PEEK | PEI (ULTEM™) | PEKK и PSU | Высокоэффективные полимеры vs металлы | Итоги: кратко
Следующие по эффективности после композитных материалов в FDM‑печати – так называемые суперконструкционные пластики, или суперпластики. Это передовые инженерные термопласты, обладающие уникальными термостойкими и прочностными характеристиками и в некоторых случаях позволяющие заменять металлы. Самые известные из них – полиэфирэфиркетон (PEEK) и полиэфиримид (PEI), полиэфиркетонкетон (PEKK) и полисульфон (PSU). Рассмотрим подробнее их параметры, особенности печати и эксплуатации.
PEEK
Полиэфирэфиркетон, он же PEEK, – высокоэффективный тугоплавкий конструкционный термопласт, один из наиболее жестких полимеров с исключительными характеристиками. Может применяться в качестве альтернативы алюминию, а иногда и сталям, при этом напечатанные изделия легче металлических.
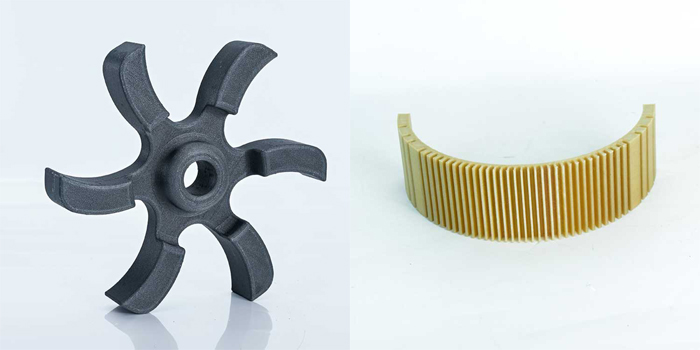
Характеристики
-
Плотность 1,3 г/см3;
-
температура плавления: 343 °C;
-
температура стеклования: 143 °C;
-
температура эксплуатации: от -70 °C до ~230 °C, выдерживает краткосрочные нагревы до 300 °C;
-
предел текучести: 120 МПа.
Плюсы и минусы
PEEK обладает действительно высокой термостойкостью и прочностью, что позволяет применять его практически в любых сферах (в частности, в авиационной промышленности и судостроении), в том числе вместо алюминия стали, плотность которых выше в два и шесть раз соответственно.
Благодаря стойкости к износу и большинству химических реагентов, готовые детали можно использовать в высоконагруженных и подвижных механизмах. Чистый PEEK является еще и биосовместимым, что позволяет использовать его в эндопротезировании. Напечатанные имплантаты получаются близкими по плотности к костям, не обладают магнитными свойствами и равноценны по прочности металлическим.
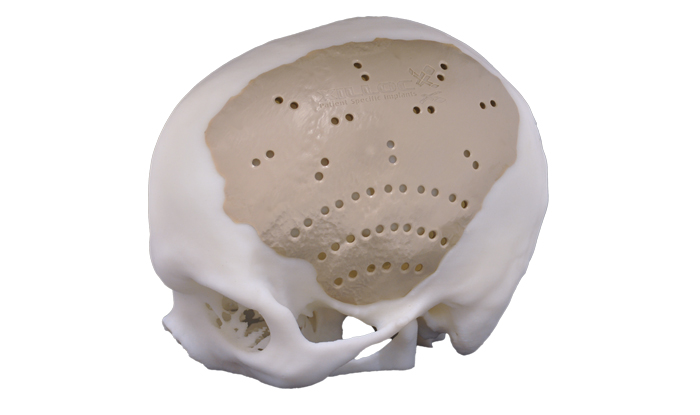
В то же время PEEK уязвим к воздействию концентрированных кислот и ультрафиолету, что может наложить небольшие ограничения на его использование, хотя современные модификации способны справиться и с этими проблемами. Один из минусов пластика – высокая цена, если сравнивать с более распространенными полимерами.
Процесс печати пластиком PEEK – сложная процедура, требующая наличия дорогой машины со специальными температурными режимами, которые помогут справиться с проблемами экструзии и термоусадкой. Разберем некоторые практические моменты работы с термопластом.
Станьте квалифицированным специалистом по аддитивным технологиям! Учебный центр iQB Technologies предлагает пройти курсы по 3D-печати, сканированию и моделированию
Подготовка к печати
PEEK не обладает сильной гигроскопичностью, однако перед печатью материал все-таки следует просушить. Хранить его лучше в темном и сухом месте, в герметичных условиях.
Во избежание термоусадки и для достижения равномерной кристаллизации обязательно наличие герметичной активной термокамеры с температурой не ниже 135 °C, а также высокотемпературного цельнометаллического экструдера с нагревом до 420 °C. Температура стола должна быть на уровне температуры камеры – 135 °C и выше. При несоблюдении температурных режимов деталь будет обладать аморфной структурой и лишится своих механических свойств.
• камера построения: 310 × 310 × 410 мм;
• система быстросъемных печатающих головок;
• максимальная температура экструдера – 500 °C, рабочего стола – 200 °C; температура камеры – 120 °C;
• толщина слоя: 0,05 – 0,3 мм;
• скорость печати: до 150 мм/с
Эксперты iQB Technologies рекомендуют статью Корпус трансформатора, эндопротез и пресс-форма: что можно напечатать из PEEK
Постобработка и отжиг
Для повышения степени кристаллизации, улучшения внутренней структуры деталей и снятия внутренних напряжений требуется отжиг – один из видов термической обработки. Процесс стоит проводить в ванне с кварцевым песком. Поместите туда напечатанный объект, после чего проведите отжиг в печи, разогретой примерно до 200 °C.
Сначала изделие необходимо выдерживать определенное время при одинаковой температуре, а затем медленно охлаждать, снижая температуру. Благодаря тугоплавкости PEEK механическая обработка не составит большого труда.
Изделия из PEEK и ULTEM™ на 50‑60% легче алюминиевых при сохранении высокой прочности и термостойкости
PEI (ULTEM™)
PEEK сегодня считается одним из самых эффективных термпопластов для 3D‑печати, однако существуют и альтернативные варианты. Один из них – полиэфиримид (PEI), аморфный термопласт в диапазоне цветов от янтарного до прозрачного, стойкий к высоким температурам, при этом не относящийся к семейству пластиков PEEK.
Коммерческое название PEI, запатентованное компанией SABIC, – ULTEM™. Основные сферы его применения – пищевая промышленность, медицина, авиационная и космическая индустрия, изготовление штамповой оснастки. В производстве чаще всего можно встретить две модификации материала – ULTEM™ 1010 и ULTEM™ 9085.
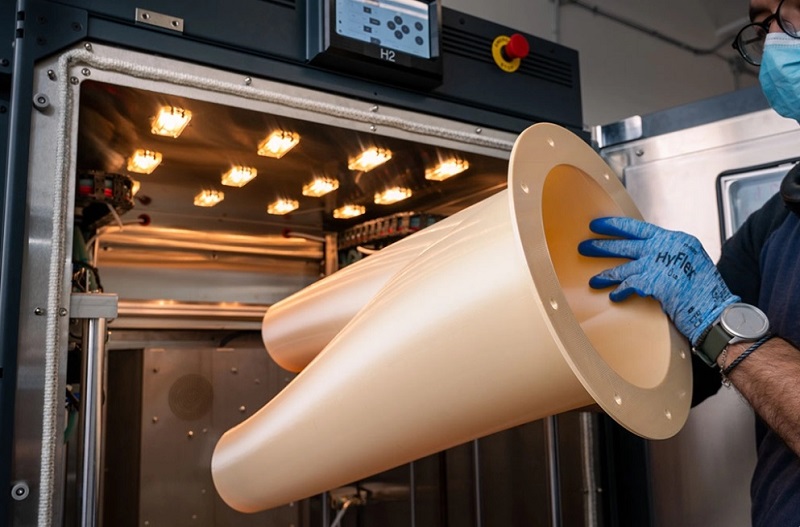
Характеристики
-
Плотность: 1,27 г/см3;
-
температура плавления: ~370 °C;
-
температура стеклования: 217 °C;
-
температура эксплуатации: от -50 °C до ~120 °C, выдерживает краткосрочные нагревы до 170 °C.
Плюсы и минусы
Хотя по своим характеристикам PEI несколько уступает PEEK, он тем не менее обладает высокой прочностью, устойчивостью к высоким температурам, едким химикатам, воде. Имеет хорошие диэлектрические свойства.
Большое преимущество ULTEM™ 1010 – в том, что это единственный пластик, имеющий сертификацию для работы с пищевыми продуктами. В свою очередь, ULTEM™ 9085 сертифицирован для производства авиационных компонентов.
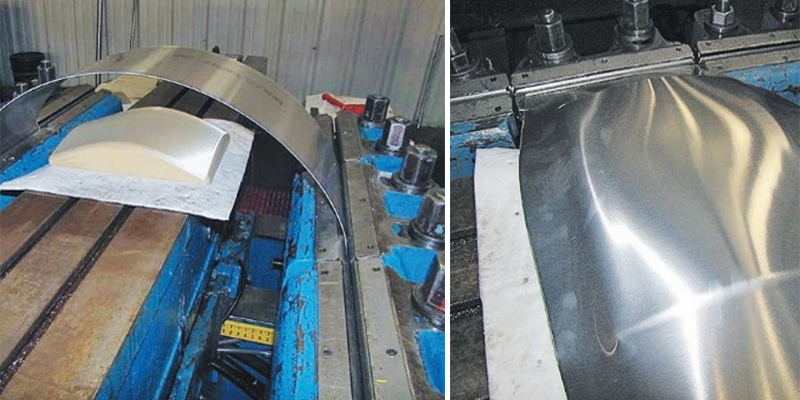
ULTEM™ 9085 также широко используется для быстрого изготовления гидроформовочной оснастки в производстве листовых и трубчатых деталей в качестве эффективной замены дорогостоящим металлическим штампам, что особенно актуально для мелкосерийного производства. Благодаря возможности приложения к пуансону из этого материала давления до 70 МПа его успешно применяют для формовки деталей из алюминиевых сплавов, стали и титана.
Цены на PEI/ULTEM™ на рынке высоки, но значительно ниже по сравнению с PEEK, а процесс аддитивного производства – сложная задача, требующая специального оборудования.
Читайте в блоге о популярных полимерах для 3D-печати: ABS | PLA | PETG | Композиты | Полиамиды | Поликарбонат
Процесс 3D‑печати
Для печати PEI обязательно следует использовать 3D‑принтер с цельнометаллическим экструдером с нагревом до 360‑390 °C, подогреваемой платформой (140-150 °C) и закрытой активной термокамерой (до 100‑150 °C). Игнорирование правильных температурных требований приведет к усадке, деформации конечной модели и плохой адгезии.
Если есть необходимость, напечатанные изделия можно подвергнуть обжигу в воздушных печах для уменьшения внутренних напряжений и улучшения структуры.
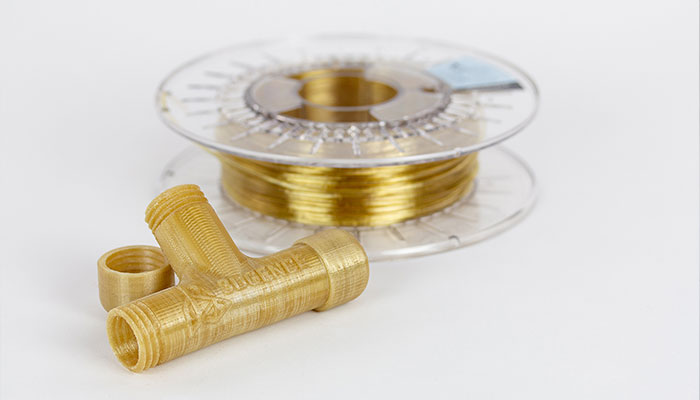
PEKK и PSU
Полиэфиркетонкетон (PEKK) – еще один термопласт из семейства PAEK (в которое входит и PEEK), обладающий исключительными термическими, механическими и химическими свойствами. Основное отличие PEKK от PEEK лежит в химической структуре этих пластиков, а именно в соотношении эфирных и кетоновых связей, что обеспечивает первому более низкую скорость кристаллизации и температуру плавления. Благодаря этому процесс печати PEKK немного проще, и практически единственное его отличие от PEEK – в термостойкости.
Полисульфон (PSU) – высокотемпературный ароматический сульфоновый полимер с уникальными термическими, химическими и прочностными характеристиками. На рынке является хорошей альтернативой ULTEM™ 9085, имеет более высокую температуру эксплуатации (170‑180 °C), низкую плотность и продается по более доступным ценам. Существует модификация PPSU, отличающаяся повышенной термической и химической стойкостью. Процесс печати полисульфоном остается сложной задачей и мало чем отличается от применения PEEK или ULTEM™.
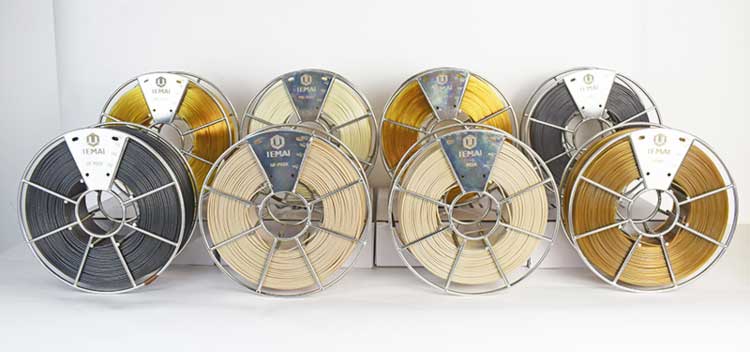
Высокоэффективные полимеры vs металлы
Говоря о замене металлов полимерами надо понимать, что эти материалы имеют фундаментальные различия. Полукристаллические полимеры частично состоят из кристаллов, в то время как металлы содержат множество кристаллических структур (зерен), различающихся по ориентации.
Поскольку цепи термопластичных полимеров химически разделены, сила притяжения между цепями слабее, чем металлическая связь между кристаллами в металлах. Поэтому металлы более устойчивы к упругим деформациям (более жесткие) и в целом более термостойкие. В то же время по мере разработки более совершенных термопластов они в плане эффективной прочности начинают соответствовать металлам, а в некоторых случаях и превосходить их.
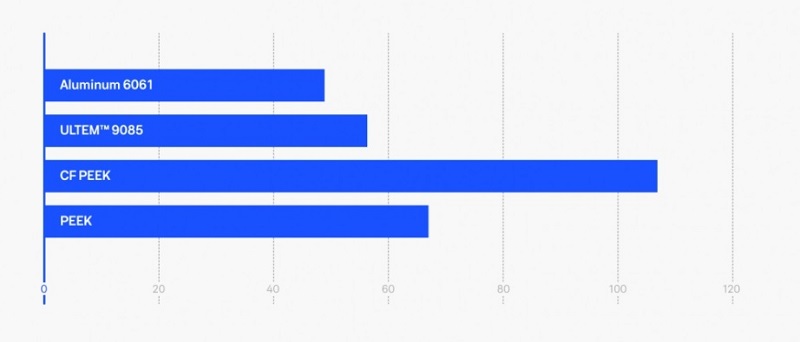
Изделия из PEEK и ULTEM™ на 50‑60% легче алюминиевых, при этом они сохраняют высокую прочность и термостойкость. Во многих отраслях, в том числе в транспортной, выбор полимеров вместо металлов будет означать бòльшую экономию топлива, снижение выбросов углекислого газа и увеличение грузоподъемности. Кроме того, эти материалы обладают высокой химической стойкостью, высокой ударопрочностью, имеют класс воспламеняемости по стандарту UL94‑V0 и соответствуют требованиям стандарта FAR 25.853 по огнестойкости, дымостойкости и токсичности, что необходимо для аэрокосмической и судостроительной промышленности.
Итоги: кратко
Существуют и другие высокоэффективные пластики для FDM‑печати, обладающие повышенной термостойкостью или другими исключительными особенностями. На приведенных выше примерах хорошо видно, что некоторые термопласты способны заменять металлы в конкретных задачах и имеют большой потенциал в производстве широкого спектра продуктов – от медицинских изделий до авиадеталей. Линейки расходных материалов расширяются и обновляются в быстром темпе, а 3D‑печать начинает захватывать все более интересные сферы применения.
Статья опубликована 01.06.2023 , обновлена 23.06.2025