Аддитивные технологии находят активное применение в энергомашиностроении, приборостроении, авиационной промышленности, космической индустрии, там, где высока потребность в изделиях сложной геометрии. В России с аддитивными технологиями познакомилось уже немало предприятий. Предлагаем вашему вниманию материал из альманаха «Управление производством», в котором описывается несколько примеров эффективного внедрения 3D-печати.
Доступность аддитивных технологий дает возможность наладить производство необходимых деталей на собственных площадках, исключив посредников, поставщиков, риски доставки и сократив себестоимость производства. Например, как отметил глава АО «Наука и инновации» Алексей Дуб, «бывают случаи, когда изделие весом 900 г изготавливается из исходной заготовки весом 28 кг. Понятно, что с учетом цены материала стоимость подобных машиностроительных работ очень высока. Но можно это сделать фактически без потерь материала и сразу выращивать это изделие».
Серьезные исследовательские проекты реализует Всероссийский НИИ авиационных материалов (в том числе по созданию расходных средств для трехмерной печати). Большой интерес высказывают предприятия металлургии, авиационной, космической промышленности и военно-промышленного комплекса, в их числе – НПО «Энергомаш», Тихвинский вагоностроительный завод, Уралвагонзавод, Воронежсельмаш, Тушинский машиностроительный завод и другие. В основном они применяют 3D-печать для создания прототипов деталей, а не конечных изделий.
«Аддитивные технологии открыли возможность изготовления деталей любой сложности и геометрии без технологических ограничений. Геометрию детали можно менять еще на стадии проектирования и испытания», – подчеркнул начальник отдела разработки перспективных технологий ремонта «Авиадвигателя» Александр Ермолаев.
На Тихвинском вагоностроительном заводе (НПК ОВК) был реализован первый в отрасли проект применения аддитивных технологий в производстве. Здесь с помощью 3D-принтера выпускаются элементы литейной модельной оснастки, служащей для получения при формовке отпечатка в песчаной огнеупорной смеси под последующую заливку металла. Оборудование гарантирует высокое качество печати – толщина каждого из слоев составляет от 0,05 до 0,15 мм в зависимости от настроек. Вес произведенного принтером изделия может достигать 150 кг, что достаточно много, учитывая использование в работе полимерного сырья. Применение новой технологии позволило сократить время выпуска крупных (длиной до 3 м) элементов оснастки сложной конфигурации всего до одной недели с последующим незамедлительным началом производства опытных отливок. Кроме того, данное оборудование имеет хорошие показатели энергоэффективности и гарантирует экономный расход материалов для 3D-принтера.
Аддитивные технологии открыли возможность изготовления деталей любой сложности и геометрии без технологических ограничений. Геометрию детали можно менять еще на стадии проектирования и испытания.
Подготовка файлов для печати осуществляется на компьютерах со стандартным программным обеспечением, в работу принимаются файлы формата STL. Это широко используемый сегодня формат хранения трехмерных объектов для стереолитографических 3D-принтеров. Инвестиции в проект составили порядка 60 млн рублей.
Александр Зданевич, ИТ-директор НПК «Объединенная Вагонная Компания»: «Технологии аддитивной печати прогрессируют, и, вероятнее всего, уже в ближайшем будущем они изменят лицо целого ряда индустрий. Главным образом это касается предприятий, на которых выпускаются штучные товары под конкретный заказ. С массовым производством дело обстоит сложнее, хотя разные типы 3D-принтеров уже сейчас находят применение в данной области.
Существует множество технологий объемного синтеза. Одной из перспективных для промышленного внедрения является лазерная стереолитография (SLA). Процесс можно разделить на два этапа. На первом формируется слой построения в виде равномерно распределенного по поверхности рабочей платформы жидкого фотополимера. Затем происходит выборочное отверждение участков данного слоя в соответствии с текущим сечением построенной на компьютере 3D-модели.
Применительно к железнодорожному машиностроению данную технологию можно использовать на этапе подготовки литейного производства, в частности, при производстве комплекта литейной оснастки. Один и тот же комплект оснастки, уникальный под каждую отливку, используется на протяжении тысяч циклов производства соответствующих литейных форм.
От соблюденной в процессе изготовления комплекта оснастки точности всех предусмотренных конструкторами параметров напрямую зависит качество конечного изделия. Традиционный способ изготовления комплекта оснастки путем механической обработки материалов (металла, пластика, иногда и дерева) весьма трудоемок и длителен (подчас занимает до нескольких месяцев), при этом чувствителен к ошибкам.
Технологии 3D-печати позволяют максимально точно воспроизводить требуемую геометрию элементов оснастки, получаемых как напрямую печатью, так и заливкой в изготовленные на принтере мастер-модели, и при этом ощутимо экономить время».
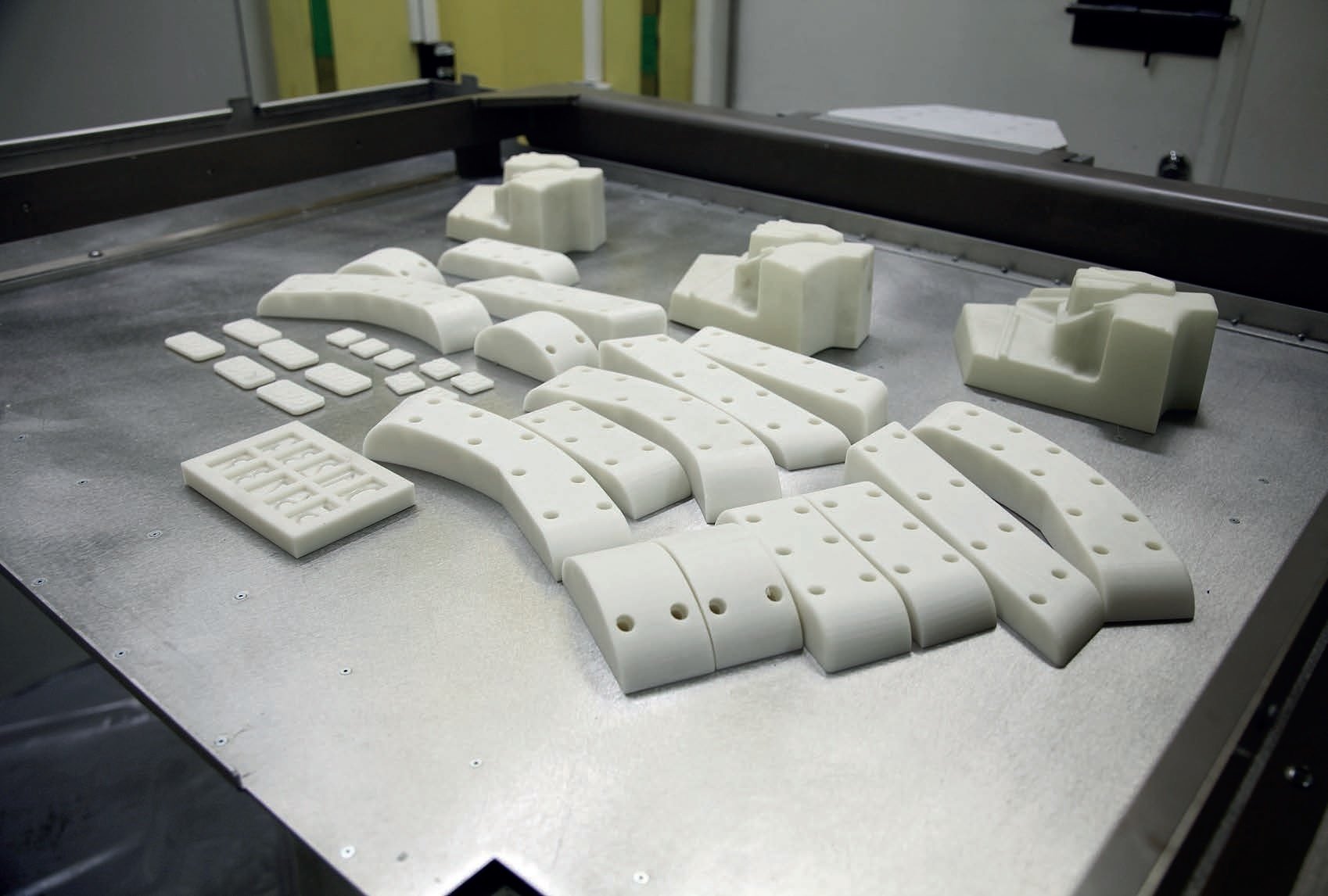
На пермском моторном заводе «Авиадвигатель» технологию селективного лазерного спекания (SLS) впервые применили еще в 2010 году для изготовления литых деталей по выжигаемым моделям. В 2011 году на предприятии появилось оборудование для ремонта деталей методом лазерной наплавки (LMD), в 2013-м – началось освоение выращивания металлических деталей по технологии селективного лазерного плавления (SLM). Оборудование «Авиадвигатель» приобретал в рамках программы техперевооружения предприятий Объединенной двигателестроительной компании, которое проводилось в преддверии начала проекта по созданию перспективного двигателя ПД-14 самолета МС-21. Также при помощи аддитивных технологий завод выполняет работы по доводке деталей для двигателей наземного применения – газовых турбиниэлектростанций.
«Сейчас конструкторы разрабатывают детали, геометрию которых традиционными методами – точением или литьем – выполнить крайне сложно или вообще технически невозможно, – поделился начальник отдела разработки перспективных технологий ремонта «Авиадвигателя» Александр Ермолаев, – а на «выращивание» одной детали, к примеру, завихрителя, кронштейна, гребенки, уходит от 6 до 40 часов». Завод использует титановые, никелевые, стальные, кобальт-хромовые порошки: для лазерного плавления требуется диаметр 10-63 мкм, для наплавки – 40-80 мкм, – в год примерно по 200 кг каждого наименования.
КБ «Луч» представило свой опыт применения возможностей 3D-печати в рамках первой конференции по аддитивным технологиям, продемонстрировав беспилотный летательный аппарат. Он был спроектирован на компьютере, причем оптимальную конструкцию предложила специальная программа. Затем все узлы и детали летательного аппарата были напечатаны при помощи 3D-принтера – эта работа заняла 30 часов. Сотрудникам КБ осталось только собрать аппарат. На всю работу, от замысла до изготовления беспилотника, ушло всего два месяца, в то время как традиционно это занимает несколько лет.
На «выращивание» одной детали, к примеру, завихрителя, кронштейна, гребенки, уходит от 6 до 40 часов.
«Данные технологии уже не являются чем-то фантастическим. Их применение может быть особенно актуально для удаленных и труднодоступных производств, которыми являются наши газоперерабатывающие заводы, – их целесообразно будет оснастить новым оборудованием, как только 3D-печать станет более-менее доступна на рынке. Это позволит на месте осуществлять быстрый выпуск деталей для внепланового ремонта в место содержания аварийно-технического запаса, – поделился собственным видением Олег Новожилов, директор по корпоративному обучению и управлению знаниямикомпании СИБУР. – У данной темы есть много нюансов, касающихся в том числе и сертификации продукции, но все проблемные моменты могут быть решены».
Активно осваивает цифровые технологии производства пензенское научно-производственное предприятие «Рубин». Инженеры-конструкторы предприятия создают объемные чертежи с помощью систем автоматизированного проектирования (САПР или CAD), а затем изготавливают прототипы с помощью 3D-принтеров. «Не каждое изделие можно получить механически. Эта технология позволяет получать очень сложные профили с такими полостями, что инструмент просто не может обеспечить», – пояснил заместитель начальника конструкторского отделения АО «НПП «Рубин» Алексей Логинов.
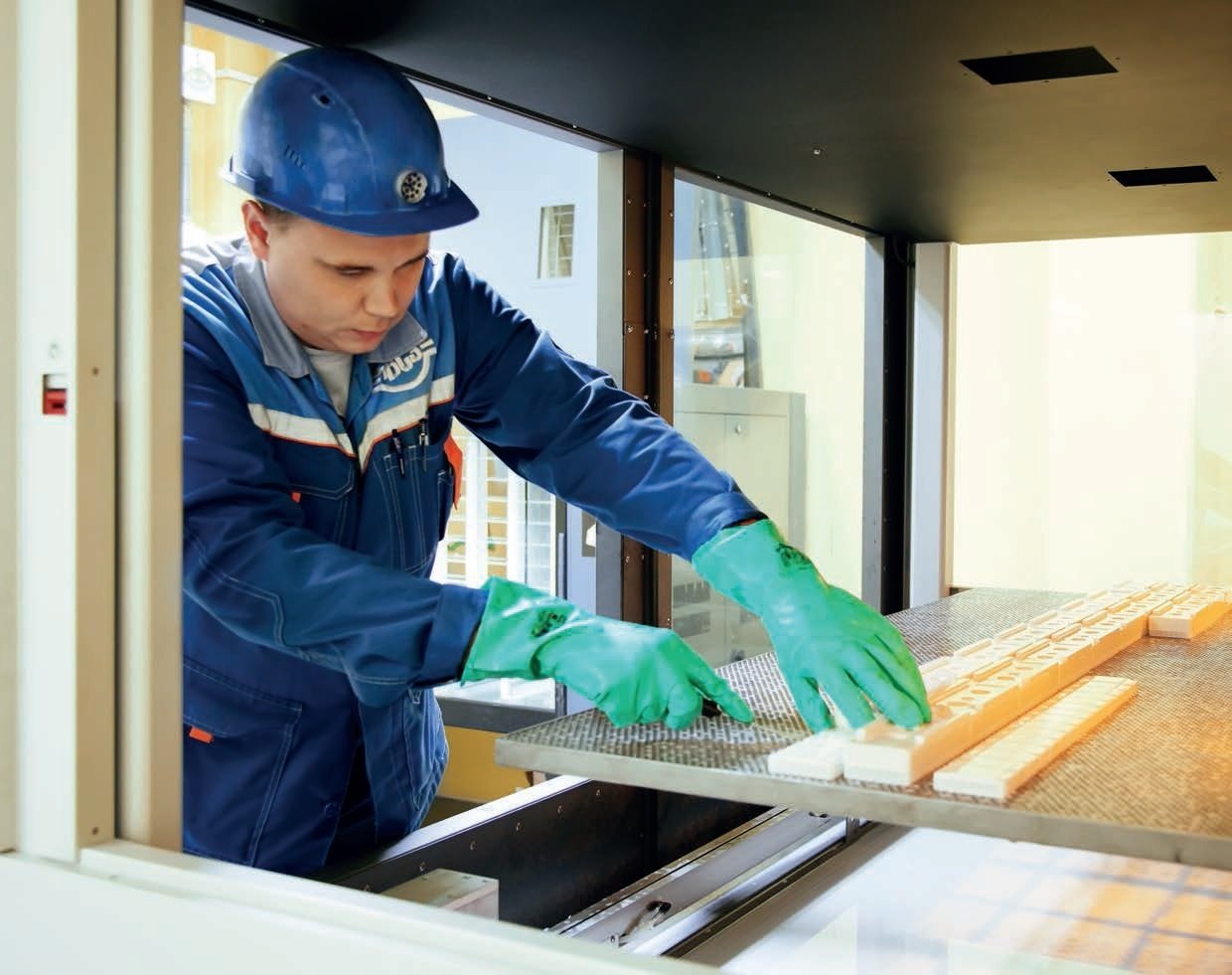
Пополнили 3D-принтером свой арсенал технических средств и разработчики ЗАО «Промтрактор-Вагон». Впервые технология начала применяться для печати деталей тележки «33». «Эти копии в уменьшенном масштабе очень пригодились для проработки алгоритмов сборки и проверки на собираемость инновационной вагонной тележки, – рассказал главный конструктор Андрей Яковлев. – Кроме тележки «33» в ОГК предприятия при помощи 3D-принтера изготовили узлы и детали вилочного погрузчика, выпускаемого в ОАО «САРЭКС».
Не каждое изделие можно получить механически. Эта технология позволяет получать очень сложные профили с такими полостями, что инструмент просто не может обеспечить.
Ранее на создание натурного прототипа из специального пластилина, например, из 50 деталей, конструкторам пришлось бы потратить недели, а то и месяцы. Потребовались бы кропотливые замеры, а затем подгонка деталей модели. «3D-принтер 'выпекает' деталь конструкции в среднем за 20-40 минут (в зависимости от сложности детали), – подчеркнул Андрей Яковлев. – Причем они могут быть самых разных цветов. Таким образом, есть возможность отпечатать полноценную конструкторскую модель, у которой каждая деталь выполнена разными оттенками. 3D-печать позволяет доработать узлы и компоненты изделий до начала серийного производства, устранить мелкие недочеты, которые неизбежны при проектировании новой продукции».
В «отпечатанные» модели можно встроить и другие узлы и агрегаты. Трехмерная печать полностью окупается за счет высокой скорости изготовления прототипов, а также за счет «доработки на столе» прямо в ОГК, которая экономит уйму времени и денег, нежели изготовление натурных образцов в «железе» на производстве.
Значительную работу по продвижению аддитивных технологий проводит Госкорпорация «Росатом». Руководство уверено, что скоро в госкорпорации будут присутствовать все компоненты «цифрового производства» – от разработки материалов, оборудования, технологий до производства изделий. В отрасли реализуется программа по аддитивным технологиям, она состоит из подразделов: технология, сырье, оборудование, стандартизация. Разработкой технологий производства металлических порошков для 3D-печати в Росатоме занимаются три института: «Гиредмет», ВНИИХТ, ВНИИНМ. Одновременно ведется работа по созданию опытного образца 3D-принтера для трехмерной печати металлических и композитных изделий. Росатом планирует представить образец уже к концу 2017 года.
Трехмерная печать полностью окупается за счет высокой скорости изготовления прототипов, а также за счет «доработки на столе» прямо в ОГК, которая экономит уйму времени и денег, нежели изготовление натурных образцов в «железе» на производстве.
«К началу 2018 года мы должны весь цикл по аддитивным технологиям внутри Росатома замкнуть. Нам нужен еще год, чтобы запустить свой собственный пилотный образец установки, и примерно столько же – для того, чтобы договориться со всеми сторонами, которые обеспечивают используемую нормативную составляющую», – рассказал Алексей Дуб.
В структуре Росатома аддитивные технологии развиваются в топливной компании «ТВЭЛ», которая активно сотрудничает с созданным при УрФУ региональным инжиниринговым центром, работая над созданием российского 3D-принтера. Для Уральского электрохимического комбината и его предприятий порошковая металлургия не новинка. Например, на заводе электрохимических преобразователей порошки применялись при производстве фильтров для газовой диффузии урана при разделении изотопов, также для припоев и поверхностного напыления.
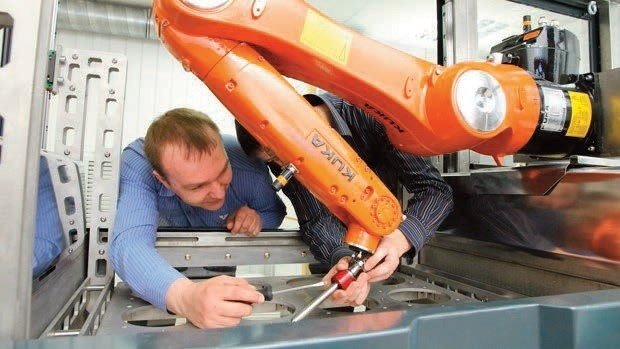
Одним из первопроходцев в области лазерных принтеров можно назвать научно-образовательный центр «Современные производственные технологии» Томского политехнического университета. Он укомплектован принтером электронно-лучевого сплавления (электронно-лучевым), лазерным принтером, принтерами, печатающими армированными композитами, а также ультразвуковым томографом, осуществляющим здесь же, «у станка», неразрушающий контроль готовых изделий. Специалисты центра изготавливают АМ-установки, разрабатывают программное обеспечение к ним и намерены продвинуться дальше «лаборатории».
В центре аддитивных технологий ТПУ настроен весь производственный цикл – от идеи до реализации готового изделия. Можно произвести и протестировать детали для обшивки космических кораблей, импланты для черепно-лицевой хирургии, изделия сложной формы для авиационной промышленности и многое другое, а также создать новые цифровые установки, например, для печати инструментов на МКС. «С помощью наших уникальных технологий мы можем создавать импортозамещающую продукцию, которая в разы дешевле импортных аналогов, при этом по качеству не хуже», – уверен директор центра Василий Федоров.
У развития аддитивных технологий есть и сдерживающие факторы.
- Во-первых, высокая стоимость технологии (оборудования и материала), впрочем в процессе развития технологий цена постепенно снижается.
- Во-вторых, нехватка квалифицированных, знающих технологию кадров.
- В-третьих, недостаточная освоенность, отсутствие метрологического обеспечения вызывает опасения при производстве деталей высокой важности.
- АМ-процессы (Additive Manufacturing) пока не интегрированы в технологию изготовления изделий. «Понятно, что любой ответственный конструктор не поставит в ответственное изделие деталь, не зная при этом, сколько она прослужит», – прокомментировал Алексей Дуб.
- Важной задачей является необходимость разработки системы сертификации и стандартизации аддитивных изделий, технологических процессов, порошков и композиций. Для решения этих вопросов при Росстандарте был сформирован технический комитет, который ведет работу по созданию нормативной документации в сфере аддитивных технологий.
3D-принтинг начинает распространяться в мире, и Россия не должна отставать в этой области. Применение данных технологий позволяет удешевить изделие, ускорить его проектирование и производство.– глава Минпромторга Денис Мантуров
Заключение
Популярность аддитивных технологий неуклонно растет. Хотя суммарный объем мирового рынка относительно невелик (порядка 6 млрд долларов), ежегодные темпы роста не могут не впечатлять – в среднем 20-30%. Впрочем единогласия в оценке роли аддитивных технологий в промышленности все еще нет: одни говорят, что внедрение методов 3D-печати приведет к закату промышленности в традиционном смысле, другие – что трехмерные принтеры станут лишь одним из элементов производственных схем. Но несмотря на все существующие разногласия, большие перспективы аддитивных технологий в промышленности невозможно отрицать.
Непосредственное выращивание изделий со сложной геометрией и из специфических материалов оказывается весьма выгодным с экономической точки зрения. Оно позволяет экономить материал, время, снижает риск ошибок. 3D-принтеры перестали быть «дорогой игрушкой», сегодня они занимают полноправное место среди ключевых технологий Индустрии 4.0.
Оригинал этого материала: Аддитивные технологии: возможности и перспективы 3D-печати. «Управление производством. Цифровое производство», апрель 2017. Публикуется в сокращении.
Статья опубликована 09.10.2017 , обновлена 15.06.2022