Как создаются композитные материалы | В чем преимущества применения композитов в 3D‑печати | 7 популярных композитов российского производства
Интенсивное развитие и внедрение аддитивных процессов во многие отрасли стало возможным не только благодаря модернизации и усовершенствованию технологий и машин, но и в силу активного расширения линейки расходных материалов для 3D‑печати. Термопласты, которые продолжительное время являлись основным сырьем и использовались для решения большинства задач, перестали удовлетворять многим параметрам конечных продуктов, что и стало предпосылкой к началу внедрения в аддитивное производство новых эффективных материалов.
Одна из таких разновидностей – композитные пластики, состоящие из нескольких компонентов и объединяющие в себе их полезные свойства. Рассмотрим процессы создания композитов, разберем их преимущества и сделаем краткий обзор некоторых популярных материалов российских производителей.
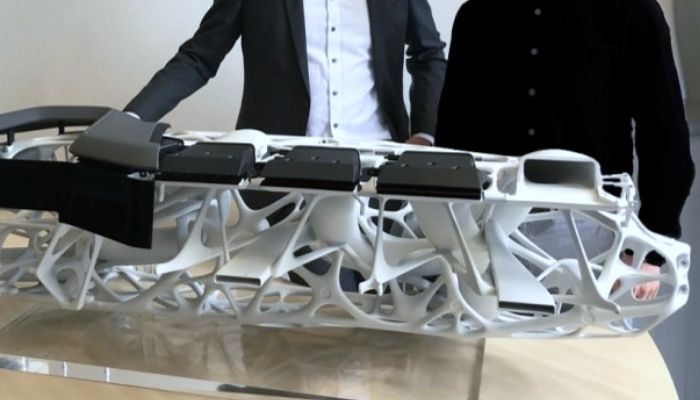
Совершенствование расходных материалов для 3D‑принтеров активно затронуло FDM‑технологию как самую распространенную, простую и дешевую, что открывает широкие возможности для интеграции самых разнообразных идей. Композитные материалы, которые используются в таком производстве, состоят из термопласта, называемого матрицей, и армирующего элемента (например, волокна). Про каждый – по порядку.
Поможет ли 3D‑печать оптимизировать производство в вашей организации? Закажите консультацию экспертов iQB Technologies и другие услуги – обучение 3D‑технологиям, тестовую печать/сканирование, выезд специалистов на предприятие:
Как создаются композитные материалы
С основным наполнителем или матрицей все довольно просто, секретов нет. Используются почти все популярные материалы для FDM-печати, в зависимости от требований, в том числе:
-
ABS (акрилонитрилбутадиенстирол);
-
PLA (полилактид);
-
PETG (полиэтилентефталат-гликоль);
-
PA (полиамиды);
-
PC (поликарбонат);
-
высокотемпературные инженерные пластики PEEK (полиэфирфэиркетон), PEI (полиэфиримид) и многие другие.
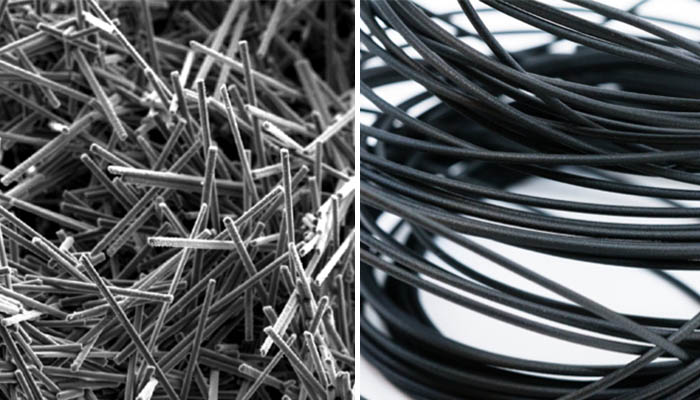
А вот с армирующими элементами вопрос обстоит гораздо интереснее и сложнее. Для этого в основном используются волокна – короткие или непрерывные. В первом варианте волокна имеют длину до 1 миллиметра и смешиваются в различных соотношениях с наполнителем, а с непрерывными процесс производства серьезно усложняется, потому что приходится интегрировать волокно прямо в процессе печати. Реализовать такую задачу довольно непросто, однако в этом случае напечатанные детали по прочности могут соперничать с металлическими. Из популярных армирующих элементов можно выделить следующие:
-
углеродное волокно;
-
стекловолокно;
-
кремнеземное волокно;
-
стеклянные и другие гранулы;
-
кевлар, графен и подобные.
Существуют также металлонаполненные полимерные композиции, в которых содержание металлов составляет 80‑90% и выше, что позволяет получить цельнометаллические изделия. Этапы процесса, который был разработан компанией BASF, включают 3D‑печать металлонаполненным филаментом в специальном принтере, каталитическое удаление связующего полимера и спекание.
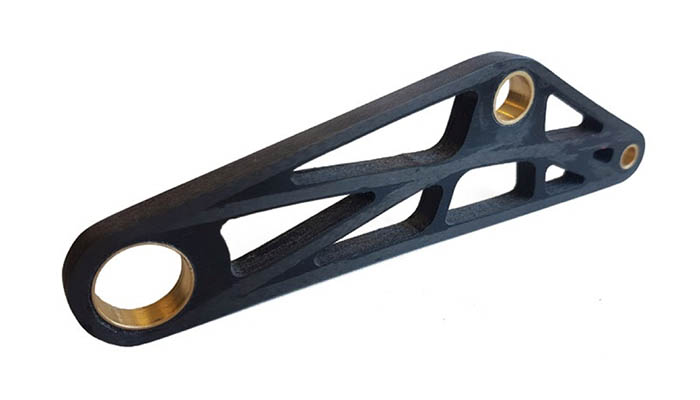
Об использовании полимеров в 3D‑печати читайте в блоге:
ABS‑пластик в аддитивном производстве: полезные советы
Всё о PLA – самом популярном пластике для FDM‑печати
Краткий гид по применению PETG в 3D‑печати
Высокоэффективные инженерные пластики – реальная альтернатива металлам?
Печатаем полиамидами: плюсы, минусы, особенности
13 советов и часто задаваемых вопросов о 3D-печати поликарбонатом
В чем преимущества применения композитов в 3D‑печати
Главный плюс композитных материалов в сравнении со стандартными полимерами – более широкий спектр температурных, механических и фрикционных характеристик. Изменяя соотношения объемов матрицы и армирующих элементов, можно значительно увеличить прочность, термо- и износостойкость, повысить сопротивление к реагентам и электричеству.
Примеры можно приводить бесконечно долго, ведь современные композиты – настоящее поле для экспериментов или даже некий конструктор, с помощью которого можно создавать расходные материалы с индивидуальными характеристиками, удовлетворяющие практически любым запросам.

Да, процесс производства такого сырья и сама 3D‑печать – сложные процедуры, а цена вопроса оставляет желать лучшего, не говоря уже про разработку конкретных видов. Но в конечном итоге результатами останется доволен каждый пользователь, и с этим сложно спорить. Уже сейчас детали, напечатанные из композитов по технологиям FDM и SLS, активно применяются в аэрокосмической, автомобилестроительной и медицинской промышленности, конкурируя с металлами.
«3D‑печать с использованием композитных материалов – новый важный тренд в аддитивном производстве, – считает генеральный директор стартапа «Анизопринт» Федор Антонов. – Она сопряжена со сложностями, но преимущества, которые вы можете получить, впечатляют. Детали могут быть в два‑три раза легче по сравнению с металлическими и при этом стоят дешевле, однако для успеха необходимы определенные знания и опыт. Снижение веса помогает значительно экономить ресурсы на каждом этапе жизненного цикла: более легкие конструкции – это меньше ресурсов для производства, меньшее потребление энергии при транспортировке, конечном использовании и переработке».
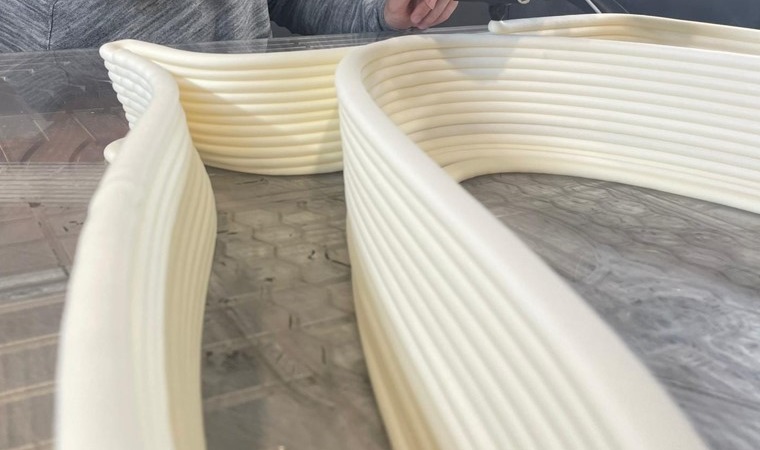
7 популярных композитов российского производства
Поскольку композиты в аддитивной отрасли – тема невероятно обширная и можно часами обсуждать модификации, чье количество стремится к бесконечности, остановимся на конкретных успешных разработках отечественных производителей.
1. Серия X‑line (REC и PICASO 3D)
Х‑line – линейка композиционных материалов, выпускаемая производителем пластиков для 3D‑печати REC в сотрудничестве с PICASO 3D и насчитывающая несколько удачных и востребованных в индустрии модификаций, таких как FormaX, UltraX и GF Max.

FormaX – инженерный пластик на основе ABS с добавлением углеволокна (порядка 15%), предназначенный для печати высоконагруженных и термостойких моделей. Из особенностей можно отметить простоту и стабильность печати, очень низкую усадку, повышенную прочность и жесткость, а также эффектный внешний вид. Идеально подойдет для нагруженных деталей любых размеров и функциональных прототипов.
UltraX – инженерный термопласт на основе PA‑6 (полиамид‑6) с добавлением короткого углеволокна. Отличается высокой прочностью, температурной и химической стойкостью, стабилен к ультрафиолету и выдерживает истирание. Сфера применения – 3D‑печать функциональных прототипов без последующей постобработки.
GF Max – инженерный пластик на основе PETG с добавлением короткого стекловолокна (порядка 10%). Прост в печати и отлично подходит для постобработки. Обладает повышенной прочностью и жесткостью, конечные изделия имеют красивый внешний вид. Подходит для большого ряда задач, в том числе для содания функциональных и нагруженных прототипов.
Эксперты iQB Technologies рекомендуют статью От протезов до оснастки: 3D‑печать термопластами и композитами на их основе
2. Clotho Filaments (REC и Imprinta)
Clotho Filaments – линейка композиционных материалов, отличающихся возможностью эксплуатации при высоких температурнах, простотой и прочностью. Разработана компаниями REC и Imprinta.
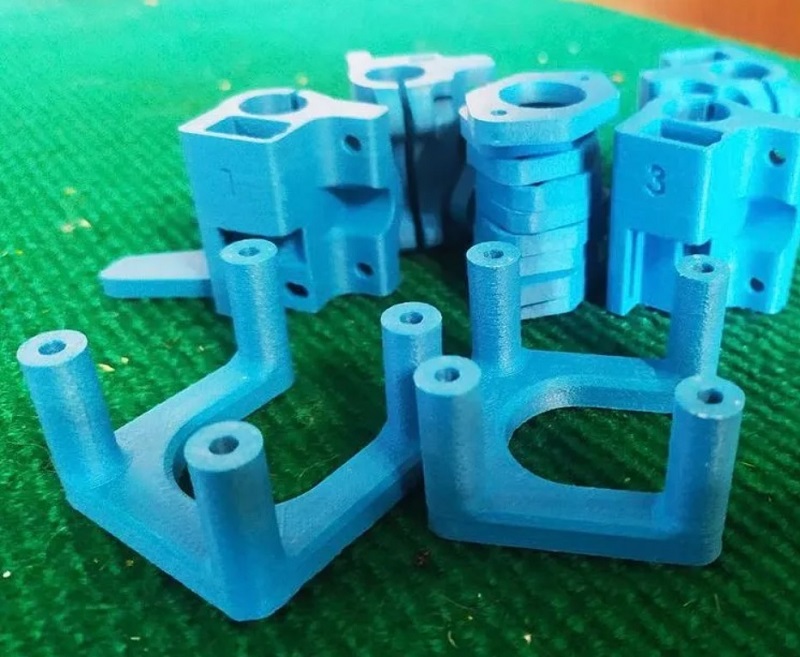
Clotho ABS GF13 – композит на основе ABS с добавлением короткого стекловолокна (порядка 13%). Материал с высокой термостойкостью – до 100 °C, высокой прочностью и жесткостью, минимальной усадкой и хорошей межслоевой адгезией. Хорошо подойдет для печати термостойких, высоконагруженных прототипов. Доступно несколько расцветок.
Clotho PA12 GF40 – композиционный материал на основе полиамида‑12 (PA‑12) с добавлением стекловолокна (порядка 40%). Обладает термостойкостью до 168 °C и исключительно высокой ударной прочностью – до 20,5 КДж/м2. Имеет более низкую усадку, хорошую адгезию и химическую стойкость к большинству реагентов. Подходит для печати изделий общего назначения, а также для термостойких, высоконагруженных механизмов, трущихся контактов.
3. Серия композитов на основе TPU (Filamentarno)
Total CF‑5 – ударопрочный композиционный материал на основе TPU (термопластичного полиуретана) с добавлением углеволокна (порядка 5%) для изготовления механически нагруженных деталей. Обладает высокой термостойкостью – до 130 °C, химической стойкостью и низкой усадкой. Применим в печати широкого спектра моделей.
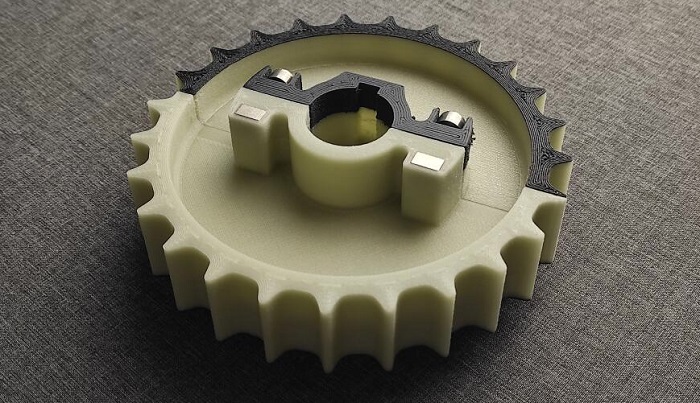
Total GF‑30 – ударопрочный пластик на основе TPU с добавлением стекловолокна (порядка 30%). Термостойкий (до 130 °C), химически стойкий, прочный композит для создания функциональных прототипов.
Мы рассмотрели лишь несколько достойных композиционных материалов, которые уже получили свое признание на российском рынке. Тема композитов не теряет актуальности, активно разрабатываются и внедряются все более совершенные модификации и технологии, о которых мы еще не раз услышим. Следите за новостями в нашем блоге и Телеграм‑канале!
Фото в заставке © 3dnatives.com
Статья опубликована 27.04.2023 , обновлена 13.09.2024