Сферы применения и решаемые задачи | Преимущества и ограничения | Возможности в цифрах | Материалы для 3D-печати | Механические свойства изделий
3D-печать относится к быстро развивающейся технологии. Она уже зарекомендовала себя как эффективный метод создания передовых продуктов и будет играть все большую роль в производстве с развитием цифровизации и переходом к модели Индустрии 4.0. Отвечаем на самые популярные вопросы о 3D-печати металлами, которые задают наши клиенты и читатели – технические специалисты, ищущие новые пути оптимизации производства и внедрения инноваций. Мы снабдили статью ссылками на другие материалы блога, где конкретные вопросы рассматриваются в деталях.
Если у вас есть вопросы по внедрению 3D-технологий, задайте их эксперту iQB Technologies онлайн!
В каких отраслях рекомендуется применение 3D-принтеров?
Самые перспективные отрасли для внедрения аддитивных технологий, в том числе 3D-печати металлом, – высокотехнологичные, наукоемкие производства, где в приоритете оптимизация или создание сложных инновационных продуктов: авиакосмическая индустрия, оборонная промышленность, машиностроение, автомобилестроение, энергетика, судостроение, нефтегазовый сектор. Нельзя не упомянуть медицину и ювелирное дело, потому что 3D-печать не имеет себе равных в создании индивидуализированных изделий.
Какие задачи выполняются с помощью этой технологии?
Печать металлами в основном решает задачи опытного и мелкосерийного производства, прототипирования, НИОКР. Поэтому сегодня основными пользователями 3D-оборудования становятся крупные исследовательские центры, а также учебные заведения, готовые инвестировать в проекты внедрения новой технологии.
Изготовление конечных серийных изделий из металлов уже активно применяется такими крупными компаниями, как General Electric, Airbus, Boeing, BMW, Michelin, а с появлением супермощных машин типа SLM NXG XII 600 массовое аддитивное производство становится реалией не столь отдаленного будущего.
Читайте в блоге: За 45 часов Bugatti сделала невозможное благодаря 3D-принтеру
В чем разница между различными процессами 3D-печати металлом?
Принцип работы подавляющего большинства современных 3D-принтеров по металлу основан на расплавлении порошков в заранее сформированном слое (Powder Bed Fusion), обычно с помощью мощного лазера.
Вы можете часто встретить такие торговые наименования, как SLM (Selective Laser Melting), DMLS (Direct Metal Laser Sintering), DMLM (Direct Metal Laser Melting) и Laser Cusing. На самом деле в современных системах всем этим названиям соответствует один и тот же процесс. Серьезные различия заключаются в том, как спроектированы и работают те или иные принтеры. В нашем блоге мы используем термин «селективное лазерное плавление» (или SLM-технология).
Принцип работы SLM-машины описан в статье Технология селективного лазерного плавления
Зачем моему предприятию 3D-принтер? Разве отливать не проще и дешевле?
Ошибочно думать, что 3D-печать призвана заменить литье или иные классические процессы. Она помогает решить специфические задачи, которые невыполнимы либо слишком трудоемки при использовании традиционных технологий, например:
-
изготовление уникальных деталей сложной геометрии, в том числе мельчайших деталей, изделий с внутренними полостями и каналами, тонкими стенками и т.п.;
-
снижение веса изделий;
-
сокращение числа единиц в сборке;
-
создание ячеистых структур.
Такие возможности обеспечивает топологическая оптимизация: проектировщики могут создавать практически любую геометрию.
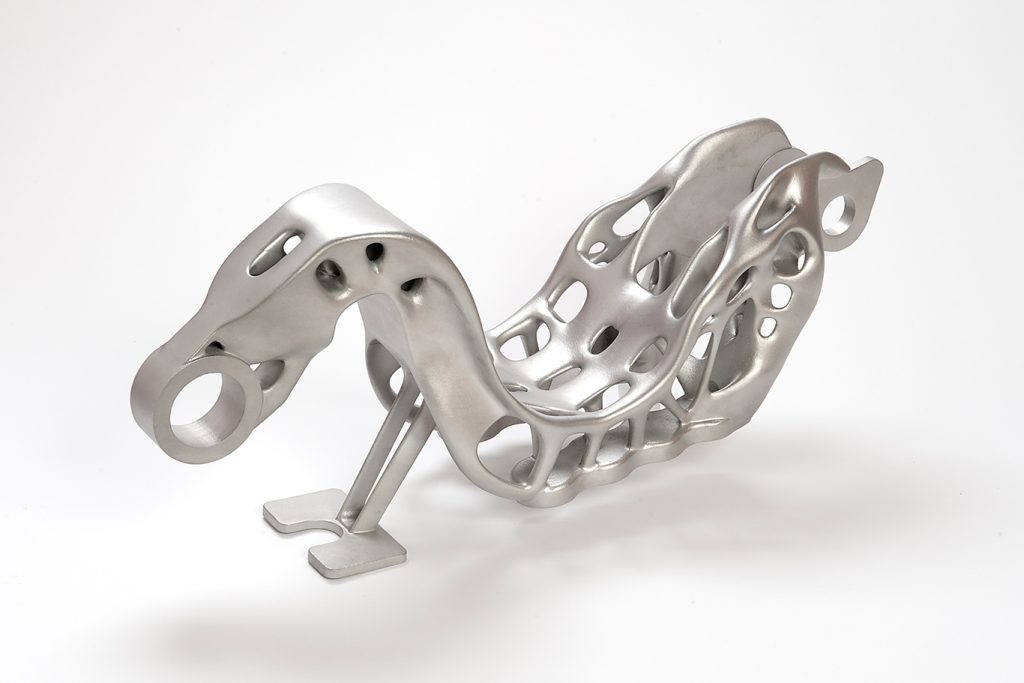
Результаты применения селективного лазерного плавления:
• cнижение массы на 31% и сокращение общего времени сборки;
• объединение трех деталей в одну;
• уменьшение коэффициента использования материала с 17 до 1,5;
• значительное сокращение времени механической обработки.
Субтрактивные методы будут и дальше применяться в тех случаях, когда это эффективно с точки зрения стоимости, типа изделий и других требований. Вопрос не в выборе между двумя технологиями, а в том, когда лучше применить аддитивную, а когда субтрактивную. Иногда при производстве одной детали уместно задействовать оба метода. К примеру, если вы понимаете, что для пресс-формы стоит изготовить вставку с конформным охлаждением, потому что это сократит цикл литья и улучшит качество изделия, используйте 3D-принтер. При этом другие компоненты вы будете производить по классической технологии.
3D-печать следует воспринимать как еще один вариант технологии получения изделий наряду с механической и пластической обработкой, литьем и др. При выборе вариантов производственного процесса взвешивайте тщательно все «за» и «против».
Рекомендуем материал Российский производитель SLM-машин развеивает мифы о технологии
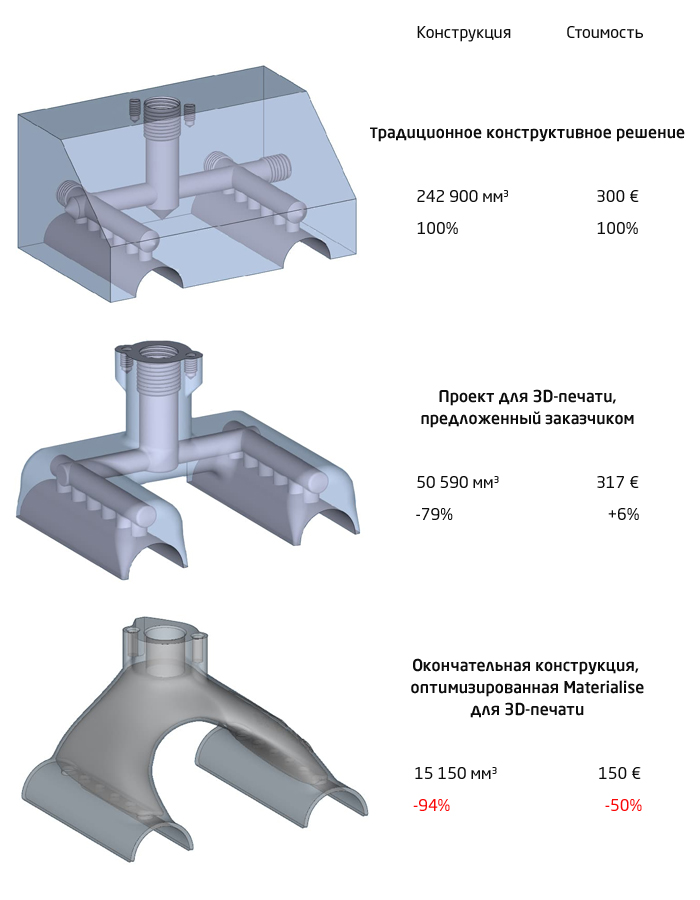
Какова экономическая эффективность аддитивного производства?
Технология SLM позволяет значительно сократить цикл производства изделия. С одной стороны, когда мы считаем стоимость материалов, аддитивное производство выходит дороже. Но если учитывать все экономические факторы, начиная с сокращения потребления электроэнергии и кончая уменьшением налоговой нагрузки, 3D-печать помогает сэкономить достаточно серьезные средства.
Кроме того, технология дает возможность резко снизить коэффициент Buy-to-Fly, то есть соотношение между количеством закупленного материала и количеством материала в готовой детали.
Какие есть ограничения?
У предприятий, решивших внедрить аддитивную технологию печати металлом в свой производственный цикл, могут возникнуть следующие трудности:
-
необходимость в последовательных научных исследованиях (в том числе для изучения свойств металлов);
-
ограничения в размерах объектов;
-
большие первоначальные вложения из-за высокой стоимости оборудования и расходных материалов;
-
особые требования к помещению и условиям эксплуатации;
-
аттестация оборудования и сертификация изделий;
-
сложность в адаптации 3D-решений к существующим технологическим циклам на производстве.
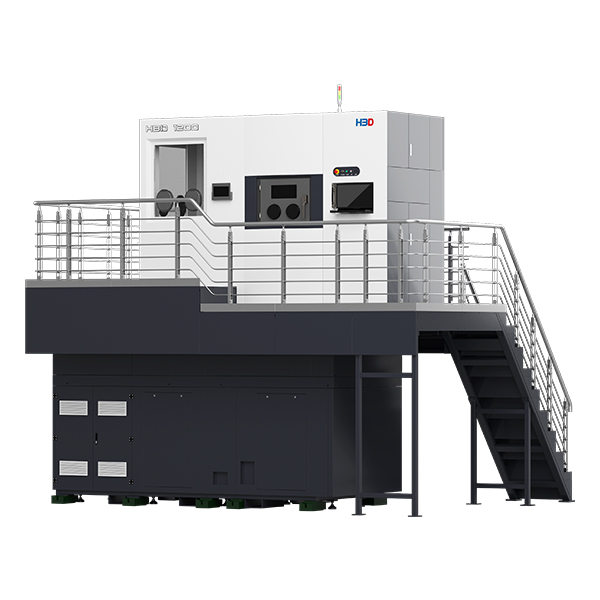
Каковы максимальные габариты напечатанного изделия?
Исторически сложившимся отраслевым стандартом оборудования на базе селективного лазерного плавления является платформа размером 250 x 250 мм с высотой построения 250-300 мм.
К самым крупноформатным принтерам на базе этой технологии можно отнести:
-
HBD 1000 (600 x 600 x 1000 мм) и HBD 1200 (460 x 460 x 1200 мм);
-
GE Atlas (1000 куб. мм);
-
SLM 800 (500 x 280 x 850 мм) и SLM NXG XII 600 (600 х 600 х 600 мм) от SLM Solutions.
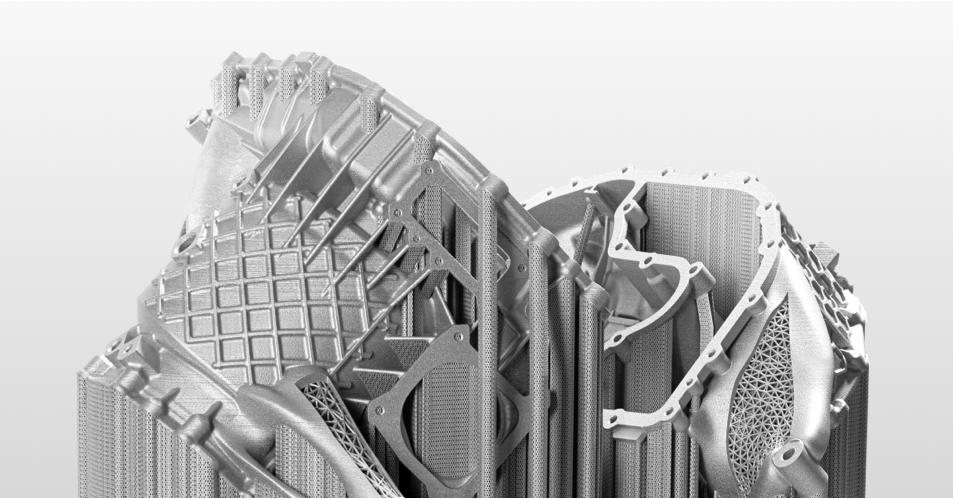
Размер: 590 х 560 x 367 мм
Вес: 15,5 кг
Материал: AlSi10Mg
Время изготовления: 21 час
А минимальная толщина стенки?
Диаметр пучка лазера в аддитивной установке печати металлами – 70-80 микрон. Можно напечатать стенку детали толщиной в два прохода лазера, т.е. минимальная толщина будет всего лишь 140-150 микрон.
Сколько по времени выращивается модель? От чего зависит скорость печати?
От нескольких часов до нескольких суток. К примеру, модель высотой 3-4 см будет печататься от 2 до 8 часов, в зависимости от ее площади и высоты. Тестовая печать на промышленном 3D‑принтере с камерой построения 280 х 280 х 360 мм занимает около суток.
Производительность аддитивных установок зависит от разных факторов:
-
Чем больше лазеров, тем выше скорость и больше количество производимых деталей (мощность лазера – 400, 700 или 1000 Вт).
-
В зависимости от конструкции системы порошок может распределяться в двух или только в одном направлении. Подача порошка в двух направлениях обеспечит значительную экономию времени производства.
-
Непрерывная или периодическая подача порошка. Системы с периодической подачей могут требовать остановку оборудования для дозаправки во время выполнения построения, что замедляет процесс.
-
Возможность настроить рабочие параметры системы для увеличения скорости.
Мы работаем напрямую с ведущими китайскими и российскими производителями металлических порошков. Обеспечиваем минимальные сроки поставки, возможность разработки индивидуальных материалов под технические требования заказчика, проведение НИОКР:
Заказать порошок под ваши требования
Какие виды металлов применяются в аддитивном производстве?
Металлические порошки представляют собой мелкодисперсные сферические гранулы. Свойства получаемой продукции в значительной степени зависят от свойств используемого в принтерах порошка – степени чистоты, текучести и объемной плотности.
Современные аддитивные технологии предполагают использование около двадцати протестированных и готовых к эксплуатации материалов, в их числе – инструментальные, нержавеющие, жаропрочные сплавы, алюминиевые и титановые сплавы, медицинские кобальт-хром и титан.
Поскольку металлов очень много, и каждый из них обладает определенными свойствами, один металл можно заменить другим исходя из технологических задач. К примеру, если в технологической цепочке необходимо задействовать титановый сплав, то технолог сможет выбрать один из множества титановых сплавов с теми свойствами, которые нужны для производства конкретного изделия.
Подробнее в статье: 5 особенностей металлических порошков для 3D-печати
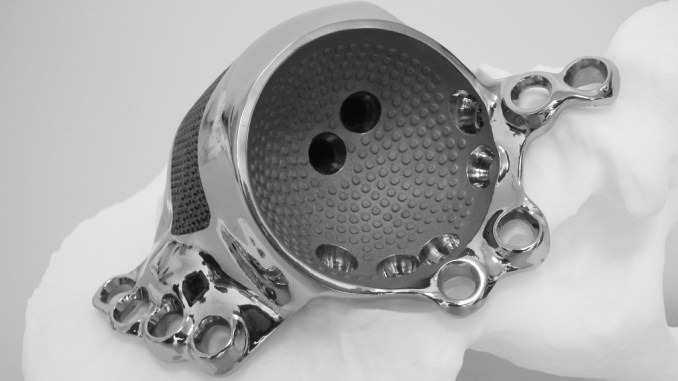
Приведите пример применения в аддитивном производстве тугоплавких металлов, например вольфрама
Вольфрам зарекомендовал себя как ценный материал для 3D-печати, и многих специалистов привлекает его термостойкость, особенно в вакууме и под высоким напряжением. Исследования показали, что технология селективного лазерного плавления может быть использована для производства вольфрамовых деталей высокой плотности, точности и сложности. Это могут быть сопла ракетных двигателей, лопасти турбин, полотна пил, сверла, подшипники, поршни, коллиматоры и т.д.
Особый интерес здесь представляет медицина, а именно сфера противорадиационной защиты и радионуклидной визуализации. В качестве примера приведем проект компании HBD по 3D-печати рентгеновского отсеивающего растра из чистого вольфрама.
Производитель имеет богатый опыт исследований высокотемпературных тугоплавких металлов, таких как вольфрам, а также воплощения с помощью 3D-печати конструкторских решений, оптимально соответствующих сценариям применения. HBD разработала процесс аддитивного производства высокоточных, высокоплотных изделий со сверхтонкими стенками, позволяющий полностью удалить примеси, благодаря чему напечатанные из чистого вольфрама детали успешно используются в вакуумной среде.
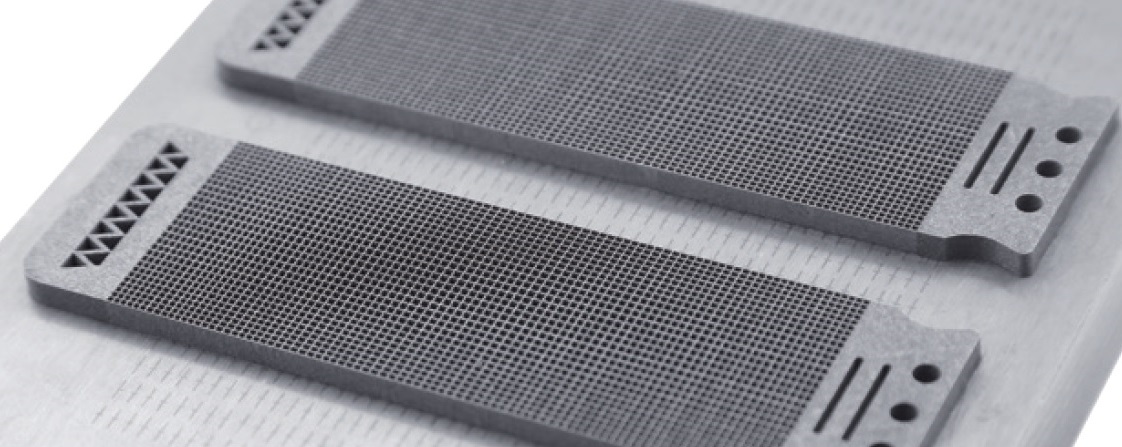
По сравнению с традиционными 2D молибденовыми или 1D решетками для рентгеновских аппаратов, 2D вольфрамовые отсеивающие растры имеют значительные преимущества. С одной стороны, более высокая плотность вольфрама способствует лучшему поглощению рентгеновского излучения. С другой стороны, цифровое производство с участием 3D-печати дает больше свободы в проектировании продукта, что влияет на более точное введение рентгеновских лучей в фотодиод.
Также читайте Гигант китайского рынка HBD: «Россия уверенно осваивает 3D‑печать металлами»
Интересуют способы производства металлических порошков.
Есть несколько технологий изготовления сферического порошка. Основным способом является атомизация, а именно: ультразвуковой ударнокинетический метод макрокапельной атомизации и микрокапельной диспергации металлов и ультразвуковой капельноволновой метод ультразвуковой атомизации металлов. Процесс происходит в атомайзере, где металл распыляется в специальной камере.
Какая дисперсность у металлов для 3D-печати?
У каждого металла своя дисперсность. При 3D-печати используются порошки дисперсностью от 4 до 80 микрон. Например, в Европе порошки меньше 8 микрон запрещены, так как они слишком взрывоопасные.
Хотелось бы сравнить прочность изделий при использовании SLM и классических технологий.
Прочностные характеристики изделий зависят от самих изделий, точнее от их геометрии, от поставленных задач, нагрузки, условий применения (морская среда, космос и т.д.).
SLM-печать дает возможность добиться прочностных показателей, сопоставимых с традиционными технологиями. Но примерно в 50% случаев отлитое или отфрезерованное изделие из идеального блока материала прочнее в сравнении с результатом 3D-печати. Причина – в пористости, которая получается по аддитивной технологии. Однако при этом напечатанные объекты становятся более упругими и выдерживают более высокие нагрузки, особенно если мы говорим о таких материалах, как титан, сталь и даже различные сплавы алюминия. Алюминий – достаточно мягкий материал, пористость добавляет ему упругости.
Необходимо сделать 3D-модель, просчитать все синтетически, провести анализ и получить предварительные данные по изделию, а затем задуматься о возможности его изготовления и тестирования в лаборатории. Такой подход поможет оптимизировать производство и не будет слишком затратным.
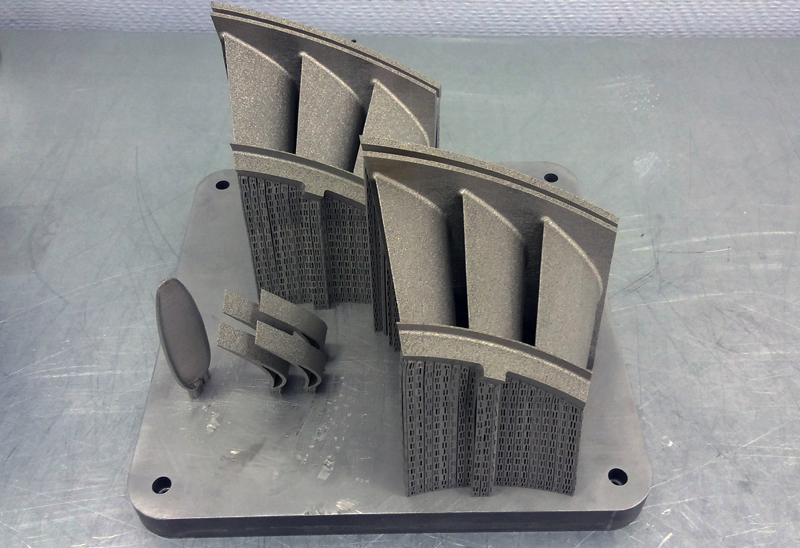
Изготовление соплового аппарата 1 и 2 ступеней ГТД из порошка сплава Inconel 738
Образец | Предел прочности, МПа | Предел текучести, МПа | Отн. удлинение, % |
Исходный | 1030 | 600 | 3,7 |
После термообработки | 1430 | 820 | 8,5 |
Но есть такие технологии, как горячее изостатическое прессование (ГИП), которые позволяют вывести эти изделия на тот же уровень механических свойств. На титановых сплавах фактически можно получить 80-90% от прочности даже не литых, а кованых изделий. За счет ГИП удается устранить внутренние дефекты, возникающие из-за неоднородности гранулометрического состава порошка, и достичь практически стопроцентной плотности.
Часто задают вопрос, может ли 3D-печать обеспечить более высокую прочность по сравнению с классическими способами. Скажем, за счет поверхностного легирования порошков можно получить структуры, действительно обладающие повышенными механическими свойствами. Это могут быть суперинварные сплавы, например, – то есть те технологии, которые могут обеспечить уникальные свойства, в том числе механические и теплофизические.
Физико-механические свойства основных сплавов приведены в брошюре: Металлы для 3D-печати
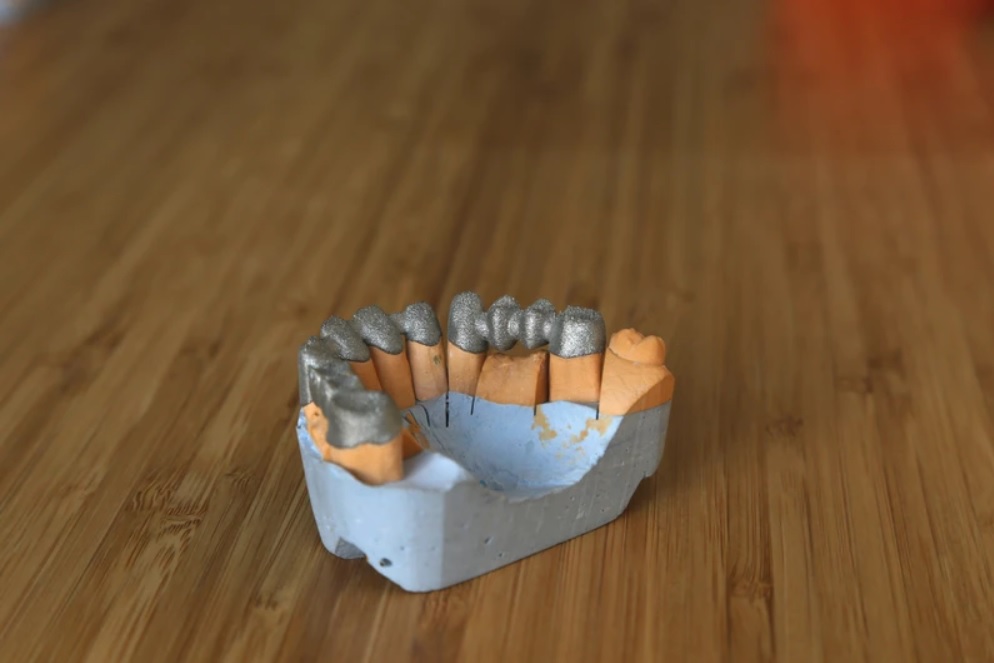
Можно ли предсказать механические свойства получаемых материалов – предел текучести, размер зерна, пористость?
Печать металлами обеспечивает очень высокую повторяемость. «Опыт работы показывает, что преемственность механических свойств есть, – рассказывает Антон Агаповичев, старший преподаватель кафедры технологий производства двигателей Самарского университета. – Определив оптимальный режим, мы печатаем стандартные цилиндрические образцы для подтверждения этих свойств. В дальнейшем, когда начинаем изготавливать детали, вместе с одной из деталей мы специально изготавливаем образцы-свидетели, на которых эти механические свойства постоянно подтверждаем. Сейчас ведутся научные работы по предсказанию механических свойств, но они касаются больше проектирования самих металлов».
Но в программном обеспечении пока что невозможно предсказать предел текучести, пористость и другие механические характеристики. Наоборот, заранее устанавливаются определенные свойства для каждого материала, которые используются в дальнейшем для моделирования процесса. Это обратный процесс, нам необходимо знать свойства материалов для того, чтобы спрогнозировать различные дефекты.
Во второй части статьи рассказываем о подготовке моделей к 3D-печати, нюансах эксплуатации принтеров по металлу и о постобработке.
Статья опубликована 01.07.2021 , обновлена 28.03.2025