Центр аддитивных технологий | Сложности при внедрении 3D-технологий | Пример аддитивного решения: завихритель для ГТД | 3D-сканирование и контроль геометрии | Как рассчитывается экономический эффект
Рыбинское ПАО «ОДК-Сатурн», ведущее свою историю с начала XX века, – одно из высокоинновационных предприятий России. Компания входит в Объединенную двигателестроительную корпорацию Ростеха и занимается разработкой, производством и обслуживанием газотурбинных двигателей для военной и гражданской авиации, наземных газоперекачивающих агрегатов и электростанций, корабельных силовых установок. «ОДК-Сатурн» участвует в многочисленных амбициозных проектах, среди них – производство совместно с Safran Aircraft Engines силовой установки SaM146 для пассажирского самолета Sukhoi Superjet 100.
Инновации, внедряемые в «Сатурне», – это и цифровизация производства газотурбинных двигателей и их компонентов, и сквозная 3D-технология проектирования и подготовки деталей под аддитивное производство, и создание цифровых двойников цехов. Ведутся активные разработки и освоение композиционных материалов.
В 2000-х годах на предприятии начал формироваться центр аддитивных технологий, где методы селективного лазерного плавления (SLM), прямого лазерного выращивания (DMLS) и 3D-печати пластиками (SLA) используются для изготовления опытных образцов и «боевых» деталей газотурбинных двигателей. Применение топологической оптимизации (ПО Materialise Magics) позволяет усовершенствовать конструкцию, снизить вес, интегрировать несколько узлов в единое изделие, реализовать элементы бионического дизайна. Центр также участвует в деятельности по разработке и получению отечественных металлических порошков.
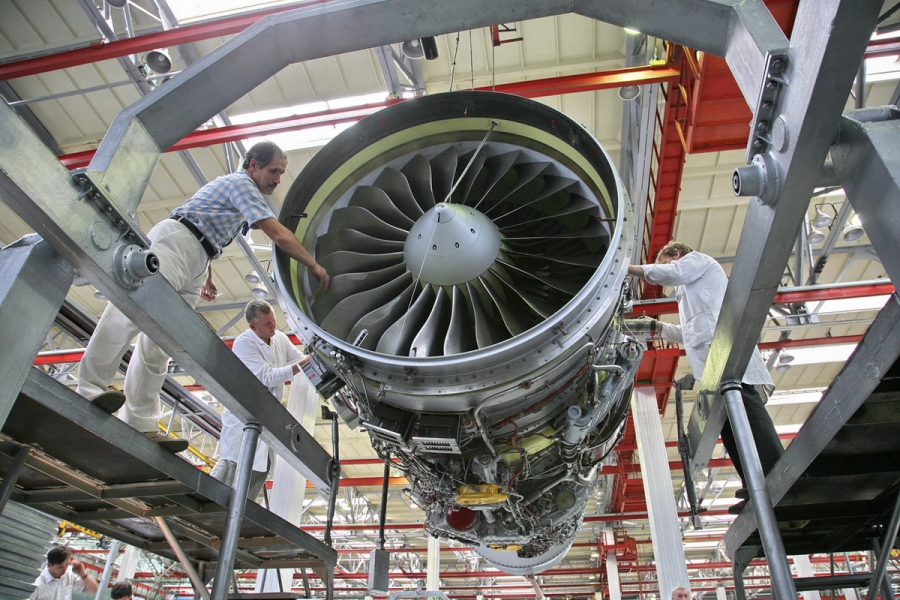
Объединенная двигателестроительная корпорация планирует использовать аддитивные технологии для выпуска отечественных газотурбинных двигателей, которые пройдут сертификацию в 2025–2030 гг. Напечатанные на 3D-принтерах компоненты будут составлять до 20% общей массы двигателя. Аддитивные методы дадут возможность в три раза сократить временные затраты и двукратно снизить стоимость производства серийных деталей.
«ОДК-Сатурн» является одним из организаторов Международного технологического форума «Инновации. Технологии. Производство», который проводится в Рыбинске ежегодно с 2014 года для представителей ведущих российских и зарубежных предприятий, НИИ и вузов. Новым решениям в области аддитивного производства посвящается отдельная сессия Форума.
Как работает аддитивное производство на одном из ведущих производственных предприятий России? Какие конкретно задачи решаются и в чем реальная выгода 3D-технологий для отечественной промышленности? На вопросы блога iQB ответил Эдуард Дубов, замначальника корпуса по технической части, специалист, стоявший у истоков центра аддитивных технологий «ОДК-Сатурн».
– Эдуард Юрьевич, с чего началось создание аддитивного центра в «ОДК-Сатурн»? Какие специалисты занимаются 3D-технологиями?
– Первые шаги к организации аддитивного производства были предприняты еще в 2003 году, тогда это был небольшой участок и всего одна установка. В 2013 году был организован корпус, размещено оборудование для 3D-печати, набрана команда, в которой сейчас несколько десятков человек. Когда был пройден этап внедрения оборудования, началась рутинная работа технологов. Технологи, прежде чем продумывать процессы, прошли обучение при монтаже и запуске аддитивных установок, изучали всё практически с нуля. Каждый из них разрабатывал технологические инструкции на конкретную единицу оборудования, изучая возможности 3D-принтеров, затем – возможности технологии, и дальше применял ее на практике.
Сегодня в «Сатурне» действует замкнутый цикл производства – от создания 3D-модели до выпуска конечного изделия. Помимо конструкторов и технологов, работает много специалистов смежных направлений – к примеру, металлургов, инженеров по прочностным расчетам, по неразрушающему контролю.
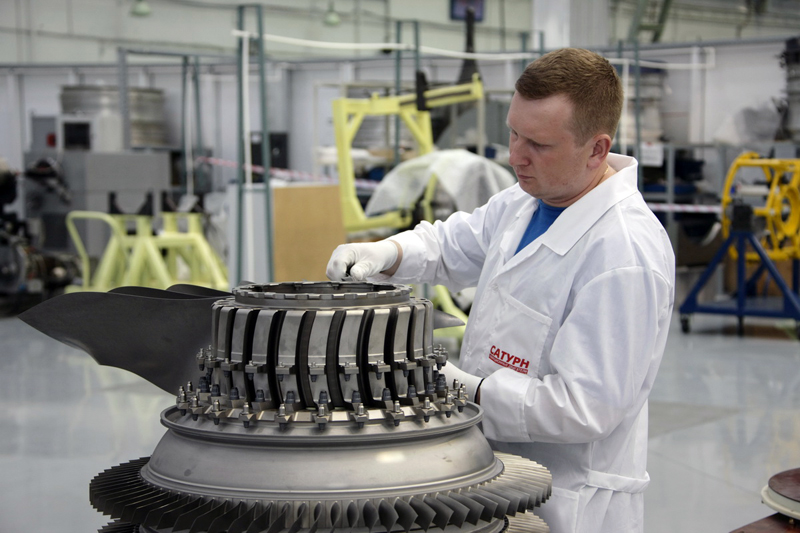
– Что было самым сложным на этапе внедрения?
– В аддитивном производстве очень многое зависит от того, как размещаются детали и поддержки. Когда объект «растет» в металлическом 3D-принтере, в металле возникают напряжения, и их необходимо учитывать в процессе установки всех деталей. С первого раза никогда не получится правильно деталь поставить. Поэтому у технолога должно быть хорошо развито пространственное мышление. Он должен знать деталь, видеть, как ее разместить на платформе, чтобы получить оптимальный результат. Вот такие проблемы были в начале, и мы постепенно их корректировали.
Эксперты iQB Technologies рекомендуют статью: 3D-технологии на взлете: тренды и задачи российского авиапрома
– С какими еще трудностями Вы сталкивались при интеграции 3D-решений в существующий процесс?
– Я думаю, главная проблема – это получение знаний, обучение персонала. Мы своих специалистов «выращивали» с 2003 года, параллельно с отработкой технологий. Сформировался костяк технологов, которые уже передают знания друг другу. Думаю, это одна из лучших, если не самая лучшая, команда специалистов по аддитивным технологиям в России.
– Какие задачи решаются на предприятии с помощью аддитивных технологий?
– Начиная от прикладных задач, например, создания оснастки для удобства механообработки, до каких-то глобальных – допустим, выращивания корпусных деталей под литье.
Кроме того, восстанавливаем детали (к примеру, вентиляторные лопатки), чтобы сократить затраты на изготовление новых. Технология восстановления на данный момент отработана на установке лазерной наплавки порошковых металлов, и в перспективе планируется уже серийное восстановление под турбовентиляторный двигатель SaM146.
3D-печать сразу дала увеличение производительности, потому что на одной платформе за 32 часа выращивается сразу несколько завихрителей
– Давайте возьмем одну задачу, выполненную аддитивным методом, и посмотрим, какие преимущества удалось получить по сравнению с традиционной технологией…
– Приведу самый простой пример – завихритель газотурбинного двигателя для электростанций. Это деталь представляет собой небольшой цилиндр сантиметров пять в диаметре, в нем находятся лопатки для создания факела распыла топлива внутри двигателя.
Когда завихритель делали традиционным способом – воск, керамика, литье, – возникала проблема: лопатки отрывались в литьевой форме. Было разработано решение, которое позволило сделать конструкцию завихрителя более технологичной. Получается, мы ушли от тонкостенных лопаток, сделали, по сути, в цилиндре обычные каналы. 3D-печать нам сразу дала увеличение производительности, потому что на одной платформе за 32 часа выращивается сразу несколько завихрителей. Выпуск такой партии готовых изделий, включая термическую и механическую обработку, занимает недели полторы. В комплекте таких завихрителей выходит более 100 штук, мы делаем их за 2-3 недели.
– Сколько времени на производство завихрителя уходило раньше?
– Они делались по одному, там много механической обработки, плюс создание восковок, литьевых форм. Это достаточно длительный цикл изготовления.
– А каковы результаты оптимизации по другим параметрам?
– Прочность завихрителя, созданного аддитивным способом, такая же, даже выше. Кроме того, по характеристикам распыл топлива при исследовании показал более стабильный факел, что для двигателя очень важно.
– Расскажите, пожалуйста, как происходит внедрение российских металлических порошков.
– Сейчас идет процесс паспортизации материалов совместно с ВИАМ. С отечественными сплавами будет гораздо более выгодно работать, когда мы их протестируем по образцам и начнем внедрение. Но отдельные материалы наши предприятия уже начали делать. Допустим, очень хорошее качество у титана ВТ6.
_800.jpg)
– Используете ли 3D-сканирование для реверс-инжиниринга и контроля геометрии?
– В нашем центре используем пока старые системы. Недавно приобрели большую роботизированную систему 3D-сканирования. Хорошим подспорьем был бы ручной 3D-сканер, который бы обеспечивал хорошее качество и был бы легким в работе. Этот вопрос мы прорабатываем.
При внедрении аддитивного производства в «ОДК-Сатурн» изначально был заложен стопроцентный контроль по геометрии. Проводится сравнение образцов с 3D-моделями, чтобы по геометрии всё строго соответствовало тем задумкам, которые мы планируем реализовать. Понятно, что любой материал имеет усадку и т.д., поэтому стараемся добиться результата, наиболее приближенного к идеальным условиям. И эта ответственная задача лежит как раз на технологе – он учитывает возможности и оборудования, и технологии.
Эксперты iQB Technologies рекомендуют статью: 9 шагов к созданию аддитивного центра на предприятии
– Как Вы считаете, что нужно, чтобы в России аддитивные технологии внедрялись более массово? Что этому мешает?
– Когда говорят, что внедрять их дорого и долго – это ошибочно. Естественно, требуются немалые затраты, но это работа на перспективу. Ни на одном производстве нельзя сразу получить экономическую прибыль.
– Кстати, как Вы просчитывали экономический эффект?
– Довольно просто. Получается, что материалы для аддитивного производства имеют высокую стоимость, но все компенсируется снижением трудозатрат и нормо-часов. И когда сравниваем, то результат получается примерно одинаковым, но здесь очень важный момент: деталь выпускается гораздо быстрее. В газотурбинном двигателе есть лопатки с внутренними каналами. Чтобы создать эти внутренние каналы, конструктор должен потратить до полугода. 3D-технологии значительно сокращают затраты: за полгода возможно изготовить несколько вариантов.
Итак, мы можем быстро внести изменения в конструкцию – это раз. Мы можем быстро это внедрить – два. И за определенный период мы можем сделать несколько итераций.
На фото в заставке: Эдуард Дубов с коллегами / Фото: «ОДК-Сатурн»
Статья опубликована 09.09.2019 , обновлена 04.03.2022