Соответствие жестким требованиям | Новая задача для испытанного 3D-принтера | Инновационная конструкция | Решение проблемы топологии поверхностей | Интенсивные испытания | Большой экономический потенциал
2015 и 2016 годы можно считать прорывными для технологии 3D-печати металлами (селективного лазерного плавления) в авиакосмической промышленности, поскольку ее стали использовать не только для изготовления опытных образцов, но и для производства деталей и узлов летательных аппаратов. За эти два года Airbus Defence and Space при поддержке 3D Systems удалось совершить поистине революционный прорыв.
Первый радиочастотный фильтр, напечатанный на 3D-принтере, прошел испытания и готов к использованию на коммерческих спутниках дальней связи. Финансирование проекта обеспечивалось Европейским агентством космических исследований.
Металлические радиочастотные и волноводные фильтры появились почти полвека тому назад вместе с первыми космическими системами связи. По своему принципу действия фильтры напоминают регулировщиков дорожного движения: они пропускают частоты одних каналов и отклоняют сигналы других.
Сегодня в авиакосмической отрасли наблюдается общая тенденция к увеличению мощности лучей на одном спутнике. На таком высокомощном спутнике, как Eutelstat KA-SAT (производство Airbus Defence and Space), установлено около 500 РЧ-фильтров и более 600 волноводов. Многие из них изготовлены на заказ и рассчитаны на определенные частоты.
Соответствие жестким требованиям Airbus
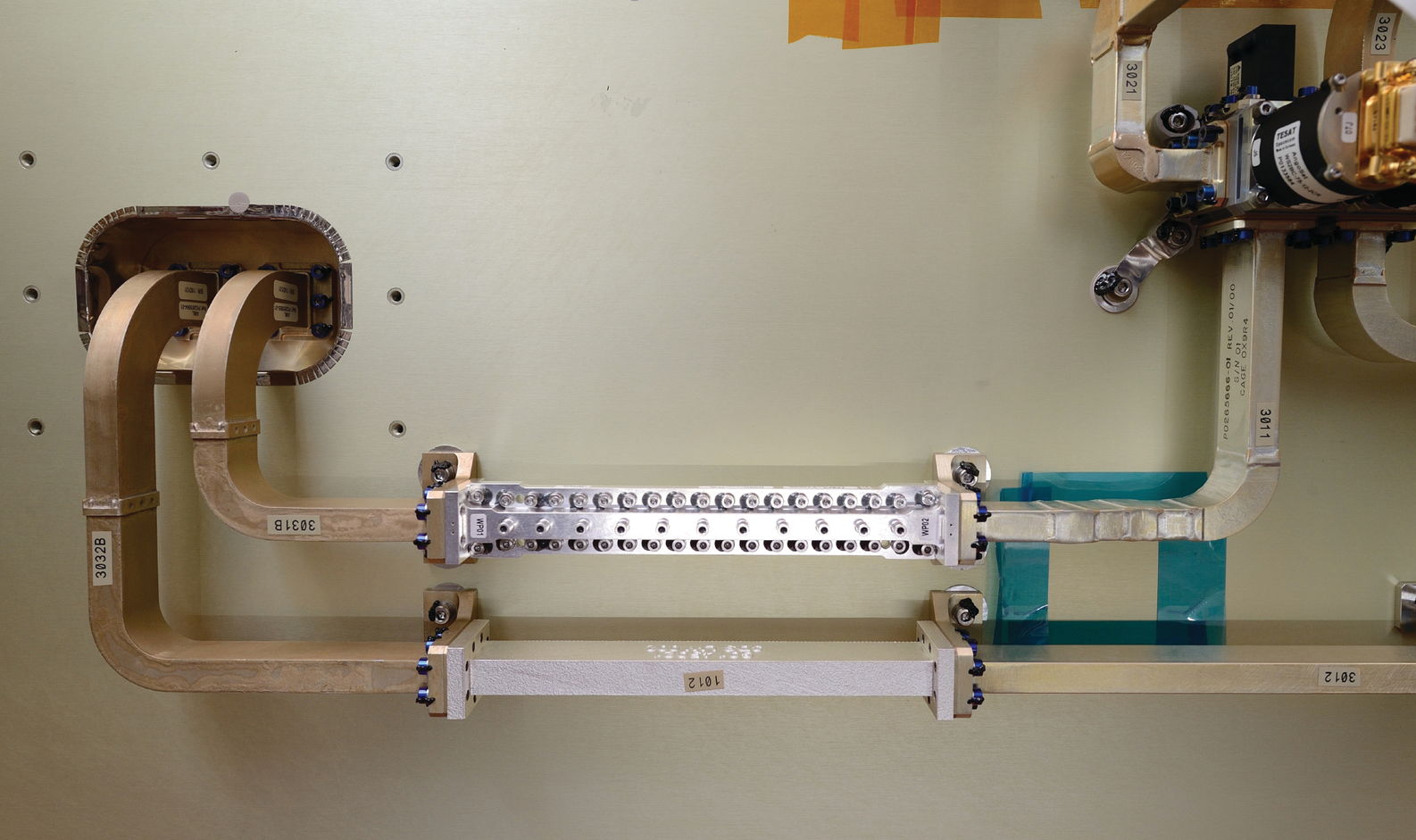
Спутники дальней связи — яркое свидетельство неустанного стремления отрасли уменьшить вес оборудования, потому что запуск спутника на геостационарную орбиту может обходиться в $20 000 за килограмм. Другими приоритетами являются непрекращающиеся инновационные разработки и сокращение сроков производства, поскольку срок службы большинства спутников – 10–15 лет.
Учитывая такие приоритеты, спутники дальней связи оказываются идеальными кандидатами на применение 3D-печати металлами. Принтер ProX® DMP 320 от 3D Systems, использованный для изготовления РЧ-фильтра для Airbus, позволяет изготавливать цельные детали, улучшать их функциональность за счет форм и поверхностей, которые невозможно получить традиционными способами, сокращать сроки производства и снижать затраты на индивидуальные заказы, а также уменьшать вес изделий, сохраняя и даже повышая прочность материала.
Новая задача для испытанного 3D-принтера
Подразделение 3D Systems в г. Левен (Бельгия) использует принтер 3D Systems ProX DMP 320 еще с тех пор, когда он только проходил бета-тестирование. Среди успешно выполненных проектов можно назвать топологическую оптимизацию, уменьшение веса и создание цельных, а не многоэлементных деталей, предназначенных для космических полетов, а именно кронштейнов и соединительной арматуры для спутников дальней связи. Специалистам подразделения 3D Systems в Левене, занятым в проекте Airbus Defence and Space, впервые пришлось работать с РЧ-фильтрами.
3D-принтер ProX DMP 320 призван обеспечить высокую точность и производительность в жестких условиях работы в круглосуточном режиме. Для достижения высокого качества изделий и стабильных характеристик специально для этого принтера был разработан и испытан широкий спектр сплавов LaserForm (титановые, из нержавеющей стали, алюминия, никель-хром и кобальт-хром).
Сменные отсеки с материалом построения обеспечивают широкие возможности применения и снижают непроизводительное время при переходе от одного материала к другому. Благодаря контролируемой вакуумной камере построения каждое изделие изготавливается с нужными свойствами, плотностью и химической чистотой материала.
Инновационная конструкция
Проект по изготовлению РЧ-фильтра для Airbus Defence and Space показывает, что с помощью технологии 3D-печати можно находить новаторские технические решения для компонентов для аэрокосмической отрасли – сферы, в которой десятилетиями не происходило никаких существенных изменений.
РЧ-фильтры обычно разрабатываются с использованием наборов стандартных элементов, таких как прямоугольные резонаторы и поперечные сечения волноводов с перпендикулярными отводами. Формы и соединения диктуются стандартными технологическими процессами, например, фрезерованием и электроэрозионной обработкой. В результате резонаторы РЧ-фильтров обычно приходится делать из двух половин, которые скрепляются болтами. Это увеличивает вес изделия, добавляет еще один шаг в технологический процесс и требует дополнительной проверки качества.
Проектирование элементов для 3D-печати дало Airbus Defence and Space возможность изучить сложные геометрические формы без дополнительных производственных затрат.
РЧ-фильтры для 3D-печати разрабатывались с использованием стандартной программы электромагнитного 3D-моделирования CST MWS с небольшой оптимизацией. Применение 3D-печати увеличило технологическую гибкость и сделало возможным появление конструкции с резонатором вогнутой суперэллипсоидной формы. Такая уникальная форма позволила проводить токи высокой частоты и найти оптимальное соотношение между коэффициентом качества (показатель эффективности волновода на основе потерь энергии) и подавлением сигналов, не входящих в диапазон.
«Инновационный прорыв состоит в том, что конструкцию оборудования теперь определяет чистая функциональность, а не возможность производства», – говорит Коэн Хейбрехтс (Koen Huybrechts), инженер-проектировщик 3D Systems в Левене. – Этот проект – классический пример формы как производной функции».
«К основным преимуществам монолитной конструкции, ставшей возможной благодаря применению 3D-печати, относится снижение массы, затрат и времени», – утверждает Пол Бут (Paul Booth), инженер по РЧ-технологиям в подразделении Airbus Defence and Space в г. Стивенидж (Великобритания). – Массу удалось снизить за счет того, что отпала необходимость в использовании крепежных элементов. 3D-печать металлами также без каких-либо дополнительных расходов дает такое преимущество, как более плотное прилегание внешнего профиля к внутреннему, поэтому расходуется ровно столько металла, сколько реально необходимо. Экономия времени и средств вызвана сокращением этапов сборки и постобработки».
Решение проблемы топологии поверхностей
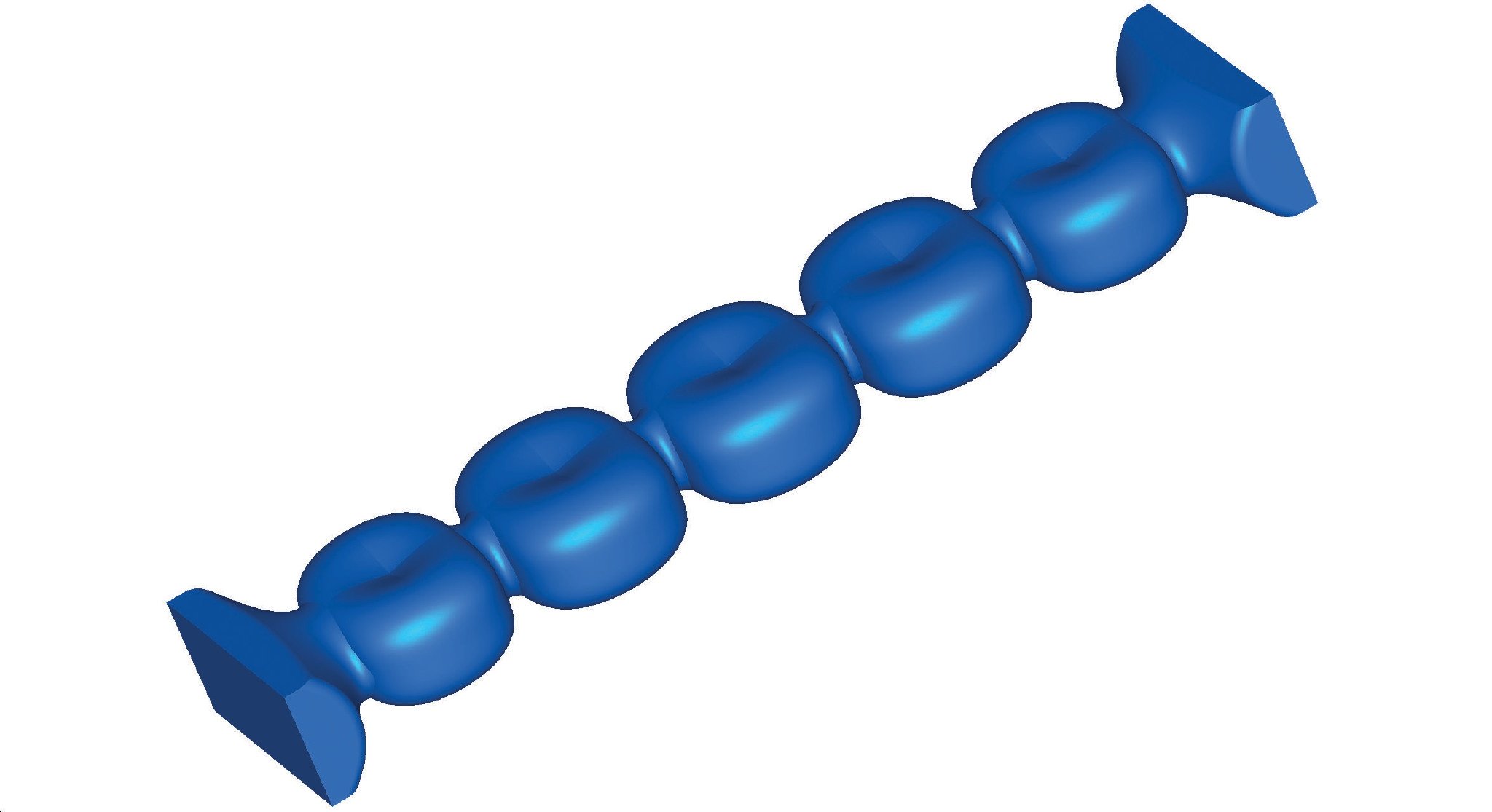
Сначала разработчики думали, что различия в топологии поверхностей деталей, напечатанных на 3D-принтере, создадут проблему, но после многочисленных испытаний специалисты Airbus Defence and Space сняли все опасения.
«Поверхности, обработанные механическим способом, имеют острые выступы и выемки, – поясняет Бут, – тогда как поверхность деталей, напечатанных на 3D-принтере, представляет собой сплавленные эллипсоиды, поэтому она более гладкая».
«Сферическая форма частиц металлического порошка, используемого для 3D-печати, приводит к некоторой волнистости и отсутствию резких переходов, – отмечает Хейбрехтс, – но возможность создавать форму детали для более эффективной фильтрации сигнала с лихвой преодолевает все опасения, связанные с топологией поверхностей».
«Мы очень довольны работой, которую проделала для нас 3D Systems. Многие специалисты Airbus отметили высокое качество поверхности, – заметил Бут. – Мы провели рентгеновскую дефектоскопию и были впечатлены плотностью материала и общим качеством поверхности».
Интенсивные испытания
Airbus Defence and Space на своем заводе в Стивенидже провела испытания трех алюминиевых образцов, напечатанных на принтере ProX DMP 320, с разными типами обработки. В ходе испытаний были воспроизведены условия, которым будут подвергаться изделия во время запуска и нахождения на орбите, включая вибрацию, ударную и тепловую нагрузки (перепады температур и вакуум). Все три образца показали либо соответствие требованиям, либо их превышение, причем наилучшие результаты были у фильтра с посеребренной поверхностью, полученной путем электролиза.
Помимо 3D-печати, сотрудничество с 3D Systems принесло и другую, важную для такого рода проекта выгоду, включая помощь сертифицированных специалистов при работе с металлическим порошком, технологический контроль для обеспечения высокой плотности материала, постобработку и надежный контроль качества.
По мнению Бута, опыт и знания 3D Systems сыграли ключевую роль в успешном исходе проекта: «Мы понимаем, что успехом проекта мы обязаны не только хорошему оборудованию, но и отличному пониманию технологического процесса специалистами 3D Systems».
Большой экономический потенциал
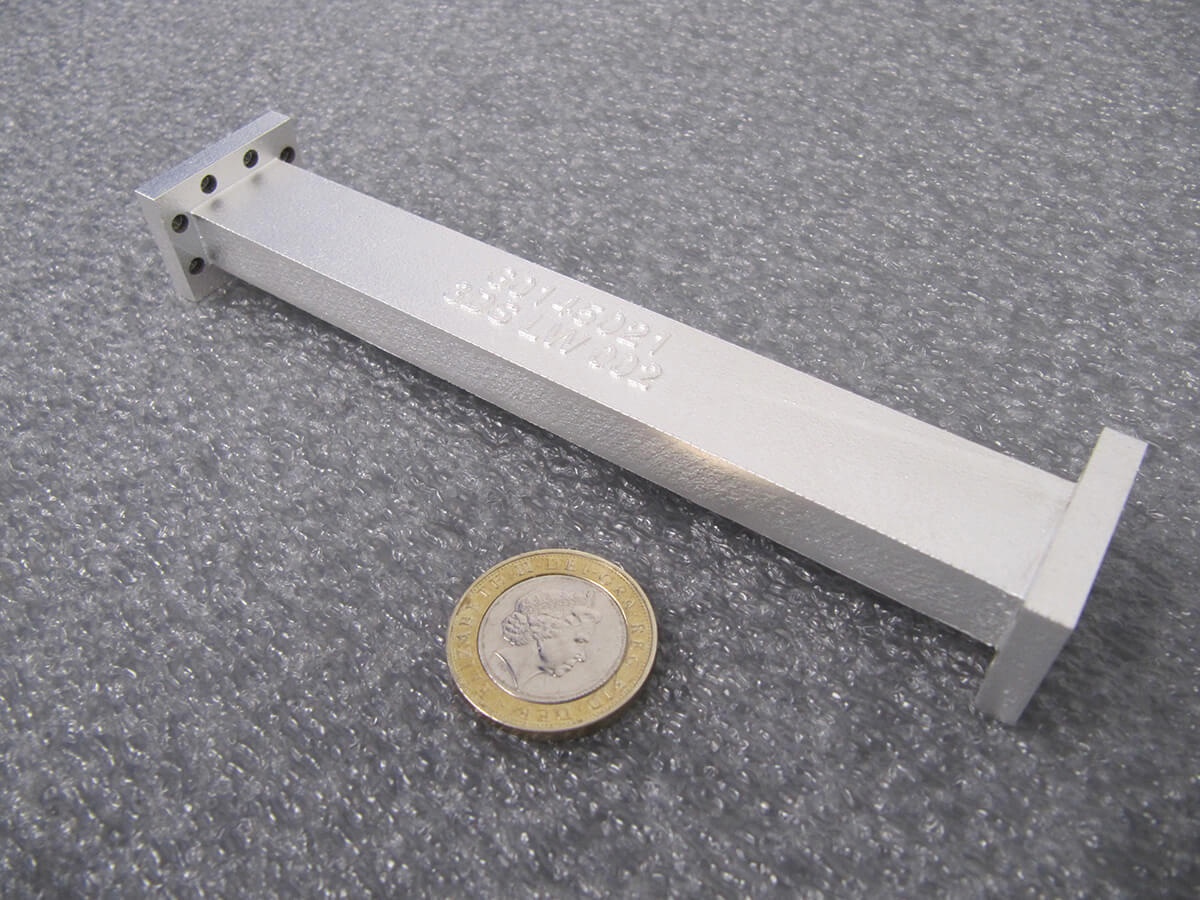
Теперь, когда процесс отработан и изделия подтвердили свое соответствие жестким стандартам авиакосмической отрасли, действующим в Airbus Defence and Space, компания начала расчеты потенциала рентабельности инвестиций в технологию 3D-печати металлом. От того потенциала рентабельности, что показал проект, могут загореться глаза у любого финансового директора: сокращение сроков производства, снижение производственных затрат и уменьшение веса вдвое!
«Нам удалось уменьшить массу, не тратя время на оптимизацию, – комментирует Бут, – причем путем доработки конструкции ее можно будет дополнительно уменьшить. Снижение массы поможет сэкономить топливо для двигателей ракеты, а также снизить нагрузку на опорные конструкции, что, в свою очередь, позволит еще больше уменьшить вес.
Успешная реализация этого проекта открывает перспективы для более тесной интеграции РЧ-фильтров с механическими и термическими элементами, с тем чтобы уменьшить число деталей и общую массу оборудования. Мы надеемся еще больше расширить функциональные возможности спутников, например, включив в фильтры или непосредственно в волновые тракты тестовые соединители. Мы видим в 3D-печати огромный потенциал в плане снижения массы, а также сокращения затрат и сроков производства».
Компания iQB Technologies предлагает вам заказать одну из следующих услуг: консультацию экспертов, обучение 3D-технологиям, тестовую 3D-печать/3D-сканирование, выезд специалистов на ваше предприятие, диагностику или заказ 3D-оборудования.
Статья опубликована 20.09.2017 , обновлена 08.04.2021