Проблемы | Решение | Контроль геометрии пресс‑форм | Проверка первого изделия и контроль качества | Итоги: кратко
Современная обрабатывающая промышленность способна производить высококачественные пластиковые изделия в огромных масштабах. Однако на качество деталей из пластиков, изготовленных методом литья под давлением, влияет множество факторов – от пресс‑формы до всевозможных параметров обработки, коэффициента использования полимерных материалов и тому подобного. Даже небольшая ошибка может привести к нарушению качества во всем процессе массового производства.
Проблемы
Типичный пример: производители пластиков сталкиваются с проблемами, связанными с прогибом плиты пресс‑формы. Прогибы могут возникать при высоком давлении и отражаться на форме, ослабляя тем самым ее конструкцию и влияя на качество конечных изделий. Важно обеспечить строгий контроль прогибов формы, особенно для сложных деталей с жесткими допусками.
Проверка размеров деталей для контроля отклонений пресс‑формы может помочь инженерам своевременно оценить ее качество. Задержки при проверке форм и при аттестации эксплуатационных характеристик влияют на весь цикл сборки, доставки и продажи продукции.
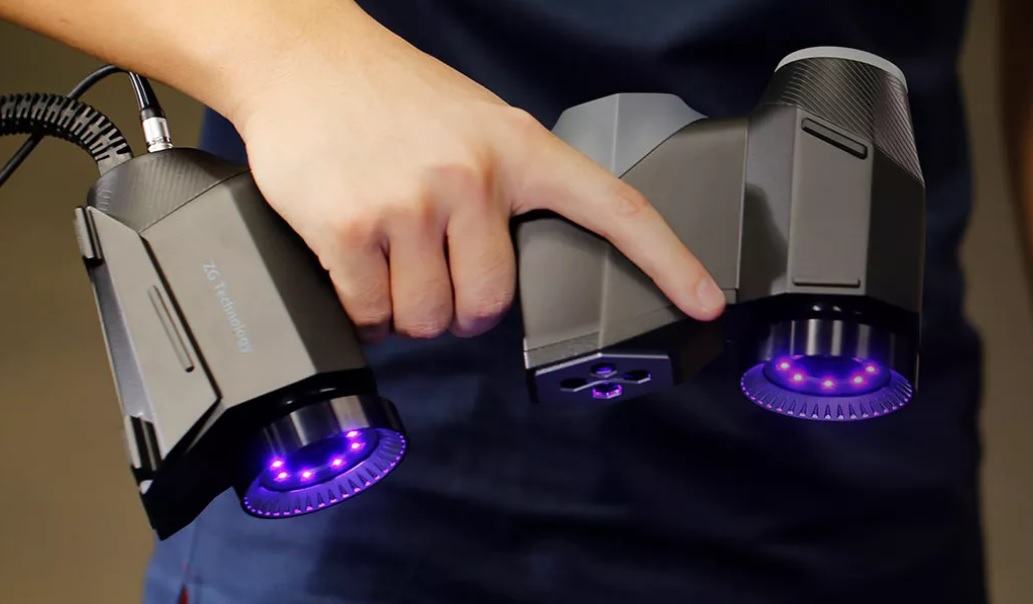
При использовании традиционных инструментов тактильных измерений форма для литья под давлением и полимерные изделия, как правило, измеряются с ограниченным числом контрольных точек, и большое пространство остается непроверенным. Кроме того, у пластиковых деталей более сложная геометрия (глубокие отверстия, карманы и скошенные края), трудно доступная классическим инструментам.
Наконец, из‑за свойств пластиков изделия очень легко деформируются даже при небольшом давлении на поверхность, что затрудняет их точное измерение. Таким образом, для ускорения контроля в литье пластмасс под давлением крайне необходима быстрая и эффективная бесконтактная измерительная система.
Хотите опробовать инновационные 3D‑решения в работе? Оставьте заявку на демонстрацию оборудования и/или тестовую услугу:
Закажите бесплатное тестовое 3D-сканирование
Решение
Ответом на вышеуказанные проблемы станет лазерный 3D‑сканер ZG, который являет собой идеальное бесконтактное решение для такого рода контроля. Технология триангуляции позволяет сканерам ZG получать наиболее точные и повторяемые данные измерений без контакта с пресс‑формой и деталями из пластика.
В режимах стандартного, однолинейного или высокоточного сканирования устройства ZG могут собирать данные по всему диапазону измерений за короткое время. Доступна точная и реалистичная оценка даже мельчайших нюансов, например, поправочных значений геометрии пресс‑формы или параметров станка и обработки. Данные сканирования нескольких деталей также можно использовать для контроля производства и анализа динамики показателей, чтобы свести к минимуму объем брака и переделок.
Эксперты iQB Technologies рекомендуют статью: Краткий тур по 3D‑измерениям вместе с ZG Technology
Контроль геометрии пресс‑форм
Пресс-‑формы, используемые в литье пластмасс под давлением, часто изготавливаются на основе модифицированных CAD‑моделей. Эти модификации включают в себя комбинацию коэффициентов равномерной и неравномерной усадки, добавление углов конусности, разъемов формы и так далее. Наилучший практический опыт учитывается и для уменьшения деформации и скручивания детали. Итак, пресс‑формы для литья полимеров под давлением нуждаются в строгом регулярном обслуживании для проведения необходимых восстановительных работ, для того чтобы обеспечить соответствие первоначальным размерам и точности.
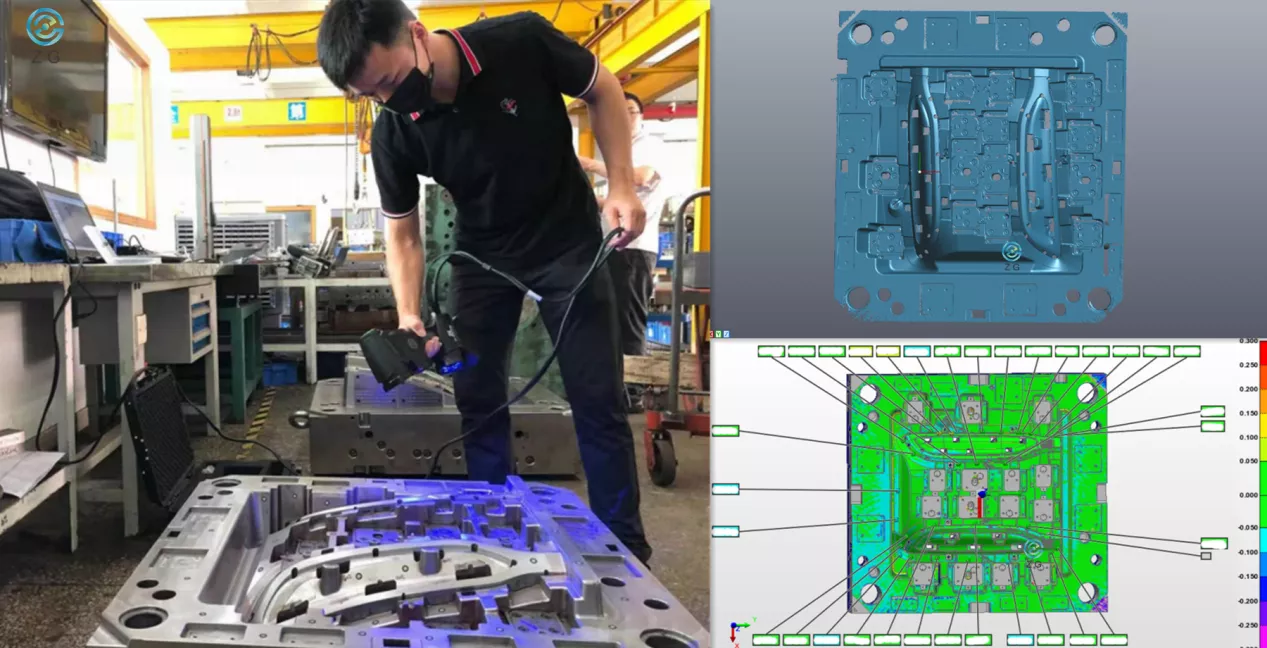
Используя универсальный 3D‑сканер метрологического класса AtlaScan, мы можем сканировать формы для литья под давлением быстро и с высокой точностью. Устройство имеет два режима сканирования, 26 синих лазерных линий для быстрой оцифровки, одну дополнительную синюю лазерную линию для сканирования глубоких отверстий и карманов и использует запатентованную технологию захвата отверстий.
Получив метрологический отчет в виде цветовой карты, инженеры могут четко определить, нуждается ли пресс‑форма в ремонте или нет. Это может не только сэкономить время, но и снизить затраты на проверку по сравнению с ручными измерениями.
В прошлом процесс измерений мог занимать десятки и даже сотни часов. С лазерными 3D‑сканерами время работы сокращается до нескольких часов или минут
Проверка первого изделия и контроль качества
Первая деталь, отлитая в форме, является критическим испытанием процесса механической обработки и самой формы. Проверка первого образца (FAI) – это процесс тщательного измерения изделия для оценки соответствия как по форме, так и по размерам, исходной CAD‑модели. В индустрии литья пластмасс под давлением любое отклонение литых пластиковых компонентов от исходной конструкции может повлиять на сборку, производительность и качество конечного продукта. Это делает первичный контроль изделия важным этапом инжекционного литья деталей из полимеров.
Предположим, у компании есть идеально выполненное и утвержденное первое изделие, на основе которого начинается массовое производство. Однако обнаруживается, что в процессе что‑то пошло не так, и вся партия не проходит контроль качества. Такое происходит даже на лучших заводах, а это значит, что одной проверки первого изделия недостаточно, также должен проводиться строгий контроль качества готовых деталей.
В прошлом этот процесс мог включать в себя множество измерительных инструментов и занимать десятки и даже сотни часов. С лазерными 3D-‑сканерами ZG время работы сокращается до нескольких часов или минут.
Используя интеллектуальный портативный лазерный 3D‑сканер RigelScan Elite, мы можем захватывать как белые, так и черные объекты без матирования и физического контакта с ними с целью проведения проверки первого образца. Более того, весь процесс оцифровки и контроля геометрии затрагивает только первое изделие. С остальными деталями операции совмещения данных сканирования с CAD‑моделью, контроля размеров и формирования отчета могут выполняться в массовом производстве автоматически.
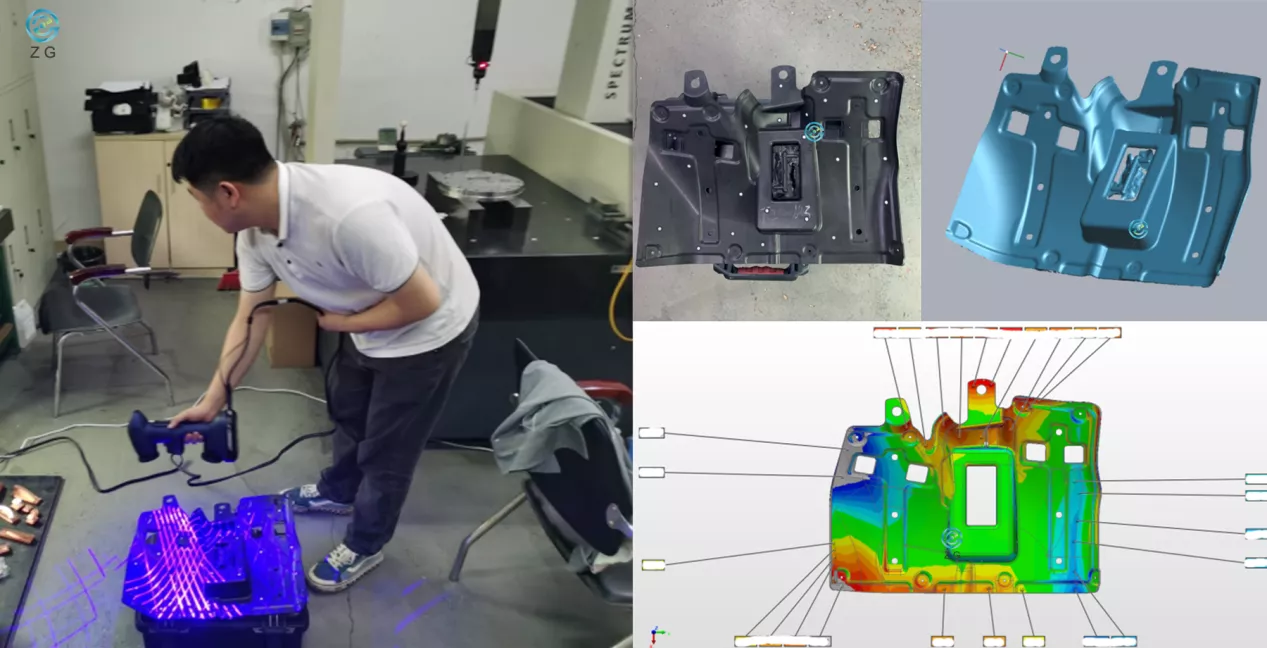
Поскольку данные 3D‑сканирования и отчет в виде цветовой карты можно без труда сохранять и загружать повторно, износ и изменения в производственном процессе легко проверять и контролировать. Таким образом, 3D‑данные первого изделия и готовой продукции позволяют специалистам ОТК не только эффективно следить за каждым процессом, но и контролировать различные производственные процессы для обеспечения качества пластиковой детали на протяжении всего ее жизненного цикла.
Итоги: кратко
Все больше компаний применяют лазерные 3D-сканеры ZG как для повышения точности измерений, так и для обеспечения всесторонней оценки всего производственного процесса путем анализа компонентов. Благодаря быстрому созданию отчетов о проверке и измерениях лазерные системы сканирования могут помочь производителям пластиковых деталей сэкономить сотни часов при изготовлении и тестировании пресс‑форм, утверждении первого изделия и контроле качества готовых изделий.
Это, в свою очередь, позволяет высвободить профессиональные ресурсы инженеров, повысить точность, сократить объемы ремонта пресс‑форм и сэкономить время выхода на рынок. В сфере литья под давлением ручные лазерные 3D‑сканеры по своим возможностям не сравнятся ни с какой другой измерительной системой.
Материал предоставлен компанией ZG Technology
Статья опубликована 29.09.2022 , обновлена 24.08.2023