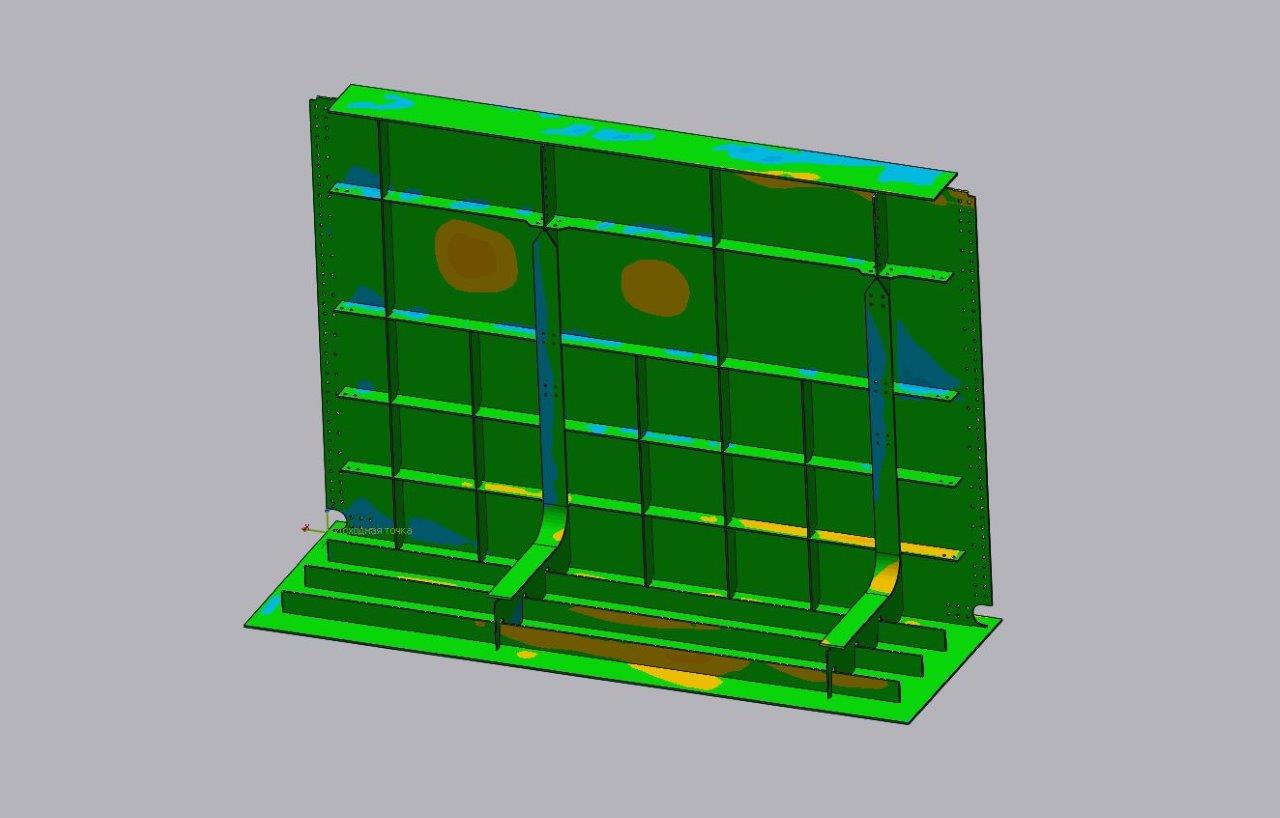
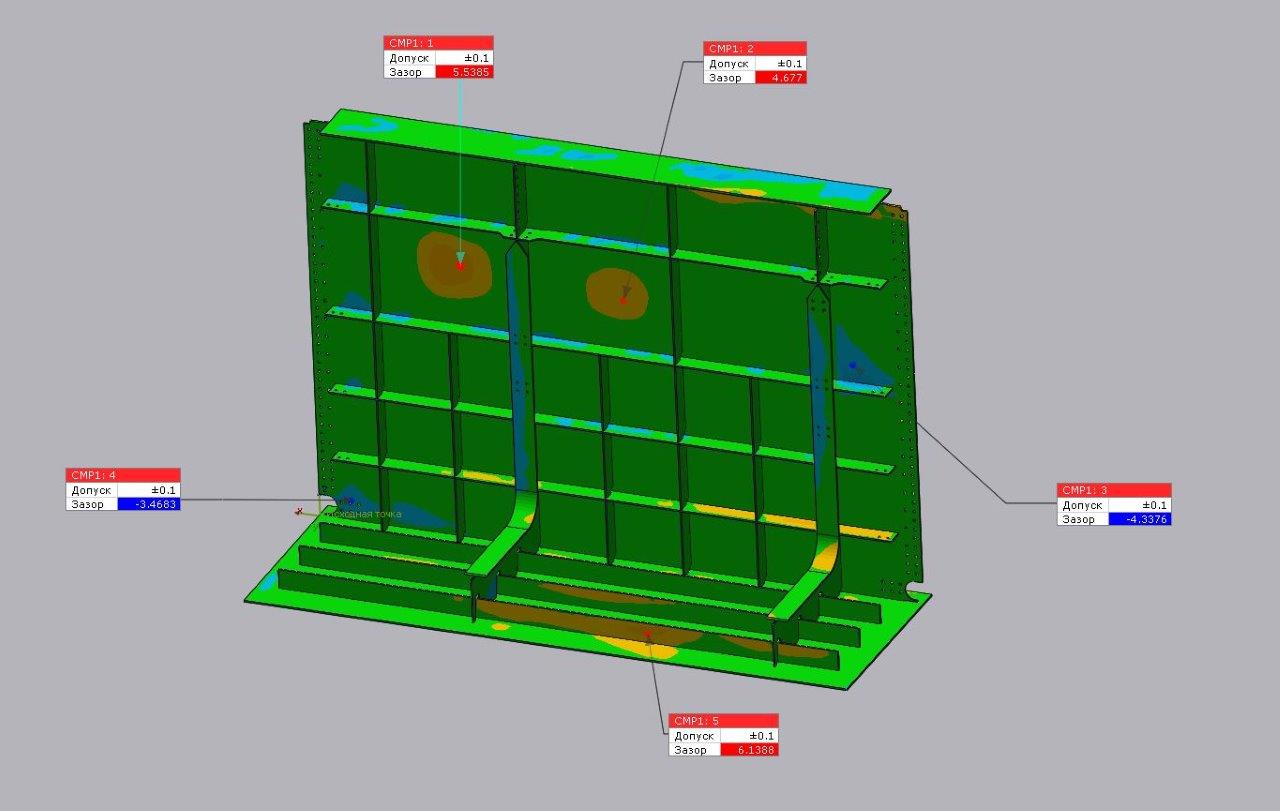
Результат проверки размеров:
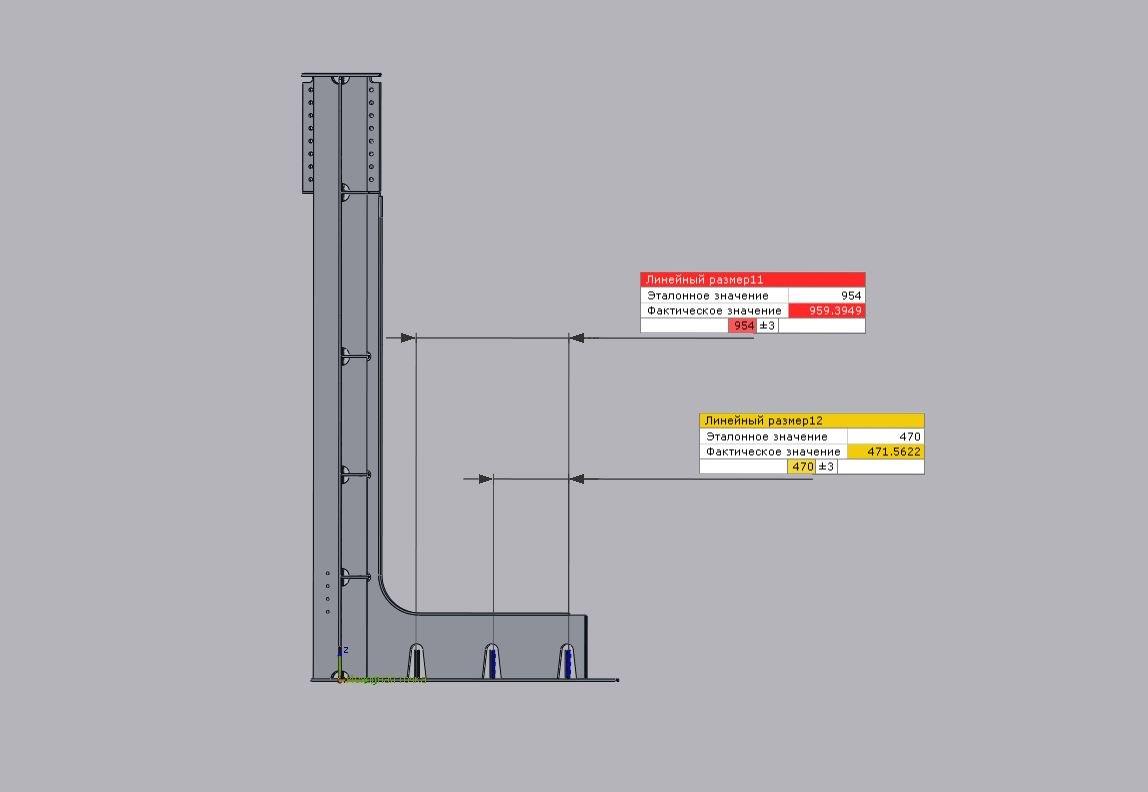
4. Проверка плоскостности и размеров в сечении. Отверстия сбоку – самые ответственные места в конструкции. Проверка двух крайних по диагонали отверстий выявила, что размеры укладываются в требуемый допуск 3 мм.
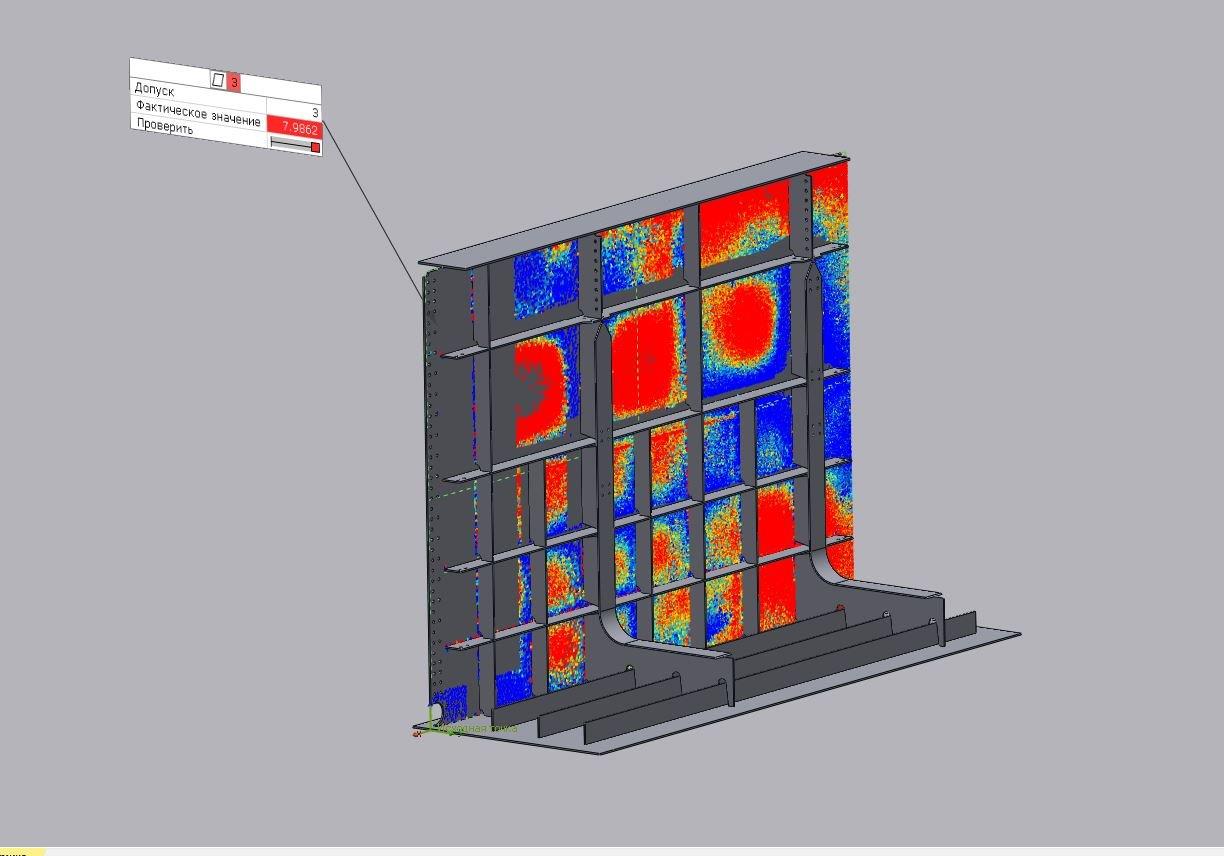
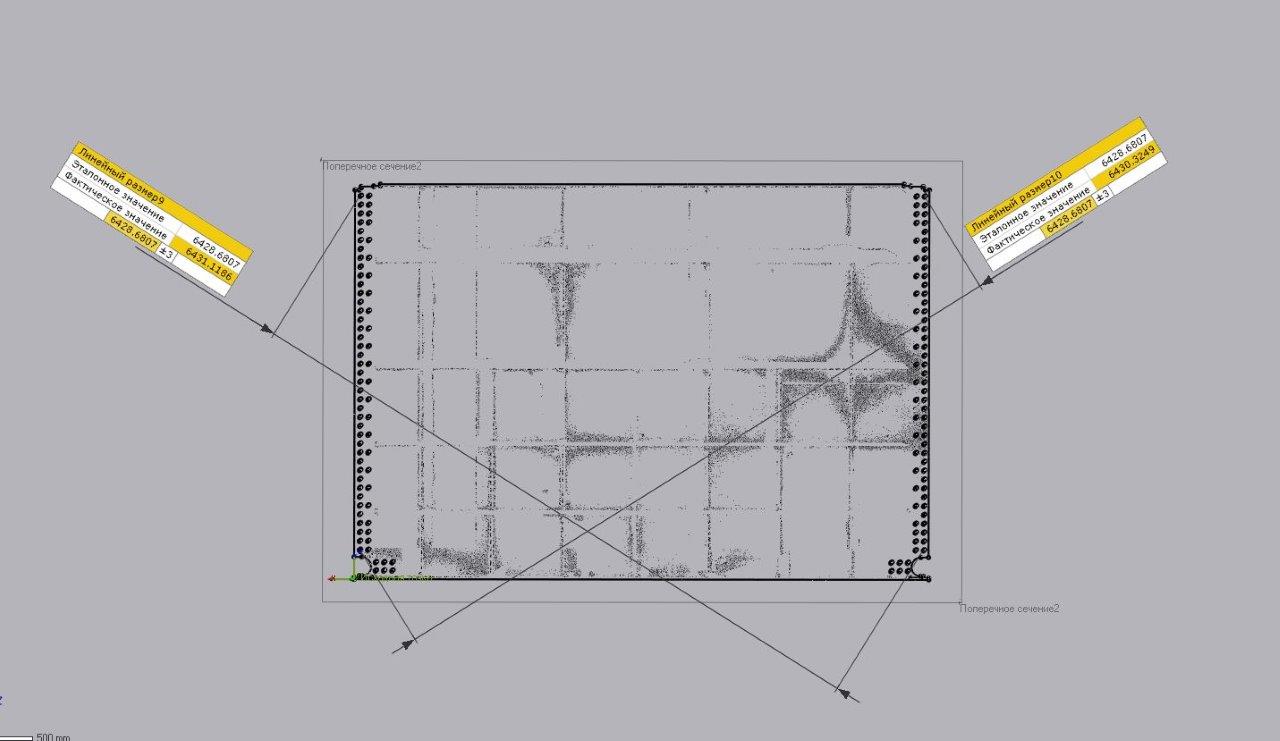
5. Проверка перпендикулярности:
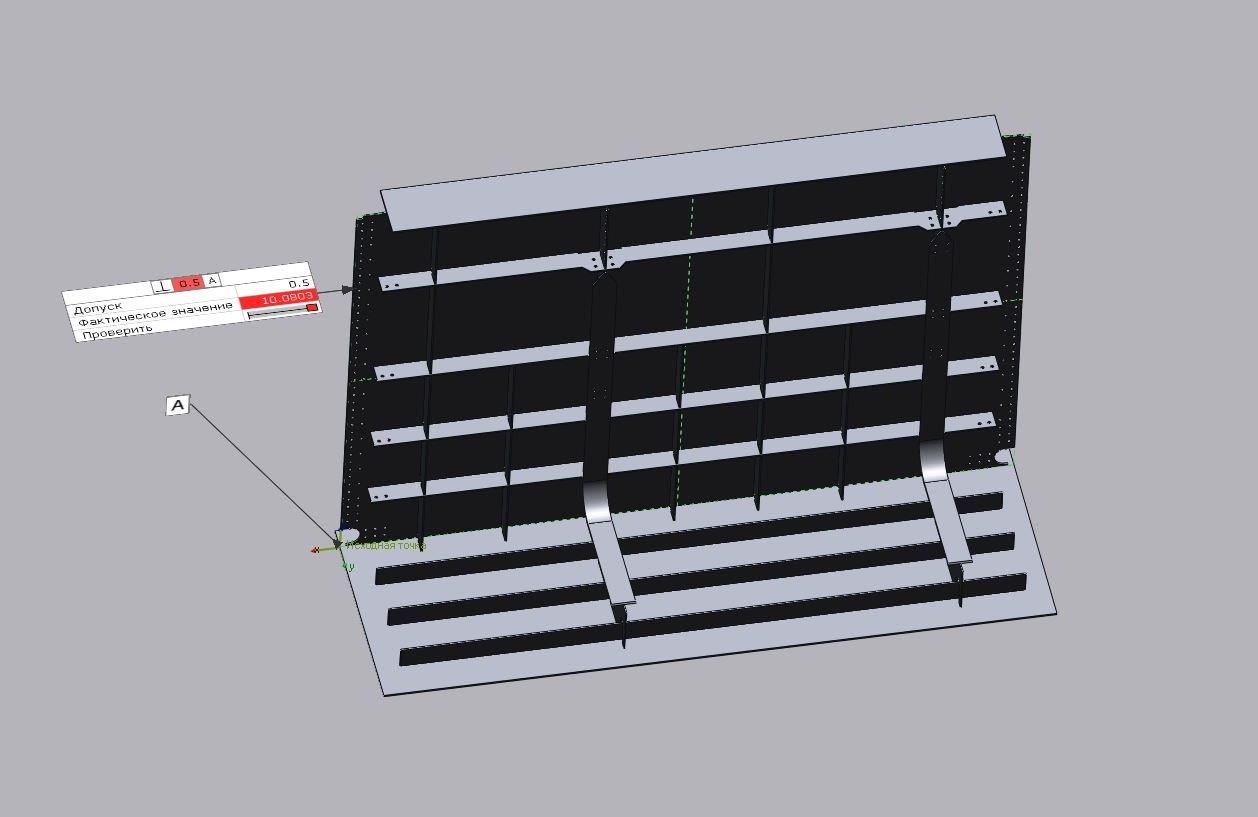
6. На финальном этапе автоматически генерируется метрологический отчет, который можно сохранить в любом требуемом формате. На основе отчета принимается заключение о годности детали.
«Мы измеряли плоскостность, перпендикулярность, прямолинейность, – комментирует Алексей. – У листа есть тонкий торец, и когда к нему что-то приваривают, он начинает изгибаться, как сабля. Его надо проверять на прямолинейность, поскольку он стыкуется со следующей деталью. Затем выполняется контроль расстояния между ребрами и общих габаритов – система может выдавать погрешности в автоматическом режиме».
Заказчик высоко оценил полученные результаты и новые возможности для повышения эффективности производственного процесса. Теперь в арсенале АО «Мостострой-11» есть современные, высокотехнологичные инструменты контроля геометрии, которые обеспечивают бòльшую точность, а значит, повышают надежность монтажа мостовых секций.
Также читайте Как отсканировать целое здание: от подготовки до первичной обработки данных
Результаты применения 3D-сканера и ПО
-
Повышение точности сборки и высокая достоверность данных (погрешность модели всего 1,6 мм). Модель содержит 14,5 млн точек.
-
Более высокое качество контрольной операции: благодаря цифровой модели можно отследить гораздо больше размеров и параметров.
-
Возможность выполнить проверку всех узлов конструкции, а не только отдельных элементов.
-
Возможность оценить плоскостность листа или перпендикулярность одного объекта относительно другого, что невозможно при использовании традиционных методов измерений.
-
Снижение вероятности ошибок, связанных с человеческим фактором.
-
Экономия времени и людских ресурсов, поскольку не требуется контрольная сборка.
Временные затраты
Время проверки секции – 1 час 20 минут.
-
полевой этап – 30 минут (сделано 8 стоянок с разрешением 6 мм, каждая стоянка заняла около 2 минут, 1 стоянка с разрешением 3 мм – 7 минут);
-
камеральный этап, или сшивка всех сканов в единую модель и ее выгрузка – 40 минут
-
доработка модели в ПО – 10 минут.
Команда высококлассных экспертов iQB Technologies поможет вам внедрить новейшие технологии и увеличить конкурентоспособность! У нас вы можете заказать следующие услуги: консультация экспертов, бесплатное тестовое 3D-сканирование/3D-печать, выезд специалистов на ваше предприятие, диагностика или заказ 3D-оборудования и ПО, обучение 3D-технологиям. Свяжитесь с нами прямо сейчас: +7 (495) 223-02-06, info@iqb.ru.
Статья опубликована 02.09.2020 , обновлена 31.01.2023