Как 3D‑печать полимером CF‑PEEK улучшает эксплуатацию бурового оборудования | Первый клинический случай имплантации ключицы с помощью 3D‑печати полиэфирэфиркетоном | PEEK в разработке пресс‑форм для производства обуви
PEEK, или полиэфирэфиркетон, считается одним из самых высокоэффективных функциональных материалов в мире. Он представляет собой полукристаллический термопласт, обладающий превосходной биосовместимостью, химической стойкостью, высокими механическими и термическими характеристиками. В отдельных случаях может стать альтернативой алюминию и даже сталям, при этом вес изделия будет меньше.
Благодаря своим уникальным свойствам полиэфирэфиркетон является одним из наиболее перспективных материалов для 3D‑печати, особенно при армировании угле- или стекловолокном. Применение PEEK в аддитивном производстве предполагает наличие FDM/FFF‑принтеров, поддерживающих высокотемпературные материалы.
PEEK используется для решения ответственных задач в таких областях, как авиакосмическая индустрия, автомобилестроение, химическая и нефтегазовая промышленность. Отличная биосовместимость, возможность многократного автоклавирования и модуль упругости почти как у костной ткани делают этот термопласт идеальным для создания эндопротезов и других медицинских приспособлений.
Рассмотрим несколько практических примеров аддитивного производства с помощью полиэфирэфиркетона в различных отраслях.
Интересуетесь 3D-печатью высокоэффективными пластиками или другими материалами? Подберем и поставим под ключ оборудование для вашего предприятия. Оставьте заявку на консультацию:
Как 3D‑печать полимером CF‑PEEK улучшает эксплуатацию бурового оборудования
Детали проекта
-
Размер изделия: 15 x 15 x 20 см
-
Объем использованного филамента: 100 г
-
Время печати: 4 часа
-
Стоимость: 52 USD
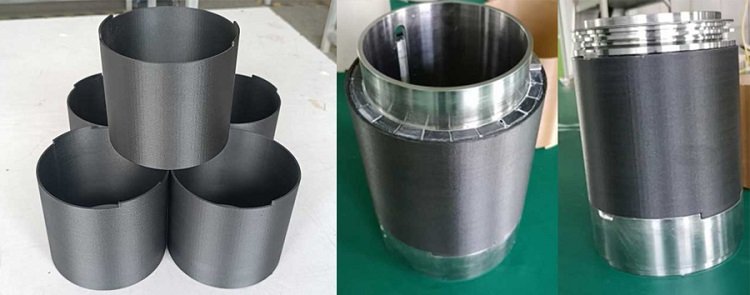
В системе управляемого роторного бурения нефтяных скважин ответственным компонентом является вращающийся трансформатор, используемый для стабильного электропитания в случае относительного вращения бурового оборудования. Чтобы обеспечить стабильную работу вращающегося трансформатора в условиях высоких температур и давления под землей, а также удовлетворить требованиям по легкости, производителю необходимо использовать высокоэффективные неметаллические материалы для изготовления корпуса вращающегося трансформатора (резольвера).
После технической оценки и анализа затрат был выбран высокотемпературный FDM‑принтер IEMAI MAGIC‑HT‑M для печати корпуса резольвера из CF‑PEEK – полимера, армированного углеродным волокном. В результате 3D‑печати получен легкий корпус резольвера, обладающий высокой прочностью, термостойкостью и устойчивостью к высоким напряжениям.
CF‑PEEK обладает превосходными механическими и термическими свойствами и высокой химической стойкостью. Он более легкий и износостойкий, чем стандартный PEEK, имеет лучшую межслойную адгезию, более высокую термостойкость и допускается к использованию в жестких условиях эксплуатации.
В ходе многократных сравнительных испытаний было установлено, что корпус, напечатанный на 3D‑принтере, полностью соответствует требованиям подземного бурения. По оценке заказчика, 3D‑печать позволит снизить стоимость не менее чем на 50% по сравнению с традиционными методами. До внедрения 3D‑принтера использовались прутки PEEK, но это приводило к 90% потерям материалов и затратам.
MAGIC‑HT‑M – 3D‑принтер, специально разработанный для печати высокотемпературными инженерными пластиками, с модульным износостойким экструдером, упрощающим печать материалом PEEK.
Первый клинический случай имплантации ключицы с помощью 3D‑печати полиэфирэфиркетоном
Стандартные медицинские имплантаты для лечения костных дефектов или деформаций не всегда эффективны из-за индивидуальных особенностей пациентов и различной степени заболевания. 3D‑печать позволяет быстро создать персонализированные и высококачественные эндопротезы, отвечающие специфическим потребностям пациентов.
В отделении торакальной хирургии Первой клинической больницы Куньминского медицинского университета для изготовления эндопротеза был выбран высокотемпературный 3D‑принтер IEMAI MAGIC‑HT‑L. Это первое в мире применение технологии 3D‑печати для создания протеза ключицы из PEEK. Такая операция решает и другие сложные проблемы пациентов с множественными поражениями, например, замену сосудов и резекцию опухоли.
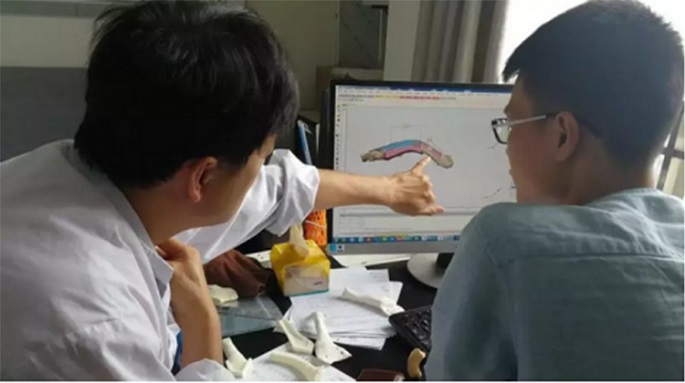
Эндопротезы, напечатанные из PEEK, обеспечивают такие преимущества, как кастомизация, высокая точность и близость к аутокости. В дальнейшем при лечении онкологических больных не будет препятствий для использования металлических материалов, они не влияют на КТ и МРТ, что полезно для последующей химиотерапии пациента и т.д.
Для первой операции был выбран материал PEEK. После неоднократных исследований, проведенных совместными усилиями врачей и инженеров, после модификации в CAD‑программах, многочисленных исправлений и демонстраций направляющая пластина и модель ключицы были окончательно доработаны.
У пациента (мужчины 57 лет) раковые клетки распространились на вены около правой подключичной и проникли в первое ребро. Чтобы выполнить резекцию вены под ключицей, пришлось отрезать ключицу. Если бы использовался традиционный метод, при котором используется титановая сетка для фиксации и закрепления после отсечения ключицы, это повлияло бы на последующее лечение пациента.
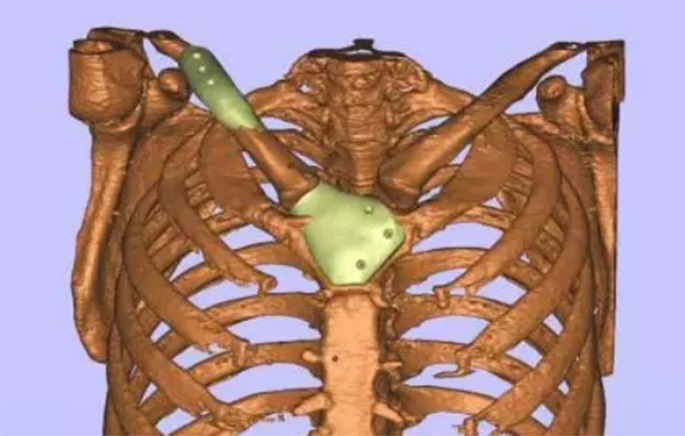
После двух недель подготовки пациент перенес всю серию операций по частичной резекции правой ключицы и первого ребра справа, резекции подключичной вены, замене кровеносного сосуда на искусственный, резекции правой верхней доли легкого и диссекции десяти средостенных лимфатических узлов под общим наркозом, а также по имплантации ключицы, напечатанной на 3D‑принтере. Процесс прошел гладко, результат был точным, и пациент хорошо восстановился после операции.
PEEK давно и активно используется в медицине: он обладает отличной биосовместимостью, а по модулю упругости аналогичен человеческой кости. В качестве искусственного костного материала он все чаще применяется вместо традиционного металлического титана и сегодня признан хорошим вариантом для костной пластики. С помощью 3D‑принтера можно создавать высокоиндивидуализированные точные протезы, что открывает для клинической медицины совершенно новые возможности.
Гиды по полимерам для 3D-печати: ABS | PLA | PETG | Композиты | Суперконструкционные пластики | Полиамиды | Поликарбонат
PEEK в разработке пресс‑форм для производства обуви
Детали проекта
-
Размер пресс‑форм: 100 х 251 х 45 мм и 100 x 251 x 53 мм
-
Объем использованного филамента: 1,2 кг
-
Время печати: 60 часов
-
Стоимость: 685 USD
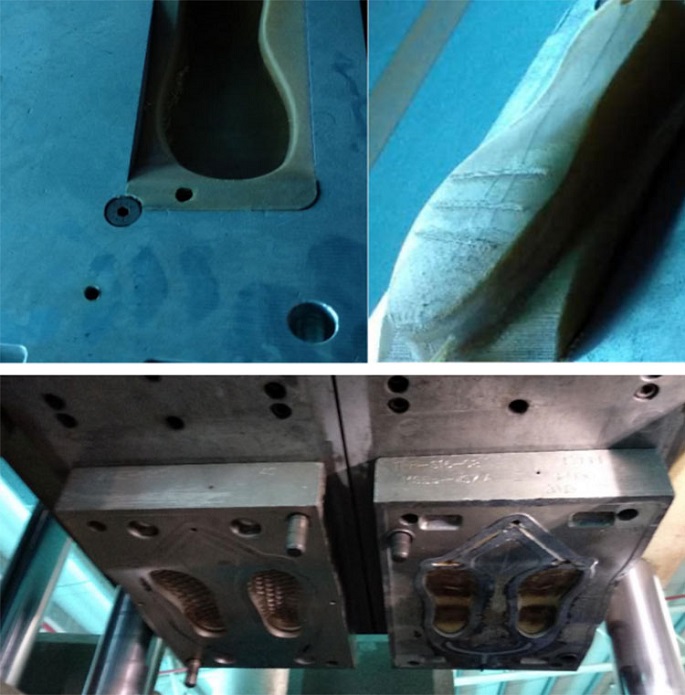
Свойства полиэфирэфиркетона также позволяют задействовать его в изготовлении обувных подошв. 3D‑печать приходит на смену традиционному методу производства и может значительно повысить эффективность разработки пресс-форм.
Классический способ изготовления предполагает, что пресс‑формы для подошв должны использоваться в течение длительного времени. Из‑за ограничений температуры и условий окружающей среды (180 °C и 140 бар), а также благодаря высокой механической прочности и легкости обработки PEEK оказался оптимально подходящим для этой задачи среди других материалов для 3D‑печати. Теоретически пластики PEEK могут использоваться в высокотемпературной среде (260 °C) долгое время и сохранять свои лучшие характеристики.
Прочность на растяжение изделий, напечатанных из PEEK, может достигать 63‑88 МПа, модуль растяжения – 3,35 МПа, прочность на сжатие – 55‑70 МПа, прочность на изгиб – 81,5 МПа, что является хорошими показателями для материалов. В целом такие пресс‑формы, напечатанные на 3D‑принтере, обычно используются только 3‑5 раз в процессе разработки, и окончательная форма делается из металла.
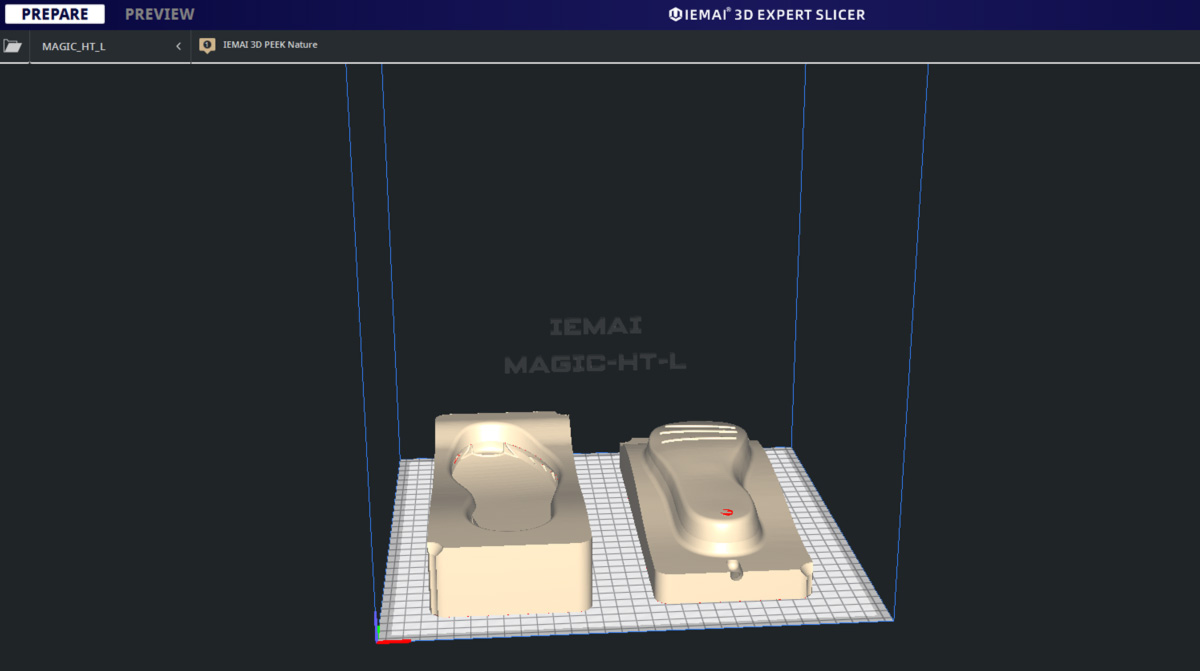
3D-печать позволяет быстрее реализовать проекты на этапе разработки пресс‑форм, повысить эффективность НИОКР и обеспечить соответствие всем критериям высокой температуры и высокого давления.
Компания Datang Xinxin Rubber and Plastic Co. Ltd, которая производит спортивное оборудование и товары для отдыха и выпускает пять миллионов пар обуви в год, выбрала для решения вышеуказанной задачи FDM‑принтер IEMAI MAGIC‑HT‑L. Машина обеспечивает разрешение слоя 0,05‑0,3 мм и отлично подходит для создания крупногабаритных форм из PEEK, при этом в процессе печати не происходит деформаций.
«Используя решения IEMAI для 3D‑печати, мы значительно сокращаем время, необходимое для разработки и проверки пресс‑форм, – отметил руководитель проекта Datang Xinxin Rubber and Plastic. – Мы верим, что технология аддитивного производства сможет изменить всю индустрию в будущем».
Материал предоставлен компанией IEMAI 3D
Статья опубликована 18.12.2023 , обновлена 10.10.2024