Измерения в условиях конвейерного производства | Принцип работы. Этап 1. Автоматическое совмещение | Этап 2. Измерения на производственной линии с помощью ручной портативной КИМ | Каким был процесс измерений в прошлом? | Вперед, к автоматизации измерений!
Одним из самых значимых достижений в метрологии за последние десятилетия стало развитие портативных измерительных устройств. Они позволяют выполнять контроль непосредственно на производственной линии, в максимальной близости к детали. Портативные измерительные манипуляторы и лазерные трекеры полностью перевернули представление о традиционных методах контроля качества.
Несмотря на это, портативные измерения все связаны с многочисленными трудностями, особенно в реальных условиях производства. Цифровые КИМ постоянно подвергаются воздействию вибрации, поступающей от оборудования (станки, прессы, транспортировочное оборудование, подъемные краны), должны соответствовать жестким требованиям по установке, перепадам температур и влажности, а также предполагают разные уровни компетенции и навыков пользователей. Поэтому неудивительно, что возникает необходимость в современных, но простых в использовании инструментах измерения прямо на производственной площадке.
Измерения в условиях конвейерного производства
Для начала рассмотрим один из самых сложных процессов на производстве — измерение объектов на конвейере. Трудность заключается в том, что на измерение деталей отведено очень короткое время (обычно менее минуты), а точность измерений с погрешностью менее одной десятой миллиметра обычно достигается, если детали неподвижны. Если не брать в расчет автоматизированные системы, измерения выполняются оператором производственной линии, который, как правило, не обладает нужной квалификацией. Это может существенно повлиять на качество измерений. Согласно выводам исследовательского отчета CMSC «Как поведение влияет на измерение», человеческая ошибка – основная причина некачественных измерений.
Эксперты iQB Technologies рекомендуют статью: 3 проблемы, о которых вы забудете благодаря автоматизации контроля качества
Портативные оптические КИМ от Creaform – это новая веха в области портативных 3D-измерений. Они используют технологию TRUaccuracy, которая существенно облегчает измерения в условиях конвейерного производства. Технология TRUaccuracy включает в себя функции самопозиционирования и динамической привязки, что позволяет измерительному устройству создавать непрерывную оптическую связь с деталью. Такой механизм полностью ограждает процесс измерений от воздействия вибраций, которые неизбежны на производстве, а впоследствии передаются на измерительную систему и измеряемый объект и могут увеличиваться при использовании неустойчивых штативов или поверхностей. Более того, технология TRUaccuracy позволяет операторам измерять движущиеся детали – например, на непрерывно движущейся производственной линии – благодаря устойчивости измеряемого объекта к любым перемещениям.
Принцип работы
Этап 1. Автоматическое совмещение
Первый этап любого трехмерного измерения – это совмещение, благодаря которому все данные измерений привязываются к единой базе, а оператор получает возможность сравнивать значения измерений и расчетные значения из CAD-файлов. Если на все измерение отводится всего лишь одна минута, ручное совмещение занимает слишком много времени и влечет за собой высокий риск ошибок.
В таких условиях правильнее всего будет использовать автоматическое совмещение, доступное только в оптических КИМ. На сборочное приспособление, которое заранее измеряется портативной оптической КИМ и связывается с плоскостью сравнения детали посредством измерения лишь нескольких точек, помещается несколько отражающих меток. Благодаря этому мы получаем возможность автоматического совмещения портативной КИМ и детали каждый раз при распознавании схемы расположения меток.
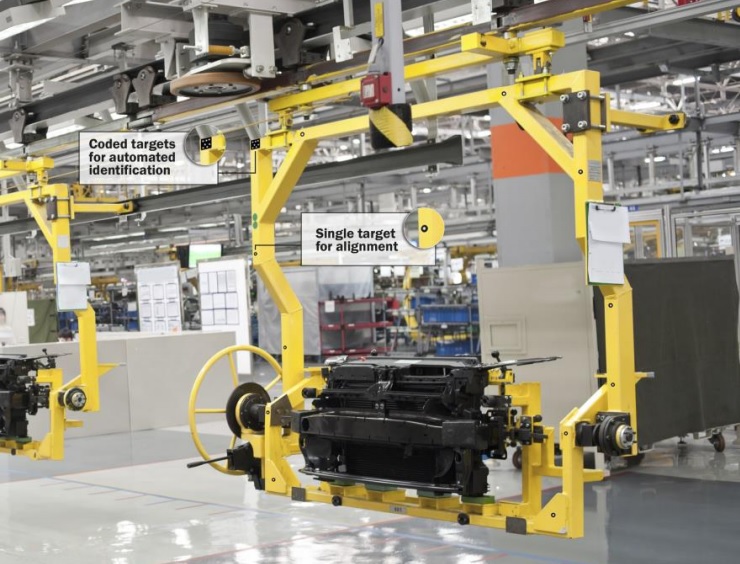
Поскольку по конвейеру движется множество разных сборочных приспособлений – каждое с собственной схемой расположения меток и данными совмещения, – на каждое приспособление для его автоматической идентификации помещается кодированная метка. Устройство также способно автоматически распознавать деталь (это могут быть детали от разных моделей на одной линии) и подгружать нужные теоретические значения. Таким образом, процесс совмещения происходит автоматически. Впоследствии можно сравнить значения измерений и обновленной детали. Также для автоматического совмещения можно использовать специальный инструмент с метками, который легко закрепляется на детали и снимается после измерения. Метки при этом необходимо зарегистрировать в системе координат, общей для детали и инструмента. Инструмент, показанный на фотографиях, состоит из пластины, V-образного элемента и T-образного элемента, оснащенных метками. Пластина совмещается с передней стороной дискового тормоза. V-образный элемент прилегает к большому цилиндру рядом с дисковым тормозом.
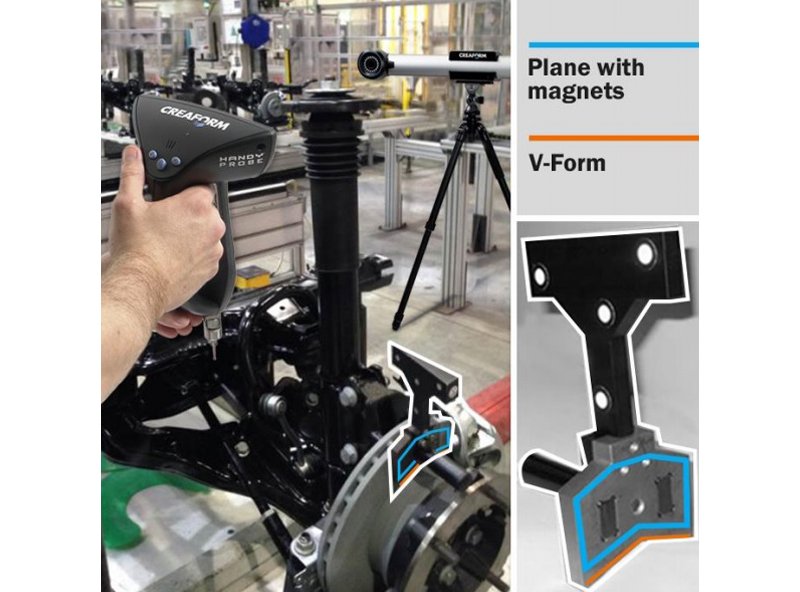
Автоматическое совмещение существенно сокращает время измерения и устраняет самые распространенные источники ошибок. Например, Creaform установила автоматизированную систему контроля качества на линии производства створок реверса самолетов компании Aircelle (Safran Group). Время, затрачиваемое на контроль качества, сократилось втрое, а количество ошибок – более чем в пять раз в сравнении с результатами механических портативных КИМ.
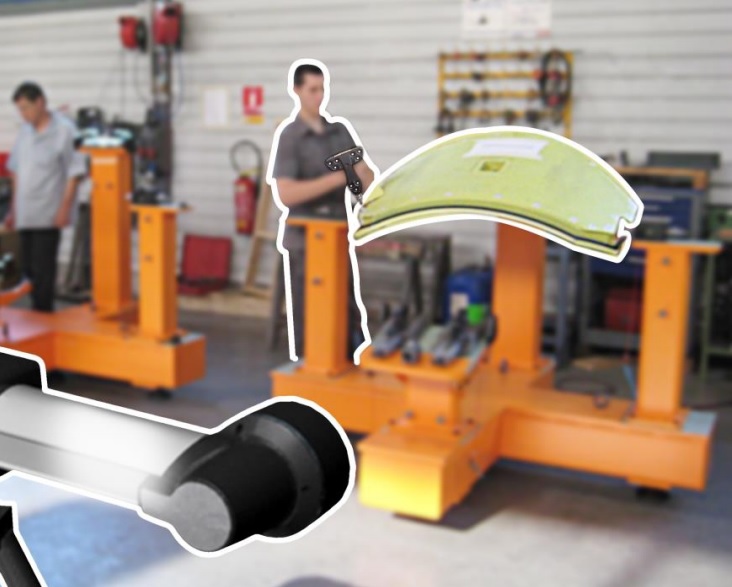
Этап 2. Измерения на производственной линии с помощью ручной портативной КИМ
После совмещения оператор может приступить к точечному измерению детали. Из-за короткого срока, отведенного на измерения, особенно в условиях конвейера, процесс измерений обычно ограничивается несколькими точками (как правило, десятью). Система Creaform используется на конвейере одного известного немецкого автопроизводителя для проверки длины сборочных узлов и оптимизации центровки деталей в уже собранных агрегатах. Для этого на каждом конце детали прибор отслеживает четыре точки. Одна дополнительная точка выступает в качестве нулевой величины. На другом конвейере этого же производителя система используется при контроле положения креплений для заблаговременного обнаружения бракованных деталей, которые впоследствии могут вызвать остановку конвейера на этапе сборки.
В предыдущем примере c тормозной системой для проверки угла между стойкой амортизатора и дисковым тормозом после сборки используется всего лишь четыре точки. Как уже было сказано, это поможет избежать будущих проблем на финальных этапах контроля качества и необходимости ремонтировать полностью собранный автомобиль. Ремонт детали до сборки позволяет значительно сэкономить.
Эксперты iQB Technologies рекомендуют статью: 3D-сканеры в автомобилестроении: 4 преимущества и 4 успешных проекта
Чтобы максимально облегчить измерения, для операторов производственных линий могут быть разработаны особые программы (с использованием стандартного метрологического ПО), обеспечивающие сопровождение всего процесса. Посмотрев на экран, любой оператор сможет понять, какие точки необходимо измерить. Для улучшения надежности измерений отслеживаются только необходимые точки. Если оператор попробует измерить точки за пределами заранее определенной зоны, устройство не примет их. Результаты измерений сохраняются автоматически в форме отчета, определяемой заказчиком.
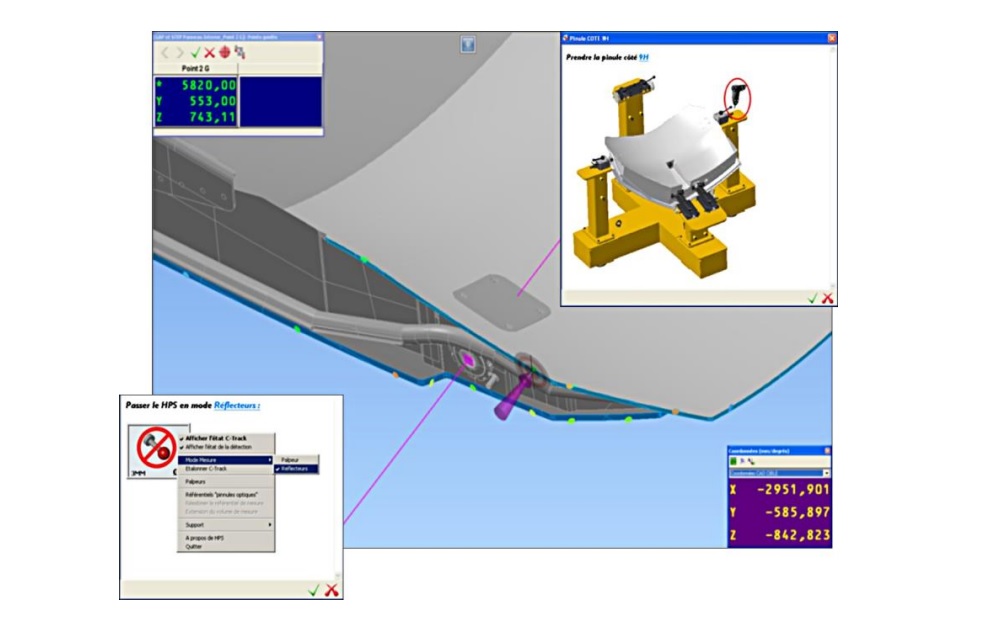
Во всех вышеприведенных примерах используются контактные измерения, однако того же результата можно достигнуть, используя 3D-сканер и портативную КИМ.
Каким был процесс измерений в прошлом?
До изобретения новых технологий и методов для измерений на производственной линии использовались два основных метода.
Первый (и самый распространенный) способ заключался в контроле деталей-образцов, взятых с производственной линии, на традиционной КИМ. Основные ограничения такого метода:
- контроль проходили не все детали; отследить можно было только общие отклонения производственного процесса. Более того, бракованная деталь могла остаться незамеченной и отправиться на сборку;
- КИМ становилась ограничивающим фактором, поскольку время контроля превышало время производственного цикла;
- при удалении детали с производственной линии нарушалась последовательность сборки. Если деталь не возвращали на свое место (например, автомобиль №123567 мог получить аудиосистему от автомобиля №123568), возникали проблемы, связанные с контролем качества.
Второй метод базировался на использовании специальных контрольных приспособлений, оснащенных ручными или электронными датчиками. Такие приспособления можно было использовать для контроля как всех, так и отдельных деталей. Основные ограничения:
- стоимость такой технологии во всем мире была непомерно высокой, поскольку для каждой новой модели детали нужно было заново разрабатывать (или адаптировать) приспособление.
Вперед, к автоматизации измерений!
Портативная КИМ Creaform способна точно и практически мгновенно определять положение сотен меток. Эта функция крайне полезна для контроля сборки узлов. Например, решение Creaform используется на объекте известного производителя ракет для динамического позиционирования системы зажигания в верхней части порохового ускорителя с точностью до 20 микрон. Такая точность обеспечивается системой, которая действует на финальном этапе сборки, на высоте 50 метров, на металлическом решетчатом полу, установленном на металлоконструкции.
Возможности сканера позволяют установить его на роботизированную руку и использовать портативную КИМ для одновременного отслеживания сканера и измеряемых деталей, вне зависимости от того, движутся они или нет. Таким образом процесс контроля качества становится полностью автоматизированным.
Автор: Жан-Франсуа Ларю, маркет-менеджер Creaform по контролю качества
Материал предоставлен компанией Creaform
Статья опубликована 03.10.2019 , обновлена 03.03.2022