Термопласты и композиты – что это такое? | Как получаются композиты? | Кто основные потребители полимеров для 3D-печати? | Какие пластики самые популярные? | Как применяется 3D-печать термопластами и композитами? Примеры готовых изделий
Нам часто задают вопрос: делают ли в России качественные, надежные и безопасные материалы для 3D-печати? Безусловно, такие производители есть, более того, в этой сфере накоплен весомый опыт и ноу-хау. Одним из пионеров на отечественном рынке производства пластиков для аддитивной отрасли была компания REC. Она занимается непосредственно производством филаментов, а ее подразделение 3D Solutions проводит НИОКР по созданию композиционных материалов.
REC и 3D Solutions в цифрах и фактах:
-
8 лет работы с термопластами в области аддитивных технологий;
-
серийно выпускается 22 различных типов материала в виде нити для FFF-печати;
-
за 2020 и 2021 год произведено и испытано более 130 различных композиций на основе термопластов;
-
собственное производственное оборудование и лабораторные комплексы для производства и тестирования термопластичных композиций как в литье, так и в 3D-печати;
-
самый узнаваемый бренд в области материалов для FDM-печати.
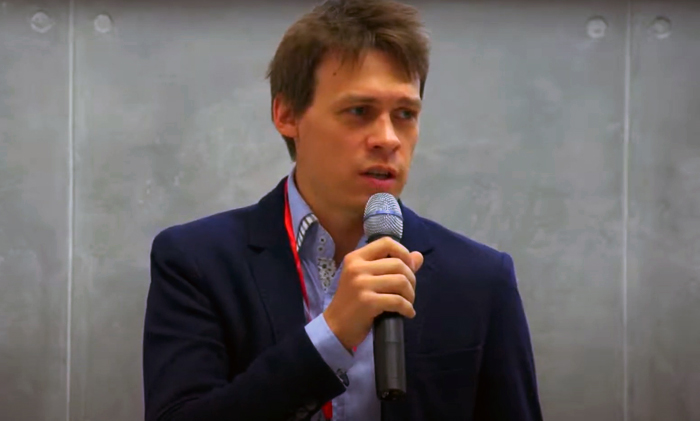
Сегодня в нашем блоге исполнительный директор REC и 3D Solutions Дмитрий Миллер делится своим опытом разработки и применения термопластов и композитных материалов и рассказывает о самых интересных проектах внедрения FDM-технологии.
Проверьте, решит ли 3D-принтер ваши задачи, – закажите услугу бесплатной тестовой 3D‑печати в iQB Technologies!
Термопласты и композиты – что это такое?
Термопласт – это полимер, который может стать пластичным при воздействии температуры. На основе термопластов производятся композиты – чистые пластики в сочетании с другими материалами, к примеру, ABS с поликарбонатом или армированный углеродным волокном. Таких вариаций может быть огромное количество.
За восемь лет на рынке мы успели поработать с большинством существующих пластиков, включая ABS, ASA, SBS, SEBS, PA, PP, PSU, PPSU, PEEK, PC, TPU, TPEE, PET, PETG, PEI, PLA, PS, PTFE, PVA, PMMA, PBT. И это не полный список – некоторые материалы, такие как ПВХ, не удалось довести до адекватно применимого состояния, поскольку возникают разного рода сложности с переработкой.
Как получаются композиты?
Мы берем необходимую полимерную основу и, в зависимости от поставленной задачи и требуемых свойств материала, модифицируем ее определенными компонентами. К ним относятся:
-
антипирены,
-
термостабилизаторы,
-
пластификаторы,
-
вспенивающие агенты,
-
прочие процессинговые добавки.
Также используется широкий ассортимент наполнителей, имеющих различные свойства. Это и самые привычные углеродные волокна, и стекловолокно, и базальтовое волокно, и кевларовые волокна. Для получения определенных свойств можно наполнять полимер пустотелыми стеклянными сферами и углеродными нанотрубками.
В нашем арсенале есть и металлонаполненные полимеры, применяемые в технологии формовки MIM (Metal Injection Molding). Правильнее называть их металлополимерными композициями, поскольку в их составе более 93% металла и не менее 7% связующего. Из такого композиционного материала с помощью литья или 3D-печати формуется изделие, затем химически вытравляется связующее, полученная модель запекается в печи, и конечном итоге мы получаем цельнометаллическую деталь.
Кроме того, можно получить композиции, проявляющие ферромагнитные свойства. Они востребованы в задачах, связанных с рентгенографией и радиоэлектроникой.
Эксперты iQB Technologies рекомендуют статью: Аддитивное производство формовочной оснастки из полимерных и композитных материалов
Кто основные потребители полимеров для 3D-печати?
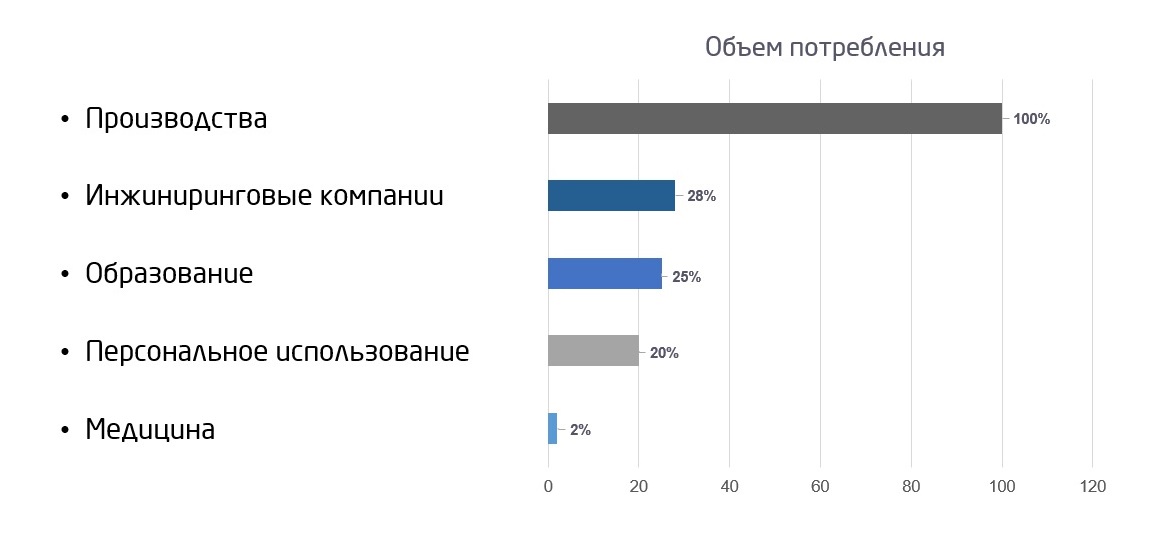
Самый главный наш потребитель – производство, поскольку аддитивными методами создают либо конечный продукт, либо какую-то его часть, либо оснастку для его производства. Большое количество заказов объясняется регулярностью, систематическим повторением и стабильностью производственного процесса.
Чуть больше четверти объема от производства – это инжиниринговые компании, которые занимаются 3D-печатью прототипов для проверки на собираемость, наглядных моделей и тому подобного.
Большой пласт, составляющий 25%, – сфера образования. Благодаря федеральным программам, таким как «Точка роста», 3D-принтеры поставлены в очень многие образовательные учреждения, и аддитивные технологии являются учебным предметом. Преподавание основ 3D-печати имеет огромное значение, поскольку помогает учащимся изменить образ мышления. Когда мы используем классические субтрактивные технологии – обтачиваем болванку или режем лазером, что-то вырезаем из плоского листа, – это одно мышление. Аддитивное производство снимает многие ограничения, мышление идет совершенно по-другому, и последующее поколение будет мыслить в техническом плане гораздо свободней.
Следующий сегмент занимает персональное потребление, которое может затрагивать абсолютно любые сферы. Это люди, а также малый бизнес, использующие 3D-принтеры для собственных целей, хобби.
И, наконец, медицина. Пока что объемы работ у нас в этой области небольшие, но прецеденты применения есть. Полимеры используется для аддитивного производства ортезов (приспособлений для фиксирования конечностей), протезирования и, совместно с образовательными учреждениями, для изготовления анатомических макетов под разные медицинские нужды.
Какие пластики самые популярные?
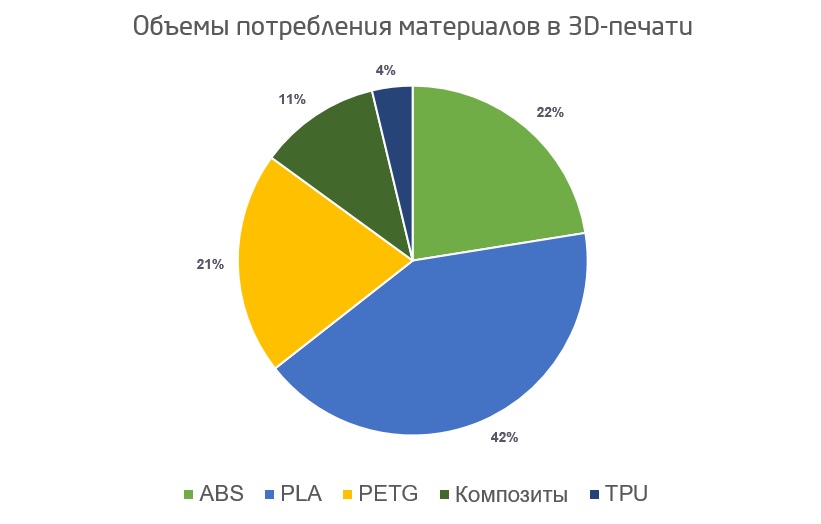
У клиентов REC и 3D Solutions первое место по объему потребления занимает PLA. Это вполне заслуженно, так как печатать им легче, чем каким-либо другим пластиком, и он наименее требователен к оборудованию. Любой самый простой персональный 3D-принтер будет прекрасно работать с этим материалом, и никаких сложностей не возникнет.
Второе место примерно поровну делят материалы ABS и PETG. Они используются в функциональном прототипировании, где PLA далеко не всегда применим из-за крайне низкой термостойкости: при 50 градусах он уже мягкий.
Далее идут различные композиционные материалы, и этот сегмент из года в год растет. В перспективе ближайших пяти лет они, вероятно, выйдут на первое место за счет возможности добиться любых необходимых свойств.
И совсем небольшой сегмент (4%) составляют полиуретаны, эфирные эластомеры – любые гибкие и эластичные полимеры. Их применяют заказчики всех остальных материалов, но для определенных задач, требующих эластичности и гибкости.
Читайте в блоге Композиты в FDM‑печати: виды, преимущества и топ российских материалов
Как применяется 3D-печать термопластами и композитами? Примеры готовых изделий
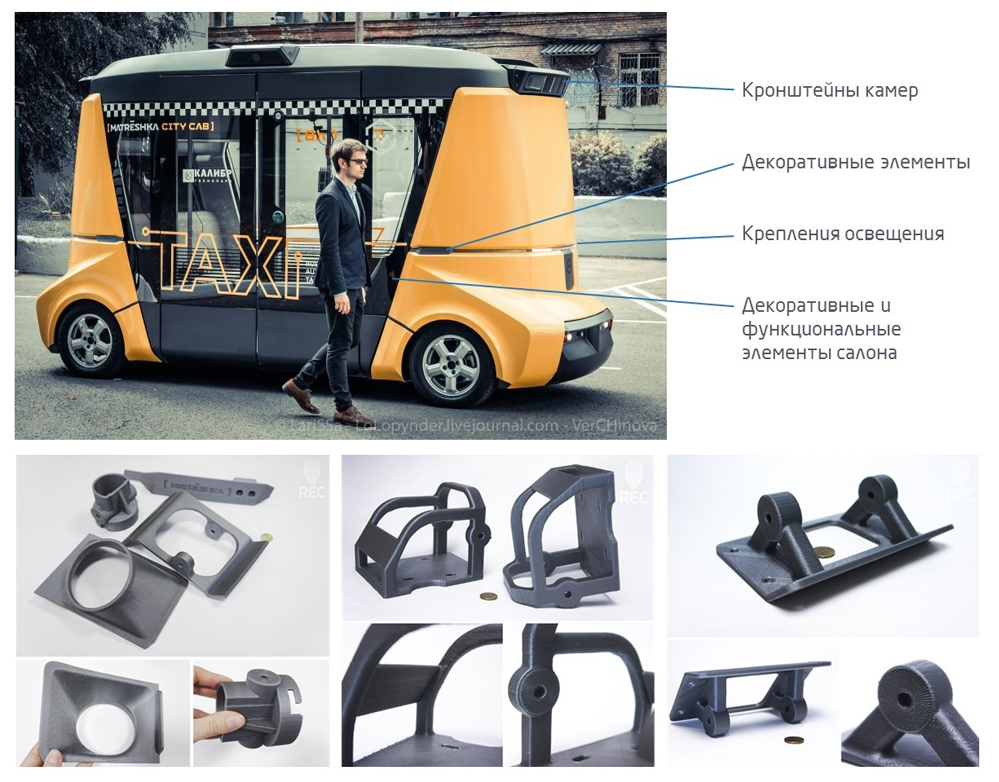
Перед вами (рис. 1) функциональный прототип беспилотного такси, содержащий в себе огромное количество деталей. Изготавливать каждую из них классическими заводскими методами достаточно сложно, накладно и долго. Благодаря 3D-печати компания-производитель оптимизировала процесс создания многих деталей – отражателей для передней оптики, кронштейнов, держателей, декоративных элементов и пр. Модели, нарисованные на компьютере, тут же на месте распечатывались и устанавливались – так, максимально быстро и просто, был реализован проект полнофункционального рабочего прототипа транспортного средства.
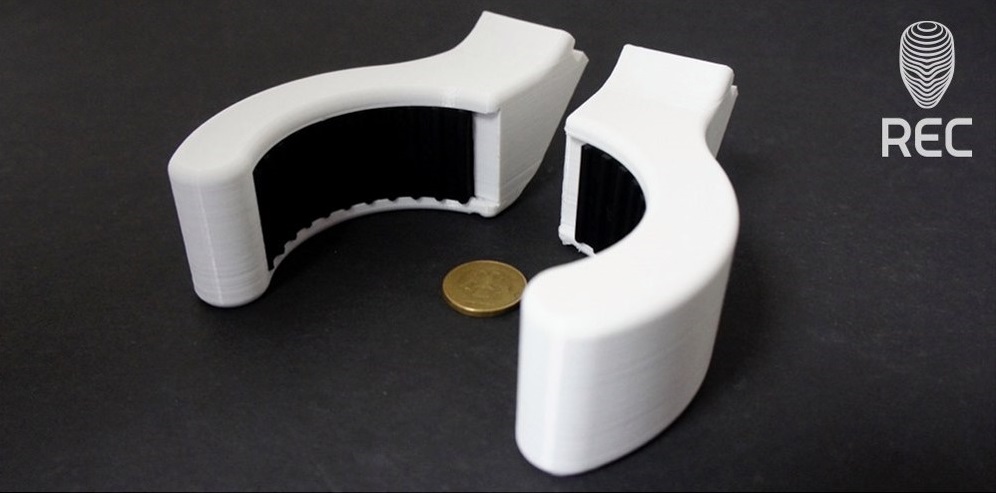
Интересный пример, когда комбинируют материалы для 3D-печати. На фото выше вы видите захват для руки робота-манипулятора. Сами клешни напечатаны из твердого пластика PETG, а внутренние накладки – из эластичного материала. Он гарантирует, что предметы не будут выскальзывать из руки манипулятора.
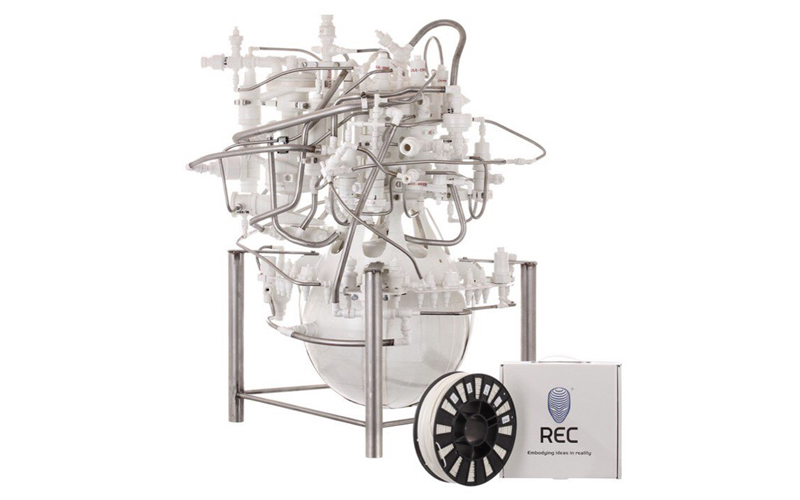
Перейдем к сложным системам. На рисунке 3 – реальный макет системы питания космической ракеты «Ангара», напечатанный из ABS-пластика, на нем проверяли собираемость. Необходимо было протестировать, можно ли разработанное устройство с большим количеством компонентов собрать без повреждений.
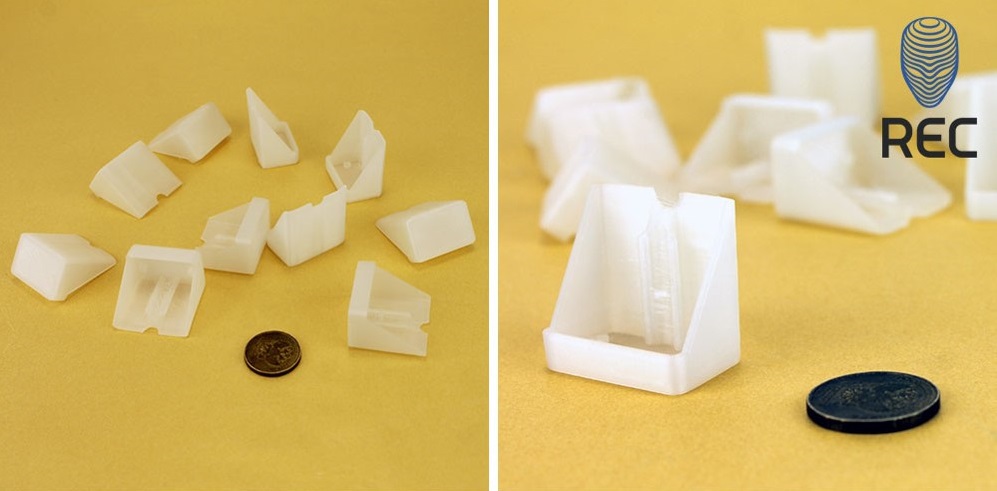
А здесь вы видите, как можно производить конечные изделия целиком при помощи 3D-печати. Компания занимается изготовлением светодиодных светильников небольшими сериями. В некоторых моделях есть пластиковые элементы – заглушки, рассеиватели света. Вся продукция дизайнерская, оригинальная, изготавливать тысячу штук методом литья в силикон получается дороже, не говоря уже о классическом литье пресс-форм: на таком тираже пресс-форма совсем не окупится, детали получатся «золотые». В данном случае 3D-печать – исключительно выгодное решение. В отличие от литья в силикон, аддитивные технологии дают больше свободы в геометрии, и партию можно произвести очень дешево и быстро.
Скорость производства определяется мощностью фермы 3D-принтеров. Как правило, когда мы интегрируем 3D-печать в производство, мы не ограничиваемся одной машиной и создаем ферму. Это целый парк идентичных аддитивных установок, на которые отправляется задание, и они сразу все вместе начинают печатать. Таким образом мы можем значительно увеличить производительность. Это легко масштабируется и стоит достаточно дешево, особенно если применяется FDM – самая доступная из всех технологий 3D-печати.
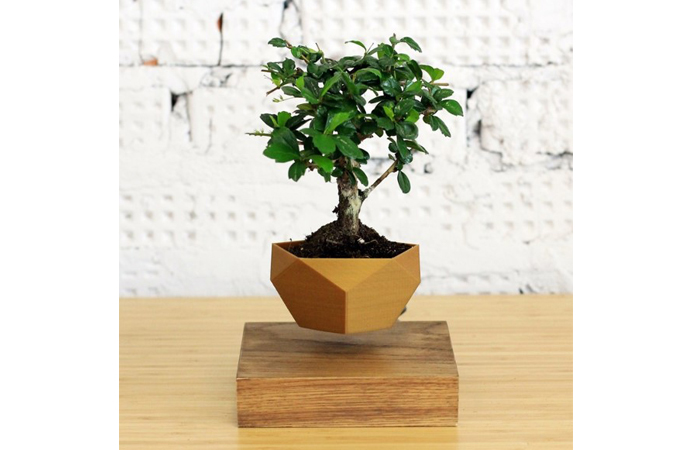
Любопытный проект стартапа, который специализируется на левитирующих растениях (рис. 5). Дерево в горшочке летает над деревянным бруском, работает приспособление на магнитах. Итак, задача была изготовить кашпо. Оно должно быть легким, не глиняным, чтобы было проще сделать магнит, и не бояться такой среды, как земля, удобрения и вода. Сначала были попытки выпускать деревянные горшочки, но дерево даже с защитными покрытиями в конечном итоге портилось от внутренней среды. Поэтому было решено внедрить 3D-печать пластиками. Компания заказывала 3D-печать у нас, но когда стало понятно, что производство рентабельно, закупила оборудование и материалы и стала производить кашпо различных дизайнов самостоятельно.
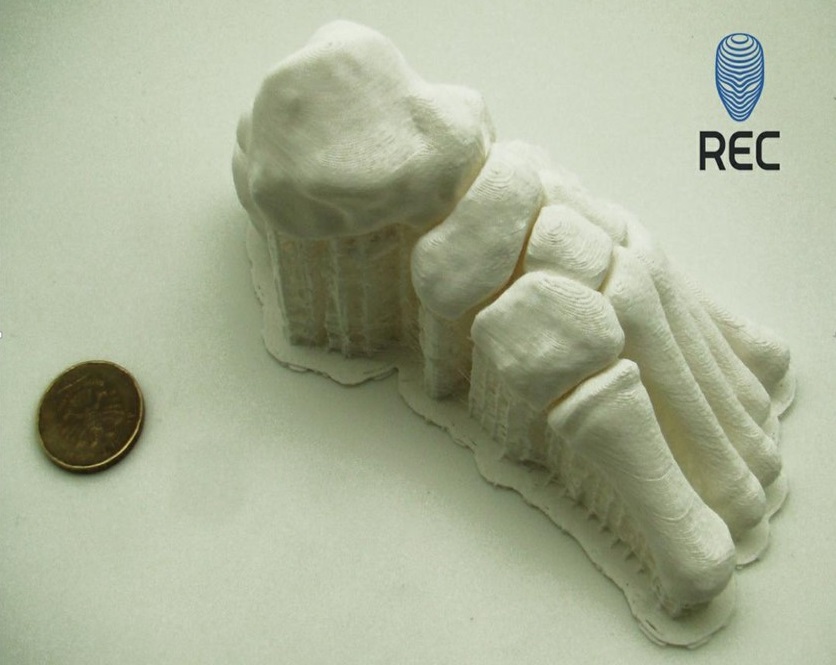
Нельзя обойти вниманием медицину. На фото – макет стопы, напечатанный из белого пластика по результатам компьютерной томографии. 3D-модель была получена на основе КТ и отправлена на 3D-принтер. У изделия есть два варианта применения:
-
студенты с помощью подобных реалистичных макетов могут практиковаться, выявлять патологии, поскольку использование реальных костей весьма ограничено;
-
хирургам по такой модели гораздо проще спланировать стратегию операции, сделать ее точнее на пациенте.
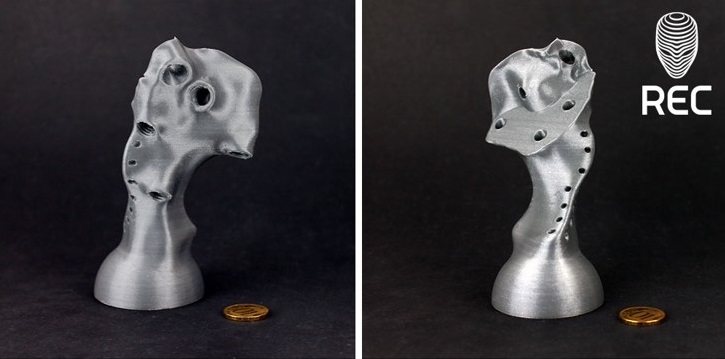
Еще одно медицинское изделие – прототип эндопротеза (рис. 7). Это предварительная модель, изготовленная из пластика, по которой проверяют точность и правильность протеза. Конечное изделие создают также на 3D-принтере, но уже из металла, по SLM-технологии, с первой попытки получая высокоточную модель индивидуального эндопротеза. Медицинский металл имеет высокую себестоимость и, чтобы исключить ошибки, протезы изначально печатают из пластика.
Читайте по теме: Пластик творит чудеса: как 3D-принтер имитирует органы человека
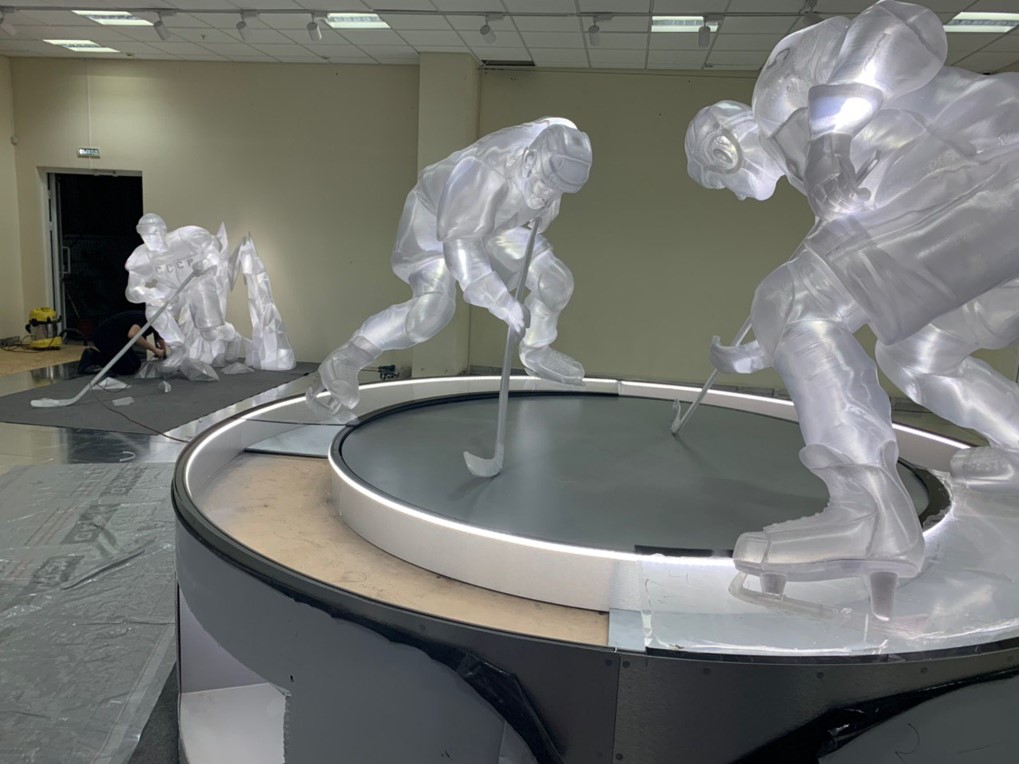
Теперь посмотрим, какие выгоды вы можете получить, используя крупноформатную 3D-печать полимерами. Одна из распространенных сегодня сфер применения – производство малых архитектурных форм: скульптур, статуй, декоративных элементов, архитектурных украшений (рис. 8). При помощи 3D-принтера такие модели создаются легко и быстро, и это один из самых дешевых способов изготовления. Кроме того, есть возможность широкого выбора материалов, добавления оптических эффектов, полупрозрачности (например, чтобы встроить внутрь скульптуры светящийся элемент для большего эффекта).
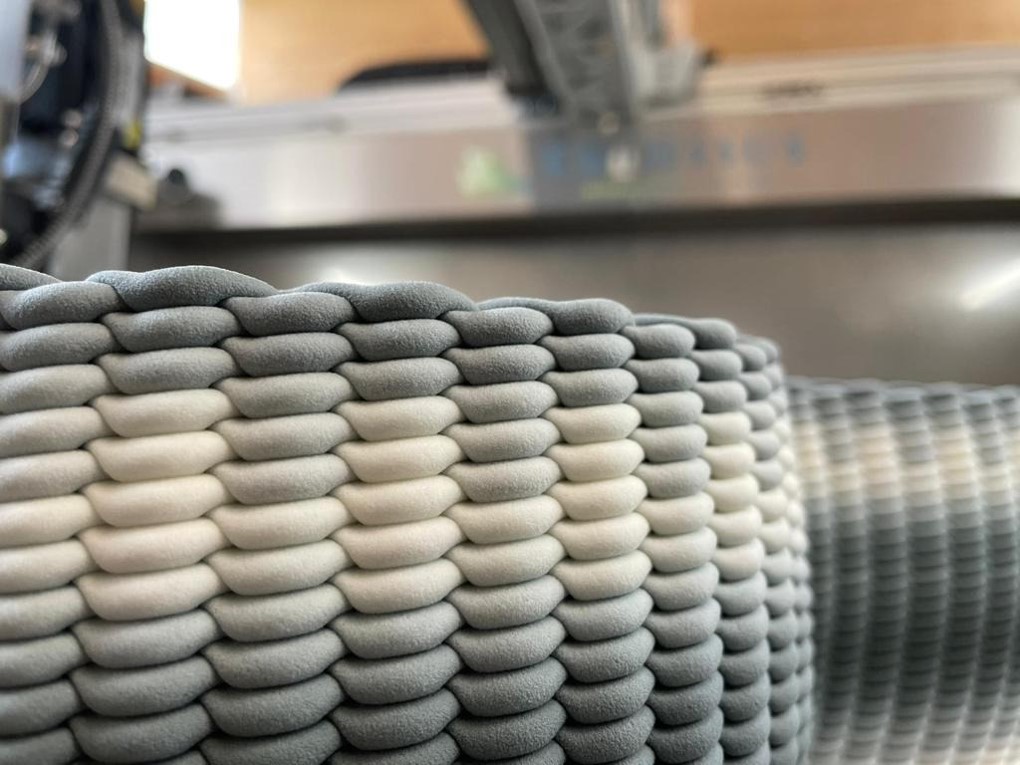
Как вы знаете, FDM-печать имеет одну особенность: из-за послойного построения детали получаются «полосатые». Однако этот недостаток можно обернуть в преимущество и при помощи крупноформатного 3D-принтера создавать интересные фактуры, как на рис. 9. Конечно же, в первую очередь это производство дизайнерской мебели и различных декоративных элементов и архитектурных форм.
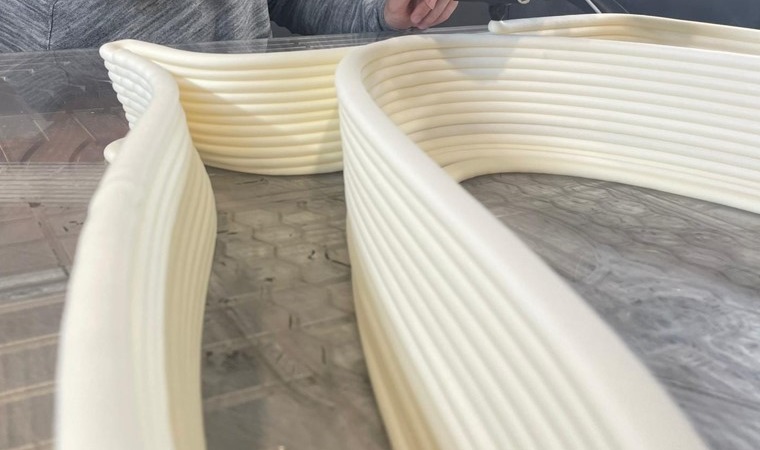
Для 3D-печати больших объектов по технологии FGF, использующей гранулы полимеров, есть отдельный пласт композиционных материалов. На рис. 10 показан процесс печати материалом, напоминающим монтажную пену. Схожесть не случайна – здесь применен вспенивающийся композит. Один кубометр сырья дает на выходе 25 кубометров вспененного материала. И, как видите, такая технология позволяет достичь очень большой высоты слоя, а чем толще слой, тем быстрее выполняется 3D-печать. А некоторое снижение плотности облегчает всю конструкцию в целом.
Подробнее о крупноформатной 3D-печати пластиком: решения, задачи, примеры внедрения
FDM/FGF-печать имеет весьма низкую точность. Тем более материалы имеют разную усадку, а в случае различной геометрии деталей усадка будет нелинейной, неодинаковой просто из-за особенности самой технологии – из-за того, как укладывается материал, какие температурные нагрузки применяются. В случае производства оснастки, как правило, используют гибридные технологии – модель печатают, а затем рабочую поверхность фрезеруют. Таким образом мы получаем нужную шероховатость и прецизионную точность.
Разная оснастка требует разных материалов. Где-то нужна высокая термостойкость, где-то высокая прочность, а где-то в приоритете максимально низкая цена. Под каждую задачу есть свой оптимальный материал.
И есть огромное поле для оптимизации производства, чтобы изготавливать достаточно большие объекты дешево и за невероятно короткие сроки – буквально за считаные часы.
Фото в заставке © zbulvar.ru
Статья опубликована 12.11.2021 , обновлена 07.10.2024