Авиация и космонавтика | Автомобилестроение | Медицина | Потребительские товары | Строительство | Культурное наследие | Наука и технологии
NASA и Rocket Lab готовят к запуску ракету Neutron с 3D‑печатными компонентами
NASA подписало соглашение с компанией Rocket Lab USA, Inc. о включении ракеты Neutron в программу VADR, направленную на поддержку частной аэрокосмической индустрии. Neutron – это ракета-носитель средней дальности с девятью многоразовыми двигателями Archimedes, разработанными для повышения эффективности и гибкости космических запусков.
Благодаря универсальности и эффективности «Нейтрона» Rocket Lab теперь может расширить сферу своих исследований до космических миссий и выйти на ранее неизведанные орбиты.
У двигателя Archimedes много интересных особенностей. В нем используется множество 3D‑печатных компонентов – от конструкций двигателя, корпусов турбонасосов и клапанов до компонентов пусковой и главной камер. Двигатель работает на жидком кислороде и метане и использует замкнутый цикл с дожиганием, богатый окислением. Это инновационное решение для космических аппаратов такого типа.
Кроме того, двигатель разработан как многоразовый, что позволяет осуществить не менее 20 запусков. Его эксплуатационная мощность также позволяет снизить нагрузку по сравнению с представленными на рынке аналогами. При максимальной мощности каждый двигатель Archimedes способен создать 165 000 фунт‑силы (733 кН), в результате чего суммарная тяга первой ступени Neutron составит 1 450 000 фунт‑силы.
Первый запуск Neutron запланирован на середину 2025 года со стартового комплекса Rocket Lab на острове Уоллопс (Вирджиния). Этот амбициозный проект – еще одна веха в истории 3D‑печати. Он в очередной раз показывает, что аддитивные технологии способны преодолевать экстремальные вызовы такой сложной и требовательной индустрии, как аэрокосмическая.
Источник: 3dnatives.com
Ростех представил новейший двигатель для Superjet
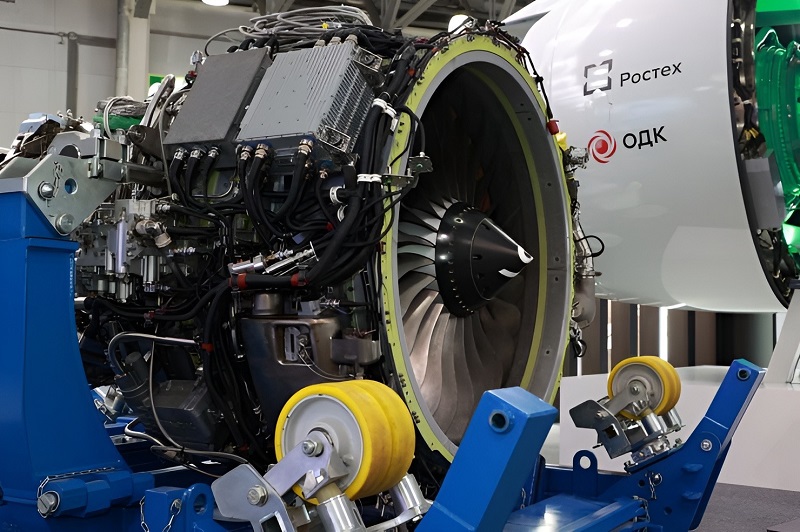
Объединенная двигателестроительная корпорация Ростеха показала линейку отечественных двигателей на выставке инфраструктуры гражданской авиации NAIS в Москве. Компания презентует силовые установки для среднемагистральных и региональных самолетов, а также перспективных вертолетов. Главная новинка – двухконтурный турбовентиляторный двигатель ПД‑8 для ближнемагистрального лайнера SJ‑100. Он создан на предприятии «ОДК‑Сатурн» с применением новейших отечественных материалов и передовых технологий, в том числе 3D‑печати.
«Работы по всем этим проектам выходят на финишную прямую: идут необходимые испытания двигателей, одновременно мы разворачиваем мощности для серийного производства. В ближайшее время ждем, что ПД‑8 впервые поднимется в воздух в составе пассажирского SJ‑100 для прохождения заключительного этапа – летных испытаний», – рассказал первый заместитель генерального директора Госкорпорации Ростех Владимир Артяков.
Источник: rostec.ru
Больше новостей, историй успеха и экспертных материалов – в нашем Telegram-канале. Подпиcывайтесь!
BMW запускает линию 3D‑печати песком для производства оснастки
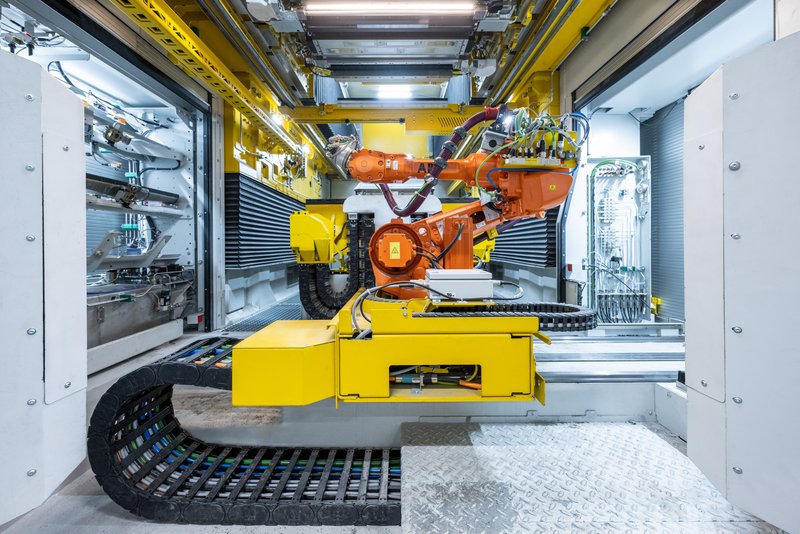
Компания Laempe Mössner Sinto поставила шесть 3D‑принтеров на литейный завод BMW в Ландсхуте, Германия. Полностью автоматизированная высокопроизводительная линия 3D‑печати по технологии Binder Jetting оптимизирована для производства песчаных стержней для пресс-форм и отвечает требованиям крупносерийного производства.
3D‑принтеры уже используются в изготовлении форм для компонентов новейших шестицилиндровых автомобилей BMW. Решение для аддитивного производства устраняет необходимость в ручных операциях, предлагая полностью автоматизированные 3D‑измерения и удаление стержней из отливок.
Технология Binder Jetting заключается в послойном склеивании композитного порошка связующим веществом (в данном случае песком) и затрагивает всю цепочку создания стоимости. BJ‑системы объединяют ключевые процессы, включая хранение сырья, подготовку формовочных материалов, 3D‑печать, упаковку, очистку и измерение компонентов. Это комплексное решение отвечает разнообразным потребностям современных литейных цехов.
Laempe заявляет, что благодаря ее инновационной аддитивной технологии в будущем будет экономически выгодно решать широкий круг задач с помощью аддитивного производства вместо классических операций изготовления стержней. BJ‑печать – реальное конкурентное преимущество и перспективное решение, которое откроет для производителей новые возможности роста.
Источник: 3dprintingindustry.com
Прочнее и дешевле: в питерском Политехе предложили новый подход к производству колесных дисков
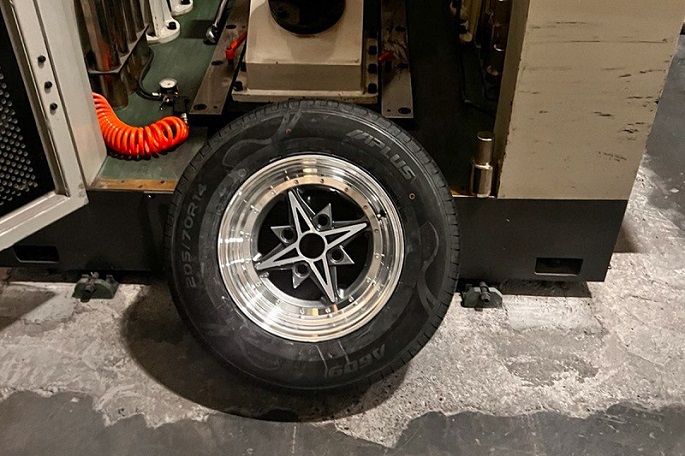
Инновационная разработка принадлежит ученым Санкт-Петербургского политехнического университета Петра Великого. Благодаря технологии электродугового выращивания был напечатан обод колеса с помощью проволоки из алюминиевого сплава 5556. Это серьезный вклад в безопасность дорожного движения, отмечают специалисты.
«Серия экспериментов показала, что при высокой нагрузке от идентичных ударов выращенный нами обод в колесе прогнулся на 4 мм меньше, чем литой при тех же условиях. При этом колесо с выращенным ободом не полностью потеряло давление, а сохранило остаточное, что более безопасно для дорожного движения. При аналогичной нагрузке колесо с литым диском не сохранило воздуха», – отметил заведующий Лабораторией легких материалов и конструкций СПбПУ Олег Панченко.
Подобных разработок – 3D‑печати ободов для автомобильных дисков – в мире нет, подчеркивают ученые. По их словам, разработанная аддитивная технология имеет себестоимость готового обода на уровне изделий, созданных традиционным путем, однако обеспечивает более высокий уровень безопасности.
Источник: spbstu.ru
3D‑биопринтинг поможет улучшить лечение обширных ожогов
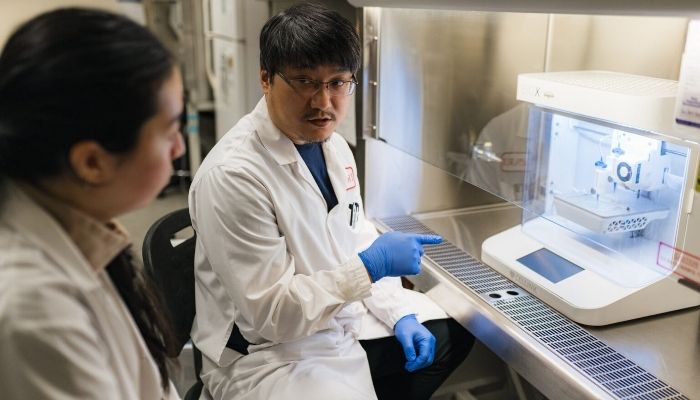
По данным ВОЗ, ожоги являются причиной смерти около 180 тысяч человек в год. Тяжелые ожоги, особенно те, которые затрагивают значительную часть тела, по‑прежнему представляют собой серьезную проблему для современной медицины. Современные методы лечения заключаются в пересадке кожи с использованием собственных здоровых тканей пациента для закрытия ран. Однако когда площадь ожога очень велика, найти достаточное количество здоровой кожи практически невозможно. В этом контексте инновационная технология, основанная на 3D‑биопринтинге и культуре стволовых клеток, может стать решением для лечения обширных ожогов.
В начале 2025 года Центр исследований ожогов при сети больниц Hamilton Health Sciences (HHS) в Канаде начал клинические испытания, в ходе которых будет оценена безопасность и эффективность использования стволовых клеток, извлеченных из обожженной кожи пациентов. Этот метод обещает регенерировать ткани, не полагаясь исключительно на здоровую кожу, что, как надеются специалисты, полностью изменит картину в лечении обширных ожогов. Стволовые клетки из обожженной ткани будут использоваться для создания биологических чернил, из которых будет формироваться новая кожа.
«С началом клинических испытаний первой фазы наша лаборатория станет первой в мире, где для лечения будут использоваться стволовые клетки, взятые из обожженной кожи пациентов», – говорит д‑р Марк Йешке, вице‑президент по исследованиям и главный научный сотрудник HHS. В испытаниях примут участие 20 пациентов с ожогами менее 20% тела. Цель – проверить, как стволовые клетки, полученные из их собственных обожженных тканей, могут ускорить заживление и уменьшить образование рубцов. Если результаты будут положительными, то в будущем эту методику можно будет распространить на пациентов с более обширными ожогами.
Источник: 3dnatives.com
Новое слово в протезировании: бионическая рука с сенсорной обратной связью
Ампутация конечностей в результате травм затрагивает более 50 миллионов человек во всем мире. Многие из пострадавших предпочитают пользоваться протезами, но их интеграция в повседневную жизнь может оказаться непростой задачей, и главная проблема – это автономность. Кроме того, протезы отличаются высокой стоимостью и хрупкостью, что ограничивает их доступность для пациентов.
Американская компания PSYONIC, основанная доктором Аадилом Ахтаром, изготавливает самые современные бионические конечности с помощью робототехники и экономичного аддитивного производства по технологиям FDM, SLA и SLS. Флагманский продукт PSYONIC – Ability Hand, бионическая рука с сенсорной обратной связью, обещающая кардинально изменить практику протезирования.
«Беседуя с пациентами и медицинскими работниками, мы выявили основную проблему, с которой они сталкивались: высококачественные протезы, изготовленные на заказ методом литья под давлением и механической обработки, часто ломались из‑за жесткой конструкции, – говорит доктор Ахтар. – Для решения этой проблемы мы выбрали более гибкий подход на основе робототехники, используя такие материалы, как силикон и резина, в дополнение к 3D‑печатным внутренним компонентам, чтобы придать им большую устойчивость к ударам».
Процесс производства включает в себя несколько этапов. Во‑первых, это сборка привода, включая двигатели, энкодеры и редукторы. Затем изготавливаются пальцы, что включает в себя создание внутренней кости и силиконовых форм, интеграцию датчиков давления и металлическое крепление к трансмиссии. Ладони производятся с применением углеродного волокна для обеспечения прочности. Электроника – ключевой компонент, в ладони расположена печатная плата, отвечающая за управление двигателем и связь с другими устройствами по Bluetooth. Наконец, за счет водонепроницаемой ткани и уплотнителей обеспечивается полная водонепроницаемость.
После того как бионическая рука полностью собрана, она отправляется к врачу-специалисту, который устанавливает ее на пациента. Затем пациент подбирает специальное гнездо для крепления бионической руки к своей культе. Интуитивное управление бионической рукой осуществляется с помощью мышечных датчиков.
Источник: 3dnatives.com
Gucci применяет SLS‑технологию в кроссовках из новой коллекции
Итальянский люксовый бренд, успешно сочетающий традиции мастерства с современными технологиями, представил серию кроссовок Cub3d для весенне-летней коллекции 2025 года. Для изготовления подошв с замысловатой решетчатой структурой была выбрана технология селективного лазерного спекания (SLS). Подошва состоит из нескольких слоев, элегантно переплетенных между собой и создающих изящную геометрическую форму.
В конструкции верха кроссовок Cub3d сетка сочетается с Demetra. Это разработанный Gucci материал, состоящий минимум на 70% из сырья растительного происхождения, включая вискозу, древесную массу и полиуретан на биооснове. Подошва сделана из биоматериала с внутренним наполнителем EVA для амортизации и внешней частью из TPU с фирменным логотипом, создающим 3D‑эффект.
Образец кроссовок Cub3d был разработан с помощью популярных инструментов параметрического дизайна Rhino и Grasshopper, позволяющих точно настраивать геометрические узоры и детали конструкции. Можно предположить, что дизайнеры Gucci использовали вычислительное моделирование для доработки структуры межподошвы перед производством. Такой подход позволил быстро итерировать сложные геометрические формы и интегрировать цифровую эстетику в физический продукт.
Источник: 3dprintingindustry.com
Первый в Европе проект социального жилья, выполненный с использованием 3D-принтера, завершен раньше срока
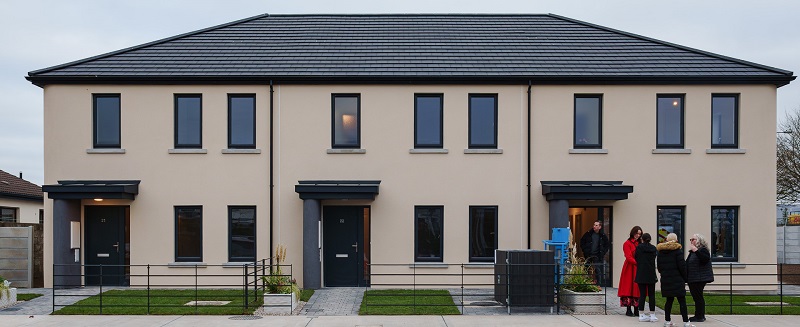
Компания Harcourt Technologies Ltd (HTL.tech), лидер в области строительной 3D‑печати в Ирландии и Великобритании, успешно завершила первый в Европе проект социального жилья с использованием аддитивной технологии, соответствующей стандарту ISO/ASTM 52939:2023. Здание, расположенное в Грейндж Клоуз (Ирландия), построено с помощью строительного 3D‑принтера BOD2 компании COBOD International всего за 132 дня. Это на 35% быстрее, чем при традиционных методах строительства, которые обычно требуют более 200 дней.
Несущие двойные пустотелые стены толщиной 10 сантиметров каждая были напечатаны без армирования в соответствии со стандартами EN206 и Eurocode 6 для неармированной каменной кладки. Этот метод не только обеспечил целостность конструкции, но и продемонстрировал значительные достижения в области экологичного строительства. Работы наземного цикла были выполнены за впечатляющие 12 дней, что подчеркивает эффективность аддитивного производства в ускорении сроков строительства.
Источник: 3dprintingindustry.com
В России запустили первый портал с трехмерными моделями памятников мировой культуры
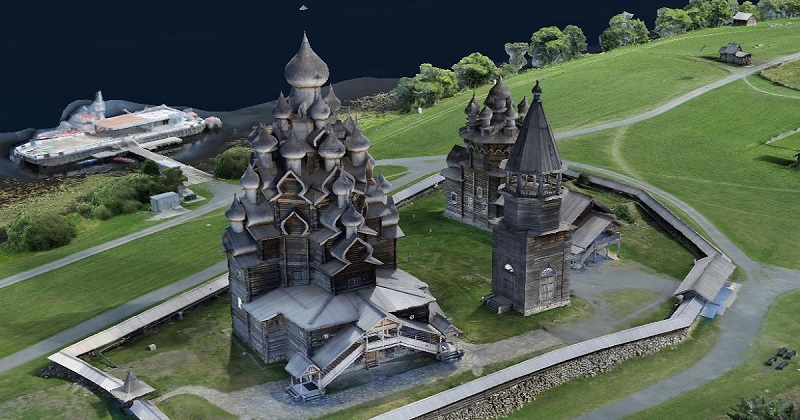
ГК «Геоскан» запустила портал «3D‑наследие: сохраняя культуру» с объемными реалистичными цифровыми моделями мировых объектов культурного наследия. Он нацелен на документирование важных исторических объектов, поддержку реставрационных работ, развитие научно-образовательной деятельности и виртуального туризма. Это первый подобный проект для профессионалов в России.
На портале heritage3d.ru размещены цифровые копии исторических памятников со всего мира: Кижского погоста в Карелии, Храма Гарни в Ереване, Цитадели Дамаска в Сирии и др. Цифровые модели с высокой степенью детализации будут помогать в работе исследователям и реставраторам, а также позволят всем желающим изучать историко-культурные ценности разных стран из любой точки земного шара.
Для регулярного пополнения библиотеки Геоскан планирует привлечь вузы и научные учреждения из России и других стран, компании и частных лиц, которые занимаются аэрофотосъемкой, лазерным сканированием, фотограмметрией и реставрационными работами.
Источник: geoscan.ru
Разработан метод 3D‑печати гибких, перерабатываемых и доступных мягких пластиков
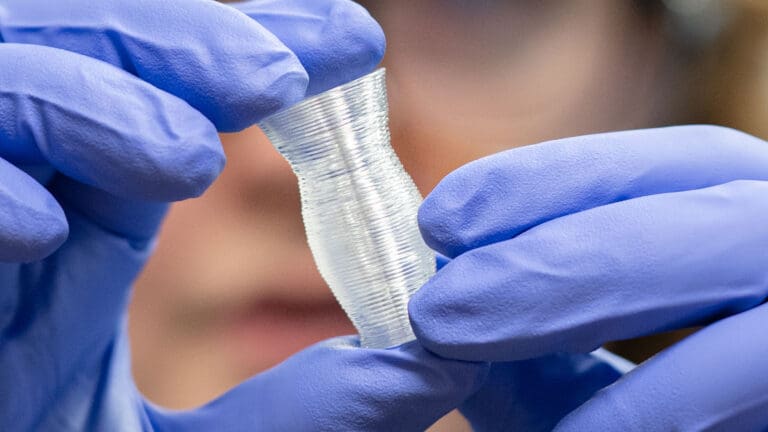
Инженеры Принстонского университета разработали новую технологию 3D‑печати для производства мягких, растягивающихся пластиков с настраиваемыми свойствами. Метод, подробно описанный в журнале Advanced Functional Materials, использует недорогие термопластичные эластомеры, стоимость которых составляет примерно один цент за грамм. Полученные материалы могут быть как гибкими, так и жесткими, при этом их можно переработать для повторного использования.
Метод основан на управлении наноразмерными структурами внутри материала в процессе печати. Исследователи использовали блок-сополимеры, которые формируют жесткие цилиндрические структуры толщиной 5‑7 нанометров, встроенные в гибкую полимерную матрицу. Эти структуры можно ориентировать в процессе печати, создавая материалы с различной степенью жесткости и гибкости в разных направлениях.
Ключевая особенность процесса – термический отжиг, который включает в себя контролируемое нагревание и охлаждение напечатанного материала. Исследовательская группа продемонстрировала универсальность своей методики, создав различные объекты, например небольшую вазу и напечатанный текст. Команда проверила способность материала к самовосстановлению, разрезав и соединив образцы путем отжига, при этом восстановленные материалы продемонстрировали свойства, аналогичные оригинальным.
Технология перспективна для решения различных задач, включая производство мягких роботов, медицинских устройств, протезов, средств защиты и кастомизированных обувных подошв. В дальнейшей работе команда исследователей планирует изучить новые структуры, подходящие для носимой электроники и биомедицинских устройств.
Источник: 3dprinting.com
3D‑печать из метаматериалов повышает эффективность звукоизоляционных панелей
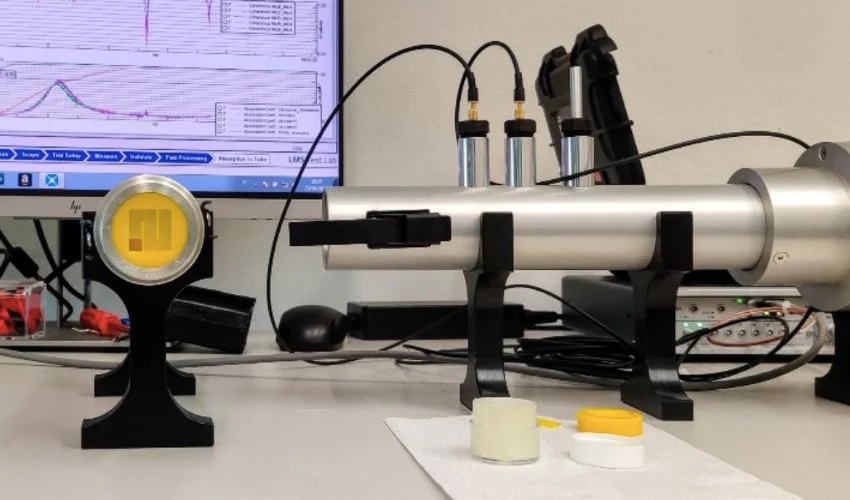
Звукоизоляция исключительно важна не только при строительстве домов или больниц, но и при создании автомобилей и в промышленной среде. Недавнее исследование показало, что 3D‑печать звукоизоляционных панелей позволяет сделать их более легкими и узкими без ущерба для эффективности. Помимо 3D‑печати, также рассматривался вопрос об использовании метаматериалов для лучшего рассеивания звука в панелях, в результате чего исследователи предложили особую конструкцию для лучшей звукоизоляции.
Особенность исследования заключается в том, что оно касается дизайна больших панелей в форме лабиринта с акустическими метаматериалами. Метаматериалы имеют совершенно иную структуру, чем «обычные» материалы. В данном случае была разработана лабиринтоподобная структура, которая рассеивает звук при прохождении через материал. Так удается добиться высокого поглощения в широком диапазоне частот, превосходя возможности панелей стандартной конструкции.
Аддитивное производство позволяет с миллиметровой точностью создавать внутренние структуры, необходимые для панелей. В исследовании предложены полимеры, оптимизированные для улучшения звукопоглощения, которые будут сочетаться с пористыми материалами для повышения их эффективности. Таким образом, 3D‑печать облегчает адаптацию конструкции к требованиям конкретного окружения.
Исследование подтверждает, что 3D‑печатные панели с метаматериалами представляют собой эффективное и универсальное решение для шумоподавления в широком спектре частот. Благодаря модульной и легкой конструкции, а также высокой поглощающей способности эти панели становятся привлекательной альтернативой традиционным системам.
Источник: 3dnatives.com
Фото в заставке © Princeton University
Статья опубликована 27.02.2025 , обновлена 25.02.2025