Задачи производства | Классический принцип работы | Новый принцип работы с Surphaser 25HSX | Преимущества применения 3D-сканера
Предприятие 'Воронежстальмост' (бывший Воронежский мостовой завод) основано в 1948 году и является ведущей российской компанией по производству металлических пролетных конструкций мостов любых типов, размеров и сложности. Производственные площади завода и имеющееся оборудование позволяют изготавливать до 55 тысяч тонн металлоконструкций в год, на предприятии трудятся более 1800 рабочих и инженеров. Компания широко использует в работе компьютерные технологии, система менеджмента качества и сварочное производство сертифицированы в соответствии с международными стандартами.
Задачи производства
'Воронежстальмост' производит отдельные элементы мостов, пролеты строений, которые отправляются на площадку, где монтаж осуществляют строители. При изготовлении таких элементов необходимо до отправки заказчику убедиться, что все размеры точно выдержаны, нет никаких перекосов, а сборка проведена качественно, – чтобы проблемы не проявились при монтаже.
Классический принцип работы
До недавнего времени такая проверка проводилась на открытой площадке на территории завода. Рабочие делали контрольную сборку – они монтировали отдельные сложные, вызывающие сомнения места, после чего инженеры вымеряли все конструкции на предмет соответствия техническому заданию. В случае обнаружения нестыковок их причины локализовывались, и проблемные элементы конструкций отправлялись на доработку.
'Этот процесс был долгим и сложным, – говорит главный технолог предприятия 'Воронежстальмост' Идаят Кулиев. – Несмотря на то что мы собирали только отдельные части конструкций, даже они обладали внушительными габаритами и требовали для своего возведения значительных временных и трудовых затрат. Нам нужно было решение, которое позволило бы перевести контрольную сборку в виртуальный режим, дало возможность проверять нестыковки на компьютере без физического монтажа'.
Сначала компания приобрела тахеометр – электронный геодезический инструмент из класса теодолитов, предназначенный для измерения расстояний. 'Он позволял нам определять расстояния между точками, – рассказывает Идаят Кулиев. – Мы и сейчас снимаем некоторые размеры с его помощью, однако практика показала, что контрольная сборка после таких замеров не всегда бывает успешной, поскольку самих данных по расстояниям очень много, они разрознены, повышается риск ошибки при расчетах'.
Стало ясно, что требуется более совершенное решение, которое позволило бы снимать все необходимые данные по контрольным точкам единовременно и передавать в компьютерное ПО модель нужного элемента для виртуальной контрольной сборки.
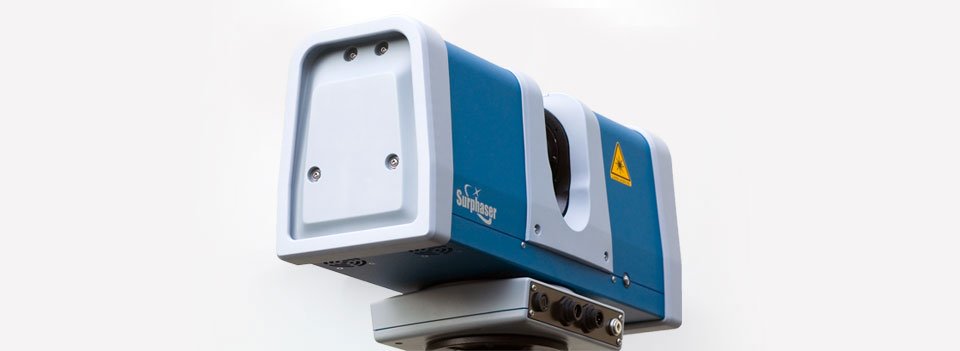
Новый принцип работы с Surphaser 25HSX
Таким решением стал трехмерный лазерный сканер Surphaser 25HSX. В этом приборе реализован фазовый метод определения расстояния, за счет которого достигается высокая скорость сканирования (до 1,2 млн точек в секунду). Сканеры Surphaser специально подготовлены для решения задач анализа и контроля геометрических параметров крупных объектов сложной формы, что полностью соответствовало требованиям предприятия 'Воронежстальмост'.
Включение трехмерного лазерного сканера в технологический процесс позволило полностью отказаться от натурной контрольной сборки. Сейчас элементы моста (такие, например, как пятнадцатиметровые блоки в 3,5 метра шириной и высотой) сканируются непосредственно в цеху. Полученные облака точек проверяются на соответствие модели в проектировочном программном обеспечении. В виртуальной модели сразу видны недочеты, несхождения контрольных точек, отклонения от чертежных данных. В случае их обнаружения элемент отправляется на доработку.
'Блоки конструкции сканируются с нескольких позиций, – говорит Евгений Куприн, руководитель бюро конструкций завода. – Полученная съемка сшивается с помощью программы Geomagic Studio, обрезается, чистится от 'мусорных' данных, масштабируется и конвертируется в координатную сетку XYZ'. Собранные и очищенные облака отдельных элементов конструкции в масштабе 1:1 накладываются в Autodesk Revit на 3D-модель моста, которую предоставляет заказчик. Это позволяет не только увидеть возможные недочеты и проверить сходимость, но и провести замеры для изготовления накладок.
'Мосты состоят из сотен элементов, – рассказывает Идаят Кулиев. – При натурной контрольной сборке мы не имели физической возможности собрать их все для проверки, поэтому выбирали сложные места, по которым у инженеров были опасения в плане геометрии. Сейчас мы имеем возможность проводить виртуальную контрольную сборку не только этих сложных элементов, но и всей конструкции'. В начале использования сканера специалисты компании провели несколько дополнительных контрольных сборок конструкций, уже проверенных на виртуальной модели, созданной с применением сканера. Никаких новых недочетов выявлено не было.
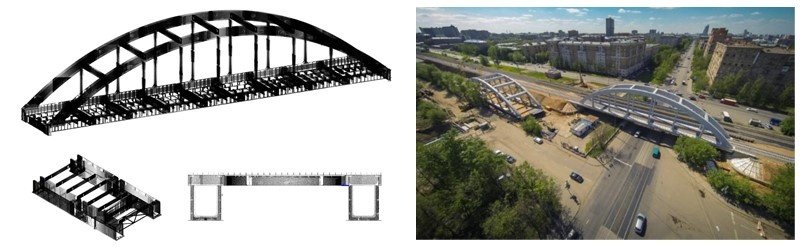
Преимущества применения 3D-сканера
'Натурная контрольная сборка – тяжелая и долгая работа, – отмечает Идаят Кулиев. – Три-четыре человека собирают часть моста на улице, в любую погоду, им нужны кран, чалочное приспособление, домкраты, нивелиры и несколько дней времени. Сканирование – тоже непростая задача, на очистку и подготовку одного элемента уходит от двух до четырех часов, но это работа одного инженера в кабинете за компьютером'.
Трехмерное сканирование снижает вероятность ошибок, связанных с человеческим фактором. 'Раньше, когда мы выполняли контрольную сборку, мы составляли протокол, куда вносили все отклонения и недостатки, – говорит Идаят Кулиев. – Затем сборка демонтировалась, в изделия вносились необходимые изменения, но иногда на монтаже вдруг обнаруживалось, что кто-то что-то недоглядел, какую-то ошибку упустили. А контрольная сборка уже разобрана, не на чем выявить расхождение, убедиться в том, что это наша ошибка. Сейчас у нас в компьютере всегда есть готовая модель, мы можем изучить проблему на ней, показать заказчику. Кроме того, повысился процент обнаружения проблемных мест – благодаря высокой точности прибора и возможности выполнить проверку всех узлов конструкции, а не только тех, на которые указали инженеры'.
'Мы недавно перешли на эту технологию, – подводит итог специалист, – и пока не до конца ее освоили, есть к чему стремиться. Однако уже сейчас можно с уверенностью сказать, что она нас полностью устраивает и возвращаться к методу контрольных сборок мы точно не собираемся'.
Статья опубликована 09.08.2017 , обновлена 22.04.2021