Можно ли использовать переработанный пластик?
Как проводятся испытания полимеров?
По какой технологии лучше изготавливать макеты?
Почему силиконовая форма не затвердела после печати?
Полимеры в медицине и проблемы сертификации
В ходе круглого стола российские специалисты по аддитивному производству ответили на популярные вопросы пользователей и обсудили проблемы отрасли. В дискуссии приняли участие эксперт iQB Technologies по решениям 3D‑печати Виктор Наумов и руководители ведущих отечественных компаний-производителей полимерных материалов для 3D‑печати:
-
Кирилл Корнилов – генеральный директор Gorky Liquid (ООО НПП «3Д Аддитивные технологии»),
-
Дмитрий Миллер – исполнительный директор REC и 3D Solutions (ООО «РЭК» и ООО НПО «3Д Солюшнс»).
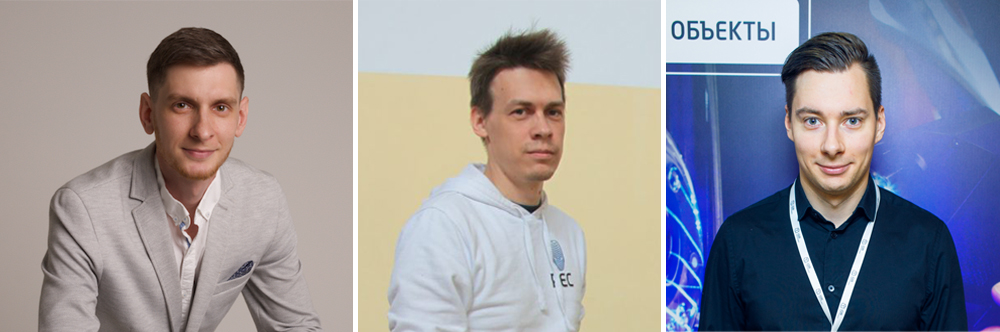
Можно ли использовать переработанный пластик?
Виктор. Переработка брака печати и вторичное использование пластика возможны?
Дмитрий. Всё зависит от полимера. На самом деле переработать можно всё, здесь вопрос о рентабельности.
Виктор. С филаментами более-менее понятно, а гранулят? Например, ABS либо какой-то ABS, наполненный углеволокном или минеральным волокном?
Дмитрий. Переработка ABS возможна, он слабо портится. С каждой термообработкой, при переплавлении полимеров, они обычно немного деградируют – в разной степени в зависимости от материала. PET и PETG можно перерабатывать десятки раз. У ABS число переработок ограничено, но в целом можно повторно его дробить, получать гранулят с дробленки и повторно использовать. Материал своих свойств в значительной степени не потеряет.
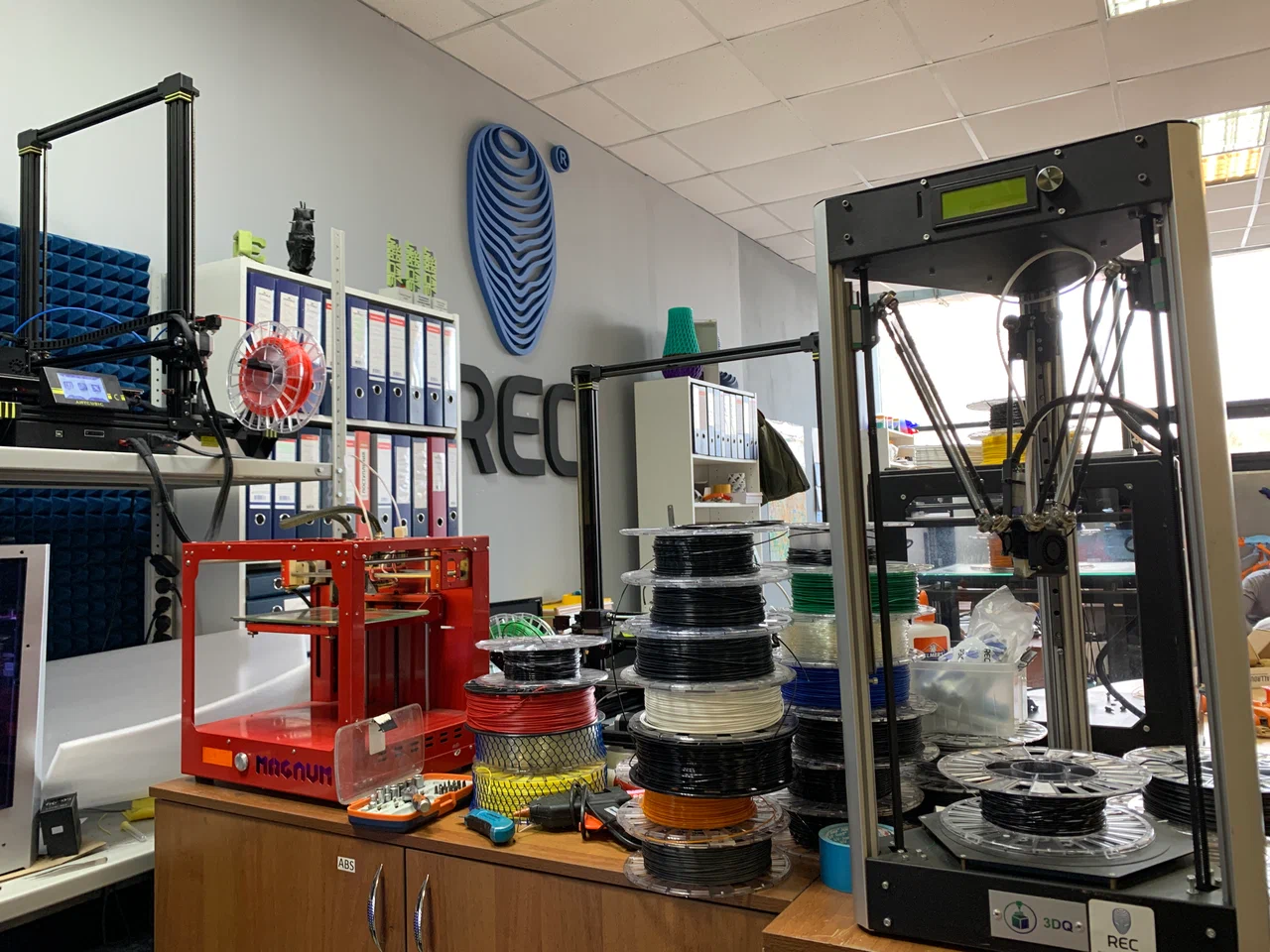
Виктор. А что насчет фотополимеров?
Кирилл. Ответ точно нет, потому что при полимеризации смола переходит из жидкого состояния в твердое. Реакция произошла, и по факту вы получаете материал, который не может быть переработан.
Эксперты iQB Technologies рекомендуют статью От протезов до оснастки: 3D‑печать термопластами и композитами на их основе
Как проводятся испытания полимеров?
Виктор. Какие методы исследования физических свойств напечатанных изделий применяются в зависимости от настроек слайсера?
Дмитрий. Для FDM‑печати никаких стандартов пока нет. Мы изготавливаем детали для испытаний на разрывных машинах (те самые лопатки, которые мы жмем, гнем, тянем и т.д.), но ГОСТов, предусматривающих использование аддитивных технологий, нет.
Но я думаю, этот вопрос решится в скором времени. Каждый производитель разрабатывает свою технологию тестирования, и мы в том числе. В паспорте каждого материала описано: каким образом печатаются лопатки, с какими параметрами, как нужно ориентировать слои, чтобы провести испытания 3D‑печати, поскольку, в отличие от литья, требуется чуть больше испытаний на разрыв или на изгиб.
Мы делаем два варианта: нагружаем деталь, напечатанную вдоль слоев и поперек слоев. В одном случае проверяется прочность самого полимера, и она, как правило, близка к литейным параметрам. А когда мы нагружаем на разрыв слоев – это слабое место 3D-печати. Правда, не со всеми материалами – есть достаточно изотропные полимеры. В большинстве своем межслойная адгезия ниже, поэтому прочность на разрыв слоев будет ниже, чем вдоль слоев. При производстве деталей важно учитывать, как ориентировать деталь при печати, чтобы она нормально выполняла предъявляемые к ней требования.
Виктор. Да, нужно следовать определенной логике, отталкиваясь от геометрии детали. Если у вас не вышло реализовать некую задачу аддитивным методом, необязательно, что вы где-то были не правы. Скорее всего при производстве был выбран неправильный подход к этой задаче. Возможно, выбрав другое положение геометрии или оптимизировав геометрию изделия, этот вопрос можно успешно решить.
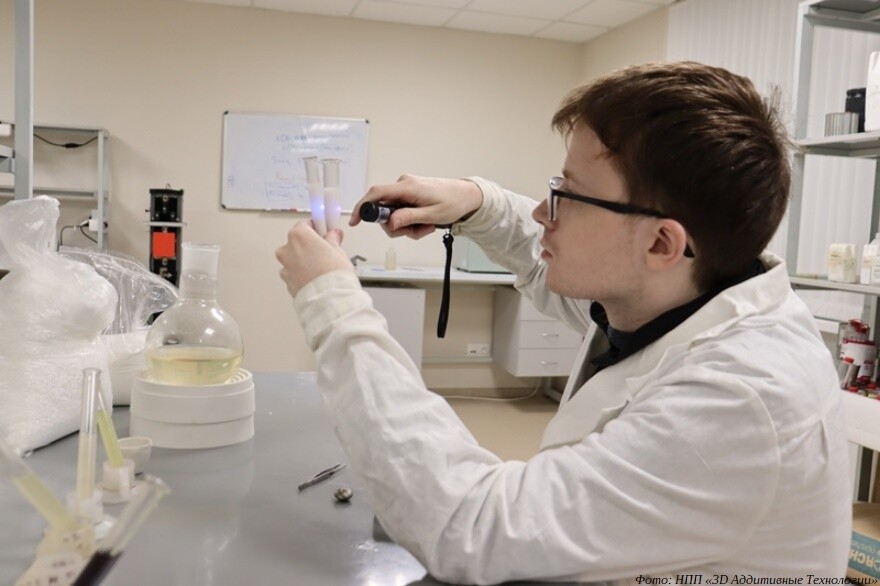
Кирилл. С фотополимерами немного другая ситуация. Не то чтобы более проблемная, это специфика технологии. Во‑первых, у нас есть свой выпущенный ГОСТ, в котором описана технология испытания, и характеристики каждого полимера можно сравнить. Во‑вторых, у нас каждая партия проверяется лабораториями на испытательном стенде, и мы практически всегда видим, что полученные данные партии напечатанных изделий всегда имеют одни и те же характеристики.
Однако есть одно но. Если мы печатаем фотополимером на другом принтере, у которого может быть, например, другая длина волны или другая мощность излучателя, то характеристики детали могут как ухудшаться, так и улучшаться. В отличие от FDM‑печати, фотополимерная модель получается монолитной, и нам не стоит задумываться, как ее расположить, чтобы она была прочнее.
И вторая проблема состоит в том, что постобработка фотополимерных изделий сложнее – их необходимо дозасветить. 3D‑принтеры поставляются с камерами засветки, у которых тоже разная мощность, разные лампы. И одна и та же деталь, напечатанная на одном принтере, но засвеченная по-разному (допустим, в течение 20 или 30 минут), будет иметь разные свойства.
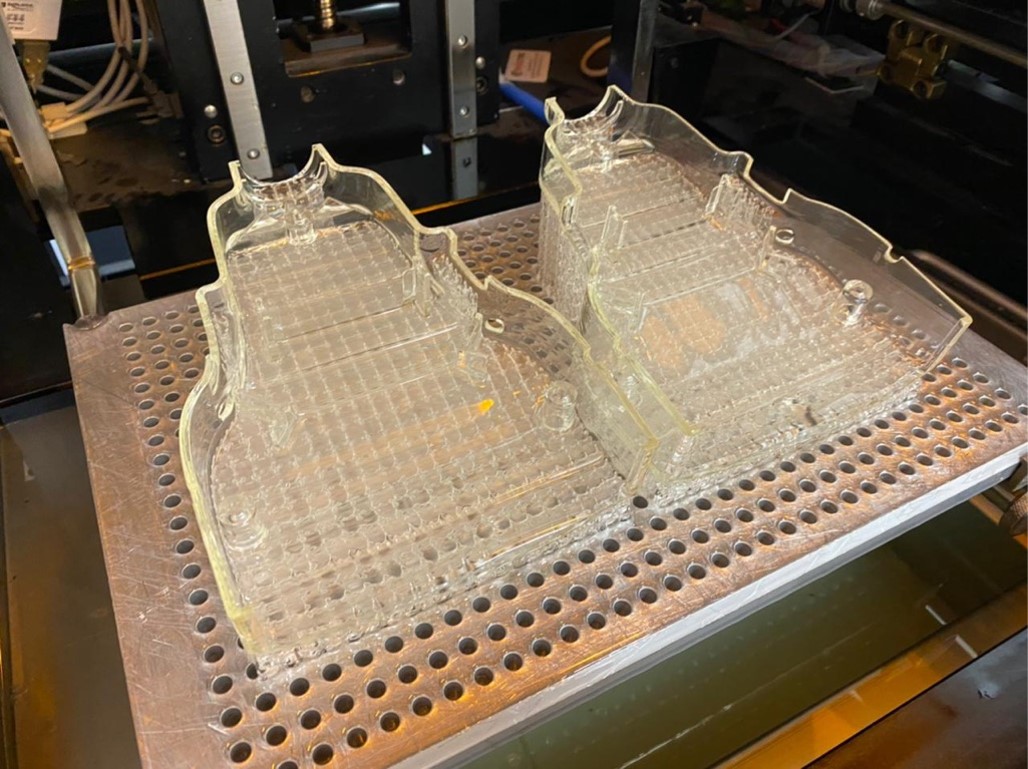
По какой технологии лучше изготавливать макеты?
Виктор. Какой метод 3D‑печати вы бы порекомендовали для производства макетов транспортных средств? Масштаб – 1:5.
Кирилл. Фотополимер, потому что разрешающая способность будет гораздо выше, чем у FDM‑печати. Хотя при масштабе один к пяти габариты макета будут примерно 40‑50 см, и возможно применение FDM‑технологии, если требования к детализации не очень высокие.
В любом случае нужно будет учесть усадку. Любой материал усаживается, в том числе в FDM‑принтере. И если это достаточно габаритная модель, то ее обязательно нужно разместить на столе печати немного по диагонали, чтобы минимизировать процент усадки. Выходит большой объем печати, и SLA, в сравнении с FDM, конечно, дороже по стоимости готового изделия.
Дмитрий. С помощью FDM такие крупные макеты печатать дешевле, но стоит помнить, что высокую детализацию обеспечит только фотополимерная печать. FDM‑принтер тоже может печатать слоями 0,01 мм, но это просто неразумно, ведь время изготовления растянется на месяцы, и это уже теряет какой-либо смысл.
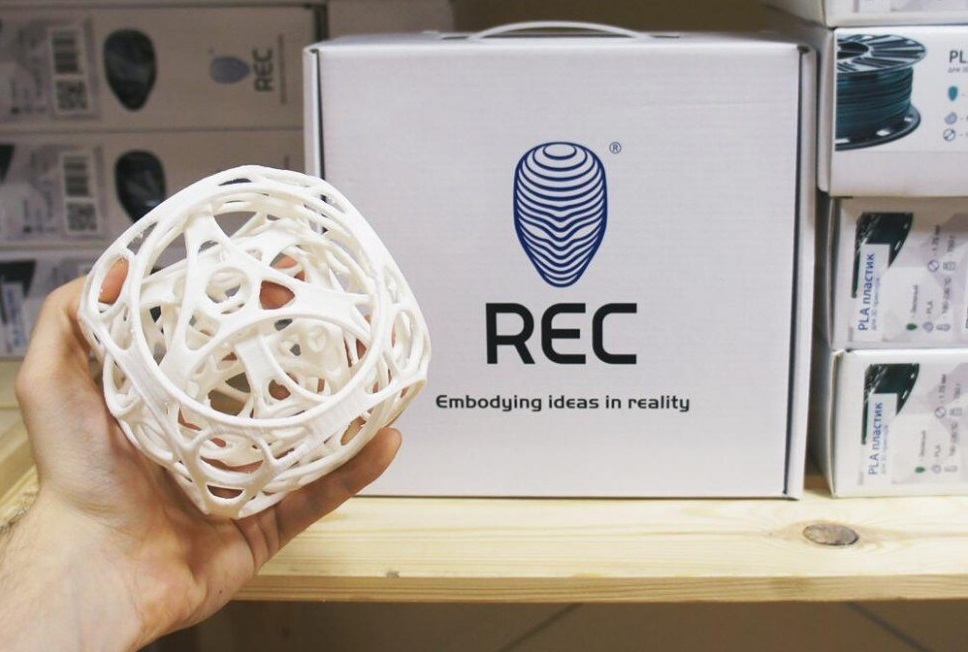
Виктор. От себя добавлю, что для любого типа макетов (не обязательно только транспортных средств) можно использовать комбинированное производство. И второй момент: для макетирования подходят крупногабаритные SLA‑принтеры. Такая машина с камерой 600 х 600 х 400 мм есть в демозале iQB Technologies, с ее помощью мы оказываем услуги.
Хотите напечатать сложный прототип или функциональное изделие из фотополимера? Обращайтесь к нам, выполним ваш заказ за 1‑2 дня!
Практика: проблемы с печатью силиконовой формы
Виктор. После 3D‑печати требуется сделать силиконовую форму. Происходит какая-то реакция между напечатанной моделью и силиконом. Когда форма затвердела, силикон вокруг модели как будто расплавился. Пожалуйста, объясните, что происходит и лучше ли использовать SLA‑технологию именно для этого промышленного сегмента?
Кирилл. Здесь вопрос не конкретно в материале. Вероятно, просто состав фотополимера не сопоставим с вашим силиконом. Скорее всего он на платиновой основе (с ним обычно бывают такие проблемы). Вторая проблема может быть в том, что неправильно отмывается модель. Если на модели есть совсем мелкие остатки материала, который не дополимеризовался, силиконовая модель не застынет. Нужно в чистом этиловом или чистом пропиловом спирте, в ультразвуковой ванночке, эту модель отмыть, высушить, можно немного погреть, два-три часа дать основательно высохнуть и после этого попробовать испытать.
Также читайте Сравнение технологий SLA, DLP и LCD: как выбрать фотополимерный 3D‑принтер
Полимеры в медицине и проблемы сертификации
Виктор. Вопрос из области медицины: какие есть пластики, допущенные к контактам с тканями человека?
Замечу, что не все напечатанное должно касаться непосредственно кожи или тканей человека. Вопрос скорее о сертификации материалов. Причем в медицине не только материалы должны быть сертифицированы, но и используемое оборудование. Прошу вас подтвердить это или опровергнуть.
Дмитрий. Если говорить о 3D‑печати металлами в медицине, сертифицированы и технология (в частности, SLM), и машины, и материалы типа медицинского титана.
С полимерами для аддитивного производства история сложнее. Есть полимеры, которые не отторгаются – полиэфирэфиркетон, к примеру. Из него изготавливаются современные имплантаты, но при помощи других методов, не аддитивных. Технология должна быть сертифицирована, а применительно к FDM с этим пока проблема. У компании REC сейчас нет решений чисто медицинских – для имплантации или эндопротезирования.
Из того, что касается человека, у нас есть допуск к материалам, разрешенным для контакта с пищей. Есть материалы, имеющие санитарно-эпидемиологические сертификаты (это нужно прежде всего для поставки в образовательные учреждения). Есть наши собственные протоколы испытаний на безопасность. Остальные касаются чисто технических областей.
Виктор. А можно ли предложить сертифицировать материал, если он отвечает физико-механическим свойствам?
Дмитрий. Да. Кстати, у нас есть партнеры, производящие ортезы при помощи 3D‑печати, они для себя сделали сертификацию на конечные изделия: провели токсикологический анализ на долговременный контакт с кожей и получили заключение, что ортезы безопасны для человека.
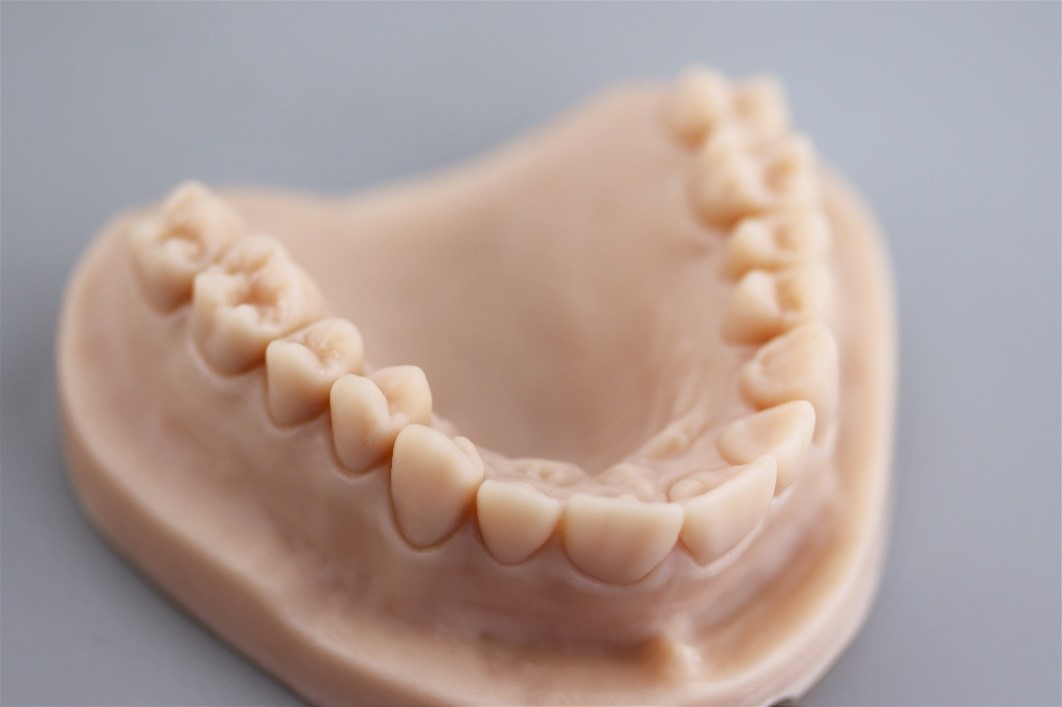
Кирилл. У Gorky Liquid вся соответствующая линейка сертифицирована. Одно из основных направлений нашего производства – стоматологические фотополимеры. Проводились токсикологические лабораторные исследования материалов, что подтверждается соответствующей документацией.
По поводу сертификации фотополимеров совместно с оборудованием – доля правды в этом есть. Сейчас центр, выдающий сертификаты, поставил на паузу некоторые материалы из-за некоторого непонимания, каким образом сертифицировать 3D-принтеры. Мы как производители фотополимеров не хотели бы, чтобы наша смола была сертифицирована только для использования на определенном принтере, для нас это большое ограничение.
Продолжение дискуссии – во второй части статьи.
Подписывайтесь на блог и следите за обновлениями!
Фото в заставке © gorkyliquid.ru
Статья опубликована 15.09.2022 , обновлена 07.10.2024