Партнерство в области НИОКР | Непрестанно совершенствуемый болид | Быстрая проверка конструкции | Новые возможности использования аэродинамической трубы | Высокая скорость и точность изготовления деталей | Новые направления развития
Гонки «Формулы-1» – это технический вид спорта, основанный на непрекращающихся инновациях и требующий от болидов высокой надежности. Гоночные команды, в том числе Renault Sport Formula One, неустанно стремятся к тому, чтобы соответствовать постоянно улучшающимся результатам лидеров и превосходить их. В этом спорте процесс исследований и разработок никогда не останавливается, и технические партнерства крайне важны для достижения организацией ее целей. Сотрудничество Renault Sport Formula One с 3D Systems ускоряет процесс разработки и стимулирует инновации на всех этапах – от испытаний в аэродинамической трубе и на аэродинамическом стенде до изготовления надежных готовых деталей.

«Гонка за гонкой применяется все больше компонентов из сложных композитов и аэрокосмических сплавов, прошедших жесткий отбор в исследовательских и экспериментальных лабораториях, – поясняет технический директор Renault Sport Formula One Ник Честер. – В конце каждого гоночного сезона мы ожидаем, что наш болид будет больше чем на секунду на круг быстрее, чем в его начале, и наши технические партнеры проходят столь же безжалостный отбор. Мы не заинтересованы в отношениях, которые не помогают нам совершенствовать свои показатели».
Критерий непрекращающегося инновационного процесса и активного сотрудничества объясняет выбор командой Renault Sport Formula One компании 3D Systems и ее пакета технологий 3D-печати.
Партнерство в области НИОКР
Команда Renault Sport Formula One, базирующаяся в Энстоуне, Великобритания, применяет технологии 3D Systems с 1998 года. Она одной из первых стала применять 3D-печать для прототипирования и тщательно отслеживала развитие этой технологии. На первых порах технология применялась для проверки проектируемых деталей с точки зрения соответствия функциональным и размерным требованиям, а также для изготовления приспособлений и крепежа для точной сборки. По мере развития партнерства между двумя компаниями инженеры 3D Systems помогли команде Renault Sport Formula One понять и использовать имеющиеся у них возможности, материалы и методологии. То, что команде удалось обеспечить загрузку своей аэродинамической трубы, свидетельствует о положительном влиянии партнерства с 3D Systems и разработке инновационных автомобильных деталей с использованием 3D-печати для литья по выжигаемым моделям, а также 3D-печати металлами (DMP).
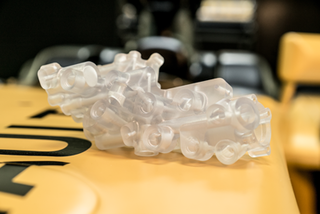
«Поддержка, предоставляемая компанией 3D Systems, также развивалась по мере расширения нашего сотрудничества, – пояснил г-н Честер. – Если оглянуться назад, мы увидим, что по мере совершенствования свойств материалов команда стремилась расширить спектр возможностей применения материалов быстрого производства для решения более сложных инженерных задач. Количество автомобильных компонентов, производимых с использованием аддитивных технологий, увеличивается с каждым годом, принося значительную выгоду команде с точки зрения гибкости применения и сокращения времени производства и затрат».
Среди установок 3D Systems, в настоящее время применяемых Renault Sport Formula One, – шесть стереолитографических 3D-принтеров и три машины селективного лазерного спекания (SLS). Применяются различные материалы – от Accura® для изготовления приспособлений и крепежа, выжигаемых моделей и деталей для аэродинамической трубы до DuraForm® PA и DuraForm GF для деталей, устанавливаемых на болид, таких как электрические распределительные коробки и каналы воздушного охлаждения. От проверки пригодности материалов до оптимизации конструкции деталей – партнерство между Renault Sport Formula One и 3D Systems обеспечивает наилучшие результаты, как на гоночной трассе, так и вне ее.
Непрестанно совершенствуемый болид
Каждый год команда Renault Sport Formula One проектирует и строит новый болид, учитывающий изменения в правилах и следующий естественному циклу НИОКР, направленных на улучшение технических характеристик болида. В качестве примера вызовов, которые влекут за собой изменения в правилах «Формулы-1», можно привести новшества 2017 года, разрешающие более тяжелые шины большего диаметра, более широкое переднее антикрыло, более низкое и более широкое заднее антикрыло и более высокий диффузор. Это означает, что детали 2016 года не могли быть повторно использованы в 2017 году.
Как только гоночный сезон начинается, напряжение только растет: иногда между гонками есть только неделя на внесение технических изменений. От специальных гоночных до неровных и извилистых уличных трасс, каждая гонка ставит перед инженерам новые вызовы, связанные с архитектурой трассы, климатом и типом асфальта.
Команда готовится к уникальным особенностям каждой трассы и использует все время в небольших промежутках между гонками для внедрения плодов исследований на болидах и оборудовании. Очевидно, что оперативность и точность 3D-печати имеют большую ценность при подготовке к новым гонкам. «Болид совершенствуется ежедневно во время гоночного сезона, – говорит Патрик Уорнер, ведущий менеджер по цифровым технологиям Renault Sport Formula One. – На каждой трассе нам нужны новые компоненты, и преимущества аддитивной технологии становятся все более актуальными».
ЗАДАЧА
- Ускорить процесс НИОКР в автомобильной отрасли и способствовать инновациям в непрерывно меняющихся условиях.
РЕШЕНИЕ
- Комплексные решения 3D Systems от принтеров и материалов до опыта применения.
РЕЗУЛЬТАТЫ
- Повышение эффективности: небольшой группе инженеров предоставлена возможность производить сотни деталей в неделю для испытаний в аэродинамической трубе.
- Изготовление сложных автомобильных деталей за несколько часов, а не недель, благодаря технологиям SLA и SLS.
- Изготовление более инновационных деталей с использованием напечатанных на 3D-принтере выжигаемых литейных моделей.
- Обеспечение качества сборки посредством разработки и изготовления высокоточных приспособлений и крепежных изделий, которые были бы невозможны или требовали бы слишком много времени при использовании традиционной технологии.
- Открытие новых возможностей разработки инновационных деталей, напечатанных на 3D-принтере, для проведения испытаний и установки на болиды.
Быстрая проверка конструкции
Быстрое прототипирование с использованием 3D-печати сразу продемонстрировало свои возможности в гонках «Формулы-1», где детали, устанавливаемые внутри болида, отличаются плотной компоновкой и ограничены обводами аэродинамической обшивки. Специалисты по аэродинамике команды Renault Sport Formula One быстро поняли потенциал 3D-печати для подтверждения соответствия функциональным и размерным требованиям, исходя из сложности деталей, изготавливаемых по технологиям 3D Systems. Благодаря этому масштабы применения 3D-технологий стали быстро расти – от быстрого прототипирования до изготовления моделей для аэродинамических испытаний.
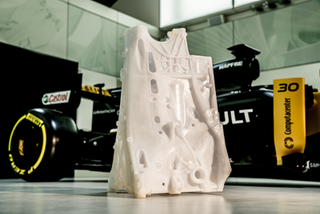
Аэродинамические испытания – это наука, основанная на опыте, – поясняет г-н Уорнер. – Мы разрабатываем и сравниваем новые идеи и определяем дальнейшие направления работы. Чем больше идей мы можем сравнить и оценить, тем успешнее пройдут гонки». С точки зрения качества деталей, срока службы и производительности оборудования, технология SLA оказалась незаменимой для гоночной команды.
Новые возможности использования аэродинамической трубы
В последние годы группа аэродинамики в гоночной команде Renault Sport Formula One значительно выросла и сейчас насчитывает 120 сотрудников, среди которых специалисты по аэродинамике, техники и моделисты. По словам Уорнера, развитие этого направления было в значительной степени обусловлено более широким применением аддитивных производственных технологий компании 3D Systems. В качестве одного из основных преимуществ технологии 3D Systems он указывает на возможность устройства в моделях для аэродинамических испытаний сложных внутренних каналов, а также возможность собирать больше показаний давления.
«Модель болида для испытаний в аэродинамической трубе снабжена сложной сетью датчиков давления, – говорит Уорнер. – До появления технологии SLA датчики устанавливали путем сверления отверстий для отбора давления в деталях из металла и углеродного волокна. Доступная нам теперь возможность изготавливать твердые тела сложной формы с разветвленной системой внутренних каналов революционизировала расположение датчиков и радикально увеличила их количество. Это мечта аэродинамика наяву».
По оценке Уорнера, только для проведения испытаний в аэродинамической трубе требуется печатать на 3D-принтере по 600 деталей в неделю – и всю эту работу выполняют всего пять инженеров группы цифровых технологий.
«Используя традиционные технологии, мы не смогли бы даже мечтать о таком результате, – замечает Патрик Уорнер. – Нам потребовался бы цех механообработки размером с небольшой город. Благодаря 3D Systems у нас есть универсальная мастерская. У нас есть необходимое оборудование, нужные материалы и опыт прикладных инженеров, которые могут немедленно приступить к выполнению поставленной задачи».
Высокая скорость и точность изготовления деталей
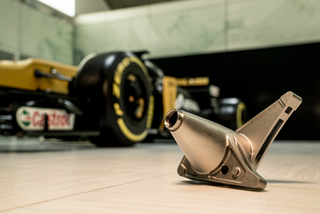
С точки зрения производительности и эффективности, 3D-печать значительно увеличила способность гоночной команды Renault Sport Formula One реагировать на новые вызовы, связанные с постоянно меняющимися правилами гонок «Формулы-1». Благодаря технологиям SLA и SLS, сложные приспособления и крепежные детали, гидродинамические детали и автомобильные компоненты можно изготавливать в течение считанных часов, а не недель, что делает 3D-технологии идеальными для решения логистических задач, характерных для гонок «Формулы-1».
Помимо огромного числа деталей, ежемесячно испытываемых в аэродинамической трубе, команда Renault Sport Formula One изготавливает ряд деталей для гоночных болидов напрямую. «Технологии 3D Systems легли в основу нового эффективного производственного процесса, который позволил нам сократить как продолжительность цикла, так и его стоимость, принеся всей команде неоценимую пользу, – говорит Роб Уайт, исполнительный директор Renault Sport Formula One. – С одной стороны, мы ценим возможность испытать несколько вариантов одной и той же детали в аэродинамической трубе. С другой стороны, мы видим, как количество деталей в болиде, изготовленных методом селективного лазерного спекания, растет с каждым годом».
3D-печать помогает команде создавать более легкие детали, которые увеличивают скорость и топливную эффективность болида, а также проводить точные и информативные расходные испытания для улучшения характеристик двигателя и уменьшения износа. Готовый проект вместе со спецификациями на материалы отправляют в группу цифровых технологий команды для изготовления детали. Благодаря технологиям SLA и SLS сложные автомобильные компоненты можно изготавливать быстрее, чем когда-либо: в некоторых случаях деталь готова к осмотру еще до завершения подготовки чертежей.
Напечатанные на стереолитографическом 3D-принтере литейные выжигаемые модели также все шире применяются гоночной командой при изготовлении таких изделий, как детали коробки передач и подвески, что устраняет ограничения на уровень сложности деталей и позволяет инженерам команды более творчески подходить к проектированию. Точность технологии SLA уменьшает сроки изготовления литейных моделей и механической обработки готовых отливок.
Новые направления развития
Преимущества технологий, опыта и услуг 3D Systems тесно связаны с важнейшими приоритетами команды Renault Sport Formula One, такими как инновации, эффективность, максимальная точность и прецизионность. Для Боба Белла, технического директора Renault Sport Formula One, 3D Systems не просто поставщик технологий: между компаниями сложилось настоящее партнерство, приносящее результаты в настоящем и создающее огромный потенциал на будущее.
«Наше партнерство с 3D Systems на протяжении последних двух десятилетий значительно повысило продуктивность и эффективность, – говорит Белл. – Оно открыло новые возможности, которые, как я полагаю, в будущем будут только расширяться».
Перевод с английского. Оригинал этого материала на сайте 3D Systems.
Компания iQB Technologies предлагает вам заказать одну из следующих услуг: консультацию экспертов, обучение 3D-технологиям, тестовую 3D-печать/3D-сканирование, выезд специалистов на ваше предприятие, диагностику или заказ 3D-оборудования.
Статья опубликована 10.11.2017 , обновлена 14.05.2021